Density is a critical property in ceramics because it directly influences the material's mechanical strength, thermal conductivity, and overall performance. In fine ceramics, achieving high density is essential for ensuring durability, resistance to wear, and efficiency in applications like electronics, aerospace, and medical devices. High-density ceramics are less porous, which enhances their structural integrity and ability to withstand harsh environments. Additionally, density affects the material's ability to conduct heat and electricity, making it a key factor in optimizing performance for specific uses. Understanding and controlling density during the manufacturing process is vital for producing ceramics that meet the demanding requirements of modern industries.
Key Points Explained:
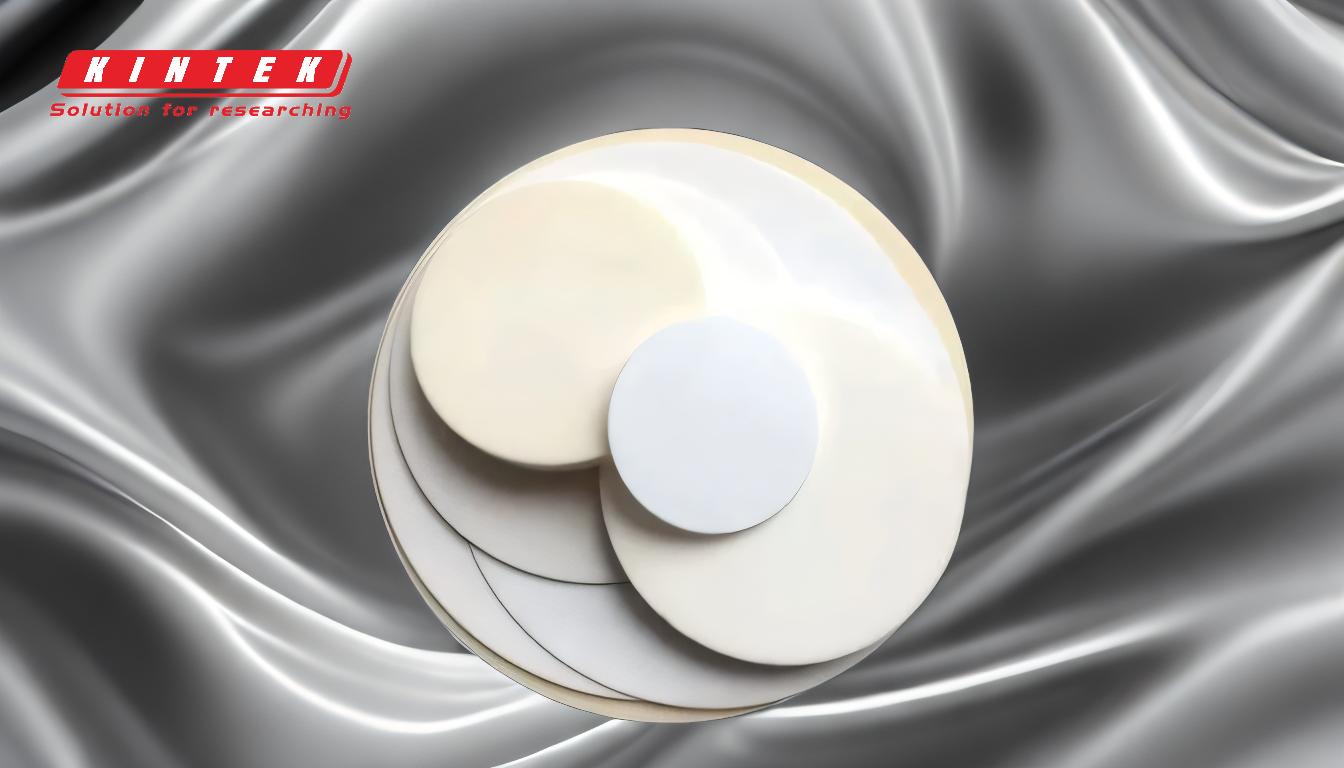
-
Mechanical Strength and Durability:
- High-density ceramics have fewer pores and defects, which significantly enhances their mechanical strength. This makes them more resistant to cracking, chipping, and wear, especially in high-stress applications.
- For example, in fine ceramics used in cutting tools or engine components, high density ensures that the material can withstand extreme mechanical forces without failing.
-
Thermal and Electrical Conductivity:
- Density plays a crucial role in determining how well a ceramic material can conduct heat or electricity. Higher density generally leads to better thermal conductivity, which is essential in applications like heat exchangers or electronic substrates.
- Conversely, lower-density ceramics with more porosity are often used as insulators, where thermal and electrical conductivity need to be minimized.
-
Resistance to Environmental Factors:
- High-density ceramics are less permeable to gases and liquids, making them more resistant to corrosion and chemical attack. This is particularly important in industries like chemical processing or medical implants, where exposure to harsh substances is common.
- The reduced porosity also prevents the absorption of moisture, which can degrade the material over time.
-
Optimization for Specific Applications:
- The density of ceramics can be tailored to meet the requirements of specific applications. For instance, in aerospace, lightweight yet strong ceramics are needed, while in industrial machinery, denser materials are preferred for their durability.
- By controlling the density during the manufacturing process, engineers can produce ceramics that are optimized for performance in their intended use.
-
Manufacturing Considerations:
- Achieving the desired density in ceramics requires precise control over the raw materials, sintering process, and other manufacturing parameters. Techniques like hot pressing or spark plasma sintering are often used to produce high-density ceramics.
- The choice of raw materials, such as fine powders with uniform particle size, also contributes to achieving higher density and better performance.
-
Impact on Cost and Efficiency:
- Higher-density ceramics may require more advanced manufacturing techniques and materials, which can increase production costs. However, the improved performance and longevity often justify the investment, especially in high-stakes applications.
- On the other hand, lower-density ceramics can be more cost-effective for applications where extreme durability is not required.
In summary, density is a fundamental property that influences the performance, durability, and suitability of ceramics for various applications. By understanding and controlling density, manufacturers can produce ceramics that meet the specific needs of industries ranging from electronics to aerospace.
Summary Table:
Aspect | Impact of High Density |
---|---|
Mechanical Strength | Fewer pores and defects enhance resistance to cracking, chipping, and wear. |
Thermal Conductivity | Higher density improves heat conduction, ideal for heat exchangers and electronic substrates. |
Environmental Resistance | Less permeable to gases and liquids, reducing corrosion and moisture absorption. |
Application Optimization | Tailored density ensures ceramics meet specific industry needs, from aerospace to medical. |
Manufacturing Techniques | Advanced methods like hot pressing achieve higher density for superior performance. |
Cost and Efficiency | Higher density may increase costs but offers better performance and longevity. |
Discover how high-density ceramics can enhance your applications—contact our experts today!