Soldering copper to copper without flux is theoretically possible, but it is not recommended for achieving strong, reliable, and clean joints. Flux plays a critical role in the soldering process by removing oxides from the metal surfaces, improving solder flow, and ensuring a strong bond. Without flux, the solder may not adhere properly, leading to weak joints, poor conductivity, and potential failure over time. While there are techniques to solder without flux, such as using very clean surfaces and high heat, they are less effective and more prone to issues compared to using flux. For most applications, especially in electronics or plumbing, using flux is essential for optimal results.
Key Points Explained:
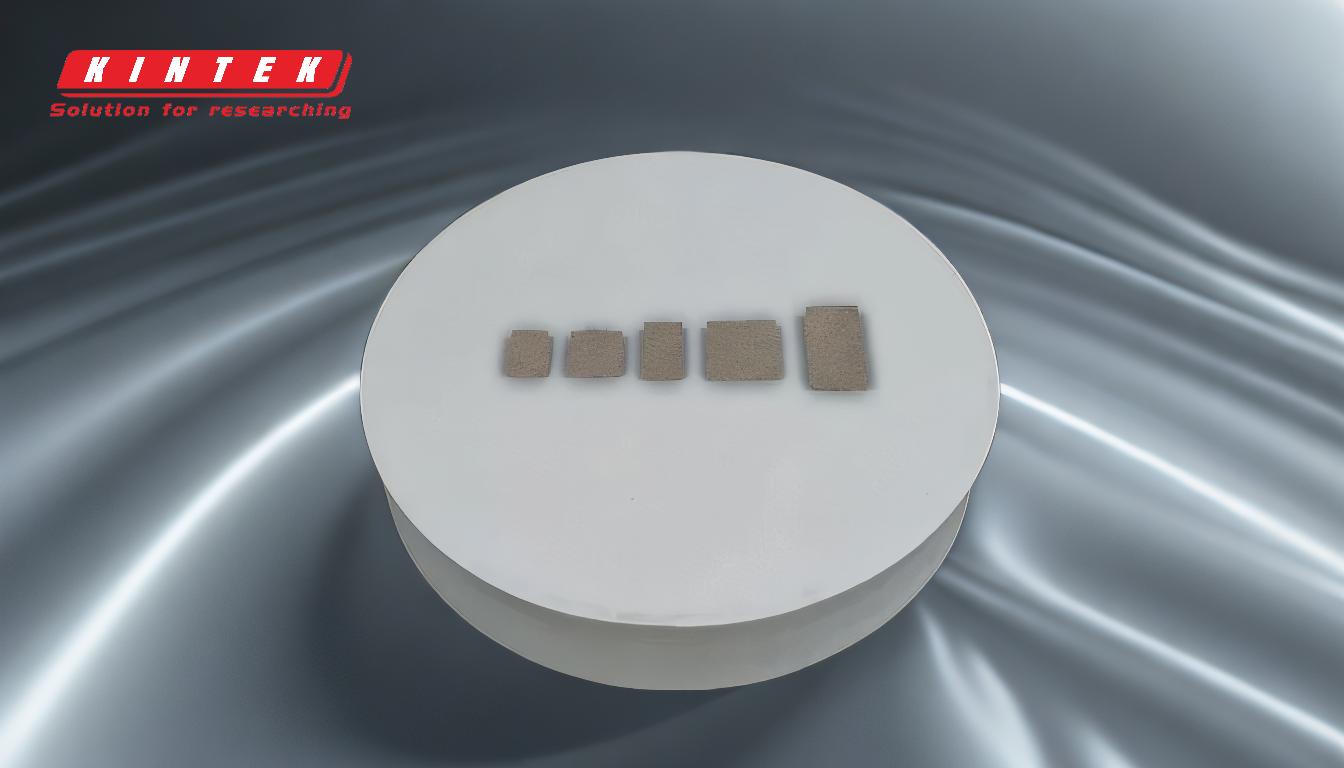
-
Role of Flux in Soldering:
- Flux is a chemical agent used in soldering to clean the metal surfaces by removing oxides and contaminants.
- It promotes wetting, which allows the solder to flow evenly and adhere to the copper surfaces.
- Without flux, oxides on the copper surface can prevent the solder from bonding properly, leading to weak or incomplete joints.
-
Challenges of Soldering Without Flux:
- Oxidation: Copper surfaces quickly form oxides when exposed to air, which act as a barrier to solder adhesion.
- Poor Wetting: Without flux, the solder may bead up or fail to spread evenly, resulting in uneven or incomplete joints.
- Increased Heat Requirement: Higher temperatures may be needed to melt the solder and overcome the lack of flux, which can damage sensitive components or surrounding materials.
-
Techniques to Solder Without Flux:
- Surface Preparation: Thoroughly clean the copper surfaces with abrasives or solvents to remove oxides and contaminants. This can improve solder adhesion but is less effective than using flux.
- High Heat: Applying higher heat can help the solder flow, but this increases the risk of damaging the materials or creating thermal stress.
- Pre-Tinning: Pre-tinning the copper surfaces with solder before joining them can improve adhesion, but this still benefits from the use of flux.
-
Why Flux is Recommended:
- Reliability: Flux ensures consistent and reliable solder joints by eliminating oxidation and promoting proper wetting.
- Ease of Use: Soldering with flux is easier and more forgiving, especially for beginners or in complex applications.
- Performance: Flux improves electrical conductivity and mechanical strength, which are critical in electronics and plumbing.
-
Types of Flux for Copper Soldering:
- Rosin Flux: Commonly used in electronics, it is non-corrosive and leaves minimal residue.
- Acid Flux: Used in plumbing, it is more aggressive and requires thorough cleaning after soldering to prevent corrosion.
- No-Clean Flux: Designed to leave minimal residue, making it suitable for applications where cleaning is difficult.
-
Applications Where Flux is Essential:
- Electronics: Flux is crucial for soldering small components and ensuring reliable electrical connections.
- Plumbing: Flux ensures leak-proof joints and strong bonds in copper pipe soldering.
- High-Stress Environments: Flux is necessary for joints that will be subjected to mechanical stress or temperature variations.
In conclusion, while it is possible to solder copper to copper without flux, the process is less effective and more prone to failure. Using flux is highly recommended for achieving strong, reliable, and clean solder joints in most applications. If flux is unavailable, meticulous surface preparation and careful heat application can improve results, but these methods are not a substitute for the benefits provided by flux.
Summary Table:
Aspect | Details |
---|---|
Role of Flux | Removes oxides, improves solder flow, and ensures strong adhesion. |
Challenges Without Flux | Oxidation, poor wetting, and higher heat requirements. |
Techniques Without Flux | Surface cleaning, high heat, and pre-tinning (less effective than flux). |
Why Use Flux? | Ensures reliability, ease of use, and better performance. |
Types of Flux | Rosin (electronics), acid (plumbing), no-clean (minimal residue). |
Applications | Electronics, plumbing, and high-stress environments. |
Need help with soldering copper? Contact our experts today for reliable solutions!