Circular Pellet Press Die Sets
Table of Contents
- Circular Pellet Press Die Sets
- Components of a Powder Pelleting Die Set
- Machining and Material Selection for Pellet Press Dies
- Precision of Powder Press Tools
- Recommended Force Usage with Pellet Die
- Considerations for Pressing Long/Tall Pellets
- Choosing the Right Hydraulic Laboratory Press for Your Pellet Die Set
- Pellet Shapes
- Applications of Pellet Press Dies
- KBR Pellet Die Sets for FTIR Analysis
Circular Pellet Press Die Sets are essential tools used to create round pellets with precise diameters. These die sets are designed to accommodate pellets ranging from very thin to over 2 inches in length. The meticulous machining and use of high-quality materials make these die sets the best in the market.
Use and Specifications of Circular Pellet Press Die Sets
A complete powder pelleting die set includes the following components:
- Die Sleeve
- Plunger rod
- Spacers (2x)
- Base plate
- Release ring with viewing slot
Round mold set parts
These components work together to ensure seamless pellet production. The die sleeve, plunger rod, and spacers form the core of the pellet press die set, while the base plate and release ring with a viewing slot provide additional support and functionality.
The machining and material selection for these pellet press die sets are of utmost importance. Each piece is meticulously designed, machined, and precision ground to ensure easy and reliable powder pressing. The steels chosen for the die sets undergo heat treatment to achieve maximum hardness and strength. This enables the die sets to withstand the large stresses exerted by hydraulic presses, ensuring long-term performance and consistent pellet quality.
The durability of these die sets is attributed to the use of hardened tool steel. This material can handle the wide range of pressures generated during the pellet pressing process. Additionally, the availability of various sizes of hydraulic and laboratory pellet press dies in the selection range provides flexibility to meet specific pellet size requirements.
At Pellet Press Die Sets, we pride ourselves on offering the largest range of off-the-shelf pellet press dies. We also provide custom-made dies on a daily basis, catering to the unique needs of our customers. Whether you have a small or large project, rest assured that we have the expertise and resources to assist you in creating high-quality pellets.
So, if you're in need of pellet production, trust Pellet Press Die Sets to provide you with reliable and efficient circular pellet press die sets.
Components of a Powder Pelleting Die Set
Die Sleeve
The die sleeve is a hollow cylindrical body that forms a blind tube into which a powder sample is poured. It acts as the main structure of the pellet die.
Plunger rod
The plunger rod is inserted into the die sleeve to complete the assembly. It is used to apply pressure to the powder sample during the pelletizing process.
Spacers
Spacers are removable components that can be used to adjust the thickness of the pellets being formed. They help in reducing cross-contamination between samples and provide flexibility in pellet thickness.
Base plate
The base plate forms the bottom of the die and provides support for the powder sample during compression. It is an essential component for the formation of solid pellets.
Release ring with viewing slot
The release ring with a viewing slot is used to separate the base from the body of the die and to push the pellet out. The viewing slot allows for easy inspection of the pellet before removal.
Powder pellet dies are precision tools designed to ensure a tight fit between the components to prevent material migration and jamming. The interior pressing surface of the die is polished to reduce friction and improve the surface finish of the pellets.
A pellet die works by compressing a powder sample against the base and walls of the die using a press. The applied load causes the powder grains to bind together and form a solid pellet. The pellet can then be removed by separating the base from the body and applying a small load to the plunger.
In laboratory settings, pellet dies are commonly used for preparing test specimens for analysis. They are available in different types, such as flat disc and cylinder, depending on the characteristics of the powder sample.
When selecting a powder pelleting die set, it is important to consider the machining and material selection. High-quality die sets are designed, machined, and precision ground for easy and reliable powder pressing. The chosen steels are heat-treated for maximum hardness and strength, ensuring long-term performance.
Overall, a powder pelleting die set consists of essential components like the die sleeve, plunger rod, spacers, base plate, and release ring with a viewing slot. These components work together to create solid pellets from powdered samples, making them valuable tools in laboratory analysis and research.
Machining and Material Selection for Pellet Press Dies
Design and material aspects for efficiency and reliability
In the process of creating compressed pellets using a laboratory press, the design and material selection of the pellet press dies play a crucial role in ensuring efficiency and reliability. The laboratory press utilizes hydraulic action to shape powdered materials into pellets. It can exert pressures ranging from 15 to 200 metric tons, making it suitable for a variety of applications such as pharmaceutical development, spectroscopy, and bomb calorimetry.
One important consideration in pellet press die design is the shape of the desired pellets. Different products may require different pellet shapes, and some laboratory presses can accommodate a wide range of sizes or customized dies. While most laboratory presses are hydraulic, there are also screw press configurations available.
Hydraulic Lab Presses
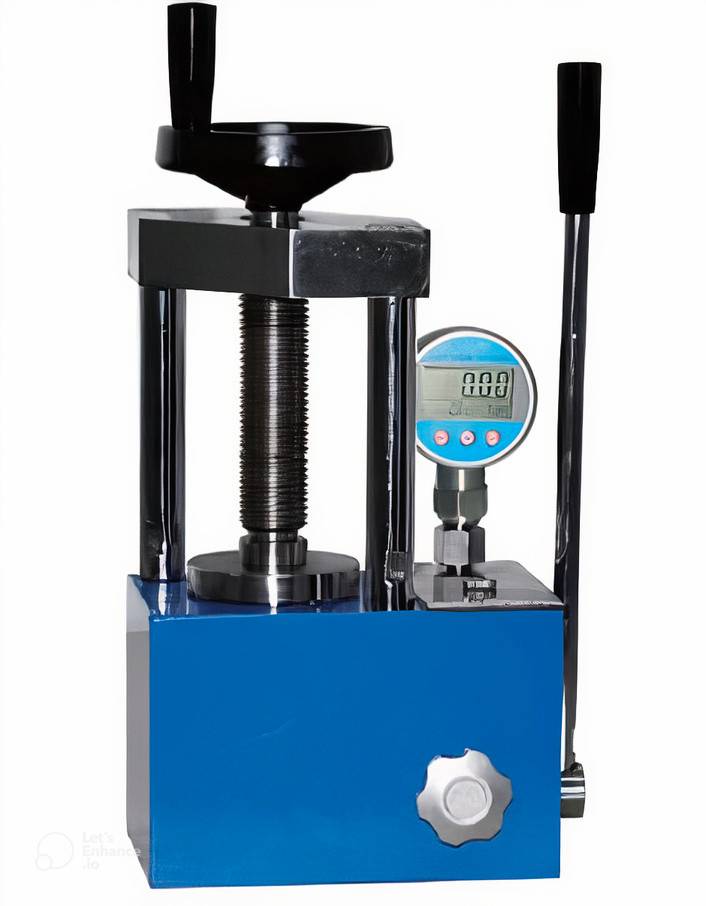
Hydraulic Lab Presses from Pellet Press Die Sets offer a range of pressing forces, including 5 Ton, 15 Ton, 25 Ton, and 40 Ton. These presses operate on the hydraulic principle, where a relatively low force can be delivered through the pumping action of the handle, resulting in high loads applied to the pellet die.
Key features of Hydraulic Lab Presses include:
- Adjustable top pressing surface
- Perspex safety guard
- Long, easy-to-use handle
- Accurate pressure gauge
- Hardened steel construction
- All-in-one leak-free design
These hydraulic presses are essential in material science labs for various processes such as pressing pellets, lamination, and punching electrodes. They can be used with Pellet Press Die Sets or other processes in the lab.
Range of hydraulic pellet press and laboratory pellet press dies
The selection of the right material for pellet press dies is crucial to ensure their longevity and performance. Pellet Press Die Sets offers a wide range of off-the-shelf pellet press dies, and they also custom-make dies to meet specific requirements.
Machining and Material Selection
Each piece in Pellet Press Die Sets' quality powder pellet press die sets is designed, machined, and precision ground for simple, easy, and reliable powder pressing. The steels used for these dies are carefully chosen and heat-treated to maximize hardness and strength, ensuring long-term performance. These durable, hardened tool steel dies can withstand the large stresses exerted by the hydraulic press, guaranteeing the production of high-quality pellets.
The range of hydraulic pellet press and laboratory pellet press dies available at Pellet Press Die Sets offers flexibility in pellet size selection. However, if a specific die size is not available, the company can custom-make it to meet the customer's needs.
In summary, the design and material selection of pellet press dies are critical factors in achieving efficient and reliable pellet production. Whether using a hydraulic or screw press configuration, the right die design and material ensure optimal performance and longevity. Pellet Press Die Sets provides a wide range of off-the-shelf and custom-made dies, machined and heat-treated for maximum hardness and strength, allowing for high-quality pellet production in various laboratory applications.
Precision of Powder Press Tools
High tolerance of pellet dies
Every one of our pellet dies is made to high tolerances to allow the pieces to slide together without allowing the powder to escape, which would cause the die set to jam up and prevent it from working efficiently. The superior level of mirror surface finish of the interior pressing surface reduces friction and removable spacers can be used to reduce cross-contamination between samples. Dies can be operated with or without spacers to give flexibility on the thickness of pellets you want to make.
Reduction of friction and cross-contamination
The precision manufacturing of our powder press tools ensures a high level of quality and performance. The mirror surface finish of the interior pressing surface reduces friction, allowing for smooth operation and efficient production of pellets. Additionally, the removable spacers help to prevent cross-contamination between different samples, ensuring the integrity of each pellet.
Flexibility on pellet thickness
Our pellet press tools offer flexibility when it comes to the thickness of the pellets you want to produce. By using or removing spacers, you can easily adjust the thickness according to your requirements. This flexibility allows for customization and ensures that you can produce pellets of varying thicknesses to meet your specific needs.
In summary, our precision powder press tools are designed to provide high tolerance, reduce friction and cross-contamination, and offer flexibility in pellet thickness. With these features, you can achieve accurate and efficient pellet production for your research or production needs.
Recommended Force Usage with Pellet Die
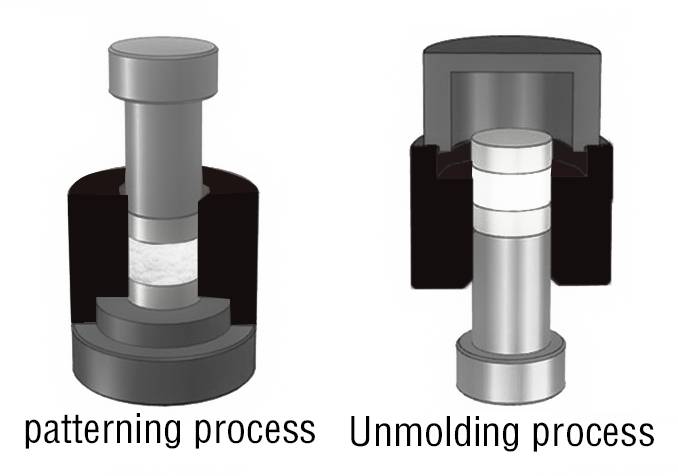
Force limitations and recommendations
When using a pellet die, it is essential to stay within the recommended force limits to ensure safety and efficiency. Here are some tips to help you make the most out of your pellet die:
-
Stay below the recommended loading on the product page: The product page for your specific pellet die will provide you with the recommended maximum force. It is crucial to adhere to this limit to avoid any potential issues.
-
Do not overfill your die sleeve with powder: Overfilling the die sleeve can lead to excessive force being applied, which may exceed the strength of the steel in the die set. This can result in die failure and compromised pellet quality.
-
Ensure proper alignment of your press and die: Proper alignment between the press and die is essential for optimal force distribution. Misalignment can lead to uneven force application and affect the quality of the pellets.
-
Always have a press guard in place: A press guard is a safety measure that protects you from any potential accidents during the pellet pressing process. It is important to ensure that the press guard is in place before operating the press.
-
Avoid testing the limits of the steel: The recommended force limits provided by the manufacturer are based on extensive testing and data analysis. It is not advisable to exceed these limits as it may lead to die failure and compromised safety.
-
Recommended force for good pellets: In most cases, you do not need excessively high forces to produce good quality pellets. The force required is typically in the range of 5,000-10,000 psi. Using super high forces can exceed the fracture strength of the compact, leading to cracking or "capping" of the pellets upon release.
-
Use a force gauge for accurate measurement: Having a force gauge is highly recommended to accurately measure the applied force. This allows you to determine the stress applied to the die set and the pellet by dividing the force by the cross-sectional area of the plunger. This value is commonly used in scientific journals and provides a transferable quantity independent of the die diameter.
-
Consider the size of the die and press: For smaller pellets with a diameter of less than 8 mm, it is recommended to use a smaller press. This allows for more accurate force application and better control over the pressing process. Using a high-force press with a small die can make it challenging to apply the desired force accurately.
Safety and efficiency tips
- Press safety guard: All our hydraulic lab presses come with a Perspex safety guard and pressure gauge. It is essential to assemble the safety guard upon receiving the press to ensure safe operation. The pressure gauge helps you monitor the force applied during the pellet pressing process.
Remember to refer to the product page of your specific pellet press die for the recommended maximum force and other guidelines. Following these recommendations will help you achieve optimal results while ensuring safety and efficiency in your pellet pressing operations.
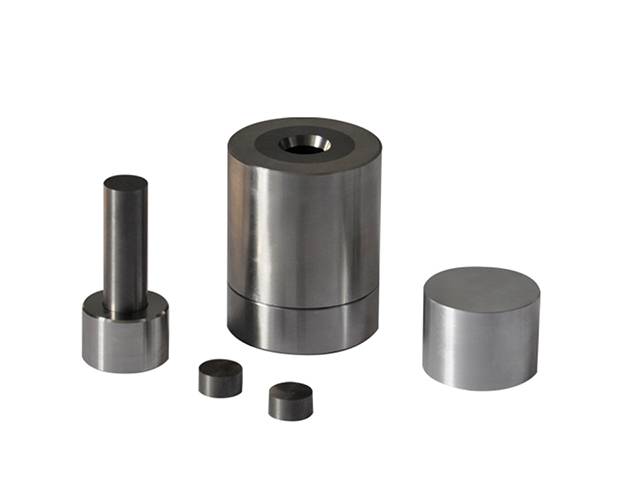
Considerations for Pressing Long/Tall Pellets
Convention and considerations for the height of a pellet
When it comes to pressing pellets in the lab, there are a few important considerations to keep in mind regarding the height of the pellet. Conventionally, it is recommended that the height (length) of a pellet should not greatly exceed the diameter. This is because the stresses in the compact are greater closer to the moving surface of the top plunger. When pellets get significantly longer than the diameter, it can lead to cracking or other adverse effects. While this rule is a general one and may not apply to all scenarios, it is still something to consider when pressing long or tall pellets.
Suggestions for pressing long pellets
If you need to press long pellets or require a greater fill height for your powders, there are a few suggestions to keep in mind. First, it is advisable to use lower forces when pressing longer pellets. This can help reduce the risk of cracking and other adverse effects. Additionally, lubricating the die can help ensure smoother pressing of the longer pellets.
Another suggestion is to use a small o-ring between the base plate and sleeve of the die. This allows for some compression of the lower pressing surface during the pressing process, resulting in more even distribution of stresses throughout the compact.
It's worth noting that when pressing longer pellets, the plunger may experience higher buckling stresses under the same load. This is due to the unsheathed plunger being exposed during pressing. If you are approaching the recommended loading for your plunger, it is advisable to either reduce the force applied, reduce the pellet height, or consider using a shorter plunger specifically designed for pressing longer pellets.
Choosing the right hydraulic laboratory press for your pellet die set
Selecting the appropriate hydraulic laboratory press for your pellet die set is essential for achieving optimal results. The size of the hydraulic press will depend on the diameter of the pellet you wish to create. If you have the option to choose, here are some recommendations.
For smaller pellets with a diameter of less than 8 mm, it is recommended to use a smaller press. This allows for greater accuracy in applying the force and provides a better sense of control during the pressing process. Using a 40-ton press for a 6 mm die set, for example, can make it challenging to accurately apply the desired force, as a single pump of the handle may quickly exceed the maximum force requirement for the smaller die. Planning ahead and being aware of the force required before pressing can help avoid errors in the process.
Press safety guard
All of our hydraulic lab presses come equipped with a Perspex safety guard and pressure gauge. This ensures that you can safely carry out the pressing process. The press is designed for easy assembly, allowing you to start pressing right away without any hassle.
Remember to always prioritize safety and follow proper procedures when using hydraulic lab presses.
Choosing the Right Hydraulic Laboratory Press for Your Pellet Die Set
Tips for selecting the right hydraulic lab press
When it comes to selecting the right hydraulic lab press for your pellet die set, there are a few factors to consider. First, you need to know the diameter of the pellet you will be making. Hydraulic lab presses come in various sizes, so it's important to choose one that suits your needs. If you have a choice, here's what we suggest:
-
For smaller pellets with a diameter of less than 8mm, it is recommended to use a smaller press. This allows for more accuracy in the force applied and provides a better sense of control while pressing.
-
If you are pressing longer pellets, it's important to consider the buckling stresses in the plunger. In this case, you might need to reduce the force, pellet height, or get a shorter plunger for use during pressing.
Disassembly diagram of hydraulic press
Importance of a force gauge
When selecting a hydraulic lab press, it is crucial to have an accurate pressure gauge. This allows you to monitor the force being applied during the pressing process. Without a force gauge, it can be challenging to ensure that you are applying the correct amount of force, especially when working with smaller pellet sizes.
A force gauge provides you with the necessary feedback to make adjustments and ensure consistent pellet quality. It helps prevent errors that can occur when the force applied exceeds the maximum limit for a smaller die set.
Checking for safety features
Safety should always be a top priority when working with hydraulic lab presses. When choosing a press, it is essential to check for safety features such as a Perspex safety guard.
The Perspex safety guard protects you from any potential hazards during the pressing process. It provides a barrier between you and the press, minimizing the risk of accidents or injuries.
Additionally, a hydraulic lab press with a Perspex safety guard often comes with a minimum assembly requirement. This means you can start using the press right away, without the need for complicated setup procedures.
In conclusion, when choosing a hydraulic lab press for your pellet die set, consider the size of your pellets, the importance of a force gauge, and the presence of safety features such as a Perspex safety guard. These factors will ensure a safer and more efficient pressing process, leading to high-quality pellets.
Pellet Shapes
Types of shapes attainable with pellet die sets
Pressed pellets are prepared by pressing loose powders filled in a ring or cup using a set of dies and a press machine. There are two types of dies, namely flat disc and cylinder types. The type to be used depends on the characteristic of the powder sample. Ease of pelletization depends on sample characteristics and grain size and can be improved by sufficient pulverization. Mixing the powder sample with a forming agent (binder) is another solution if pelletization is difficult. Rings and cups used for forming pressed pellets are available in various sizes with 10 –43 mm inner diameter and are made of either aluminum or PVC. Cup materials are either aluminum or iron, and available inner diameters are 32–45 mm. The selection of die type depends on the characteristics of the sample.
At Pellet Press Die Sets, we offer the largest range of off the shelf pellet press dies and custom make dies on a daily basis for our happy customers. So if you have a project big or small and you need to make pellets - you're in good hands with us.
Homemade Wood Pellet Machine
Pellet Press Dies - Circular
Circular Pellet Press Die Sets are used to make round pellets with precise diameters from very thin up to over 2 inch length. We take great pride in precision machining each out of quality materials to make them the best die sets available.
WHAT SHAPES CAN YOU MAKE PELLETS IN?
We make die sets for the following shapes:
- Circular - this is the most common (using our standard dies, vacuum dies, low profile dies or custom dies)
- Square / Rectangular (we stock a few sizes or make custom die sets)
- Ring Shapes (Annual Die Sets)
- Custom dies for almost any profile shapes or curved surfaces
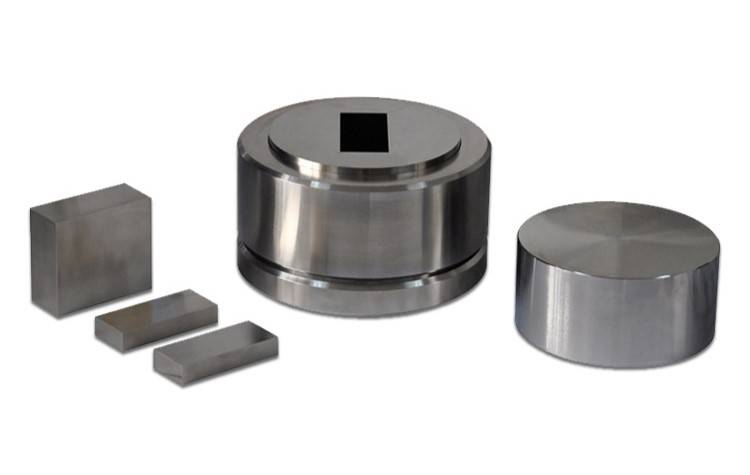
WHAT CAN THE PELLETS USED FOR?
Our Pellet Press Dies are used across the works in universities, research centers, big pharmaceutical firms, small businesses, and Fortune 500 companies. Whenever there's a powder which is required in solid form, you use a pellet die. So whether it's a geological sample from the field, an electrode for a new type of battery, a sputtering target, or a new material for a space rocket nozzle, it's going to get compressed into a solid pellet form for moving around, testing, and analysis.
Applications of Pellet Press Dies
Various uses of pellets in different sectors
Pellet Press Dies - Circular
Circular Pellet Press Die Sets are used to make round pellets with precise diameters from very thin up to over 2 inch length. These die sets are precision machined from quality materials to ensure the best quality pellets.
Pellet Press
KinTek's benchtop Pellet Press provides a convenient and economical means for compressing powdered materials into pellet or tablet form without the need for expensive tablet making machinery. It is a compact, hand-operated press that can be used anywhere in the laboratory, requiring very little bench space. The Pellet Press produces uniform pellets in a polished die and ejects them smoothly into a receiver without contamination.
The pellets produced by the Pellet Press are cylindrical in shape with flat ends. The height or thickness of the pellets depends on the amount of material compressed and the force applied. The dies are not fastened down and can be easily reloaded.
WHAT SHAPES CAN YOU MAKE PELLETS IN?
We offer die sets for the following shapes:
- Circular - this is the most common shape and can be made using standard dies, vacuum dies, low profile dies, or custom dies.
- Square / Rectangular - we stock a few sizes of square and rectangular dies, but we can also make custom die sets.
- Ring Shapes - annual die sets are available for making pellets in ring shapes.
- Custom dies - we can create dies for almost any profile shape or curved surface.
WHAT CAN THE PELLETS BE USED FOR?
Our Pellet Press Dies are used in various sectors including universities, research centers, big pharmaceutical firms, small businesses, and Fortune 500 companies. Pellet dies are used whenever a powder needs to be converted into a solid form. Whether it's a geological sample, an electrode for a new type of battery, a sputtering target, or a new material for a space rocket nozzle, the powder is compressed into a solid pellet form for ease of handling, testing, and analysis.
At Pellet Press Die Sets, we offer the largest range of off-the-shelf pellet press dies and also custom make dies on a daily basis for our customers. So, whether you have a big project or a small one that requires making pellets, you can rely on us for high-quality pellet press dies.
KBR Pellet Die Sets for FTIR Analysis
Fourier-Transform Infrared Spectroscopy (FTIR) is a method used to characterize new materials or identify and verify known and unknown samples by analyzing the absorption of infrared light. To prepare a sample for FTIR analysis, a small amount of the powder to be investigated is typically ground and pressed with KBr powder in a pellet press die set that is transparent to IR radiation.
Die Sets for KBr Pellet Making & XRF Spectroscopy
KinTek offers a range of die sets for KBr pellet making and XRF spectroscopy. All die sets are made from hardened aerospace grade stainless steel for durability. The smaller diameter dies (3mm to 19mm) are primarily used for KBr pellets for transmission analysis by IR spectroscopy. The larger dies are commonly used for producing briquettes for XRF spectroscopy.
The 13mm Macro-Micro die is a popular choice for KBr pellets. It is available with paper inserts that have various small apertures (1.5mm, 3mm, 5mm, and 11mm), allowing the user to make micro-pellets with a 13mm die set. These paper inserts also serve as a useful frame for mounting and storing the pellets.
All KinTek dies have upper and lower stainless steel sections for easy disassembly, and they are sealed with viton seals for efficient use.
Pellet Dies for Spectroscopy
Pellet dies are commonly used in the preparation of samples for spectroscopic analysis techniques such as FTIR spectroscopy and X-Ray Fluorescence (XRF) spectroscopy.
For FTIR analysis, the sample is usually ground with an excess of potassium bromide (KBr) and pressed using a die with a 13mm internal diameter. Other diameters such as 5mm, 10mm, and 20mm are also available.
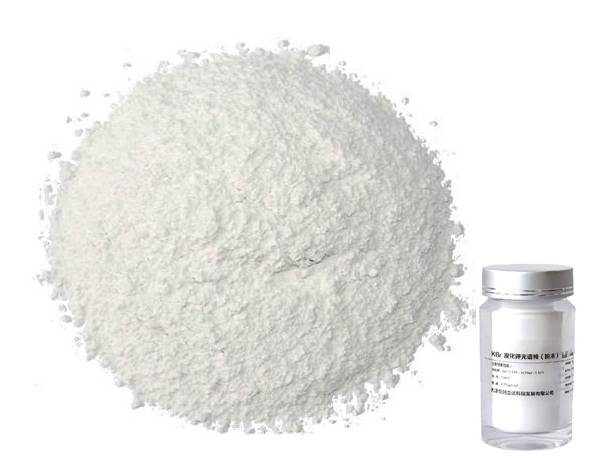
For samples to be analyzed with XRF, not all powders compact easily to form a pellet. In such cases, a sample support cup may be required. The support cup is a thin flexible dish made of aluminum that is placed inside the die before sample loading. When the powder is compacted, the support cup deforms around the bottom of the die and captures the sample, providing support from the bottom and sides while leaving the top surface exposed for analysis. Wax binding additives can be used to enhance the adherence of powder grains to one another.
KBR pellet die sets are essential tools for FTIR analysis, allowing for the efficient preparation of samples for accurate spectroscopic analysis. KinTek offers a range of high-quality die sets suitable for various applications in spectroscopy.
If you are interested in this product you can browse our company website:https://kindle-tech.com/thematics/xrf-pellet-press, we always insist on the principle of quality first. During the production process, we strictly control every step of the process, using high quality materials and advanced production technology to ensure the stability and durability of our products. to ensure that their performance meets the highest standards. We believe that only by providing customers with excellent quality can we win their trust and long-term cooperation.
CONTACT US FOR A FREE CONSULTATION
KINTEK LAB SOLUTION's products and services have been recognized by customers around the world. Our staff will be happy to assist with any inquiry you might have. Contact us for a free consultation and talk to a product specialist to find the most suitable solution for your application needs!