PECVD (Plasma-Enhanced Chemical Vapor Deposition) achieves high deposition rates at relatively low temperatures due to its unique combination of thermal energy and plasma-induced chemical reactions. Unlike traditional CVD, which relies solely on thermal energy, PECVD utilizes RF-induced glow discharge to provide part of the energy required for chemical reactions. This reduces the dependence on high temperatures, allowing the substrate to remain at lower temperatures while maintaining fast deposition rates. Additionally, PECVD offers uniform coatings, excellent film quality, and compatibility with thermally sensitive materials, making it a preferred choice for applications in integrated circuits, optoelectronics, and MEMS.
Key Points Explained:
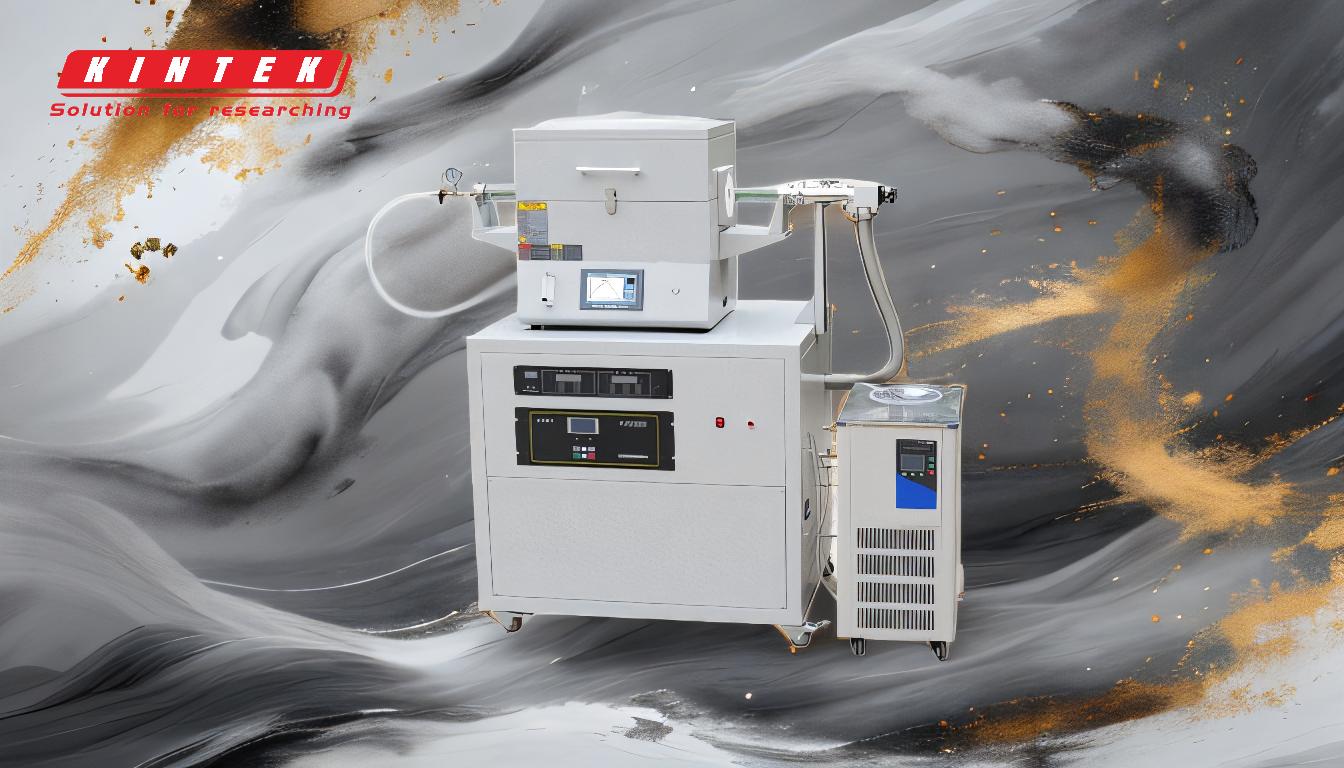
-
Mechanism of PECVD:
- PECVD combines thermal energy with RF-induced glow discharge to initiate chemical reactions.
- The glow discharge provides additional energy, reducing the need for high thermal energy.
- This dual-energy mechanism allows the process to operate at lower temperatures while maintaining high deposition rates.
-
Advantages of Low-Temperature Deposition:
- Low temperatures are crucial for thermally sensitive substrates, such as plastics or materials that cannot withstand high-temperature processing.
- Reduced thermal damage to the substrate ensures better material integrity and performance.
- PECVD enables the deposition of high-quality films with excellent electrical properties, adhesion, and step coverage.
-
High Deposition Rates:
- PECVD's ability to control deposition speed (e.g., 35 minutes for specific processes) significantly improves production efficiency.
- The fast deposition rate is achieved without compromising film quality, making it suitable for high-throughput manufacturing.
-
Uniformity and Quality of Deposited Films:
- PECVD provides highly uniform coatings, even on complex three-dimensional structures, due to its operation at reduced pressures.
- The deposited films exhibit low stress and uniform stoichiometry, which are critical for applications in integrated circuits and optoelectronics.
-
Ease of Maintenance and Cleaning:
- The deposition process is primarily confined to the quartz boat, making it easier to clean and maintain the chamber.
- This reduces contamination risks and ensures consistent film quality over multiple deposition cycles.
-
Applications and Suitability:
- PECVD is widely used in very large-scale integrated circuits, MEMS, and optoelectronic devices due to its low-temperature operation and high-quality film deposition.
- Its compatibility with thermally sensitive materials expands its applicability to a broader range of substrates and industries.
By leveraging plasma energy to supplement thermal energy, PECVD achieves a balance between high deposition rates and low-temperature operation, making it a versatile and efficient deposition technique for modern manufacturing processes.
Summary Table:
Aspect | Details |
---|---|
Mechanism | Combines thermal energy with RF-induced glow discharge for chemical reactions. |
Low-Temperature Benefits | Suitable for thermally sensitive substrates, reduces thermal damage. |
High Deposition Rates | Achieves fast deposition (e.g., 35 mins) without compromising film quality. |
Film Uniformity | Provides uniform coatings on complex 3D structures with low stress. |
Ease of Maintenance | Easy to clean quartz boat, reducing contamination risks. |
Applications | Widely used in ICs, MEMS, and optoelectronics for low-temperature processing. |
Learn how PECVD can enhance your manufacturing process—contact our experts today!