Sputtering deposition is slower than evaporation deposition due to fundamental differences in their mechanisms and operational conditions. Sputtering involves the physical ejection of atoms from a target material using energetic ions, which is a less efficient process compared to the thermal vaporization used in evaporation. Evaporation relies on heating the source material to high temperatures, creating a robust vapor stream that condenses on the substrate at a faster rate. Additionally, sputtering occurs at higher gas pressures, where collisions with gas particles slow down the deposition process, whereas evaporation operates in a high vacuum, allowing for a direct line-of-sight trajectory and faster deposition. These factors collectively contribute to the slower deposition rates observed in sputtering compared to evaporation.
Key Points Explained:
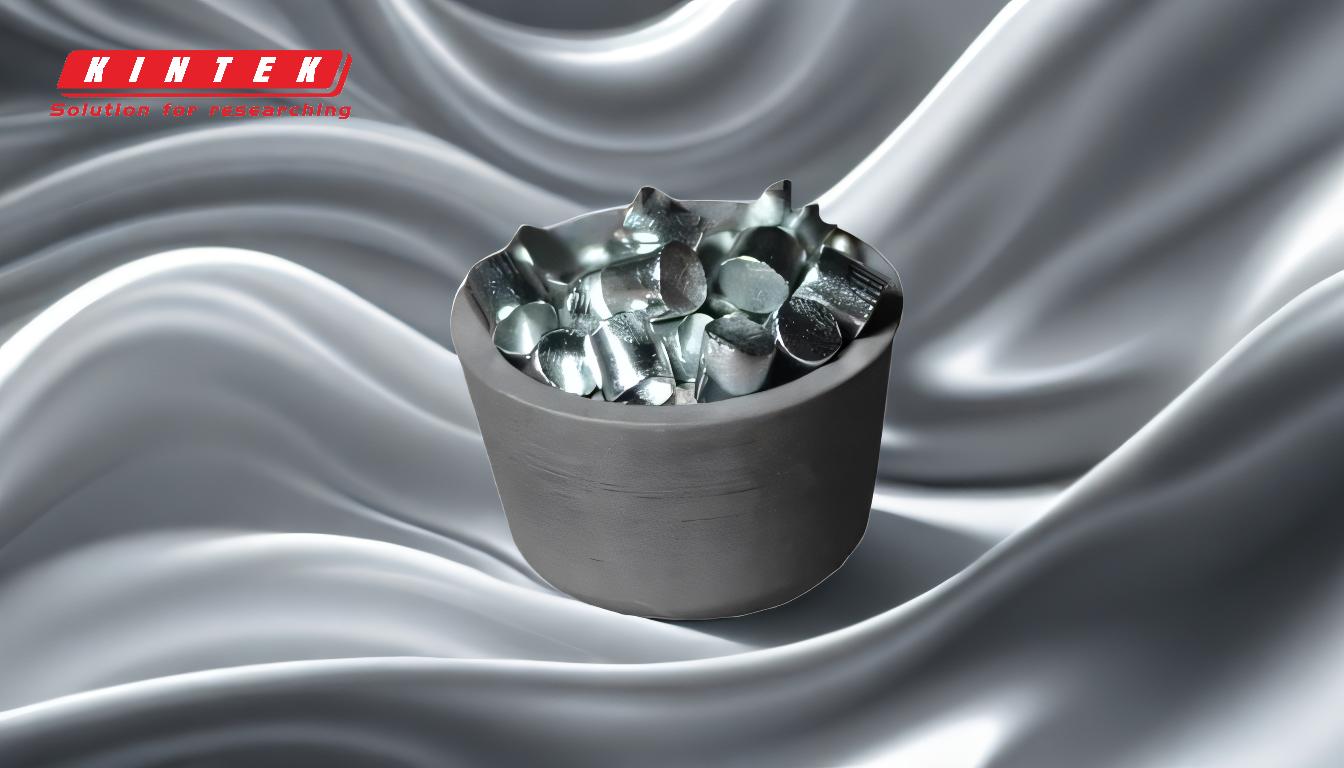
-
Mechanism of Material Vaporization:
- Sputtering: Involves the collision of energetic ions with a target material, ejecting atoms one at a time or in small clusters. This process is inherently slower because it relies on physical bombardment rather than thermal energy.
- Evaporation: Uses thermal energy to heat the source material past its vaporization temperature, creating a continuous and robust vapor stream. This method is more efficient and results in higher deposition rates.
-
Operational Conditions:
- Sputtering: Operates at higher gas pressures (5-15 mTorr), where sputtered particles undergo multiple collisions with gas molecules before reaching the substrate. These collisions slow down the particles, reducing the overall deposition rate.
- Evaporation: Typically performed in a high vacuum environment, allowing for a direct line-of-sight trajectory of vaporized particles to the substrate. This minimizes collisions and results in faster deposition.
-
Energy and Efficiency:
- Sputtering: Requires complex and higher-wattage power sources to generate the energetic ions needed for the sputtering process. The energy transfer is less efficient compared to thermal evaporation.
- Evaporation: Efficiently uses thermal energy to vaporize the source material, leading to a more rapid and continuous deposition process.
-
Deposition Rate:
- Sputtering: Generally has a lower deposition rate, especially for non-metallic materials. The process is slower due to the step-by-step ejection of atoms and the slower travel of particles through the gas.
- Evaporation: Offers a higher deposition rate, as the vapor stream is more intense and direct, allowing for quicker film formation on the substrate.
-
Film Quality and Uniformity:
- Sputtering: Produces films with better step coverage and uniformity, especially on uneven surfaces. However, this comes at the cost of slower deposition rates.
- Evaporation: While faster, it may result in less uniform films, particularly on complex or uneven substrates, due to the more directional nature of the vapor stream.
-
Scalability and Automation:
- Sputtering: Although slower, sputtering is highly scalable and can be automated for large-scale production, making it suitable for applications where uniformity and quality are critical.
- Evaporation: Faster deposition rates make it ideal for applications requiring quick turnaround times, but it may be less suitable for large-scale or automated processes due to potential uniformity issues.
In summary, the slower deposition rate of sputtering compared to evaporation is primarily due to the less efficient mechanism of material ejection, higher operational gas pressures, and the need for complex power sources. While sputtering offers advantages in film quality and scalability, evaporation remains the preferred method for applications requiring high deposition rates.
Summary Table:
Aspect | Sputtering Deposition | Evaporation Deposition |
---|---|---|
Mechanism | Ejection of atoms via energetic ion bombardment | Thermal vaporization of source material |
Operational Pressure | Higher gas pressures (5-15 mTorr), causing particle collisions | High vacuum, enabling direct line-of-sight deposition |
Energy Efficiency | Less efficient due to complex power requirements | More efficient, utilizing thermal energy for rapid vaporization |
Deposition Rate | Slower, especially for non-metallic materials | Faster, with intense and direct vapor stream |
Film Quality | Better uniformity and step coverage, ideal for uneven surfaces | Less uniform, particularly on complex or uneven substrates |
Scalability | Highly scalable and suitable for large-scale production | Faster but less suitable for large-scale or automated processes |
Need help choosing the right deposition method for your application? Contact our experts today for personalized advice!