The synthesis of Carbon Nanotubes (CNTs) involves the use of specific metals as catalysts, which play a crucial role in the growth and structure of the nanotubes. Common metals used as catalysts include iron (Fe), nickel (Ni), cobalt (Co), and sometimes molybdenum (Mo) or a combination of these metals. These catalysts are typically supported on substrates like silicon or alumina to enhance their efficiency. The choice of catalyst and its preparation significantly influence the quality, yield, and type (single-walled or multi-walled) of CNTs produced. The process often involves chemical vapor deposition (CVD), where the metal catalyst facilitates the decomposition of carbon-containing gases into carbon atoms that form the nanotubes.
Key Points Explained:
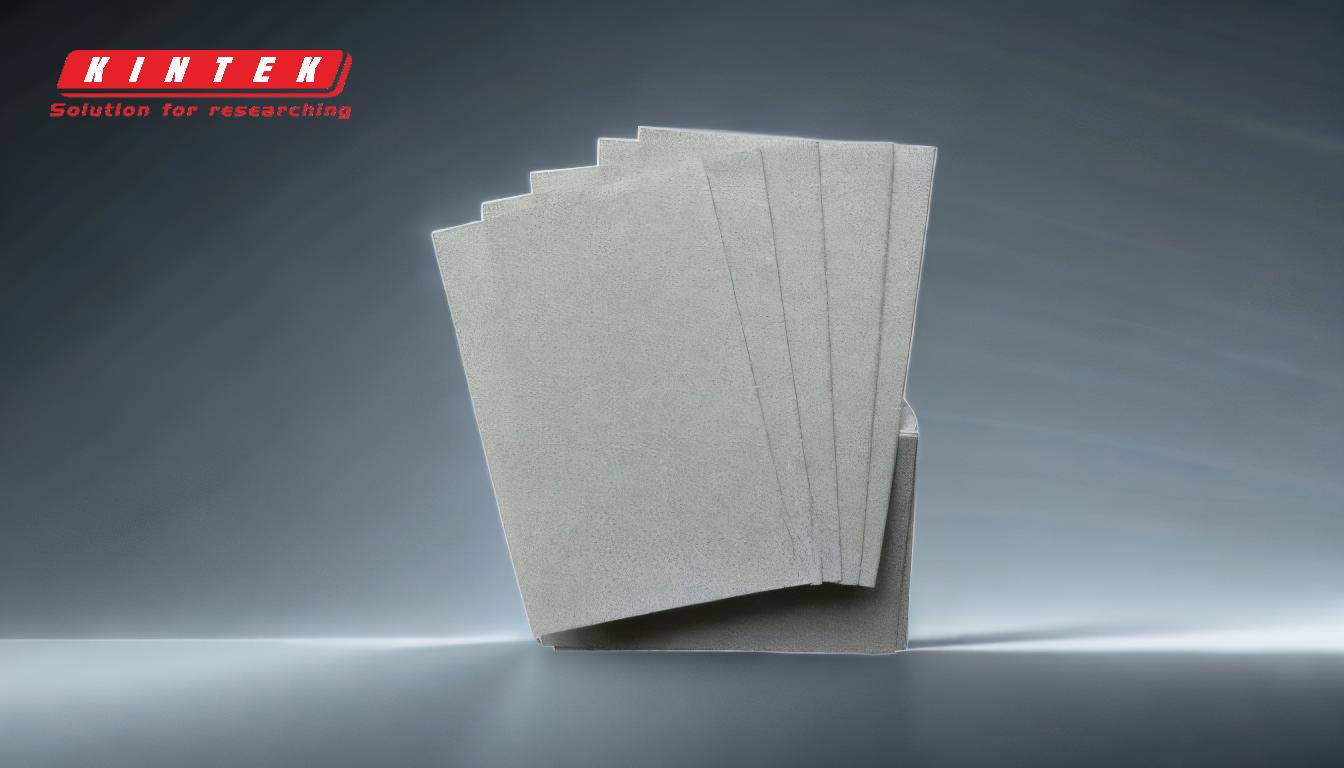
-
Common Catalytic Metals:
- Iron (Fe): Iron is one of the most widely used catalysts for CNT synthesis. It is effective in promoting the growth of both single-walled carbon nanotubes (SWCNTs) and multi-walled carbon nanotubes (MWCNTs). Iron nanoparticles are often used due to their high catalytic activity and ability to control the diameter of the nanotubes.
- Nickel (Ni): Nickel is another popular catalyst, particularly for the synthesis of MWCNTs. It has a high carbon solubility, which allows for efficient carbon diffusion and nanotube growth. Nickel is often used in combination with other metals to enhance its catalytic properties.
- Cobalt (Co): Cobalt is known for its effectiveness in producing high-quality SWCNTs. It has a moderate carbon solubility and can be used to control the chirality of the nanotubes, which is crucial for their electronic properties.
- Molybdenum (Mo): Molybdenum is less commonly used but can be effective, especially when combined with other metals like iron or cobalt. It is often used in bimetallic catalysts to improve the yield and quality of CNTs.
-
Catalyst Preparation and Support:
- The preparation of the catalyst is critical for the successful synthesis of CNTs. The metal catalysts are often deposited on a substrate such as silicon dioxide (SiO2) or alumina (Al2O3) to provide a stable surface for nanotube growth.
- The size and distribution of the catalyst particles on the substrate are crucial. Smaller, well-dispersed particles tend to produce nanotubes with more uniform diameters and fewer defects.
- The choice of substrate can also influence the growth process. For example, alumina is often preferred for its thermal stability and ability to support high-density nanotube growth.
-
Chemical Vapor Deposition (CVD) Process:
- The CVD process is the most common method for synthesizing CNTs. In this process, a carbon-containing gas (such as methane or ethylene) is introduced into a reaction chamber where it decomposes on the surface of the metal catalyst at high temperatures (typically between 600°C and 1000°C).
- The metal catalyst facilitates the decomposition of the carbon gas, allowing carbon atoms to diffuse and form the hexagonal lattice structure of the nanotubes. The catalyst particles remain at the tips or bases of the growing nanotubes, depending on the growth mechanism (tip-growth or base-growth).
-
Influence of Catalyst on CNT Properties:
- The choice of catalyst can significantly influence the properties of the synthesized CNTs, including their diameter, length, chirality, and whether they are single-walled or multi-walled.
- For example, iron catalysts are known to produce nanotubes with a wide range of diameters, while cobalt catalysts are more effective in producing narrow-diameter SWCNTs with specific chiralities.
- The catalyst's ability to control the chirality of the nanotubes is particularly important for applications in electronics, where the electronic properties of the nanotubes are determined by their chirality.
-
Bimetallic Catalysts:
- In some cases, bimetallic catalysts (combinations of two metals) are used to enhance the catalytic activity and control the growth of CNTs. For example, a combination of iron and cobalt can be used to produce high-quality SWCNTs with controlled chirality.
- Bimetallic catalysts can also improve the yield and uniformity of the nanotubes by providing a more stable and active surface for carbon decomposition and diffusion.
In summary, the synthesis of CNTs relies heavily on the use of specific metal catalysts, with iron, nickel, cobalt, and molybdenum being the most common. The preparation and choice of catalyst, along with the CVD process, play a critical role in determining the quality, yield, and properties of the resulting nanotubes. Understanding the role of these catalysts is essential for optimizing the synthesis process and tailoring CNTs for specific applications.
Summary Table:
Catalyst | Role in CNT Synthesis | Key Properties |
---|---|---|
Iron (Fe) | Promotes SWCNT and MWCNT growth | High catalytic activity, controls nanotube diameter |
Nickel (Ni) | Effective for MWCNT synthesis | High carbon solubility, enhances catalytic properties |
Cobalt (Co) | Produces high-quality SWCNTs | Controls chirality, moderate carbon solubility |
Molybdenum (Mo) | Used in bimetallic catalysts | Improves yield and quality of CNTs |
Optimize your CNT synthesis process with the right catalysts—contact our experts today!