Sputter deposition is slower than evaporation deposition due to fundamental differences in their mechanisms and operational parameters. Sputtering involves the ejection of single atoms or clusters from a target material through ion bombardment, which is a less efficient process compared to the robust vapor stream generated by thermal evaporation. Additionally, sputtering operates at higher gas pressures, causing sputtered particles to undergo gas-phase collisions, further slowing deposition. In contrast, evaporation deposition relies on heating the source material to create a high-density vapor stream, enabling faster deposition rates. These factors, combined with differences in energy transfer, particle trajectories, and scalability, contribute to the slower deposition rates observed in sputtering.
Key Points Explained:
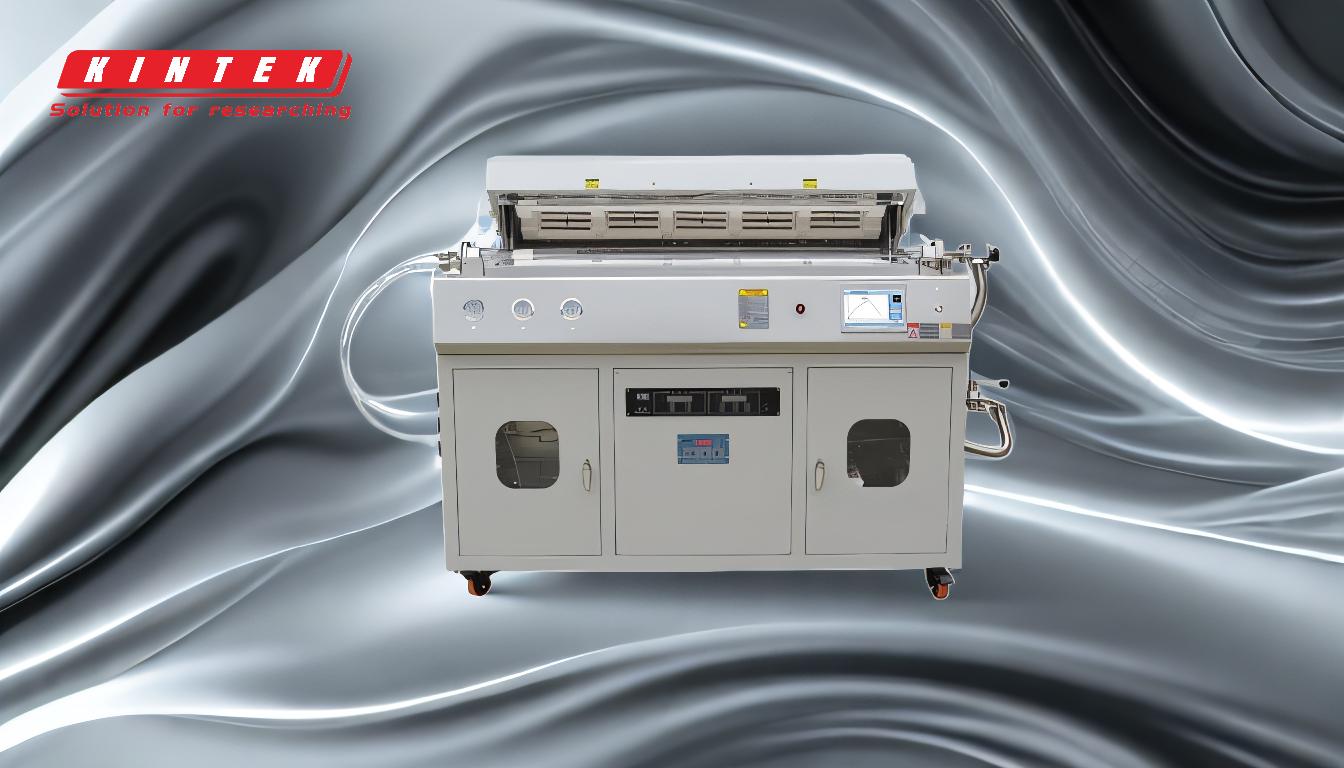
-
Mechanism of Material Ejection:
- Sputtering: Involves the collision of energetic ions with a target material, ejecting single atoms or small clusters. This process is less efficient because it requires precise ion bombardment and energy transfer to dislodge atoms.
- Evaporation: Relies on heating the source material past its vaporization temperature, creating a dense vapor stream. This thermal process is more efficient and produces a higher flux of material, leading to faster deposition rates.
-
Energy Transfer and Particle Behavior:
- Sputtering: The ejected atoms or clusters have higher kinetic energy due to the ion bombardment process. However, sputtering operates at higher gas pressures (5-15 mTorr), causing sputtered particles to collide with gas molecules and lose energy, slowing their deposition onto the substrate.
- Evaporation: Particles in the vapor stream have lower kinetic energy and follow a direct line-of-sight trajectory to the substrate. This minimizes energy loss and allows for faster deposition.
-
Scalability and Automation:
- Sputtering: While slower, sputtering offers better scalability and can be automated for various applications. It is particularly useful for depositing uniform thin films on uneven surfaces due to its better step coverage.
- Evaporation: Although faster, evaporation is less scalable and typically limited to simpler geometries due to its line-of-sight deposition nature.
-
Deposition Rate and Efficiency:
- Sputtering: The deposition rate is inherently lower because the process depends on the ejection of individual atoms or small clusters. Additionally, the need for higher-wattage power sources and complex setups further limits the speed.
- Evaporation: The thermal process generates a robust vapor stream, enabling higher deposition rates and shorter run times. This makes evaporation more suitable for applications requiring rapid coating.
-
Film Quality and Substrate Impact:
- Sputtering: Produces films with higher adhesion, better homogeneity, and smaller grain sizes. However, the high-speed atoms can potentially damage sensitive substrates.
- Evaporation: While faster, evaporation may result in films with lower adhesion and larger grain sizes. It is less likely to damage substrates due to the lower energy of deposited particles.
-
Operational Parameters:
- Sputtering: Operates at higher gas pressures, which thermalizes particles and slows their deposition. This is in contrast to the low-pressure environment of evaporation, which allows for faster and more direct deposition.
- Evaporation: Requires a high vacuum, which minimizes particle collisions and ensures a direct vapor stream to the substrate, enhancing deposition speed.
In summary, sputter deposition is slower than evaporation deposition due to its reliance on ion bombardment, higher gas pressures, and the need for precise energy transfer. While sputtering offers advantages in film quality and scalability, evaporation's thermal process and direct vapor stream enable significantly faster deposition rates.
Summary Table:
Aspect | Sputter Deposition | Evaporation Deposition |
---|---|---|
Mechanism | Ion bombardment ejects single atoms or small clusters. | Heating source material creates a high-density vapor stream. |
Energy Transfer | Higher kinetic energy but slowed by gas-phase collisions. | Lower kinetic energy with direct line-of-sight deposition. |
Deposition Rate | Slower due to less efficient ejection and higher gas pressures. | Faster due to robust vapor stream and minimal particle collisions. |
Film Quality | Higher adhesion, better homogeneity, smaller grain sizes. | Lower adhesion, larger grain sizes, but less substrate damage. |
Scalability | Better for uneven surfaces and automation. | Limited to simpler geometries due to line-of-sight nature. |
Operational Pressure | Higher gas pressures (5-15 mTorr). | High vacuum for minimal particle collisions. |
Need help choosing the right deposition method for your application? Contact our experts today for personalized advice!