Conventional pyrolysis is typically conducted at temperatures ranging from 350°C to 1000°C, depending on the specific type of pyrolysis process being employed. For instance, slow pyrolysis often operates at lower temperatures (350-400°C), while fast pyrolysis occurs at around 500°C. Medium-temperature pyrolysis ranges between 600-700°C, and high-temperature pyrolysis for materials like pyrocarbon can reach up to 800-1000°C. Each temperature range is optimized for specific outcomes, such as maximizing bio-oil, bio-char, or syngas yields. The choice of temperature depends on the desired end products and the feedstock being processed.
Key Points Explained:
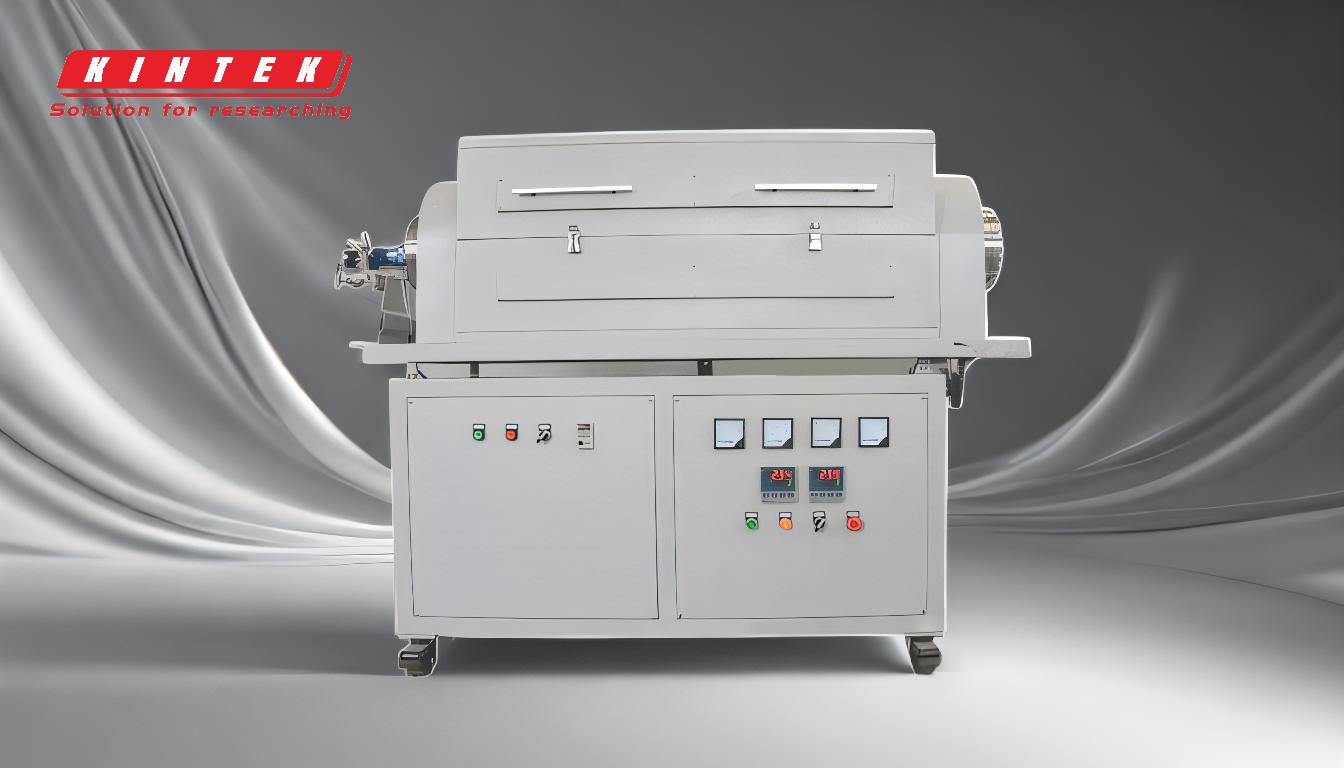
-
Temperature Ranges for Different Pyrolysis Types:
- Slow Pyrolysis: Conducted at 350-400°C, often used for producing bio-char and syngas. It involves lower heating rates (1-30°C/min) and longer residence times.
- Fast Pyrolysis: Operates at around 500°C with high heating rates (up to 1000°C/s). This process is optimized for bio-oil production, yielding 60-70 wt% bio-oil.
- Medium-Temperature Pyrolysis: Occurs between 600-700°C, often used for intermediate products and specific feedstock types.
- High-Temperature Pyrolysis: Reaches 800-1000°C, typically for producing pyrocarbon or other high-value materials.
-
Factors Influencing Temperature Selection:
- Feedstock Type: Different materials (e.g., biomass, plastics, rubber) require specific temperature ranges for optimal breakdown.
- Desired Products: Bio-oil, bio-char, and syngas yields vary significantly with temperature. For example, fast pyrolysis at 500°C maximizes bio-oil, while slow pyrolysis at 350-400°C favors bio-char.
- Heating Rate and Residence Time: Faster heating rates (e.g., 1000°C/s in fast pyrolysis) require higher temperatures for rapid decomposition.
-
Process Conditions:
- Pressure: Pyrolysis is typically conducted at atmospheric pressure, though some processes (e.g., involving liquid and gaseous species) may operate at 1-30 bar.
- Environment: An oxygen-free or oxygen-limited environment is essential to prevent combustion and ensure controlled thermal decomposition.
-
Equipment Considerations:
- Reactor Design: Pyrolysis reactors must withstand high temperatures and corrosive environments. For example, refractory alloy tubes are used for processes at 700-1200°C.
- Heat Source: External energy sources, such as gas combustion or partial feedstock combustion, are commonly used to maintain the required temperatures.
-
Applications and Outcomes:
- Bio-Oil Production: Fast pyrolysis at 500°C is ideal for generating bio-oil, a renewable fuel alternative.
- Bio-Char and Syngas: Slow pyrolysis at 350-400°C produces bio-char (used in agriculture) and syngas (a fuel gas).
- High-Value Materials: High-temperature pyrolysis (800-1000°C) is used to produce pyrocarbon, a material with applications in electronics and advanced manufacturing.
By understanding these key points, equipment and consumable purchasers can make informed decisions about the pyrolysis systems and materials best suited for their specific needs.
Summary Table:
Pyrolysis Type | Temperature Range | Key Products | Heating Rate |
---|---|---|---|
Slow Pyrolysis | 350-400°C | Bio-char, Syngas | 1-30°C/min |
Fast Pyrolysis | ~500°C | Bio-oil | Up to 1000°C/s |
Medium-Temperature | 600-700°C | Intermediate Products | Varies |
High-Temperature | 800-1000°C | Pyrocarbon | Varies |
Need help selecting the right pyrolysis system for your needs? Contact our experts today!