Classification of Muffle Furnace
By Heating Element
Muffle furnaces are distinguished by their heating elements, which significantly influence their performance and application areas. The primary types of heating elements include:
-
Electric Wire Muffle Furnace: This type utilizes electric resistance wires as the heating element. These wires are typically made from materials like nichrome, which offer a balance between resistance and durability. Electric wire muffle furnaces are versatile and widely used in various laboratory settings due to their reliability and ease of maintenance.
-
Silicon Carbon Rod Muffle Furnace: Silicon carbide rods serve as the heating elements in these furnaces. Known for their high resistance to thermal shock and excellent thermal conductivity, silicon carbide rods can operate at temperatures up to 1300°C. This makes them ideal for applications requiring high-temperature processing, such as ceramic sintering and glass annealing.
-
Silicon Molybdenum Rod Muffle Furnace: These furnaces use silicon molybdenum rods as heating elements, which can withstand temperatures exceeding 1600°C. Silicon molybdenum rods are prized for their high melting points and resistance to oxidation at high temperatures. This type of muffle furnace is particularly suited for advanced materials research and high-temperature synthesis processes.
Each type of heating element offers unique advantages and is selected based on the specific requirements of the application, such as temperature range, durability, and thermal efficiency.
By Temperature Range
Muffle furnaces are categorized based on their operational temperature ranges, each designed to meet specific heating requirements. Generally, these ranges are classified into three primary categories:
-
Box-Type Muffle Furnace (Below 1000°C):
- Ideal for applications requiring moderate temperatures.
- Commonly used in laboratories for routine heating processes.
- Offers a balance between cost and performance for lower temperature needs.
-
Silicon Carbon Rod Muffle Furnace (1100°C - 1300°C):
- Suitable for high-temperature applications.
- Utilizes silicon carbon rods as the heating element, providing efficient and stable heat.
- Widely used in materials testing and research where precise temperature control is essential.
-
Silicon Molybdenum Rod Muffle Furnace (Above 1600°C):
- Designed for ultra-high temperature applications.
- Employs silicon molybdenum rods, known for their high-temperature resistance and durability.
- Essential for advanced materials research and industrial processes requiring extreme heat.
Each temperature range offers unique advantages, ensuring that users can select the most suitable muffle furnace for their specific needs.
By Controller Type
Muffle furnaces can be categorized based on their control systems, which are essential for regulating temperature and ensuring precise heating processes. The two primary types of controller-based muffle furnaces are:
-
PID Control Muffle Furnace: This type utilizes a PID (Proportional-Integral-Derivative) controller, which is known for its accuracy and responsiveness in maintaining set temperatures. The PID controller is typically paired with a silicon digital display temperature controller. This combination allows for real-time monitoring and adjustment of the furnace's temperature, making it ideal for applications requiring high precision, such as scientific research and quality control in manufacturing.
-
Program Control Muffle Furnace: In contrast, the program control muffle furnace employs a computer temperature programmer. This advanced system allows users to pre-set specific temperature profiles and heating schedules, which can be particularly useful for processes that require multiple temperature steps or for automating repetitive tasks. The computer interface provides flexibility and ease of use, enabling complex heating protocols to be executed with minimal manual intervention.
These controller types cater to different operational needs, offering a balance between precision and flexibility in temperature management.
By Insulation Material
Muffle furnaces can be categorized based on their insulation materials, which play a crucial role in determining their thermal efficiency and durability. The primary types include:
-
Ordinary Refractory Brick Muffle Furnace: This type uses traditional refractory bricks for insulation. These bricks are known for their high resistance to heat and chemical erosion, making them suitable for maintaining consistent temperatures within the furnace. However, they tend to be heavier and less energy-efficient compared to modern alternatives.
-
Ceramic Fiber Muffle Furnace: This modern variant employs ceramic fibers for insulation. Ceramic fibers are lightweight, highly flexible, and offer superior thermal insulation properties. They can withstand extreme temperatures and are more energy-efficient, resulting in quicker heating and cooling cycles. This makes them ideal for applications requiring rapid temperature changes and precise control.
The choice between these two types depends on the specific requirements of the application, including temperature range, heating speed, and energy efficiency.
Installation Precautions
Initial Setup
Upon receiving the muffle furnace, the first step is to conduct a thorough inspection. Ensure that the furnace is intact and that all accessories are included, as per the manufacturer's specifications. Typically, a muffle furnace does not require any specialized installation procedures. It can be simply placed on a solid, flat surface, such as an indoor concrete table or a sturdy shelf. It is crucial to position the furnace in an area free from any flammable or explosive substances, ensuring a safe operational environment.
Additionally, consider the following steps to ensure a smooth initial setup:
- Check for Damages: Inspect the furnace for any visible damages or defects. This includes checking the exterior casing, door, and any visible wiring.
- Verify Accessories: Ensure that all accessories, such as thermocouples, controllers, and any specialized tools, are included and in good condition.
- Environmental Considerations: Place the furnace in a well-ventilated area to prevent the buildup of heat and fumes. Ensure the surrounding area is clear of any combustible materials.
By following these steps, you can ensure that your muffle furnace is ready for safe and effective use in ash detection.
Thermocouple Installation
When installing the thermocouple into the muffle furnace, it is crucial to position it correctly within the furnace chamber. Typically, the thermocouple should be inserted 20-50mm into the chamber to ensure accurate temperature readings. To maintain the integrity of the installation, use asbestos rope to fill any gaps between the hole and the thermocouple, ensuring a snug fit.
Connecting the thermocouple to the controller requires careful attention to detail. It is recommended to use compensation wire or insulated steel core wire for this purpose. This type of wire not only ensures reliable conductivity but also protects against potential hazards. Importantly, always double-check the polarity of the connections; the positive and negative poles must be correctly aligned. Incorrect polarity can lead to erroneous temperature readings and potential damage to the thermocouple or controller.
Connection Type | Recommended Use | Importance of Polarity |
---|---|---|
Compensation Wire | Ideal for maintaining accuracy | Critical |
Insulated Steel Core Wire | Provides robust protection | Essential |
By following these guidelines, you can ensure that your thermocouple installation is both accurate and safe, contributing to the overall efficiency and reliability of your muffle furnace operation.
Power Supply and Grounding
To ensure the safe and efficient operation of the muffle furnace, it is imperative to implement proper power supply and grounding measures. The installation process should begin with the introduction of a dedicated power switch, which allows for the control of the total power supply. This switch serves as a crucial safety measure, enabling operators to disconnect the power source when necessary, such as during maintenance or emergency situations.
In addition to the power switch, reliable grounding is essential for the furnace and its controller. Grounding helps to dissipate any electrical surges or faults, thereby protecting both the equipment and the operators from potential hazards. The grounding system should be thoroughly inspected and tested to ensure it meets the necessary standards and effectively mitigates risks.
To further enhance safety, consider the following best practices:
- Regular Inspections: Conduct routine checks on the power supply and grounding connections to ensure they remain intact and functional.
- Documentation: Maintain detailed records of all power supply and grounding installations, including the date of installation, type of materials used, and any maintenance activities performed.
- Training: Ensure that all operators are trained in the proper use of the power switch and the importance of grounding for safety.
By adhering to these guidelines, you can significantly reduce the risk of electrical accidents and ensure the longevity of your muffle furnace.
Temperature Adjustment
Before initiating operation, it is crucial to calibrate the thermostat to its zero point. This preliminary step ensures that the temperature readings are accurate and reliable. Once the thermostat is set to zero, the next step involves adjusting the temperature to the desired operating level. This can be achieved by using the temperature control knobs or digital interface, depending on the model of the muffle furnace.
To set the temperature, follow these steps:
- Identify the Required Temperature: Consult the experimental protocol or user manual to determine the optimal operating temperature for your specific application.
- Adjust the Thermostat: Use the control panel to input the desired temperature. Ensure that the temperature setting aligns with the furnace's capabilities, avoiding any setting that exceeds its maximum rated temperature.
- Power On: After confirming the temperature setting, turn on the power supply to the furnace. Monitor the temperature as it approaches the set point to ensure accurate heating.
Step | Action | Purpose |
---|---|---|
1 | Identify Required Temperature | Ensures the experiment is conducted at the optimal temperature |
2 | Adjust Thermostat | Sets the furnace to the correct operating temperature |
3 | Power On | Initiates the heating process |
By following these steps, you ensure that the muffle furnace operates efficiently and safely, contributing to accurate and reliable experimental results.
Daily Maintenance
Initial Use and Temperature Limits
When initiating the use of a muffle furnace, whether it's the first time or after an extended period of inactivity, it is imperative to conduct a thorough baking process. This initial step ensures that the furnace is properly conditioned and ready for operation. During this phase, it is crucial to adhere to the temperature guidelines provided by the manufacturer. Specifically, the maximum operating temperature should never exceed the furnace's rated temperature. This precaution is essential to prevent potential damage to the heating elements and to maintain the structural integrity of the furnace.
To provide a clearer understanding, here are some key points to consider during the initial use and temperature management:
- Baking Process: The furnace must undergo a controlled heating process to remove any moisture or contaminants that may have accumulated during storage. This typically involves gradually increasing the temperature over several hours.
- Temperature Monitoring: Continuous monitoring of the furnace temperature is necessary to ensure it remains within the safe operating range. Modern muffle furnaces are often equipped with advanced temperature controllers that provide real-time data and alerts.
- Temperature Limits: The maximum temperature should strictly follow the manufacturer's recommendations. Exceeding these limits can lead to rapid degradation of the heating elements and other critical components.
By adhering to these guidelines, users can ensure the longevity and optimal performance of their muffle furnace, thereby maintaining the accuracy and reliability of ash detection processes.
Environmental Conditions
The operation environment of a muffle furnace and its controller is crucial for maintaining optimal performance and ensuring safety. Relative humidity should not exceed 85% to prevent condensation and potential electrical faults. Conductive dust can interfere with the furnace's electrical components, leading to malfunctions or short circuits. Explosive or corrosive gases pose significant risks, as they can cause rapid deterioration of the furnace's materials and potentially lead to catastrophic failures.
To maintain a safe working environment, it is essential to:
- Monitor Humidity Levels: Regularly check and control the relative humidity within the workspace.
- Prevent Dust Accumulation: Implement measures to minimize the presence of conductive dust, such as regular cleaning and the use of protective covers.
- Control Gas Exposure: Ensure that the area around the muffle furnace is free from explosive or corrosive gases by using appropriate ventilation systems and storing chemicals safely.
Environmental Factor | Recommended Condition | Potential Issues |
---|---|---|
Relative Humidity | < 85% | Condensation, electrical faults |
Conductive Dust | None | Malfunctions, short circuits |
Explosive/Corrosive Gases | None | Material deterioration, catastrophic failures |
By adhering to these guidelines, you can significantly enhance the longevity and safety of your muffle furnace and controller.
Controller Environment
The environment in which the muffle furnace controller operates is a critical factor that directly impacts its performance and longevity. The controller, which is responsible for regulating the temperature within the furnace, should be situated in an ambient temperature range of 0 to 40 ℃. This temperature range ensures that the controller functions optimally without overheating or freezing, which could lead to malfunctions or reduced lifespan.
In addition to temperature, the controller's operating environment should be free from excessive humidity, ideally not exceeding 85% relative humidity. High humidity levels can cause condensation within the controller, leading to electrical failures or corrosion. Moreover, the presence of conductive dust, explosive gases, or corrosive substances should be strictly avoided, as these can pose significant risks to the controller's internal components and overall functionality.
To maintain the integrity and reliability of the muffle furnace controller, it is essential to place it in a well-ventilated area that is protected from direct sunlight and extreme temperature fluctuations. Regular inspections and maintenance of the controller, including checking the wiring and ensuring proper grounding, are also crucial steps in preserving its operational efficiency.
By adhering to these environmental guidelines, users can ensure that the muffle furnace controller operates smoothly, contributing to the accurate and safe functioning of the entire furnace system.
Regular Inspections
Regular and frequent inspections are crucial for maintaining the integrity and safety of the muffle furnace. These inspections should cover multiple components to ensure optimal functioning and prevent potential hazards.
-
Controller Wiring: The wiring connections between the controller and the furnace should be meticulously checked. Ensure that all connections are secure and free from any signs of wear or damage. Loose or corroded wires can lead to malfunctions and pose significant safety risks.
-
Thermocouple Grounding: The thermocouple, an essential component for temperature measurement, must be properly grounded. The metal protection tube, or shell, of the thermocouple should be securely grounded to prevent electrical interference and ensure accurate temperature readings. This grounding is particularly important in environments with high electromagnetic activity.
-
Visual Inspections: Conduct visual inspections of the furnace chamber and external components. Look for any signs of physical damage, such as cracks in the insulation or deformation of the furnace casing. These issues can compromise the furnace's performance and safety.
-
Operational Checks: Periodically test the furnace's operational parameters. This includes verifying the accuracy of the temperature controller and ensuring that the furnace reaches and maintains the set temperatures correctly. Any deviations should be addressed promptly to prevent inaccurate test results or equipment failure.
By adhering to these regular inspection protocols, users can ensure the longevity and reliability of their muffle furnace, thereby maintaining the accuracy and safety of their ash detection procedures.
Cleaning and Corrosion Prevention
Regular maintenance is crucial for the longevity and efficiency of a muffle furnace. One of the primary tasks in this maintenance routine is the meticulous cleaning of the furnace chamber. This involves the systematic removal of oxides, residues, and other contaminants that may accumulate during operation. The cleaning process should be conducted with precision to avoid any damage to the furnace's interior.
In addition to regular cleaning, the use of corrosive substances, such as alkaline materials, must be carefully managed. When melting specimens or cauterizing sediments with alkaline substances, it is imperative to strictly adhere to the recommended operating conditions. This includes controlling the temperature and duration of the process to prevent any adverse reactions that could lead to corrosion or damage.
To further safeguard the furnace, it is advisable to implement a schedule for periodic inspections. These inspections should focus on identifying any signs of wear or corrosion, particularly in areas exposed to high temperatures and chemical interactions. By addressing these issues promptly, you can significantly extend the lifespan of your muffle furnace and ensure its continued optimal performance.
Maintenance Task | Frequency | Purpose |
---|---|---|
Cleaning Furnace Chamber | Weekly | Removal of oxides and residues |
Inspection for Corrosion | Monthly | Identify and address wear and corrosion |
Control of Alkaline Use | As Needed | Prevent adverse chemical reactions |
By adhering to these maintenance practices, you can maintain a clean and corrosion-resistant environment within your muffle furnace, thereby enhancing its overall effectiveness and reliability.
Safe Operating Procedures
Temperature Control
To ensure the safe and effective operation of the resistance furnace, it is crucial to maintain strict temperature control. Exceeding the maximum allowable temperature can lead to irreversible damage to the furnace, compromising its performance and longevity. The recommended temperature ranges for different types of muffle furnaces are as follows:
Furnace Type | Temperature Range |
---|---|
Box-type muffle furnace | Below 1000°C |
Silicon carbon rod muffle furnace | 1100°C - 1300°C |
Silicon molybdenum rod muffle furnace | Above 1600°C |
Adhering to these temperature limits not only safeguards the equipment but also ensures accurate and consistent results in ash detection processes. Additionally, it is advisable to use a calibrated thermocouple and a reliable temperature controller to monitor and adjust the furnace temperature in real-time. This proactive approach helps in preventing overheating and maintaining optimal operational conditions.
Power Safety
Ensuring power safety is paramount when operating a muffle furnace, especially during critical tasks such as loading and unloading specimens. To prevent electric shock and ensure the safety of both the operator and the equipment, it is imperative to follow a few key procedures.
Firstly, always cut off the power supply before handling any specimens. This precautionary measure eliminates the risk of electric shock, which can be particularly hazardous when working with high-temperature equipment.
Additionally, it is advisable to double-check the power status before initiating any activity. This can be done by visually inspecting the power switch or using a multimeter to verify that the circuit is indeed off.
Moreover, regular maintenance and inspection of the power supply and grounding systems are crucial. Faulty wiring or inadequate grounding can lead to severe electrical hazards. Regular checks ensure that the system remains in optimal condition, reducing the likelihood of accidents.
Safety Measure | Description |
---|---|
Cut Off Power | Ensure the power supply is disconnected before loading or unloading specimens. |
Double-Check | Use a multimeter or visual inspection to confirm the power is off. |
Regular Inspections | Conduct routine checks on wiring and grounding to prevent electrical hazards. |
By adhering to these power safety protocols, you can significantly mitigate risks and ensure a safer working environment.
Loading and Unloading Specimens
When handling specimens in the muffle furnace, it is crucial to minimize the exposure time of the furnace door. This practice not only extends the overall service life of the furnace but also ensures consistent temperature within the chamber. To further protect yourself and the equipment, always wear heat-resistant gloves during the loading and unloading process. These gloves serve as a vital safeguard, preventing burns that could occur from direct contact with the hot surfaces or specimens.
Additionally, proper handling techniques are essential. Specimens should be placed in the middle of the furnace chamber to ensure even heating and avoid any potential damage to the furnace walls. It is also advisable to use appropriate tools, such as tongs, to handle the specimens, ensuring that the operation is both safe and efficient. By adhering to these guidelines, you can maintain the integrity of your experiments while ensuring the longevity and safety of your muffle furnace.
Specimen Handling
When handling specimens for insertion into the muffle furnace, it is crucial to ensure that they are free from any contaminants such as water or oil. Contaminated specimens can lead to inaccurate test results and potentially damage the furnace chamber. Similarly, clamps used to load the specimens should also be clean and free from such contaminants to prevent any cross-contamination or damage.
The specimen should be carefully placed in the central area of the furnace chamber. Proper placement ensures even heating and consistent results. It is advisable to arrange the specimen neatly to avoid any obstructions or uneven distribution of heat. Avoid placing the specimen haphazardly, as this can lead to suboptimal conditions for the test.
Handling Step | Precaution |
---|---|
Specimen | Ensure free from water and oil contaminants |
Clamps | Ensure clamps are clean and free from contaminants |
Placement | Place in the middle of the furnace chamber, neatly arranged |
By adhering to these guidelines, you can maintain the integrity of your testing environment and ensure the reliability of your results.
Post-Use Procedures
After completing the operation of the resistance furnace, it is crucial to immediately cut off the power supply and water supply to ensure safety and prevent any potential hazards. This step is essential to safeguard both the equipment and the operator. Without explicit authorization from management personnel, no one should attempt to operate the resistance furnace. This strict adherence to operating procedures is non-negotiable to maintain the integrity and longevity of the equipment.
Moreover, it is advisable to conduct a thorough inspection of the furnace and its surroundings post-use. This includes checking for any signs of damage, ensuring all components are in their proper places, and verifying that the environment is free from flammable or explosive substances. Regular inspections can help identify and address potential issues before they escalate, thereby enhancing the overall operational safety and efficiency.
Lastly, cleaning and maintenance should be performed regularly. This involves removing any residues or debris from the furnace chamber to prevent contamination and ensure optimal performance in future uses. By following these post-use procedures meticulously, one can significantly enhance the safety and reliability of the resistance furnace in ash detection applications.
Ash Testing Precautions
Sample Pre-Treatment
After the preliminary cauterization, the sample is carefully removed and allowed to cool. To facilitate the dissolution of water-soluble salts and the exposure of encapsulated carbon particles, a small amount of deionized water is slowly added from the edge of the crucible. This process is crucial for ensuring that the salts are effectively dissolved without causing any splashing or loss of sample material.
Once the salts are dissolved, the mixture is gently evaporated on a water bath to remove the excess water. The crucible is then transferred to an oven set at a temperature range of 120°C to 130°C. This step is essential for fully drying the sample, ensuring that all residual moisture is eliminated.
Finally, the crucible is subjected to further cauterization until it reaches a constant weight. This final step ensures that the sample is thoroughly processed and ready for subsequent analysis.
Step | Description |
---|---|
1 | Cooling: Allow the sample to cool after preliminary cauterization. |
2 | Dissolution: Slowly add deionized water to dissolve water-soluble salts. |
3 | Evaporation: Gently evaporate the water on a water bath. |
4 | Drying: Place the crucible in an oven at 120°C to 130°C for full drying. |
5 | Cauterization: Subject the crucible to further cauterization until a constant weight is achieved. |
Crucible Handling
When transferring a crucible into or out of a muffle furnace, it is crucial to handle it with care to avoid thermal shock. This involves allowing the crucible to acclimate to the ambient temperature at the furnace's mouth before fully inserting it or removing it. By doing so, you can mitigate the risk of the crucible cracking or shattering due to sudden temperature changes.
Here are the steps to safely handle crucibles:
-
Preheat the Crucible: When placing the crucible into the furnace, hold it at the furnace's mouth for a few moments to allow it to gradually heat up. This preheating process helps in equalizing the temperature gradient, reducing the likelihood of thermal stress.
-
Cool Down the Crucible: Similarly, when taking the crucible out of the furnace, pause at the mouth of the furnace to let it cool slightly. This gradual cooling prevents rapid contraction that could lead to cracks or fractures.
-
Use Appropriate Tools: Always use crucible tongs that have been preheated to avoid introducing a cold surface that could cause thermal shock. Preheating the tongs ensures they are at a similar temperature to the crucible, minimizing temperature discrepancies.
-
Monitor Temperature Changes: Continuously monitor the temperature changes both inside the furnace and the ambient environment around the crucible. This helps in maintaining a controlled thermal environment, essential for preventing thermal shock.
By adhering to these practices, you can ensure the longevity and integrity of your crucibles, thereby maintaining the accuracy and reliability of your ash detection experiments.
Crucible Tongs
Crucible tongs are essential tools for safely handling crucibles, especially when dealing with high temperatures in an electric furnace or muffle furnace. To ensure the integrity of both the crucible and the tongs, it is crucial to preheat the tongs before use. This preheating process helps to equalize the temperature between the tongs and the crucible, preventing thermal shock that could lead to damage or failure.
When using crucible tongs, it is advisable to select a pair that fits the crucible snugly. Improperly fitting tongs can cause the crucible to slip or tilt, potentially leading to spills or breakage. Additionally, placing a piece of cardboard between the crucible and the furnace base before heating can provide an extra layer of protection. As the cardboard burns off, it leaves a carbon layer that prevents the crucible from bonding to the furnace bottom.
To further safeguard the crucible, it is recommended to use different crucibles for different types of metals to avoid contamination. After each use, ensure that the crucible is completely emptied to prevent any residual metal from expanding upon re-heating, which could lead to cracking or destruction of the crucible.
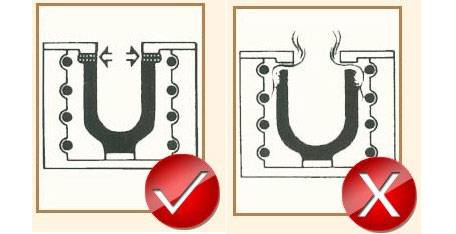
Before using a new crucible, it should be "tempered" to remove any moisture. This involves heating the empty crucible to approximately 500°F (260°C) and maintaining that temperature for about 20 minutes. Subsequently, the crucible should be brought to red heat, the heat source turned off, and the crucible allowed to cool slowly. Once cooled, the crucible is ready for use, ensuring a longer lifespan and better performance during high-temperature operations.
Cooling and Storage
After the burning process is complete, it is crucial to ensure that the crucible is cooled down to a temperature below 200℃ before transferring it into a drier. This gradual cooling process helps in maintaining the integrity of the crucible and prevents any thermal shock that could lead to cracking.
When it comes to removing the crucible from the desiccator, it is essential to exercise caution. The action should be performed slowly and deliberately to allow air to flow gradually. This slow air flow helps in preventing any residual ash from scattering, thereby maintaining a clean working environment and preserving the integrity of the sample.
To summarize, the cooling and storage procedures for the crucible involve:
- Cooling: Gradually cooling the crucible to below 200℃.
- Storage: Carefully transferring the cooled crucible into a drier.
- Removal: Easing the removal of the crucible from the desiccator to prevent ash scattering.
These steps are integral to ensuring the accuracy and safety of the ash detection process.
CONTACT US FOR A FREE CONSULTATION
KINTEK LAB SOLUTION's products and services have been recognized by customers around the world. Our staff will be happy to assist with any inquiry you might have. Contact us for a free consultation and talk to a product specialist to find the most suitable solution for your application needs!