When selecting a mill for weight grinding, the choice depends on factors such as the material being ground, the desired particle size, throughput requirements, and the specific application. For weight grinding, where precision and consistency are critical, ball mills and vibratory mills are often preferred. Ball mills are versatile and effective for fine grinding, while vibratory mills offer higher energy efficiency and faster grinding times. Jet mills are ideal for ultrafine grinding but may not be suitable for all materials. The decision should also consider operational costs, maintenance, and the potential for contamination. Below, we explore the key factors and options in detail.
Key Points Explained:
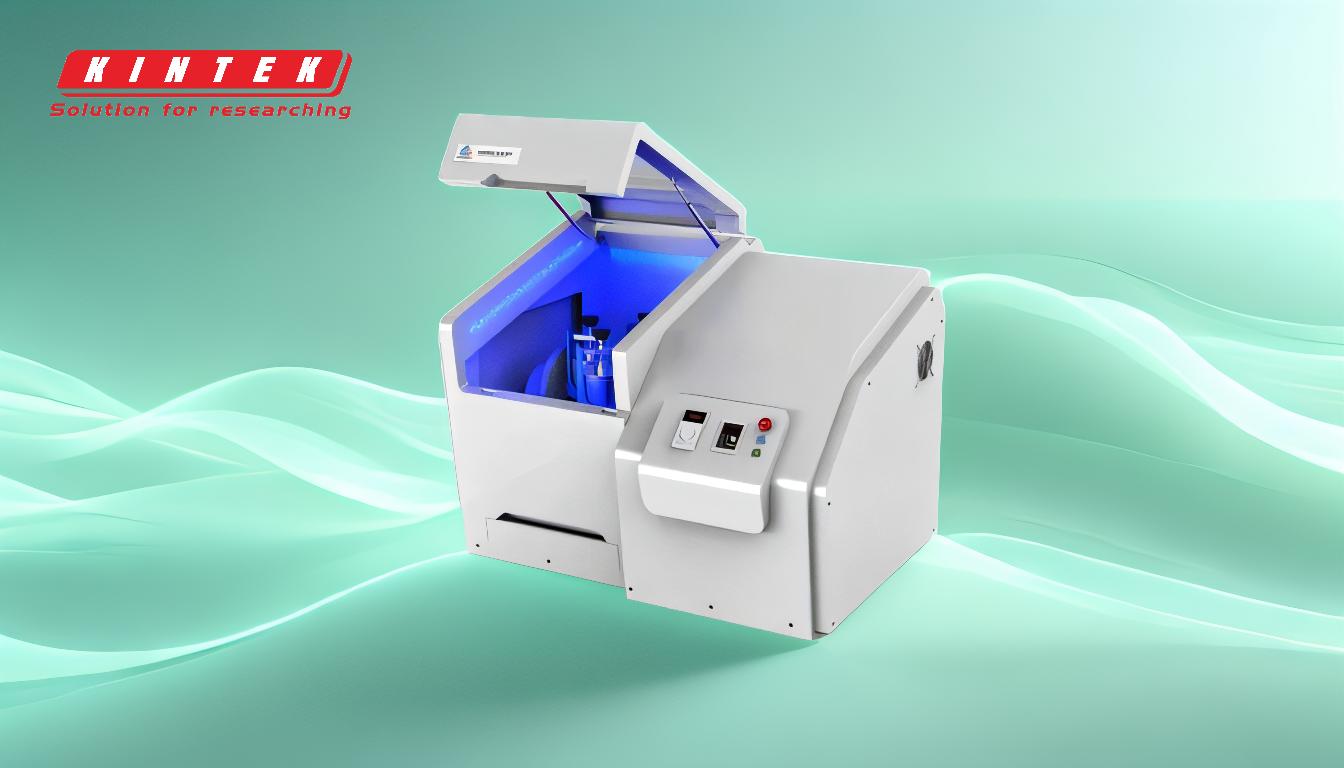
-
Types of Mills Suitable for Weight Grinding
-
Ball Mills:
- Use rotating cylinders with grinding media (e.g., steel balls) to grind materials.
- Ideal for fine and ultrafine grinding of hard, brittle, and fibrous materials.
- Provide consistent particle size distribution, making them suitable for weight-critical applications.
-
Vibratory Mills:
- Use high-frequency vibrations to grind materials with minimal energy consumption.
- Faster grinding times compared to ball mills.
- Suitable for small-scale operations where precision is required.
-
Jet Mills:
- Use high-speed jets of air or gas to grind materials into ultrafine particles.
- Best for heat-sensitive or brittle materials.
- May not be ideal for weight grinding due to potential variations in particle size distribution.
-
Ball Mills:
-
Factors to Consider When Choosing a Mill
-
Material Properties:
- Hardness, brittleness, and moisture content of the material influence the choice of mill.
- For example, ball mills are better suited for hard materials, while jet mills work well with brittle materials.
-
Desired Particle Size:
- Ball mills and vibratory mills are excellent for achieving fine and consistent particle sizes.
- Jet mills are preferred for ultrafine grinding but may not provide the same consistency.
-
Throughput Requirements:
- Ball mills are suitable for high-capacity operations.
- Vibratory mills are better for smaller-scale, precision-focused tasks.
-
Operational Costs:
- Vibratory mills are energy-efficient but may have higher initial costs.
- Ball mills are cost-effective for large-scale operations but require regular maintenance.
-
Contamination Risks:
- Ball mills with ceramic or stainless steel grinding media reduce contamination risks.
- Jet mills are contamination-free but may not be suitable for all materials.
-
Material Properties:
-
Applications of Weight Grinding
-
Pharmaceuticals:
- Precision grinding is critical for drug formulation and dosage accuracy.
- Vibratory mills are often used for their consistency and low contamination risks.
-
Ceramics and Glass:
- Ball mills are preferred for grinding ceramic powders to precise sizes.
-
Metallurgy:
- Ball mills are used for grinding ores and metals to specific weights for further processing.
-
Food Industry:
- Jet mills are used for grinding heat-sensitive food products without altering their properties.
-
Pharmaceuticals:
-
Advantages and Disadvantages of Each Mill Type
-
Ball Mills:
- Advantages: Versatile, cost-effective, and capable of fine grinding.
- Disadvantages: High energy consumption and potential for contamination.
-
Vibratory Mills:
- Advantages: Energy-efficient, fast grinding, and precise particle size control.
- Disadvantages: Higher initial cost and limited capacity.
-
Jet Mills:
- Advantages: Contamination-free, suitable for heat-sensitive materials.
- Disadvantages: Higher operational costs and less consistent particle size distribution.
-
Ball Mills:
-
Recommendations for Weight Grinding
- For general-purpose weight grinding with high throughput, ball mills are the most versatile and cost-effective option.
- For precision grinding in small-scale operations, vibratory mills are preferred due to their efficiency and consistency.
- For ultrafine grinding of brittle or heat-sensitive materials, jet mills are ideal, but their suitability for weight grinding depends on the specific application.
By carefully evaluating the material properties, desired outcomes, and operational constraints, you can choose the most appropriate mill for your weight grinding needs.
Summary Table:
Factor | Ball Mills | Vibratory Mills | Jet Mills |
---|---|---|---|
Material Suitability | Hard, brittle, fibrous materials | Small-scale, precision tasks | Brittle, heat-sensitive materials |
Particle Size | Fine and consistent | Fine and consistent | Ultrafine, less consistent |
Throughput | High-capacity operations | Small-scale operations | Moderate throughput |
Operational Costs | Cost-effective, high maintenance | Energy-efficient, higher initial cost | Higher operational costs |
Contamination Risks | Low with ceramic/stainless steel media | Low contamination risks | Contamination-free |
Need help choosing the right mill for your weight grinding needs? Contact our experts today for personalized advice!