Pyrolysis and gasification are both thermal conversion processes used to transform organic materials into useful products, but they differ significantly in their mechanisms, outputs, and applications. Pyrolysis occurs in the absence of oxygen, producing bio-oil, bio-char, and syngas, while gasification involves partial oxidation with oxygen or steam, primarily yielding syngas. Pyrolysis is often considered better than gasification for specific applications due to its ability to produce high-value byproducts like bio-oil and bio-char, its simpler process conditions, and its lower environmental impact. However, gasification is more efficient for energy production and electricity generation. The choice between the two depends on the desired end products and specific use cases.
Key Points Explained:
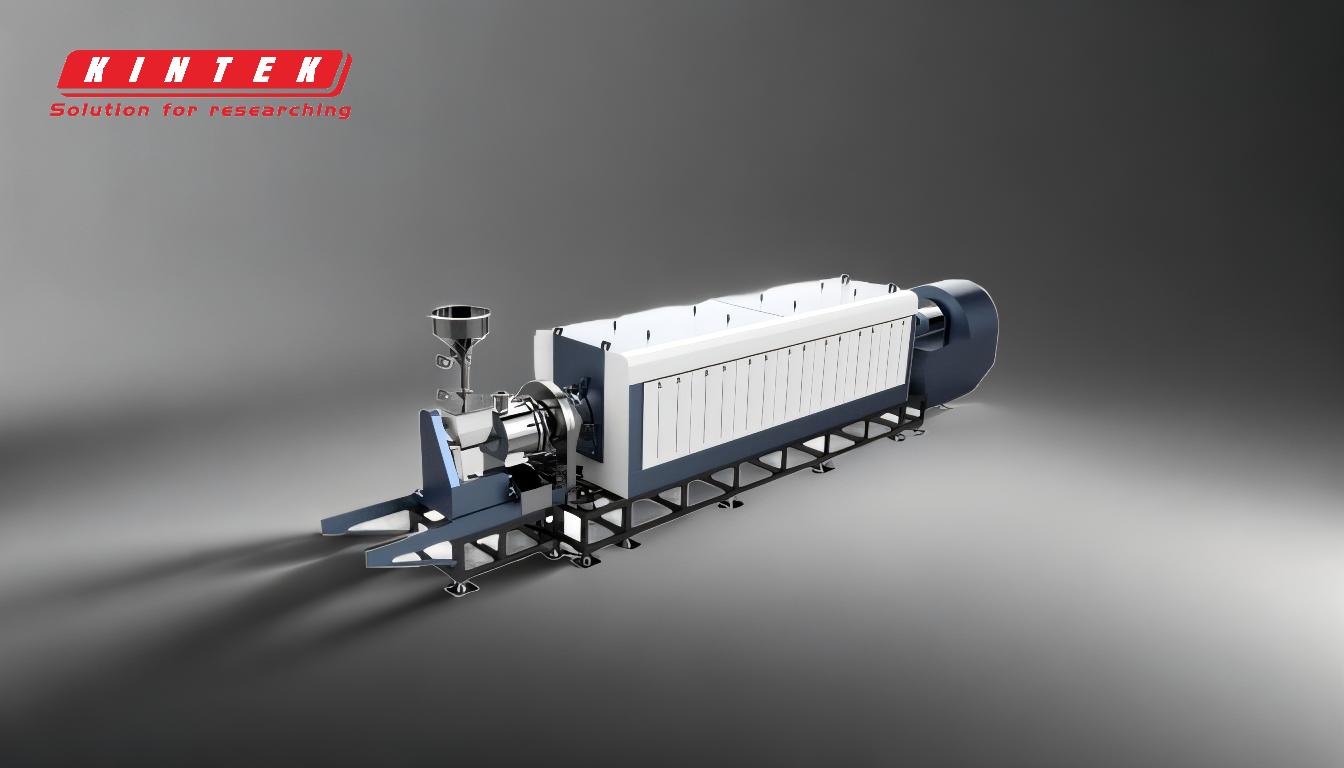
-
Process Conditions and Mechanism:
- Pyrolysis: Occurs in the complete absence of oxygen or with a limited supply, preventing oxidation. This process involves heating organic materials to high temperatures (typically 400–800°C) in an inert atmosphere, leading to the breakdown of complex molecules into simpler compounds. The primary products are bio-oil, bio-char, and syngas.
- Gasification: Involves partial oxidation, where a controlled amount of oxygen or steam is introduced. This process operates at higher temperatures (above 700°C) and converts biomass into syngas, primarily composed of carbon monoxide and hydrogen. Gasification is more complex due to the need for precise oxygen control and additional chemical reactions.
-
Product Outputs:
- Pyrolysis: Produces a diverse range of outputs, including bio-oil (a liquid fuel), bio-char (a solid carbon-rich material), and syngas. Bio-oil can be refined for use as a transportation fuel, while bio-char is valuable as a soil amendment or carbon sequestration agent.
- Gasification: Focuses on producing syngas, which is primarily used for electricity generation, heat production, or as a feedstock for chemical synthesis. Gasification does not produce bio-oil or bio-char, limiting its versatility in certain applications.
-
Energy Efficiency:
- Pyrolysis: While pyrolysis is less energy-efficient than gasification, it compensates by producing high-value byproducts like bio-oil and bio-char, which have specific commercial and environmental applications.
- Gasification: More efficient in terms of energy output, making it ideal for large-scale energy production and industrial applications. However, it lacks the ability to produce secondary products like bio-oil and bio-char.
-
Environmental Impact:
- Pyrolysis: Produces fewer emissions compared to gasification because it operates without oxygen, minimizing the formation of pollutants like nitrogen oxides (NOx) and sulfur oxides (SOx). Bio-char also serves as a carbon sink, reducing greenhouse gas emissions.
- Gasification: While efficient, gasification can produce more emissions due to the partial oxidation process, which may require additional cleaning and scrubbing of the syngas to remove impurities.
-
Applications and Use Cases:
- Pyrolysis: Better suited for applications requiring bio-oil (e.g., transportation fuels) and bio-char (e.g., agriculture, carbon sequestration). It is also preferred for smaller-scale operations and decentralized energy systems.
- Gasification: More suitable for centralized energy production, such as power plants and industrial facilities, where the primary goal is to generate electricity or heat.
-
Complexity and Cost:
- Pyrolysis: Simpler and less expensive to operate due to the absence of oxygen and lower process temperatures. It also requires less infrastructure for gas cleaning and processing.
- Gasification: More complex and costly due to the need for precise oxygen control, higher temperatures, and additional steps to clean and process syngas.
-
Flexibility and Versatility:
- Pyrolysis: Offers greater flexibility in terms of feedstock and product diversity. It can process a wide range of organic materials and produce multiple valuable outputs.
- Gasification: Limited to producing syngas, which restricts its versatility compared to pyrolysis.
In conclusion, pyrolysis is often considered better than gasification for applications requiring high-value byproducts like bio-oil and bio-char, simpler process conditions, and lower environmental impact. However, gasification excels in energy efficiency and large-scale energy production. The choice between the two depends on the specific requirements of the project, including the desired end products, scale, and environmental considerations.
Summary Table:
Aspect | Pyrolysis | Gasification |
---|---|---|
Process Conditions | No oxygen, 400–800°C | Partial oxidation, above 700°C |
Primary Outputs | Bio-oil, bio-char, syngas | Syngas |
Energy Efficiency | Lower energy efficiency, high-value byproducts | Higher energy efficiency, limited byproducts |
Environmental Impact | Fewer emissions, bio-char as carbon sink | More emissions, requires gas cleaning |
Applications | Bio-oil (transportation), bio-char (agriculture, carbon sequestration) | Electricity generation, heat production, chemical synthesis |
Complexity & Cost | Simpler, less expensive | More complex, higher costs |
Flexibility | Processes diverse feedstocks, produces multiple outputs | Limited to syngas production |
Want to learn more about pyrolysis and gasification? Contact our experts today for tailored solutions!