Crucibles are specifically designed to withstand extreme heat, making them indispensable in high-temperature applications such as metallurgy, chemistry, and materials science. They are constructed from durable materials like graphite, ceramic, or refractory metals, which can endure temperatures ranging from 2000 °C to as high as 3000 °C, depending on the material. Their ability to resist heat stress, chemical reactions, and contamination ensures their effectiveness in melting metals, conducting experiments, and processing materials. This makes crucibles a reliable tool for industries and laboratories requiring precision and durability under extreme conditions.
Key Points Explained:
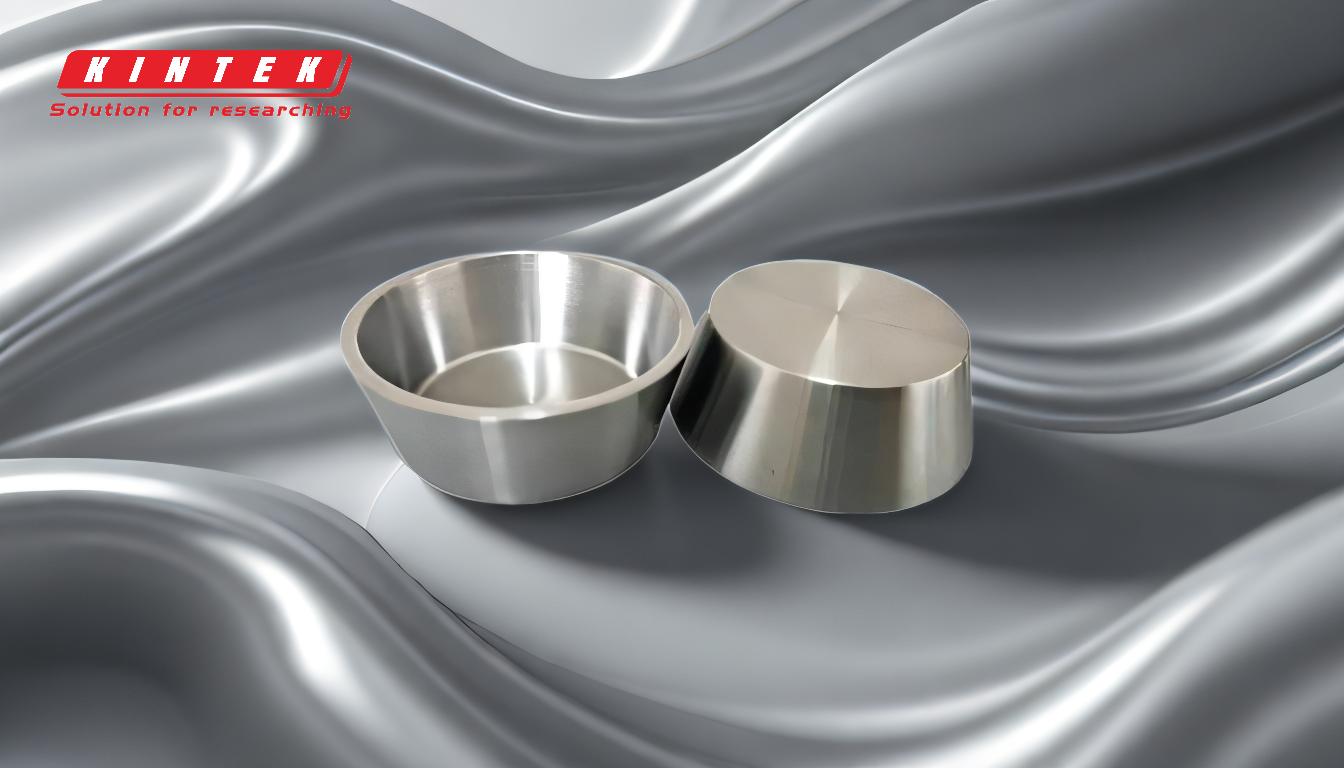
-
Heat Resistance of Crucibles:
- Crucibles are engineered to withstand extremely high temperatures, typically up to 2000 °C, with some high-purity graphite crucibles capable of enduring temperatures as high as 3000 °C.
- This heat resistance is critical for applications such as metal melting, alloy creation, and high-temperature chemical reactions.
-
Materials Used in Crucible Construction:
- Crucibles are made from materials like graphite, ceramics, and refractory metals, which are chosen for their ability to endure extreme heat and resist chemical reactions.
- Graphite crucibles, for example, are ideal for melting metals like aluminum, copper, and brass due to their high thermal conductivity and resistance to contamination.
-
Applications in Industry and Science:
- In metallurgy, crucibles are used for melting metals, creating alloys, and recycling scrap metal.
- In laboratories, they play a vital role in analytical chemistry, particularly for trace and ultra-trace level analysis of sample constituents.
-
Durability and Precision:
- Crucibles are designed to resist heat stress and chemical degradation, ensuring long-term durability and reliability.
- Their precision in maintaining structural integrity under extreme conditions makes them essential for high-temperature processes.
-
Versatility Across Fields:
- Crucibles are used across various fields, including chemistry, metallurgy, and materials science, highlighting their versatility and importance in both industrial and scientific contexts.
By understanding these key points, it is clear that crucibles are not only capable of withstanding heat but are also critical tools for ensuring precision and efficiency in high-temperature applications.
Summary Table:
Key Aspect | Details |
---|---|
Heat Resistance | Withstands temperatures up to 2000 °C (3000 °C for high-purity graphite). |
Materials | Graphite, ceramics, refractory metals. |
Applications | Metal melting, alloy creation, chemical reactions, and trace analysis. |
Durability & Precision | Resists heat stress, chemical degradation, and ensures structural integrity. |
Versatility | Used in metallurgy, chemistry, and materials science. |
Need a crucible for your high-temperature applications? Contact us today to find the perfect solution!