Hydrogenation reactors are specialized equipment designed to facilitate the chemical reaction of hydrogen with other compounds, typically in the presence of a catalyst. The two primary types of industrial hydrogenation reactors are Batch Hydrogenation Reactors and Continuous Flow/Tubular/Fixed Bed Reactors. Batch reactors are large, pressurized vessels equipped with heating elements and agitators, making them suitable for processes like the hydrogenation of edible fats and pharmaceuticals. Continuous flow reactors, on the other hand, are tube-shaped with fixed catalyst beds and are commonly used in petroleum purification and pharmaceutical manufacturing. The choice of reactor depends on factors such as the scale of production, the nature of the reactants, and the desired reaction conditions.
Key Points Explained:
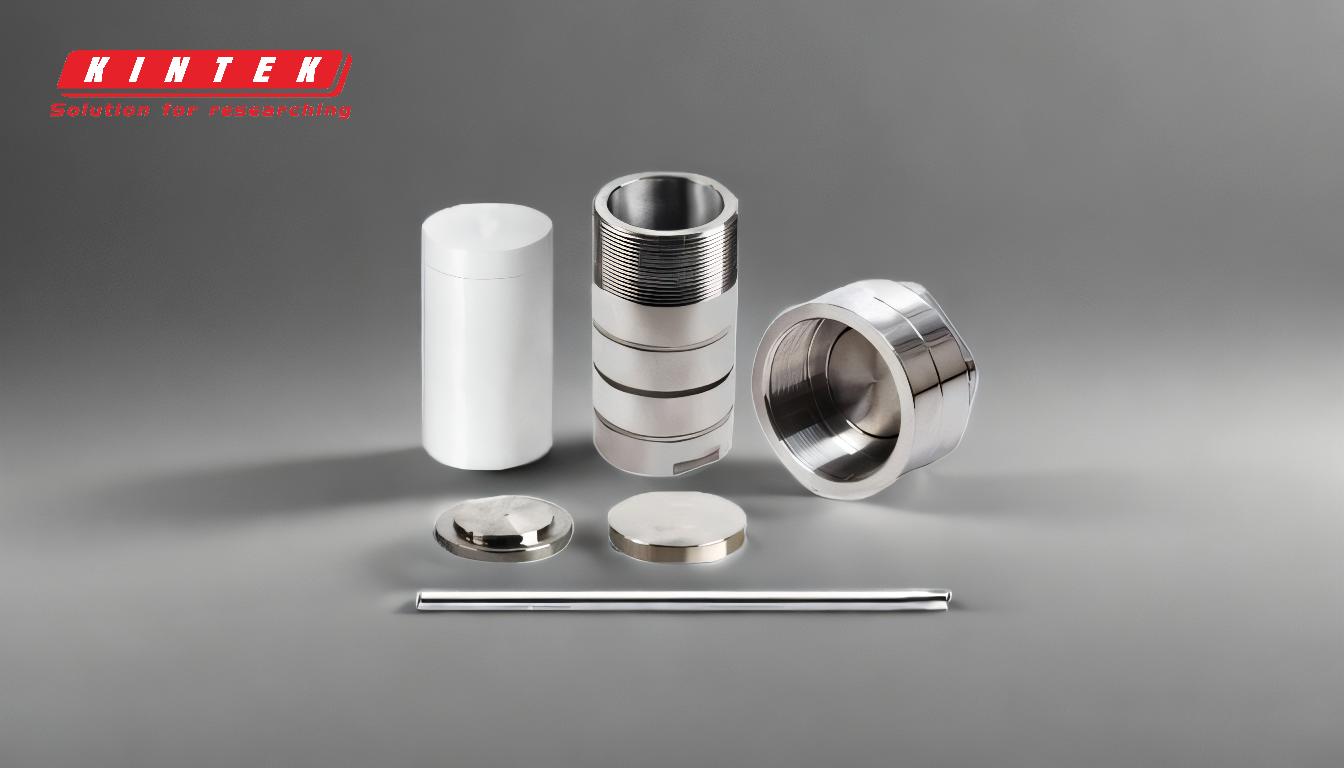
-
Types of Hydrogenation Reactors:
- Batch Hydrogenation Reactors: These are large, pressurized vessels that operate in a batch-wise manner. They are equipped with heating elements and agitators to ensure uniform mixing and temperature control. Batch reactors are commonly used in industries such as food (e.g., hydrogenation of edible fats) and pharmaceuticals, where precise control over reaction conditions is crucial.
- Continuous Flow/Tubular/Fixed Bed Reactors: These reactors are designed for continuous operation, with reactants flowing through a tube-shaped vessel containing a fixed bed of catalyst. They are particularly suited for large-scale industrial processes like petroleum purification and pharmaceutical manufacturing, where continuous production is required.
-
Catalysts Used in Hydrogenation:
- Common Catalysts: Metals such as nickel, platinum, and palladium, as well as their oxides, are widely used as catalysts in hydrogenation reactions. These catalysts are chosen for their ability to facilitate the addition of hydrogen to unsaturated compounds.
- High-Pressure Catalysts: For high-pressure hydrogenation reactions, copper chromite and nickel supported on kieselguhr are extensively used. These catalysts are effective under the high-pressure conditions often required for hydrogenation processes.
-
Reactor Design and Features:
- Pressure Reactors and Gas Dosing Systems: The combination of a pressure reactor and a gas dosing system is considered optimal for hydrogenation reactions. This setup ensures safe, accurate, and reproducible reactions by controlling the pressure and flow of hydrogen gas.
- Glass Reactors in Laboratories: In laboratory settings, glass reactors, such as glass jacketed reactors and filter reactors, are commonly used. These reactors are ideal for small-scale experiments and provide excellent visibility of the reaction process.
-
Applications of Hydrogenation Reactors:
- Edible Fats and Pharmaceuticals: Batch reactors are frequently used for the hydrogenation of edible fats, a process that converts liquid oils into semi-solid fats. They are also used in the pharmaceutical industry for the synthesis of various drugs.
- Petroleum Purification: Continuous flow reactors are essential in the petroleum industry for the purification of fuels and other petroleum products through hydrogenation.
-
Comparison with Other Reactor Types:
- Pyrolysis Reactors: While not directly related to hydrogenation, pyrolysis reactors (e.g., fluidized bed, fixed bed, rotary cylinder) are used for thermal decomposition of materials in the absence of oxygen. These reactors operate under different principles and are used for processes like biomass conversion and waste treatment.
- Other Chemical Reactors: Reactors like Plug Flow Reactors, Continuous Stirred-tank Reactors, and Loop Reactors are used for various chemical processes but are not specifically designed for hydrogenation. Each reactor type has its own set of applications and operational characteristics.
-
Safety and Control in Hydrogenation Reactors:
- Safety Considerations: Hydrogenation reactions often involve high pressures and flammable gases, making safety a critical concern. Reactors are designed with safety features such as pressure relief valves and gas monitoring systems to prevent accidents.
- Process Control: Precise control over temperature, pressure, and gas flow is essential for successful hydrogenation. Modern reactors are equipped with advanced control systems to maintain optimal reaction conditions.
In summary, the choice of hydrogenation reactor depends on the specific requirements of the process, including the scale of production, the nature of the reactants, and the desired reaction conditions. Batch reactors are ideal for small-scale, precise operations, while continuous flow reactors are better suited for large-scale, continuous production. The use of appropriate catalysts and safety measures is also crucial for the successful implementation of hydrogenation processes.
Summary Table:
Aspect | Batch Reactors | Continuous Flow Reactors |
---|---|---|
Design | Large, pressurized vessels with heating elements and agitators | Tube-shaped with fixed catalyst beds |
Operation | Batch-wise | Continuous |
Applications | Hydrogenation of edible fats, pharmaceuticals | Petroleum purification, pharmaceutical manufacturing |
Catalysts | Nickel, platinum, palladium, copper chromite, nickel on kieselguhr | Same as batch reactors |
Safety Features | Pressure relief valves, gas monitoring systems | Advanced control systems for temperature, pressure, and gas flow |
Discover the right hydrogenation reactor for your needs—contact our experts today!