Yes, an induction heater can melt aluminum. Induction heating is a highly efficient and effective method for melting conductive materials like aluminum. The process relies on electromagnetic induction to generate heat within the aluminum itself, ensuring uniform heating and melting. Below is a detailed explanation of how induction heaters work with aluminum, their advantages, and the key factors involved in the process.
Key Points Explained:
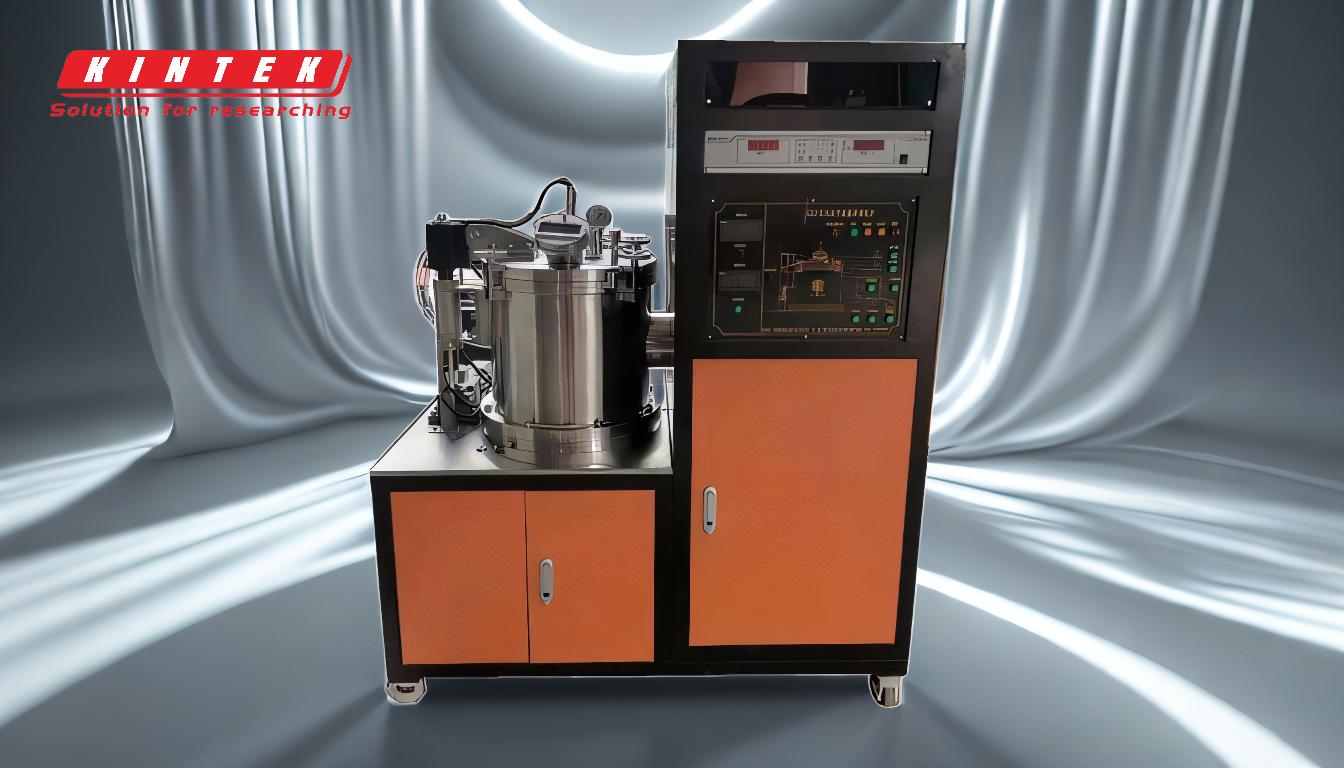
-
How Induction Heating Works for Aluminum
- Induction heating uses alternating current (AC) passed through an induction coil to create a rapidly changing magnetic field.
- When aluminum (a conductive material) is placed within this magnetic field, Faraday’s Law induces eddy currents within the aluminum.
- The resistance of the aluminum to these eddy currents generates heat, a phenomenon known as Joule heating.
- This heat is generated internally within the aluminum, ensuring rapid and uniform heating.
- The magnetic field also causes inductive stirring, which helps mix the molten aluminum and ensures a uniform temperature and composition.
-
Advantages of Induction Heating for Aluminum Melting
- Energy Efficiency: Induction furnaces are highly energy-efficient, making them ideal for melting aluminum, which is an energy-intensive process.
- Uniform Heating: The electromagnetic stirring effect ensures even temperature distribution, reducing the risk of hot spots and uneven melting.
- Reduced Impurities: The stirring action helps impurities rise to the surface, where they can be easily removed, resulting in purer aluminum.
- Less Oxidation and Burning Loss: Induction heating minimizes exposure to oxygen, reducing oxidation and material loss during melting.
- Precision and Control: Induction furnaces allow precise control over temperature and heating rates, which is critical for producing high-quality aluminum alloys.
-
Factors Influencing Aluminum Melting in Induction Heaters
- Frequency of Alternating Current: The frequency of the AC used in the induction coil affects the depth of heat penetration into the aluminum. Higher frequencies are typically used for smaller pieces or thin sections, while lower frequencies are better for larger volumes.
- Material Conductivity: Aluminum’s high electrical conductivity makes it well-suited for induction heating, as it efficiently generates heat through eddy currents.
- Crucible Design: The crucible used in the induction furnace must be compatible with aluminum and withstand the high temperatures required for melting.
- Magnetic Field Strength: The strength of the magnetic field determines the intensity of the eddy currents and, consequently, the rate of heating.
-
Applications of Induction Heating for Aluminum
- Primary Aluminum Production: Induction furnaces are used to convert alumina into pure aluminum and then into aluminum alloys.
- Recycling: Induction heating is ideal for recycling aluminum scraps, as it ensures efficient melting and purification.
- Alloy Production: The precise control and uniform heating provided by induction furnaces make them suitable for producing high-quality aluminum alloys with specific properties.
- Casting and Molding: Molten aluminum from induction furnaces can be directly used for casting and molding processes.
-
Challenges and Considerations
- Initial Cost: Induction furnaces can have a higher upfront cost compared to traditional melting methods, but their energy efficiency and operational benefits often offset this over time.
- Maintenance: The induction coil and crucible require regular maintenance to ensure optimal performance and longevity.
- Material Compatibility: While aluminum is well-suited for induction heating, the process may not be as effective for non-conductive materials or materials with low electrical conductivity.
In summary, induction heaters are not only capable of melting aluminum but are also highly efficient and effective for this purpose. They offer numerous advantages, including energy efficiency, uniform heating, and reduced impurities, making them a preferred choice for aluminum melting in various industrial applications.
Summary Table:
Aspect | Details |
---|---|
How It Works | Uses electromagnetic induction to generate internal heat in aluminum. |
Key Advantages | Energy efficiency, uniform heating, reduced impurities, precise control. |
Influencing Factors | AC frequency, material conductivity, crucible design, magnetic field strength. |
Applications | Primary aluminum production, recycling, alloy production, casting & molding. |
Challenges | Higher initial cost, maintenance requirements, material compatibility. |
Ready to explore induction heating for your aluminum melting needs? Contact us today for expert advice and solutions!