Plastic pyrolysis, a process that converts plastic waste into fuel or other chemicals through thermal decomposition, is often touted as a solution to the global plastic waste crisis. However, it is not a sustainable solution due to several critical issues. These include high energy consumption, the production of toxic byproducts, inefficiency in handling mixed plastics, and the perpetuation of a linear economy rather than promoting a circular one. Additionally, the economic viability of pyrolysis is questionable, and it does not address the root cause of plastic pollution, which is overproduction and overconsumption of single-use plastics. Below, we explore these key points in detail.
Key Points Explained:
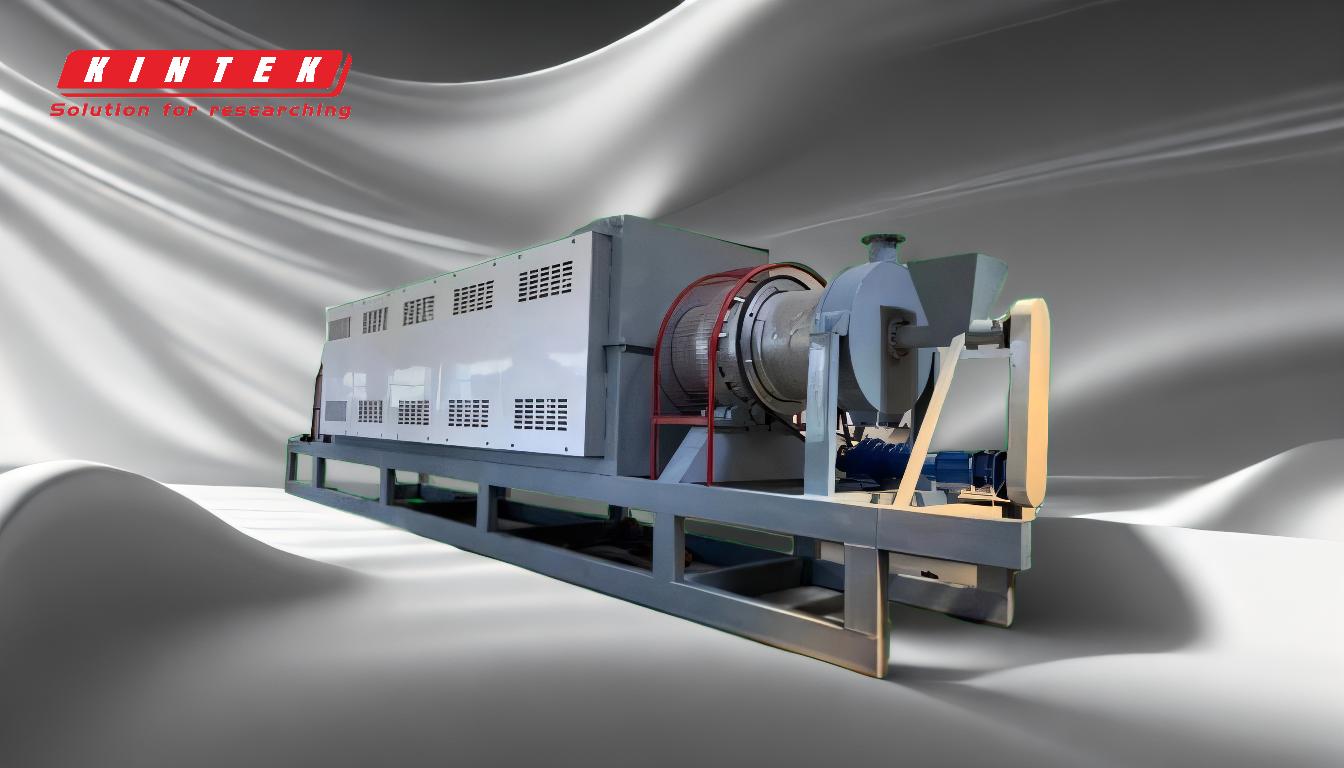
-
High Energy Consumption:
- Plastic pyrolysis requires significant amounts of energy to heat the plastic to high temperatures (typically 300–900°C) in the absence of oxygen. This energy demand often comes from fossil fuels, which negates the environmental benefits of recycling plastic.
- The process is energy-intensive and costly, making it less sustainable compared to mechanical recycling or reducing plastic use altogether.
-
Production of Toxic Byproducts:
- Pyrolysis can release harmful pollutants, such as dioxins, furans, and volatile organic compounds (VOCs), which pose risks to human health and the environment.
- The process also generates char and ash residues, which may contain heavy metals and other contaminants, requiring careful disposal to avoid environmental contamination.
-
Inefficiency with Mixed Plastics:
- Pyrolysis struggles to handle mixed or contaminated plastics effectively. Different types of plastics have varying chemical compositions and melting points, leading to inconsistent outputs and reduced efficiency.
- Contaminants like food residues, adhesives, or non-plastic materials can further complicate the process and degrade the quality of the end products.
-
Perpetuation of a Linear Economy:
- Pyrolysis converts plastic waste into fuel, which is then burned, releasing carbon dioxide and other greenhouse gases. This approach does not close the loop on plastic use but instead perpetuates a linear "take-make-dispose" model.
- True sustainability requires transitioning to a circular economy, where plastics are reused, repaired, or recycled without downcycling into lower-value products.
-
Economic Viability Challenges:
- The cost of setting up and operating pyrolysis plants is high, and the market for pyrolysis-derived fuels is often unstable. This makes it difficult for pyrolysis to compete with traditional fossil fuels or other recycling methods.
- Subsidies and incentives are often required to make pyrolysis economically feasible, which raises questions about its long-term sustainability.
-
Failure to Address Root Causes:
- Pyrolysis does not tackle the root causes of plastic pollution, such as the overproduction and overconsumption of single-use plastics. Instead, it provides a false sense of security by suggesting that plastic waste can be "solved" through technological means.
- A sustainable approach must focus on reducing plastic production, improving waste management systems, and promoting alternatives to single-use plastics.
In conclusion, while plastic pyrolysis may appear to be an innovative solution to plastic waste, it is not sustainable due to its high energy requirements, toxic byproducts, inefficiency with mixed plastics, and failure to promote a circular economy. Addressing plastic pollution requires systemic changes, including reducing plastic production, improving recycling infrastructure, and fostering a shift toward reusable and biodegradable materials.
Summary Table:
Key Issue | Description |
---|---|
High Energy Consumption | Requires significant energy (300–900°C), often from fossil fuels, making it costly and unsustainable. |
Toxic Byproducts | Releases harmful pollutants like dioxins, VOCs, and heavy metals, posing health and environmental risks. |
Inefficiency with Mixed Plastics | Struggles with mixed or contaminated plastics, leading to inconsistent outputs and reduced efficiency. |
Perpetuates Linear Economy | Converts plastic into fuel, burning it and releasing greenhouse gases, failing to promote a circular economy. |
Economic Viability Issues | High setup and operational costs, unstable markets, and reliance on subsidies make it economically unfeasible. |
Fails to Address Root Causes | Does not tackle overproduction or overconsumption of single-use plastics, offering a false solution to plastic waste. |
Concerned about sustainable waste management? Contact us today to explore eco-friendly solutions!