Tungsten, despite its exceptional properties such as the highest melting point of all metals and high tensile strength, is not commonly used as a heating element in many applications due to several critical limitations. These include susceptibility to embrittlement, mechanical and thermal shock, and oxidation at elevated temperatures. Tungsten must be operated in controlled environments, such as vacuum or inert atmospheres, to prevent oxidation above 500°C. Additionally, its brittleness and the need for specialized temperature control systems make it less practical for general heating applications compared to other materials like nichrome or Kanthal.
Key Points Explained:
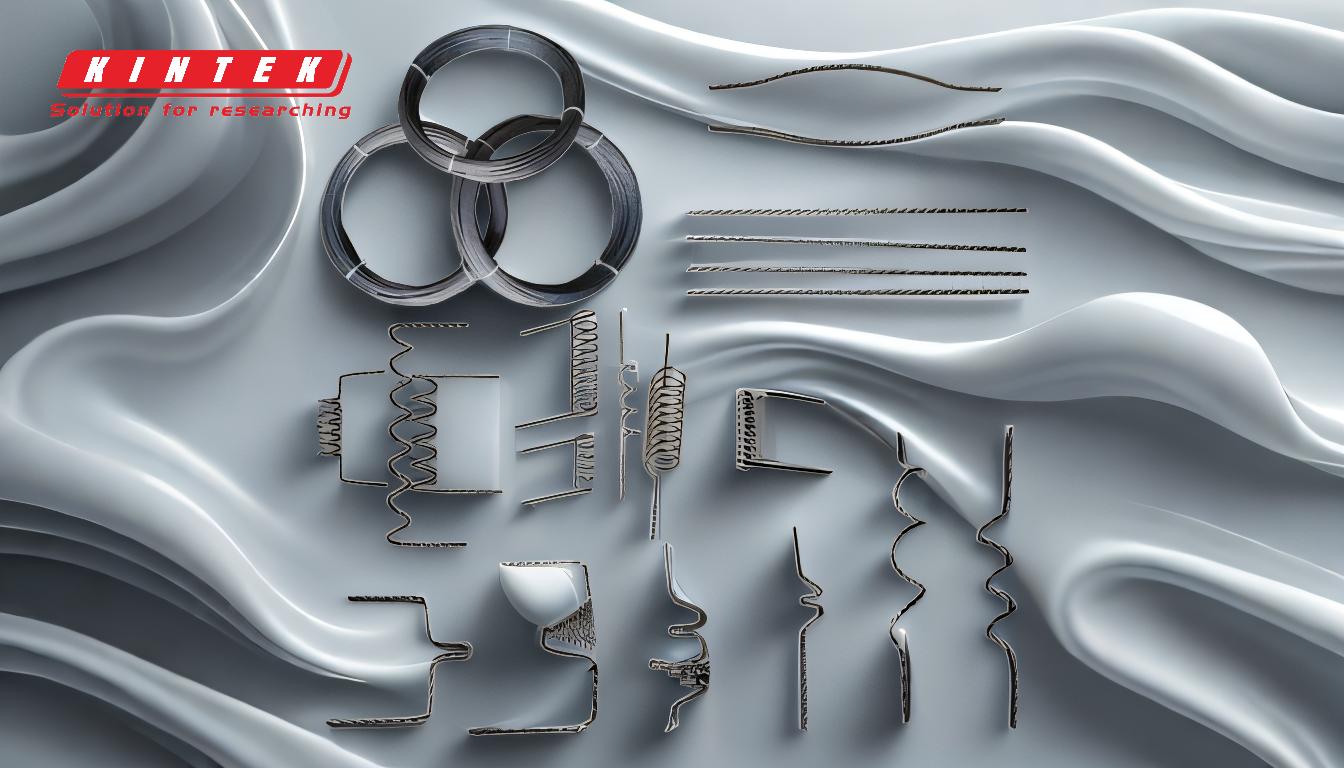
-
Susceptibility to Embrittlement and Shock:
- Tungsten heating elements are prone to embrittlement, especially during cold start-ups. This brittleness can lead to mechanical failure under stress or thermal shock, making it unsuitable for applications where rapid temperature changes are common.
- A ramping temperature control system is required to gradually heat tungsten elements, which adds complexity and cost to the heating system.
-
Oxidation at High Temperatures:
- Tungsten oxidizes rapidly in air at temperatures above 500°C (932°F). This oxidation can degrade the material, reducing its lifespan and efficiency.
- To prevent oxidation, tungsten heating elements must be used in vacuum or inert gas environments, which limits their applicability in many industrial settings.
-
High Melting Point and Thermal Stability:
- Tungsten has the highest melting point of all metals at 3422°C (6192°F), making it ideal for extremely high-temperature applications.
- However, this property is only beneficial in specialized environments, such as vacuum furnaces, where oxidation and embrittlement can be controlled.
-
Applications in Specialized Environments:
- Tungsten mesh heating elements are primarily used in vacuum tungsten furnaces for high-temperature heat treatment and processing. They can withstand temperatures up to 2400°C and offer precise temperature control and long service life.
- The use of tungsten in these specialized applications highlights its niche role rather than its suitability for general-purpose heating.
-
Comparison with Other Heating Elements:
- Materials like nichrome and Kanthal are more commonly used as heating elements due to their resistance to oxidation, ease of use, and lower cost.
- These materials do not require the same level of environmental control as tungsten, making them more practical for a wide range of applications.
-
Role of Tungsten in Industrial Applications:
- Tungsten's hardness and strength at high temperatures have made it valuable in the manufacture of high-speed steel and cemented tungsten carbides, which are used in tooling, drilling, and construction industries.
- While tungsten excels in these applications, its limitations as a heating element restrict its use in broader heating contexts.
In summary, while tungsten possesses remarkable properties that make it indispensable in certain high-temperature and specialized applications, its brittleness, susceptibility to oxidation, and the need for controlled environments make it unsuitable for general use as a heating element. For more information on tungsten's applications, you can explore the topic of tungsten boat.
Summary Table:
Key Limitation | Explanation |
---|---|
Susceptibility to Embrittlement | Prone to brittleness and mechanical failure under stress or thermal shock. |
Oxidation at High Temperatures | Oxidizes rapidly above 500°C, requiring vacuum or inert gas environments. |
High Melting Point | Ideal for extreme temperatures but only in specialized environments. |
Specialized Applications | Used in vacuum furnaces for high-temperature processing, not general heating. |
Comparison with Other Materials | Nichrome and Kanthal are more practical for general use due to cost and ease. |
Learn more about tungsten's specialized applications—contact our experts today!