Biochar production involves various reactor configurations, each with unique advantages depending on the desired yield, quality, and operational efficiency. The choice of reactor is influenced by factors such as heat transfer mechanisms, solids handling, and mixing efficiency. Key reactor types include fixed bed, fluidized bed, and rotary kiln, each suited to specific production goals. The highest treatment temperature (HTT), heating rate, and residence time are critical parameters affecting biochar properties. Slow pyrolysis, often using fixed-bed reactors, is preferred for high biochar yield, while fast pyrolysis, utilizing fluidized bed or rotary kiln reactors, is better for maximizing bio-oil production.
Key Points Explained:
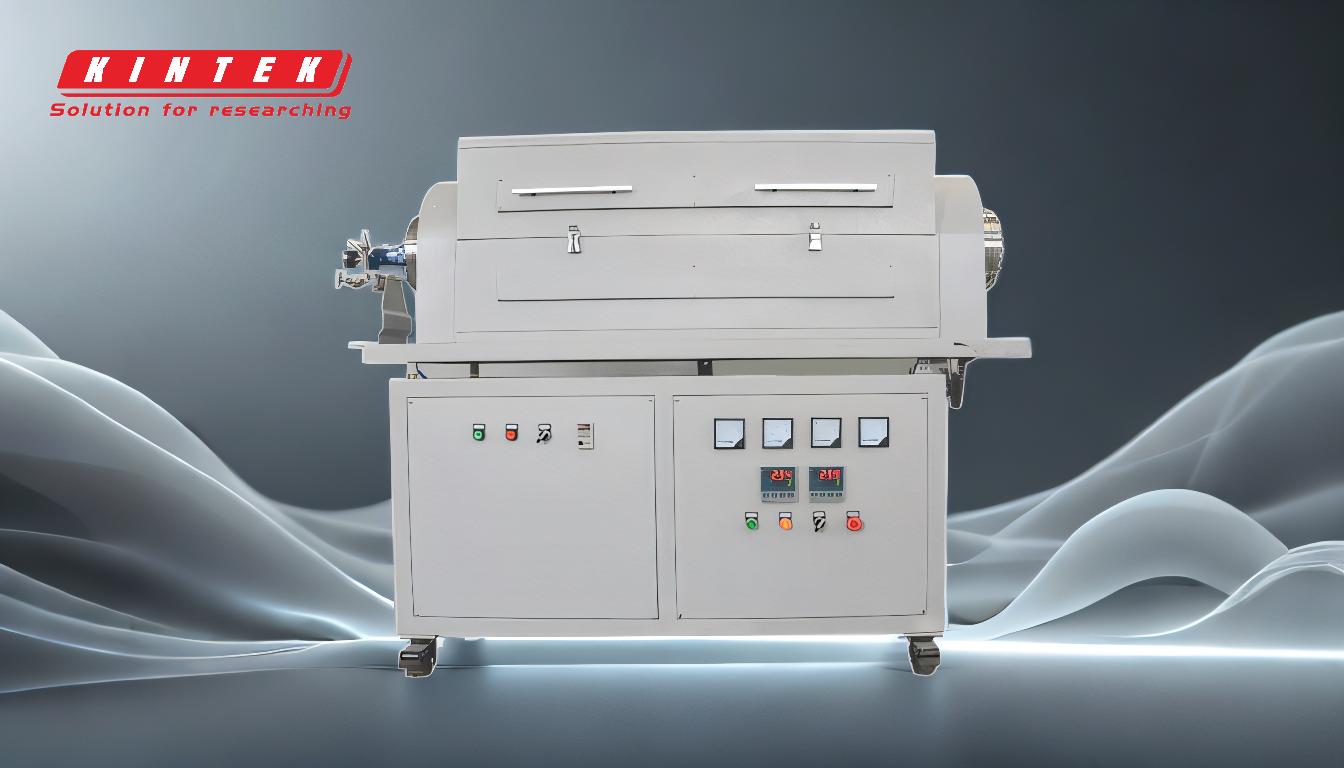
-
Reactor Configurations in Biochar Production:
- Fixed Bed Reactors: Commonly used in slow pyrolysis, these reactors are simple and cost-effective. The biomass is loaded into a stationary chamber, and heat is applied externally. This configuration is ideal for high biochar yield and is often used for wood feedstock.
- Fluidized Bed Reactors: These reactors provide excellent heat transfer and mixing, making them suitable for fast pyrolysis. They are efficient for producing bio-oil and syngas but may yield less biochar compared to fixed bed reactors.
- Rotary Kiln Reactors: These reactors are versatile and can handle a variety of feedstocks. The efficiency of a rotary kiln is influenced by the speed of rotation and heat supply, making it suitable for continuous feed systems.
-
Factors Influencing Biochar Yield and Properties:
- Highest Treatment Temperature (HTT): HTT is the most significant factor affecting biochar properties. Higher temperatures generally result in biochar with higher carbon content and lower volatile matter.
- Heating Rate: Faster heating rates are associated with fast pyrolysis, which favors the production of bio-oil and gas. Slower heating rates, typical of slow pyrolysis, favor biochar production.
- Residence Time: Longer residence times in the reactor allow for more complete decomposition of biomass, affecting the yield and quality of biochar.
-
Operational Considerations:
- Heat Transfer and Mixing: Efficient heat transfer and mixing are crucial for uniform pyrolysis and optimal product yield. Fluidized bed reactors excel in this aspect due to their design.
- Solids Handling: The ability to handle and process different types of biomass feedstocks is a critical consideration. Rotary kiln reactors are particularly adept at handling diverse feedstocks.
-
Preferred Reactor Configuration:
- For high biochar yield, slow pyrolysis using fixed bed reactors is preferred due to its simplicity and effectiveness.
- For maximizing bio-oil production, fast pyrolysis using fluidized bed reactors is more suitable.
- For versatility and continuous operation, rotary kiln reactors are advantageous, especially when dealing with varied feedstocks.
In summary, the choice of reactor configuration in biochar production depends on the specific goals of the process, whether prioritizing biochar yield, bio-oil production, or operational flexibility. Each reactor type offers distinct benefits and is selected based on the desired end products and operational requirements.
Summary Table:
Reactor Type | Key Features | Best Use Case |
---|---|---|
Fixed Bed | Simple, cost-effective, high biochar yield | Slow pyrolysis for high biochar |
Fluidized Bed | Excellent heat transfer, high bio-oil yield | Fast pyrolysis for bio-oil |
Rotary Kiln | Versatile, handles diverse feedstocks | Continuous operation, flexibility |
Ready to optimize your biochar production? Contact our experts today for tailored solutions!