PVD (Physical Vapor Deposition) coating is a versatile process used to apply thin films of various materials onto substrates to enhance their properties such as hardness, wear resistance, and corrosion resistance. The materials used for PVD coatings are diverse, ranging from metals and alloys to ceramics and specialized compounds. Common materials include titanium, zirconium, aluminum, stainless steel, copper, and gold, with gold being particularly important in aerospace electronics. Additionally, specialized coatings like TiN (Titanium Nitride), Cr2N (Chromium Nitride), ZnSn (Zinc Tin), AlCr (Aluminum Chromium), and ITO (Indium Tin Oxide) are widely used in various industries for their unique properties. These coatings can be applied to a variety of substrates, including metals, plastics, glass, and ceramics, making PVD a highly adaptable and widely used technology.
Key Points Explained:
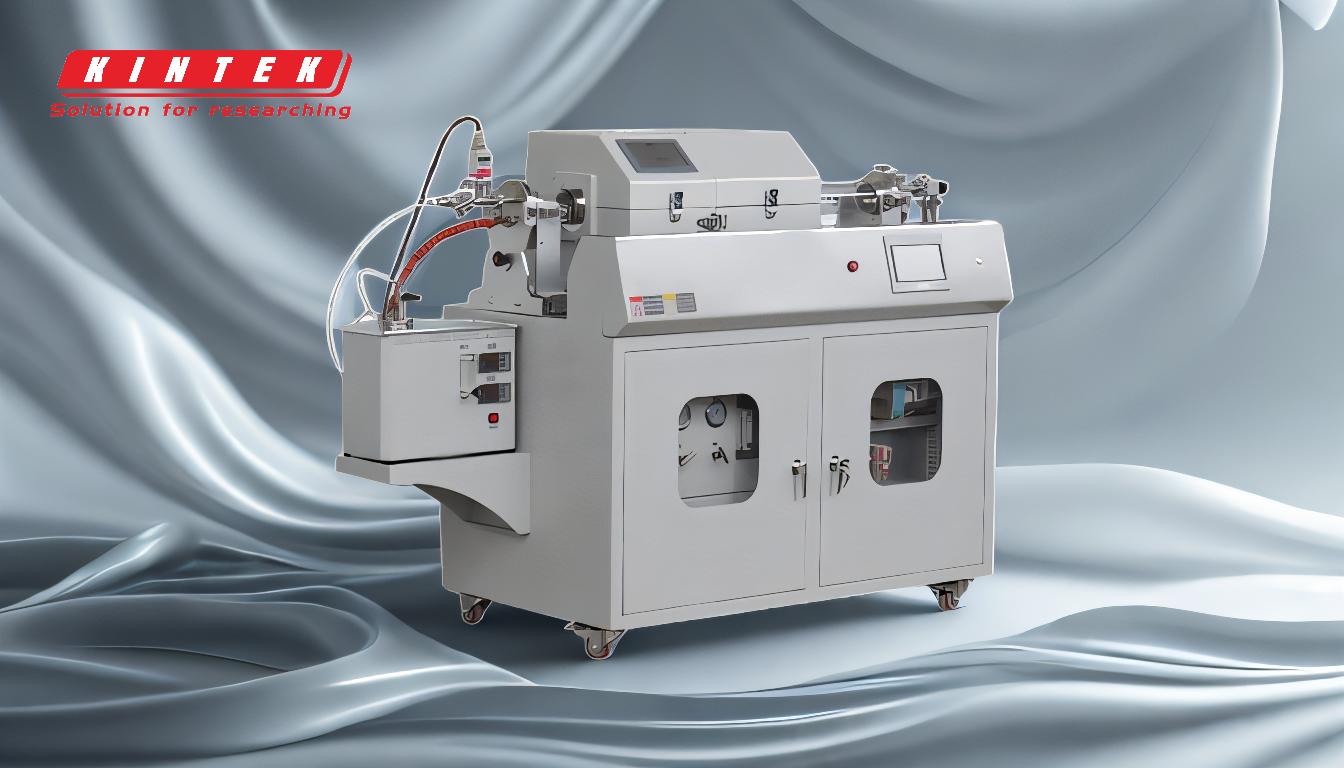
-
Common PVD Coating Materials:
- Titanium (Ti): Widely used for its excellent hardness and corrosion resistance. Often used in the form of Titanium Nitride (TiN), which is popular for decorative and functional applications.
- Zirconium (Zr): Known for its high resistance to wear and corrosion, often used in demanding environments.
- Aluminum (Al): Used for its lightweight and corrosion-resistant properties, often in combination with other elements.
- Stainless Steel: Provides durability and resistance to corrosion, often used in industrial applications.
- Copper (Cu): Used for its excellent electrical conductivity, often in electronic applications.
- Gold (Au): Highly valued in aerospace and electronics for its superior conductivity and resistance to corrosion.
-
Specialized PVD Coating Materials:
- Cr2N (Chromium Nitride): Used in watches and jewelry for its decorative appeal and durability.
- TiN (Titanium Nitride): Commonly used for decorative purposes on items like phones, glasses, and hardware parts, as well as for its hardness and wear resistance.
- ZnSn (Zinc Tin): An optical coating used in low-emissivity (low-e) windows and glass to improve energy efficiency.
- AlCr (Aluminum Chromium): Extends the service life of tools and machine parts by providing enhanced wear resistance.
- ITO (Indium Tin Oxide): A high-conductivity, high-hardness film used in LCDs, plasma displays, and touch panels.
-
Substrates for PVD Coatings:
- Metals: Stainless steel, aluminum, and brass are common substrates due to their compatibility with PVD processes.
- Plastics: ABS plastic and other polymers can be coated with PVD films, often after pre-treatment to ensure adhesion.
- Glass and Ceramics: These materials are often coated for optical and decorative applications.
- Other Materials: Zinc and other metals can also be used as substrates, depending on the application.
-
Pre-Treatment of Substrates:
- Substrates often require pre-treatment to ensure they are vacuum-compatible and to improve adhesion of the PVD coating. Common pre-treatments include organic coatings or electroplating with nickel and chromium.
-
Applications of PVD Coatings:
- Aerospace: Gold and other specialized coatings are used for their high conductivity and resistance to harsh environments.
- Automotive: Coatings like AlCr and TiN are used to enhance the durability and performance of engine parts and tools.
- Electronics: ITO and other conductive coatings are essential for display technologies and touch panels.
- Decorative: Cr2N and TiN are used in jewelry, watches, and consumer electronics for their aesthetic appeal and durability.
-
Performance Requirements:
- Different industries have specific performance requirements for PVD coatings. For example, aerospace and automotive industries often require coatings with high wear resistance and thermal stability, while the electronics industry prioritizes conductivity and optical properties.
In summary, PVD coating materials are selected based on the desired properties and the specific application. The versatility of PVD allows it to be used across a wide range of industries, from aerospace and automotive to electronics and decorative applications. The choice of material and substrate, along with proper pre-treatment, ensures that the final product meets the required performance standards.
Summary Table:
Category | Materials | Key Properties | Applications |
---|---|---|---|
Common Materials | Titanium (Ti), Zirconium (Zr), Aluminum (Al), Stainless Steel, Copper (Cu), Gold (Au) | Hardness, corrosion resistance, wear resistance, conductivity, lightweight | Aerospace, electronics, industrial, decorative |
Specialized Coatings | Cr2N, TiN, ZnSn, AlCr, ITO | Decorative appeal, wear resistance, optical efficiency, conductivity, durability | Watches, jewelry, low-e windows, tools, LCDs, touch panels |
Substrates | Metals, plastics, glass, ceramics | Compatibility, adhesion, durability | Automotive, electronics, decorative, optical applications |
Unlock the potential of PVD coatings for your industry—contact our experts today to learn more!