Physical Vapor Deposition (PVD) techniques are widely used to deposit thin films with high purity and performance. Among the various PVD methods, sputtering and evaporation are the most commonly compared for film purity. Sputtering, particularly magnetron sputtering, is often considered superior for achieving high-purity films due to its ability to operate in a controlled environment with minimal contamination. Evaporation, while capable of high-purity deposition, can sometimes introduce impurities due to the heating process. The choice of technique depends on the specific application, material, and desired film properties.
Key Points Explained:
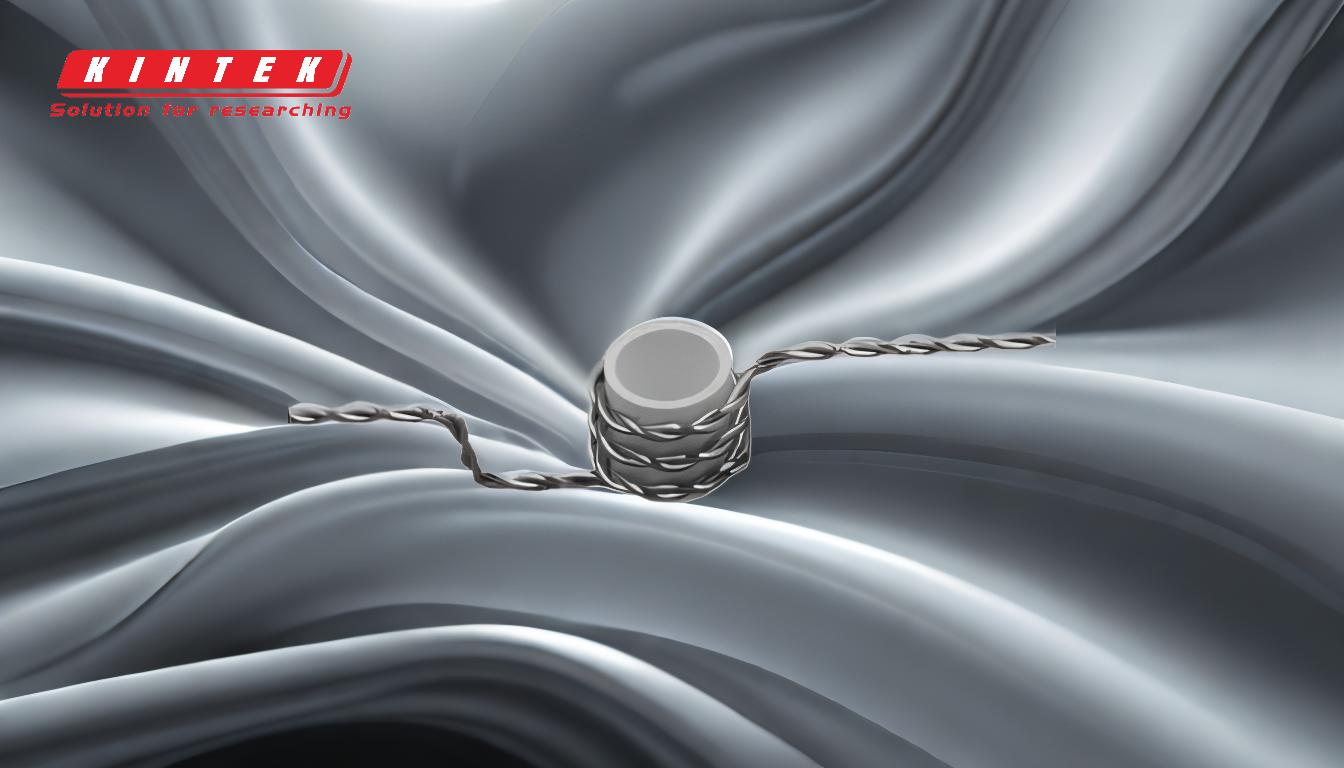
-
Overview of PVD Techniques:
- PVD involves depositing thin films by physically transferring material from a source to a substrate in a vacuum environment.
- Common PVD techniques include sputtering and evaporation, each with unique advantages and limitations.
-
Sputtering for High-Purity Films:
- Sputtering, especially magnetron sputtering, is highly effective for depositing high-purity films.
- The process involves bombarding a target material with ions, causing atoms to be ejected and deposited onto the substrate.
- Advantages:
- Operates in a high-vacuum environment, minimizing contamination.
- Suitable for a wide range of materials, including metals, alloys, and ceramics.
- Allows precise control over film composition and thickness.
- Disadvantages:
- Higher equipment and operational costs compared to evaporation.
- Slower deposition rates in some cases.
-
Evaporation for High-Purity Films:
- Evaporation involves heating a material until it vaporizes and then condenses onto the substrate.
- Techniques like electron beam evaporation and thermal evaporation are commonly used.
- Advantages:
- High deposition rates.
- Simpler and more cost-effective for certain materials.
- Disadvantages:
- Potential for contamination due to heating elements or crucibles.
- Limited to materials with lower melting points.
-
Factors Influencing Film Purity:
- Vacuum Quality: Higher vacuum levels reduce the presence of contaminants.
- Target Material: High-purity targets yield high-purity films.
- Process Control: Precise control over parameters like temperature, pressure, and deposition rate is critical.
- Substrate Preparation: Clean and well-prepared substrates minimize impurities.
-
Comparison of Sputtering and Evaporation:
- Purity: Sputtering generally offers better purity due to its controlled environment and ability to handle a wider range of materials.
- Application Suitability: Sputtering is preferred for complex materials and multi-layer films, while evaporation is ideal for simpler, high-rate depositions.
- Cost and Complexity: Sputtering systems are more expensive and complex, but they provide greater flexibility and control.
-
Conclusion:
- For applications requiring high-purity films, sputtering, particularly magnetron sputtering, is often the preferred PVD technique due to its superior control over contamination and material versatility.
- Evaporation can also achieve high purity but is more limited by material compatibility and potential contamination sources.
- The choice between sputtering and evaporation ultimately depends on the specific requirements of the application, including material type, film properties, and budget constraints.
Summary Table:
Aspect | Sputtering | Evaporation |
---|---|---|
Purity | Superior due to controlled environment and minimal contamination. | High purity possible but prone to contamination from heating elements. |
Material Versatility | Suitable for metals, alloys, and ceramics. | Limited to materials with lower melting points. |
Deposition Rate | Slower in some cases. | Higher deposition rates. |
Cost and Complexity | Higher equipment and operational costs. | Simpler and more cost-effective for certain materials. |
Application Suitability | Preferred for complex materials and multi-layer films. | Ideal for simpler, high-rate depositions. |
Need help choosing the right PVD technique for your application? Contact our experts today!