Yes, an induction furnace can melt iron. Induction furnaces are highly efficient and widely used in metal casting and foundry operations to melt various metals, including iron. The process involves generating eddy currents within the metal using an alternating magnetic field, which heats and melts the metal through Joule heating. The furnace's design ensures precise temperature control, uniform heating, and efficient melting, making it suitable for melting iron and other metals.
Key Points Explained:
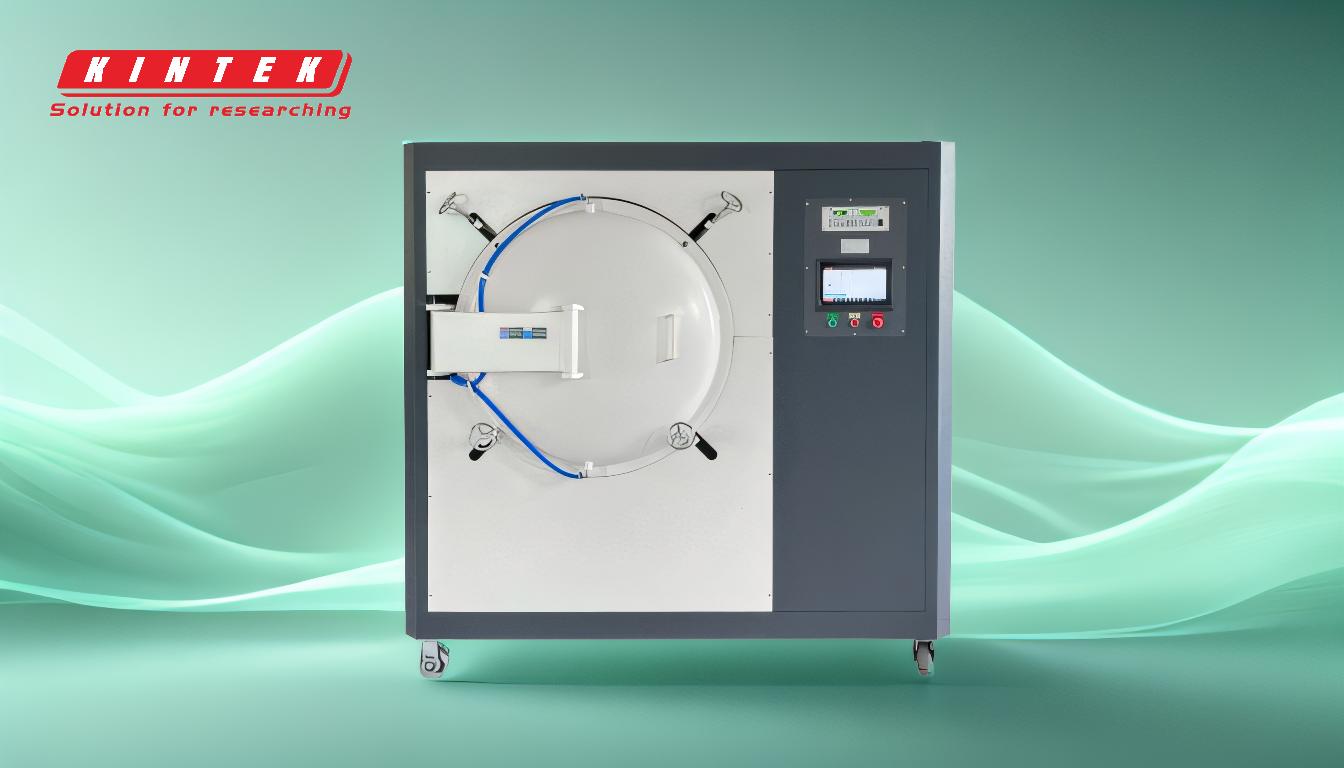
-
How Induction Furnaces Work
- Induction furnaces use electromagnetic induction to generate heat within the metal itself.
- An alternating current flows through a coil (usually made of copper), creating a rapidly reversing magnetic field.
- This magnetic field induces eddy currents in the metal charge (e.g., iron), which flow through the metal's electrical resistance, generating heat via Joule heating.
- The heat is produced directly within the metal, making the process efficient and clean.
-
Suitability for Melting Iron
- Induction furnaces are capable of reaching the high temperatures required to melt iron, which has a melting point of approximately 1538°C (2800°F).
- The process is highly controllable, allowing for precise temperature regulation, which is critical for melting iron and achieving the desired alloy composition.
- The electromagnetic stirring effect ensures uniform mixing and temperature distribution in the molten metal, reducing the risk of impurities or inconsistencies.
-
Advantages of Using Induction Furnaces for Iron Melting
- Efficiency: Heat is generated directly within the metal, minimizing energy loss.
- Clean Process: No need for external combustion or gases, reducing contamination and environmental impact.
- Precision: Tight control over temperature and alloy composition ensures high-quality output.
- Versatility: Suitable for melting various metals, including iron, steel, and alloys.
-
Applications in Foundries and Metallurgy
- Induction furnaces are commonly used in foundries for melting iron and steel, as well as for producing alloys with exact compositions.
- They are also used in scientific research and high-precision industries, such as aerospace and electronics, for processing high-grade alloys and pure metals.
-
Technical Specifications
- Induction furnaces operate at medium frequencies (150 Hz to 8000 Hz), which determine the depth of current penetration into the metal.
- Higher frequencies result in shallower penetration, making them suitable for smaller charges or precise heating.
- The furnace's power supply converts alternating current into a medium-frequency current, enabling efficient heat generation.
-
Comparison with Other Melting Methods
- Unlike traditional furnaces that rely on external heat sources (e.g., gas or coal), induction furnaces generate heat internally within the metal, reducing energy waste and contamination.
- The electromagnetic stirring effect in induction furnaces ensures better mixing and homogeneity compared to other methods.
In summary, induction furnaces are highly effective for melting iron due to their efficiency, precision, and clean operation. Their ability to generate high temperatures and ensure uniform heating makes them a preferred choice in industrial and scientific applications.
Summary Table:
Aspect | Details |
---|---|
How It Works | Uses electromagnetic induction to generate heat directly within the metal. |
Suitability for Iron | Reaches high temperatures (1538°C/2800°F) with precise control. |
Advantages | High efficiency, clean process, precise alloy composition, and versatility. |
Applications | Foundries, steel production, aerospace, electronics, and research. |
Technical Specs | Operates at 150 Hz to 8000 Hz for efficient heat generation. |
Ready to enhance your metal melting process? Contact us today to learn more about induction furnaces!