Sputtering deposition is slower than evaporation deposition primarily due to the fundamental differences in their mechanisms and operational conditions. Sputtering involves the ejection of atoms from a target material through high-energy ion bombardment, which is a less efficient process compared to the direct thermal vaporization used in evaporation. The sputtered particles undergo gas-phase collisions, slowing them down before they reach the substrate, whereas evaporated particles travel in a direct line-of-sight trajectory. Additionally, sputtering operates at higher gas pressures, which further reduces the deposition rate. These factors collectively contribute to the slower deposition rates observed in sputtering compared to evaporation.
Key Points Explained:
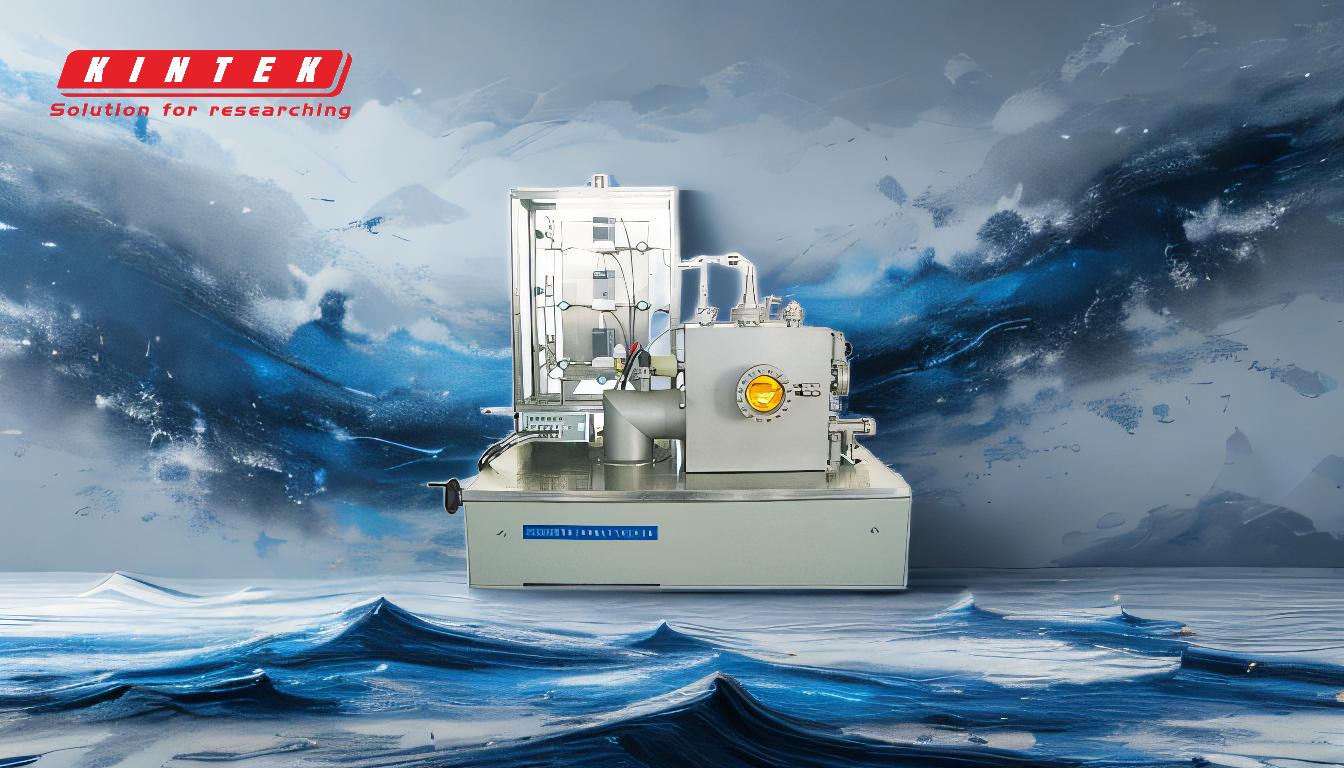
-
Mechanism of Material Ejection:
- Sputtering: Involves the collision of high-energy ions with a target material, ejecting atoms or clusters. This process is less efficient because it relies on physical collisions rather than thermal energy.
- Evaporation: Uses thermal energy to heat the source material past its vaporization point, creating a robust vapor stream. This method is more efficient as it directly converts the material into vapor.
-
Trajectory of Particles:
- Sputtering: Sputtered particles are ejected in various directions and undergo multiple collisions with gas molecules before reaching the substrate. This scattering effect reduces the overall deposition rate.
- Evaporation: Evaporated particles travel in a straight line-of-sight trajectory from the source to the substrate, leading to a more direct and faster deposition process.
-
Operational Pressure:
- Sputtering: Typically performed at higher gas pressures (5-15 mTorr), which increases the likelihood of gas-phase collisions. These collisions slow down the sputtered particles, further reducing the deposition rate.
- Evaporation: Conducted under high vacuum conditions, minimizing gas-phase collisions and allowing for a more efficient transfer of material to the substrate.
-
Energy and Speed of Particles:
- Sputtering: Produces high-energy particles that can potentially damage the substrate. The high energy of these particles also means they are more likely to be scattered and slowed down by collisions.
- Evaporation: Generates lower-energy particles, which are less likely to cause substrate damage and are more efficiently deposited onto the substrate due to their lower energy and reduced scattering.
-
Deposition Rate:
- Sputtering: Generally has a lower deposition rate due to the combined effects of the ejection mechanism, particle trajectory, and operational pressure.
- Evaporation: Offers a higher deposition rate because of the direct vaporization process and minimal interference from gas-phase collisions.
-
Scalability and Automation:
- Sputtering: While slower, sputtering is more scalable and can be automated for many applications, making it suitable for large-scale production despite its lower deposition rate.
- Evaporation: Although faster, it may not be as easily scalable or automated, limiting its use in certain large-scale applications.
In summary, the slower deposition rate of sputtering compared to evaporation is a result of the less efficient ejection mechanism, the scattering of particles due to gas-phase collisions, and the higher operational pressures. These factors, while contributing to slower deposition, also provide benefits such as better step coverage and more uniform thin films, making sputtering a valuable technique in specific applications.
Summary Table:
Aspect | Sputtering | Evaporation |
---|---|---|
Mechanism | High-energy ion bombardment ejects atoms; less efficient due to collisions. | Thermal vaporization directly converts material into vapor; more efficient. |
Particle Trajectory | Particles scatter due to gas-phase collisions, slowing deposition. | Particles travel in a direct line-of-sight, enabling faster deposition. |
Operational Pressure | Higher gas pressures (5-15 mTorr) increase collisions, reducing deposition. | High vacuum minimizes collisions, allowing efficient material transfer. |
Energy of Particles | High-energy particles may damage substrates and scatter more. | Lower-energy particles deposit efficiently with minimal scattering. |
Deposition Rate | Slower due to ejection mechanism, scattering, and higher pressure. | Faster due to direct vaporization and minimal interference. |
Scalability | More scalable and automated, suitable for large-scale production. | Less scalable and harder to automate for large-scale applications. |
Need help choosing the right deposition method for your project? Contact our experts today!