Chemical vapor deposition (CVD) is a widely used thin film deposition method with numerous advantages, such as high purity, uniformity, and the ability to coat complex shapes. However, it also has several key disadvantages, including high operating temperatures, the need for toxic precursors, and challenges in synthesizing multi-component materials. These drawbacks can limit its applicability in certain scenarios, particularly when working with thermally sensitive substrates or requiring on-site deposition.
Key Points Explained:
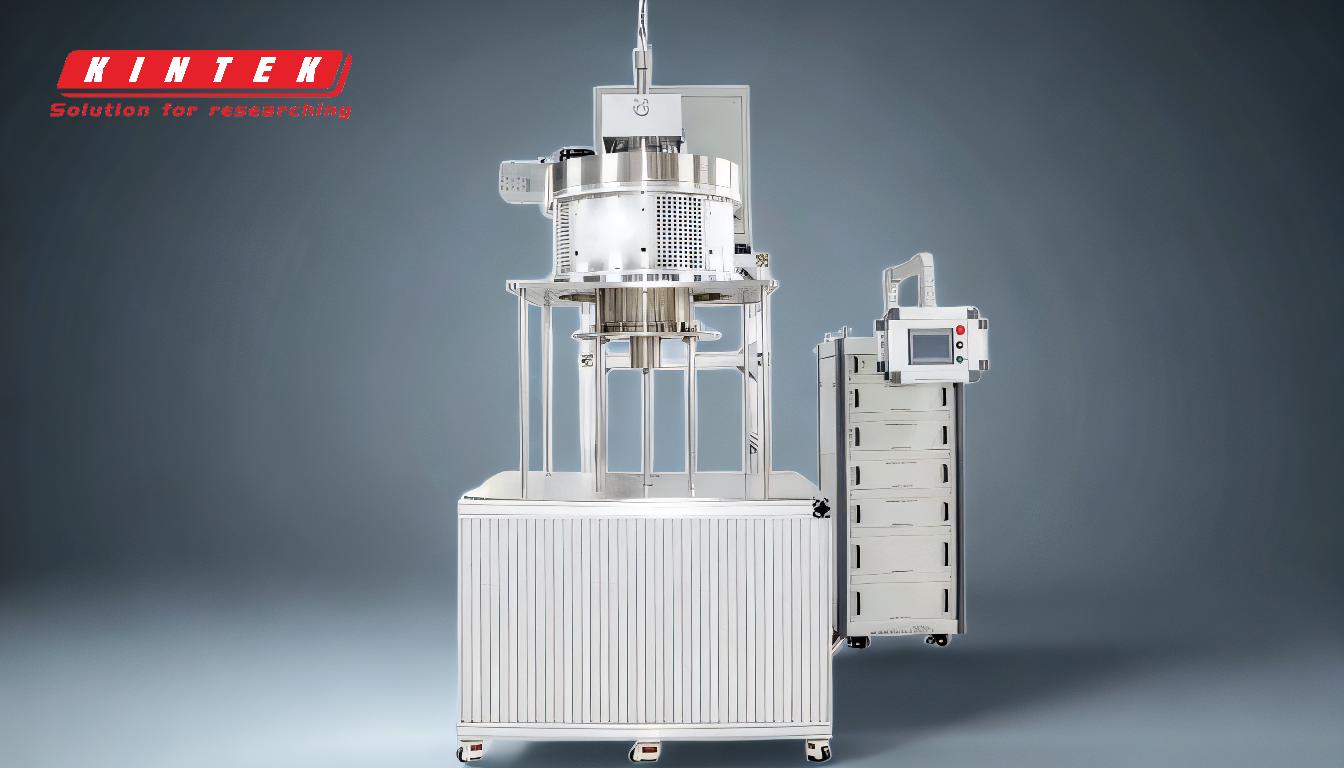
-
High Operating Temperatures:
- CVD typically operates at high temperatures, which can cause thermal instability in many substrates. This is particularly problematic for materials that cannot withstand high heat, limiting the range of materials that can be processed using CVD.
-
Toxic and Dangerous Precursors:
- The process requires chemical precursors with high vapor pressure, which are often highly toxic and dangerous. Handling these precursors requires stringent safety measures, increasing the complexity and cost of the process.
-
Challenges in Synthesizing Multi-Component Materials:
- CVD faces difficulties in synthesizing multi-component materials due to variations in vapor pressure, nucleation, and growth rates during the gas-to-particle conversion. This results in heterogeneous composition of particles, which can be a significant drawback when uniformity is critical.
-
Environmental and Safety Concerns:
- The by-products of CVD are often toxic and corrosive, requiring neutralization, which can be both problematic and costly. This adds to the overall expense and environmental impact of the process.
-
Limitations in Coating Larger Surfaces:
- The size of the vacuum chamber used in CVD is limited, making it difficult to coat larger surfaces. This can be a significant limitation for applications requiring large-area coatings.
-
All-or-Nothing Process:
- CVD is an all-or-nothing process, meaning it is difficult to partially coat a material. This can be a drawback when selective coating is required.
-
On-Site Deposition Challenges:
- CVD usually cannot be performed on-site and must be delivered to a coating center. This can be inconvenient and costly, especially for large or complex parts that need to be transported.
-
Economic Considerations:
- While CVD is relatively economical in terms of coating numerous parts simultaneously, the overall cost can be high due to the need for specialized equipment, safety measures, and waste neutralization.
In summary, while CVD offers many advantages, its key disadvantages include high operating temperatures, the need for toxic precursors, challenges in synthesizing multi-component materials, and environmental and safety concerns. These factors must be carefully considered when choosing CVD as a thin film deposition method. For more information on related processes, you can explore short path vacuum distillation.
Summary Table:
Disadvantage | Description |
---|---|
High Operating Temperatures | Limits use with thermally sensitive substrates due to thermal instability. |
Toxic and Dangerous Precursors | Requires stringent safety measures, increasing complexity and cost. |
Challenges in Multi-Component Materials | Difficulty in achieving uniform composition due to vapor pressure and growth rate variations. |
Environmental and Safety Concerns | Toxic by-products require neutralization, adding to cost and environmental impact. |
Limitations in Coating Larger Surfaces | Restricted by the size of the vacuum chamber, making large-area coatings difficult. |
All-or-Nothing Process | Partial coating is challenging, limiting selective coating applications. |
On-Site Deposition Challenges | Requires transportation to coating centers, increasing inconvenience and cost. |
Economic Considerations | High overall costs due to specialized equipment, safety measures, and waste neutralization. |
Need help navigating the challenges of CVD? Contact our experts today for tailored solutions!