Pressed and Loose Powder Methods
Table of Contents
- Pressed and Loose Powder Methods
- Overview of two main sample preparation techniques for powder measurements with XRF: pressed and loose powder methods
- Selection of appropriate accessories and sample preparation to prevent breakage during measurement
- Importance of selecting the right method to minimize analysis errors of target elements
- Pressed Pellets Preparation
- Pelletization of Difficult Powders
- Use of binder for pelletizing powders that are difficult to form into pellets
- Potential contamination issues with fine powder particles in vacuum mode
- Challenges with pelletizing spherically shaped particles
- Typical mixing ratio of sample to binder
- Importance of selecting a binder that does not include the elements to be analyzed
- Types of commonly used binders
- Importance of accurate weighing and complete mixing to minimize analysis errors
- Press Machines
- Availability of manual and automatic press machines
- Maximum load options for press machines
- Use of both flat and cylinder type dies in press machines
- Effect of pelletization pressure on X-ray intensity
- Need for consistent sample amount and pressure for each pellet preparation
- Issues with pressure release after pelletization
- Considerations in Pressed Powder Method
- Methods for Small Quantity Sample Preparation
Overview of two main sample preparation techniques for powder measurements with XRF: pressed and loose powder methods
X-ray fluorescence (XRF) analysis is a common technique used for analyzing powders in various industries. When it comes to preparing powder samples for XRF analysis, there are two main methods: pressed powder method and loose powder method.
The pressed powder method involves compressing the sample into a pellet or disk, while the loose powder method involves simply placing the sample into a cup or container. Each method has its advantages and disadvantages, and the choice of method depends on the specific requirements of the analysis.
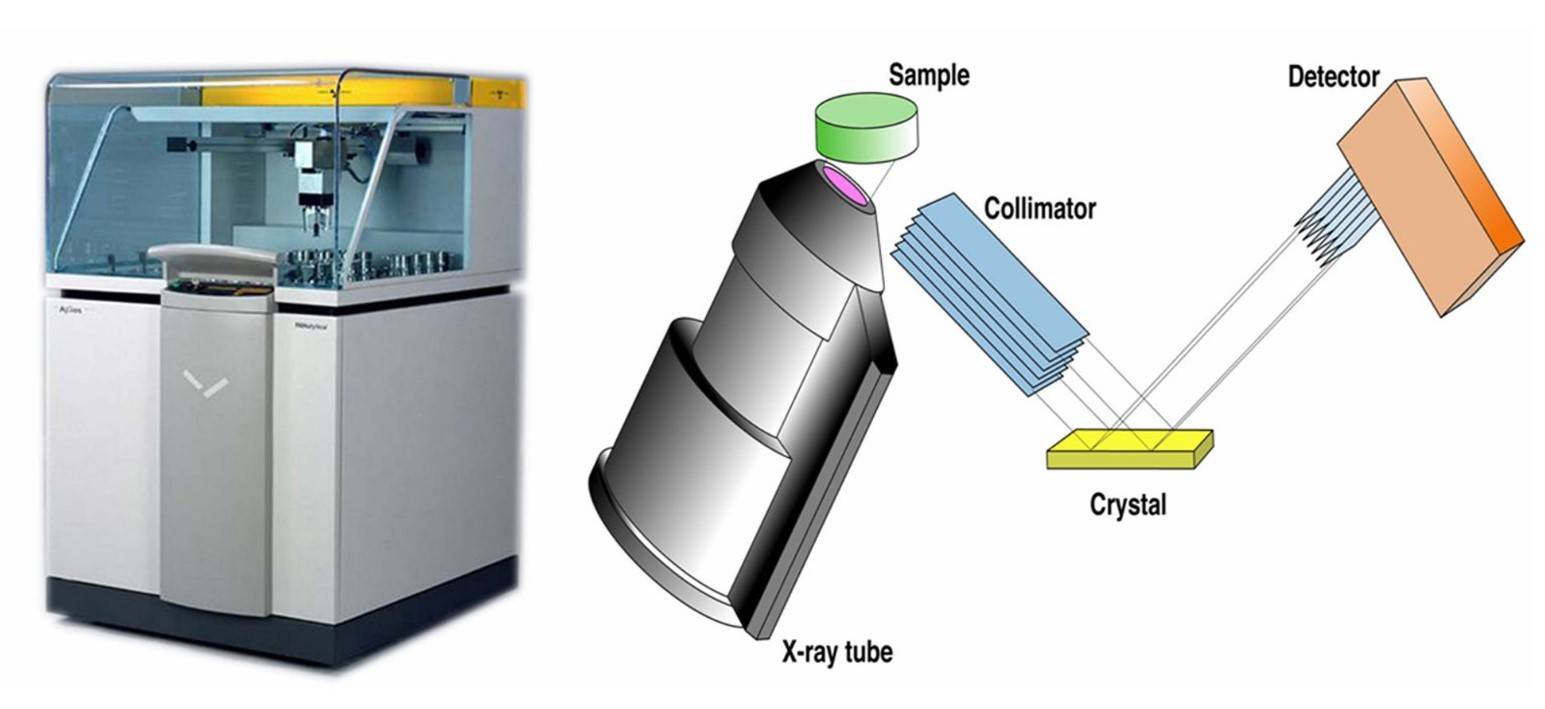
Selection of appropriate accessories and sample preparation to prevent breakage during measurement
In order to ensure accurate and reliable measurements, it is important to select the appropriate accessories and prepare the sample properly to prevent breakage during measurement.
For the pressed powder method, it is important to choose the appropriate die material and pressure. Aluminum rings are preferred for samples that expand after pressure release, while rings that do not expand are chosen for samples that do not expand. It is also recommended to release pressure several times before reaching the target pressure to avoid sample breakage due to trapped air expansion.
Importance of selecting the right method to minimize analysis errors of target elements
Selecting the right sample preparation method is crucial to minimize analysis errors of target elements. The pressed powder method provides better analytical results than loose powders because the grinding and compression create a more homogeneous representation of the sample with no void spaces and little sample dilution. This leads to higher intensities for most elements than loose powders.
Pressed pellets are also relatively simple and inexpensive to prepare, only requiring a pulverizing mill and sample press. They are excellent for the analysis of elements in the ppm range. However, it is important to note that pressed pellets are still susceptible to particle size effects if not ground fine enough, and mineralogical effects can also affect the analysis of major elements.
In conclusion, the choice between pressed and loose powder methods for sample preparation in XRF analysis depends on the specific requirements of the analysis. The pressed powder method provides better analytical results and is suitable for samples with narrow calibration ranges. On the other hand, the loose powder method is more practical and convenient for screening or quick control of raw materials. By selecting the appropriate accessories and sample preparation techniques, you can prevent breakage during measurement and minimize analysis errors of target elements.
Pressed Pellets Preparation
Pressed pellets are prepared by pressing loose powders filled in a ring or cup using a set of dies and a press machine. There are two types of dies, namely flat disc and cylinder types. The type to be used depends on the characteristic of the powder sample. Ease of pelletization depends on sample characteristics and grain size and can be improved by sufficient pulverization. Mixing the powder sample with a forming agent (binder) is another solution if pelletization is difficult. Rings and cups used for forming pressed pellets are available in various sizes with 10 –43 mm inner diameter and are made of either aluminum or PVC. Cup materials are either aluminum or iron, and available inner diameters are 32–45 mm. The selection of die type depends on the characteristics of the sample.
What is a pellet die?
A pellet die is a simple tool used to form thin cylindrical pellets from a powder using a pellet press. At its simplest, a pellet die consists of a hollow cylindrical body capped at one end, which forms a blind tube into which a powder sample is poured.
How does a pellet die work?
The cap usually forms the base of the die. A plunger is then inserted into the tube to complete the assembly. The die is then transferred to a press, which applies a load of several tons to the plunger, compressing the powder against the base and walls of the tube.
If sufficient load is applied, the powder grains will bind to form a solid that can be removed by separating the base from the body and applying a small load to the plunger to push the pellet out from the die body.
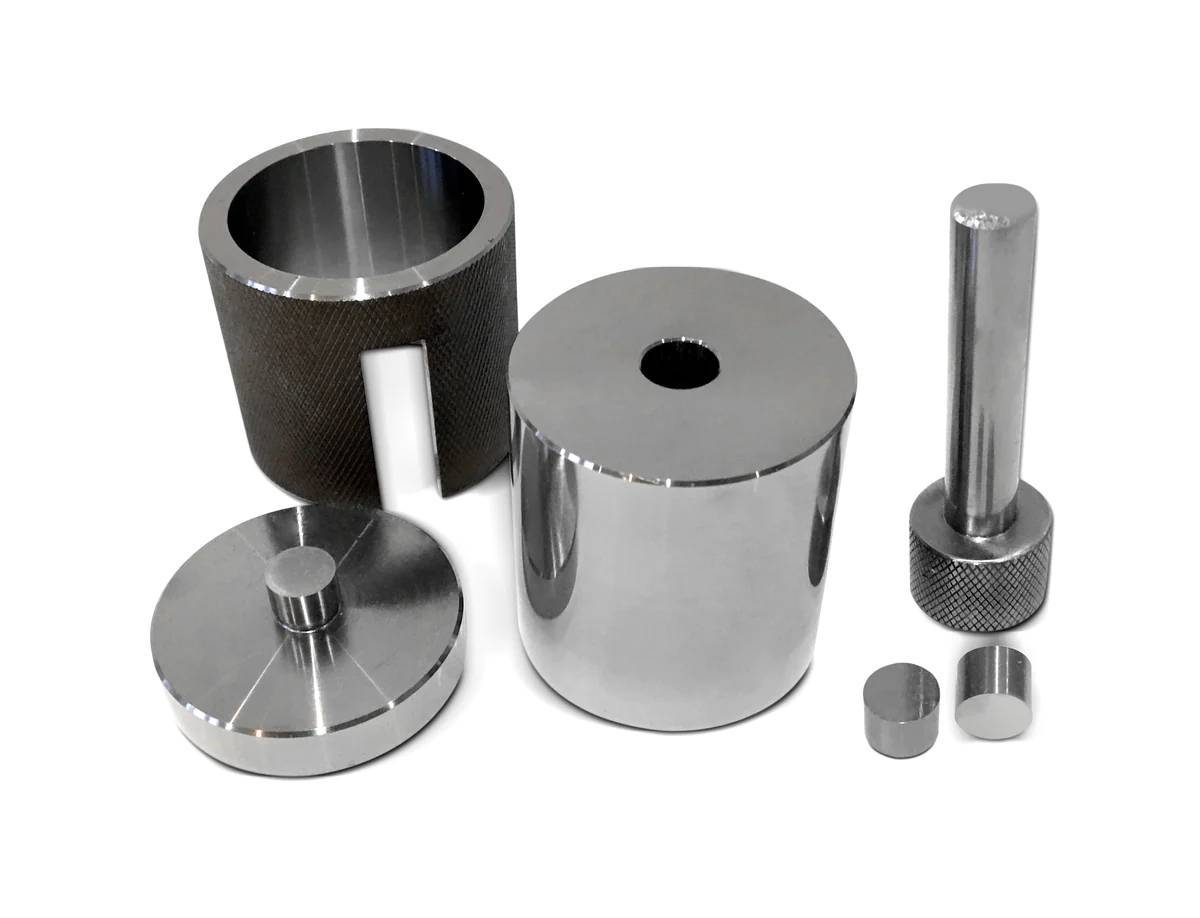
Laboratory pellet dies
In laboratories, pellet dies are typically used for the preparation of test specimens for analysis.
Sample Preparation for Pressed Pellets
The process of making pressed pellets for XRF analysis includes grinding the sample to a fine particle size, mixing it with a binder/ grinding aid in a grinding or mixing vessel, pouring the mixture into a pressing die and pressing the sample at a pressure of between 15 and 35T. The resulting pellet or tablet is then ready for analysis. While this is a common and relatively straightforward approach to preparing samples for XRF analysis, there are several important aspects that should be considered when designing a sample preparation protocol. These include the particle size of the sample, the choice of binder, the dilution ratio, the amount of pressure applied to the sample and the thickness of the final pellet. An additional consideration is sample contamination.
Loose powders and granulates in liquid cups
For screening or quick control of raw materials, you could analyze granulates and powders ‘as is’ in liquid cups. This practical and quick solution has its advantages when accuracy and reproducibility are not the driving factors. There will be a loss of intensity for light elements though.
Pressing
Pressed powders are often very successfully used in production control, especially if the calibration ranges are narrow.
Pellets can be pressed free, into Al cups or steel rings. The use of binders is usually required to achieve the necessary mechanical stability and robustness.
Hot-pressing
Granulates, fibers or powders from hot-moldable polymers, like PE or PP are ideally prepared by hot-pressing into solid homogeneous disks. The choice of the correct temperature and pressure is fundamental for the reproducibility of the analytical method.

Contamination from the die surface is a concern when pelletizing samples.
To prevent contamination, it is recommended to clean the die surface before each pelletization and to start with lower concentrations. A film can be placed between the powder and the die to minimize contamination and prevent powder sticking.
If the sample quantity is too small for pelletization, the double pellet or embedded methods can be used. These methods involve covering a previously pressed powder with a small amount of sample and pelletizing again, or placing the sample in the center of a previously formed pellet and reapplying pressure to form the embedded pellet.
The grass sample can be pressed onto polypropylene discs with an adhesive surface, which can be used in combination with cylinder-type dies for small quantities of dried grass sample or powder.
Summary
The most common contributors to error in the preparation of pressed pellets include the particle size of the sample, the choice of binder, the dilution ratio, the amount of pressure applied to the sample, the thickness of the final pellet and sample to sample cross contamination. The best practices for limiting this error require good method development coupled with attention to detail and consistency.
Pressed Pellets
Pressing powder into pellets is a more rigorous sample preparation than pouring loose powders into a sample cup. The process includes grinding a sample into a fine powder, ideally to a grain size of <75um, mixing it with a binding /grinding aid and then pressing the mixture in a die at between 20 and 30T to produce a homogeneous sample pellet. The binding /grinding aid is usually a cellulose wax mixture and combines with the sample in a proportion of 20%-30% binder to sample.
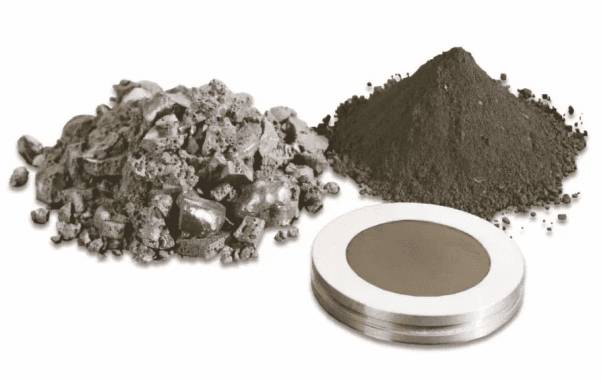
Pelletization of Difficult Powders
Use of binder for pelletizing powders that are difficult to form into pellets
Pressed pellets are prepared by pressing loose powders filled in a ring or cup using a set of dies and a press machine. The type of die used depends on the characteristics of the powder sample. If pelletization is difficult, one solution is to mix the powder sample with a forming agent, also known as a binder. This binder helps to hold the powders together during the mixing and pressing stages, making it easier to form pellets.
Potential contamination issues with fine powder particles in vacuum mode
When pelletizing powders in vacuum mode, there is a risk of contamination from fine powder particles. Without a binder, these particles may fall off or scatter from the pellet surface, potentially contaminating the sample chamber of the spectrometer. To avoid this issue, it is important to use a binder that can effectively bind the powders together and minimize the risk of contamination.
Challenges with pelletizing spherically shaped particles
Powders with particles that are spherically shaped, such as SiO2 or burned ash, can be difficult to pelletize. The shape of these particles makes it challenging for them to bind together and form pellets. In such cases, the use of a binder becomes even more important to improve the pelletization process.
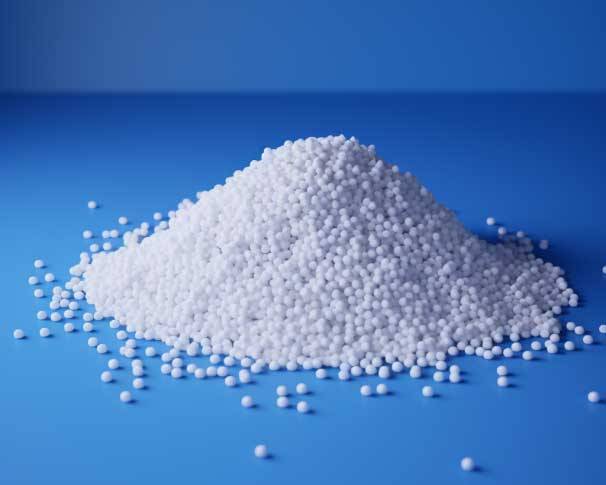
Typical mixing ratio of sample to binder
The typical mixing ratio of sample to binder is 10(sample) : 1(binder) or 10 : 2. This means that for every 10 parts of the sample, 1 or 2 parts of binder are used. It is important to maintain consistency in the mixing ratio for accurate results and to avoid over-diluting the sample.
Importance of selecting a binder that does not include the elements to be analyzed
When selecting a binder, it is crucial to choose one that does not include the elements to be analyzed. This is because the content of the pellet is analyzed in spectroscopy, and any binder contamination can interfere with the analysis. Therefore, it is recommended to use a binder that is free from the elements of interest.
Types of commonly used binders
Some commonly used binders for pelletization include wax types called Spectro Blend, polystyrene-based powders, and boric acid and cellulose powders. These binders have proven to be effective in holding the powders together during the pelletizing process.
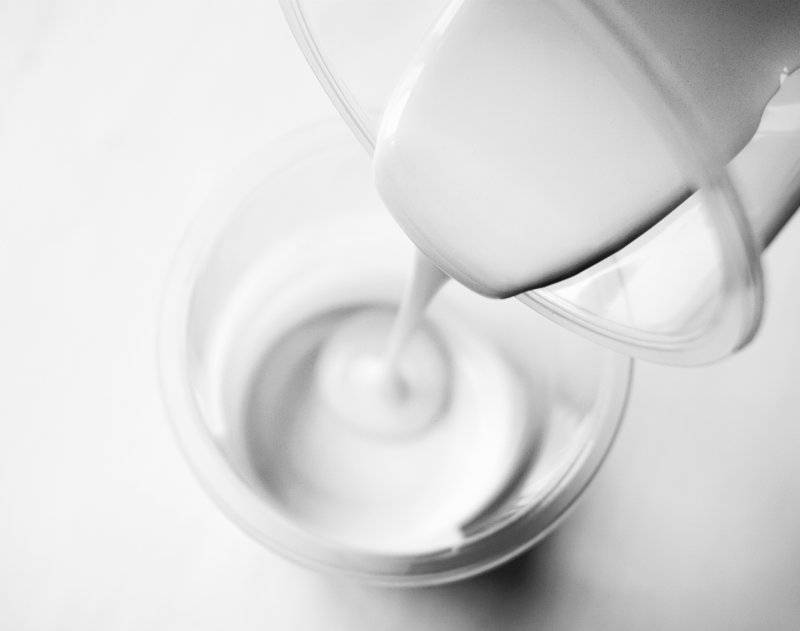
Importance of accurate weighing and complete mixing to minimize analysis errors
Accurate weighing and complete mixing of the sample and binder are essential to minimize analysis errors. Inaccurate weighing or incomplete mixing can lead to inconsistent pellet formation and skewed results. Therefore, attention to detail and consistency in the weighing and mixing process are crucial for obtaining reliable analytical results.
Press Machines
Availability of manual and automatic press machines
Press machines are essential tools in various industries, including woodworking, laboratory analysis, and manufacturing. These machines are available in both manual and automatic models, allowing businesses to choose the one that suits their specific production techniques and methods.
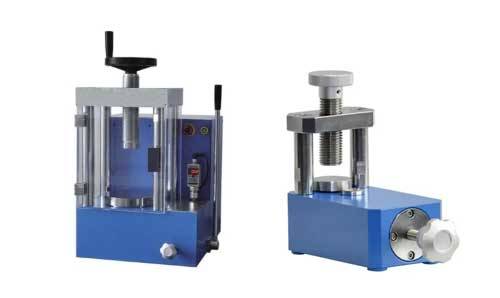
Manual press machines, such as the Manual Hydraulic Pellet Press, offer a simple and easy operation for the preparation of pellets used in spectral analyses like X-ray fluorescence analysis or infrared spectroscopy. These machines come with pressing tools of different diameters, variable pressure force, and a clearly designed pressure force display. They are compact, solid, and easy to clean, making them ideal for laboratory use.
On the other hand, automatic press machines, like the ones provided by KINTEK, offer advanced features and precise force generation for efficient sample preparation. These machines are operated with a button and often have automated actions for pressing and releasing the die. They are versatile and can be used for various applications, including hot embossing, laminating, and melting polymers for thin films.
Maximum load options for press machines
Both manual and automatic press machines have maximum load options to ensure efficient and effective pelletization. The maximum load refers to the amount of force that can be applied to the sample during the pressing process.
For example, the manual hydraulic pellet press offers a variable pressure force of up to 250 kN. This allows for the preparation of high-quality pellets with a smooth, homogeneous surface. The pressing tools available for this machine range from 15 mm to 40 mm in diameter, providing flexibility in pellet size.
Similarly, automatic press machines, like the ones provided by KINTEK, have different models with varying maximum load options. These machines can generate precise and consistent force, ensuring that the sample is completely compacted and ready for analysis.
Use of both flat and cylinder type dies in press machines
Pressed pellets are prepared by pressing loose powders filled in a ring or cup using a set of dies and a press machine. There are two types of dies commonly used: flat disc and cylinder types. The choice of die type depends on the characteristics of the powder sample.
Flat disc dies are suitable for samples with fine particle size and homogeneous composition. They provide a smooth and uniform pellet surface, making them ideal for spectral analyses like infrared spectroscopy.
Cylinder dies, on the other hand, are often used for samples with larger particle size or samples that require a higher pressure for compaction. They can provide more pressure and force during the pressing process, resulting in denser and more compact pellets.
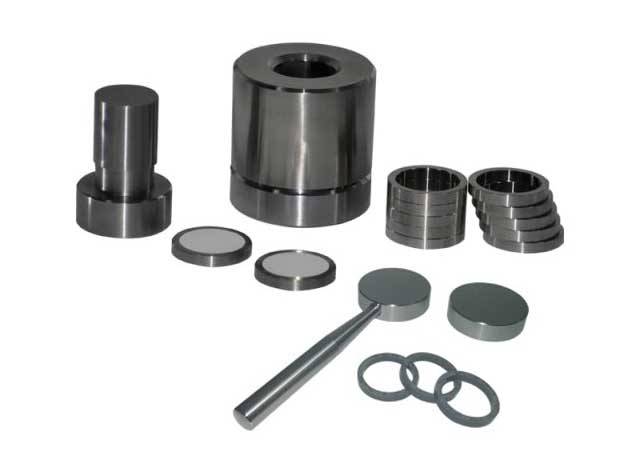
The selection of die type depends on the specific characteristics of the sample and the desired outcome of the analysis.
Effect of pelletization pressure on X-ray intensity
The pressure applied during pelletization can have an effect on the X-ray intensity of the sample. It is important to keep the sample amount and pressure constant for each pellet preparation to minimize errors and inconsistencies in the analysis.
When a mixed sample and KBr powder are compressed inside a die using a hydraulic press, the uniform force applied produces a solid pellet that is mostly transparent to infrared light. However, the pellet also contains a dilute quantity of sample within the detection range of an FTIR instrument.
To achieve consistent and reliable X-ray intensity results, it is recommended to pelletize the sample with a pressure at which the X-ray intensity saturates. This ensures that the sample is properly compacted and prepared for accurate analysis.
Need for consistent sample amount and pressure for each pellet preparation
Consistency is key in sample preparation for accurate analysis. It is important to maintain a consistent sample amount and pressure for each pellet preparation to minimize errors and ensure reproducibility.
The amount of sample used for pelletization should be consistent to avoid variations in the analysis results. Similarly, the pressure applied during the pressing process should be controlled and kept constant to achieve uniform and reliable pellet formation.
By maintaining consistent sample amount and pressure, businesses can ensure the accuracy and reproducibility of their analysis results.
Issues with pressure release after pelletization
After the pelletization process, it is important to release the pressure properly to avoid potential issues. The compressed ring and sample can slowly expand over time when the pressure is released, leading to height differences between the sample surface and the ring.
This height difference can result in changes in X-ray intensity or even breakage of the pellet. To prevent these issues, it is recommended to release the pressure slowly and carefully, allowing the pellet to adjust without causing any damage.
Businesses should pay attention to the pressure release process to ensure the integrity and reliability of their analysis results.
In conclusion, press machines are valuable tools in various industries, offering reliable performance and efficient sample preparation. Whether manual or automatic, these machines provide the necessary force and pressure for pelletization. The use of different types of dies allows for flexibility in sample preparation. It is important to maintain consistent sample amount and pressure for accurate analysis, and proper pressure release is crucial to avoid potential issues. By investing in high-quality press machines, businesses can optimize their production processes and achieve reliable analysis results.
Considerations in Pressed Powder Method
Choosing appropriate die material and pressure
When using the pressed powder method for sample preparation in X-ray fluorescence analysis, it is important to consider the appropriate die material and pressure. Aluminum rings are preferred for samples that expand after pressure release, while rings that do not expand are chosen for samples that do not expand. The choice of die material should be based on the specific characteristics of the sample.
Recommendation for pressure release to avoid sample breakage
To avoid sample breakage during the pressed powder method, it is recommended to release pressure several times before reaching the target pressure. This helps to prevent sample breakage due to trapped air expansion. By gradually increasing the pressure and releasing it multiple times, the sample can be effectively compressed without any damage.
Concerns about contamination from die surface during pelletizing
Contamination from the die surface is a common concern when pelletizing samples using the pressed powder method. To minimize contamination, it is recommended to clean the die surface before each pelletization and to start with lower concentrations. This helps to ensure that the resulting pellet is free from any unwanted contaminants.
Preventive measures for contamination
In addition to cleaning the die surface, there are other preventive measures that can be taken to minimize contamination during pelletizing. One effective measure is to use a film between the powder and the die. This film acts as a barrier, preventing direct contact between the powder and the die surface. This helps to minimize the risk of contamination and also prevents the powder from sticking to the die.
Use of a film between the powder and die to prevent sticking
To prevent sticking of the powder to the die during pelletizing, it is recommended to use a film between the powder and the die. This film acts as a lubricant, reducing the friction between the powder and the die surface. By using a film, the powder can be easily compressed into a pellet without any sticking issues.
In summary, the pressed powder method for sample preparation in X-ray fluorescence analysis requires careful consideration of various factors. Choosing the appropriate die material and pressure, releasing pressure gradually to avoid sample breakage, preventing contamination from the die surface, and using a film to prevent sticking are all important considerations. By following these guidelines, accurate and reliable sample pellets can be obtained for analysis.
Methods for Small Quantity Sample Preparation
Use of double pellet or embedded methods for small sample quantities
If the sample quantity is too small for traditional pelletization methods, such as pressing powders into pellets, the double pellet or embedded methods can be used. These methods allow for the preparation of small sample quantities by either covering a previously pressed powder with a small amount of sample and pelletizing again, or by placing the sample in the center of a previously formed pellet and reapplying pressure to form the embedded pellet. This is especially useful when working with limited sample sizes or when trying to conserve precious or rare samples.
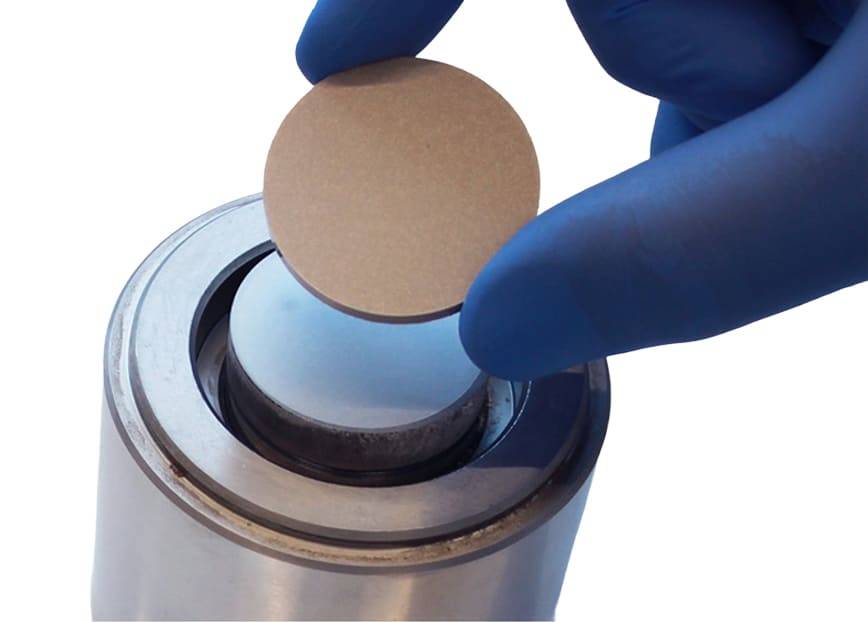
Process of double pellet and embedded methods
The double pellet method involves first pressing a powder sample into a pellet, and then covering it with a small amount of additional sample material. The pellet is then pressed again to form a new pellet with the combined sample materials. This method allows for the analysis of small sample quantities without the need for additional sample preparation steps.
In the embedded method, a previously formed pellet is taken and a small amount of sample material is placed in the center. Pressure is then applied to the pellet to form the embedded sample pellet. This method is particularly useful when the sample material is too small to be pressed into a pellet on its own.
Both the double pellet and embedded methods provide a way to analyze small sample quantities without the need for extensive sample preparation. These methods can be especially beneficial in situations where the sample is limited or difficult to obtain.
Use of polypropylene discs with adhesive surface for small dried grass samples or powder
For small quantities of dried grass samples or powder, polypropylene discs with an adhesive surface can be used. These discs provide a convenient way to hold the sample material in place during the pelletization process. The sample is pressed onto the adhesive surface of the disc, ensuring that it remains in position during the pelletization process.
Polypropylene discs with adhesive surfaces are particularly useful for small quantities of sample material that may be difficult to handle or manipulate during traditional sample preparation methods. By using these discs, the sample material can be securely held in place, allowing for easier handling and preparation.
In summary, when working with small sample quantities, there are several methods that can be used for sample preparation. The double pellet and embedded methods provide options for analyzing small quantities of sample material without the need for extensive sample preparation steps. Additionally, the use of polypropylene discs with adhesive surfaces can be beneficial for small dried grass samples or powder. These methods offer flexibility and convenience for small quantity sample preparation in various analytical applications.
If you are interested in this product you can browse our company website:https://kindle-tech.com/product-categories/heated-lab-press, we understand that every customer's needs are unique. Therefore, we offer a flexible customisation service to meet your specific requirements. Whether it is the specification, functionality or design of the equipment, we are able to personalise it to suit your needs. Our dedicated team will work closely with you to ensure that the customised solution will perfectly meet your experimental needs.
CONTACT US FOR A FREE CONSULTATION
KINTEK LAB SOLUTION's products and services have been recognized by customers around the world. Our staff will be happy to assist with any inquiry you might have. Contact us for a free consultation and talk to a product specialist to find the most suitable solution for your application needs!