Sputter coating is a widely used technique in various industries due to its ability to create uniform, durable, and high-quality thin films on substrates. It is particularly valued for its stable plasma generation, which ensures consistent deposition and strong adhesion at the atomic level. This process is essential in applications such as preparing non-conducting specimens for scanning electron microscopy (SEM), enhancing the performance of cutting instruments, and improving the durability of mission-critical products. By transforming solid materials into microscopic particles and depositing them as thin films, sputter coating offers a reliable method for achieving precise and functional coatings.
Key Points Explained:
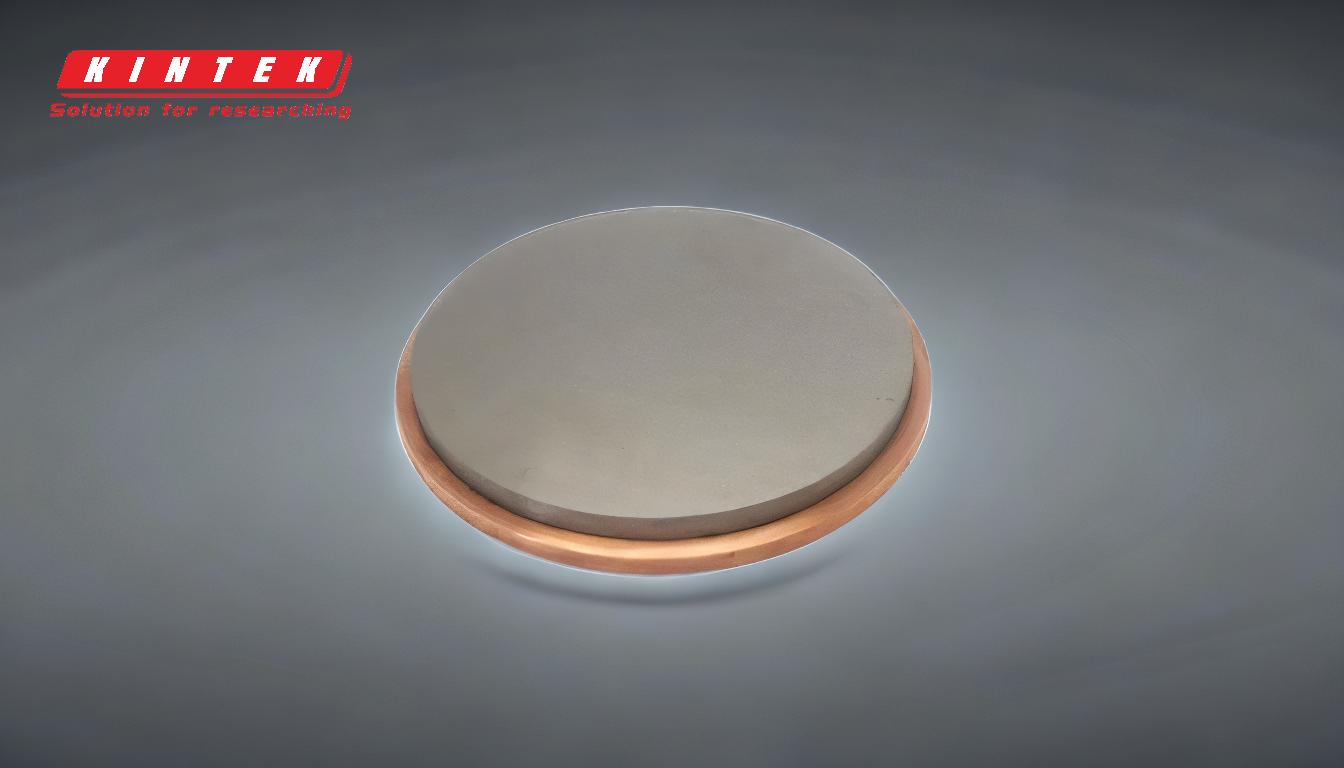
-
Uniform and Durable Coatings:
- Sputter coating creates a stable plasma during the process, which ensures a uniform deposition of material onto the substrate. This results in coatings that are consistent in thickness and highly durable. The uniformity is critical for applications where precise and even coverage is required, such as in semiconductor manufacturing or optical coatings.
-
Atomic-Level Adhesion:
- Unlike traditional surface coatings, sputter coating integrates the deposited material into the substrate at an atomic level. This means the coating becomes a permanent part of the substrate, rather than just an applied layer. This strong adhesion improves the longevity and performance of the coated product, making it ideal for high-stress applications.
-
Versatility in Material Deposition:
- Sputter coating can deposit a wide range of materials, including metals (e.g., gold, platinum, iridium) and non-metals (e.g., diamond dust or nanoscale films). This versatility allows it to be used in diverse industries, from electronics to cutting tools, where specific material properties are required.
-
Preparation of Non-Conducting Specimens for SEM:
- One of the most common uses of sputter coating is in preparing non-conducting or poorly conducting specimens for scanning electron microscopy (SEM). By applying a thin conductive layer (typically a metal), the specimen becomes electrically conductive, enabling clear and accurate imaging without charging effects.
-
Enhanced Performance of Cutting Instruments:
- Sputter coating is used to apply thin films of hard materials, such as diamond dust, to cutting instruments. This enhances their performance by increasing hardness, wear resistance, and durability, making them suitable for mission-critical applications in industries like aerospace and manufacturing.
-
Evolution of Sputter Coating Technology:
- While early sputter coating methods like DC diode sputtering had limitations such as low deposition rates and inability to coat insulating materials, advancements like DC triple sputtering and quadrupole sputtering have improved ionization and stabilized discharge. These innovations have expanded the range of materials and substrates that can be coated, though challenges like low deposition rates still persist in some cases.
-
Physical Vapor Deposition Process:
- Sputter coating is a type of physical vapor deposition (PVD) process. It involves electrically charging a sputtering cathode to form a plasma, which ejects material from the target surface and deposits it onto the substrate. This method is highly controllable and allows for the creation of very thin, functional coatings.
-
Applications in Mission-Critical Products:
- The ability to apply nanoscale films and coatings makes sputter coating invaluable for mission-critical products. These coatings improve performance, durability, and reliability in applications ranging from medical devices to aerospace components.
By leveraging these advantages, sputter coating has become an indispensable technology in modern manufacturing and research, offering precise, durable, and high-performance solutions for a wide range of applications.
Summary Table:
Key Feature | Description |
---|---|
Uniform & Durable Coatings | Ensures consistent thickness and durability for precise applications. |
Atomic-Level Adhesion | Integrates coatings at the atomic level for long-lasting performance. |
Versatile Material Deposition | Deposits metals (gold, platinum) and non-metals (diamond dust) for diverse uses. |
SEM Specimen Preparation | Makes non-conducting specimens conductive for accurate imaging. |
Enhanced Cutting Instruments | Improves hardness and wear resistance for mission-critical applications. |
Advanced Technology | Innovations like DC triple sputtering improve material and substrate range. |
PVD Process | Uses plasma to deposit thin, functional coatings with high precision. |
Mission-Critical Applications | Enhances durability and reliability in aerospace, medical, and more. |
Learn how sputter coating can transform your applications—contact our experts today!