Yes, aluminum can be heated in an induction heater. Induction heating is a highly efficient method for heating conductive materials like aluminum. The process involves generating eddy currents within the aluminum, which produce heat due to the material's electrical resistance. This method is widely used in industrial applications, including melting, forging, and heat treatment of aluminum. Below, I will explain the key aspects of heating aluminum using an induction heater in detail.
Key Points Explained:
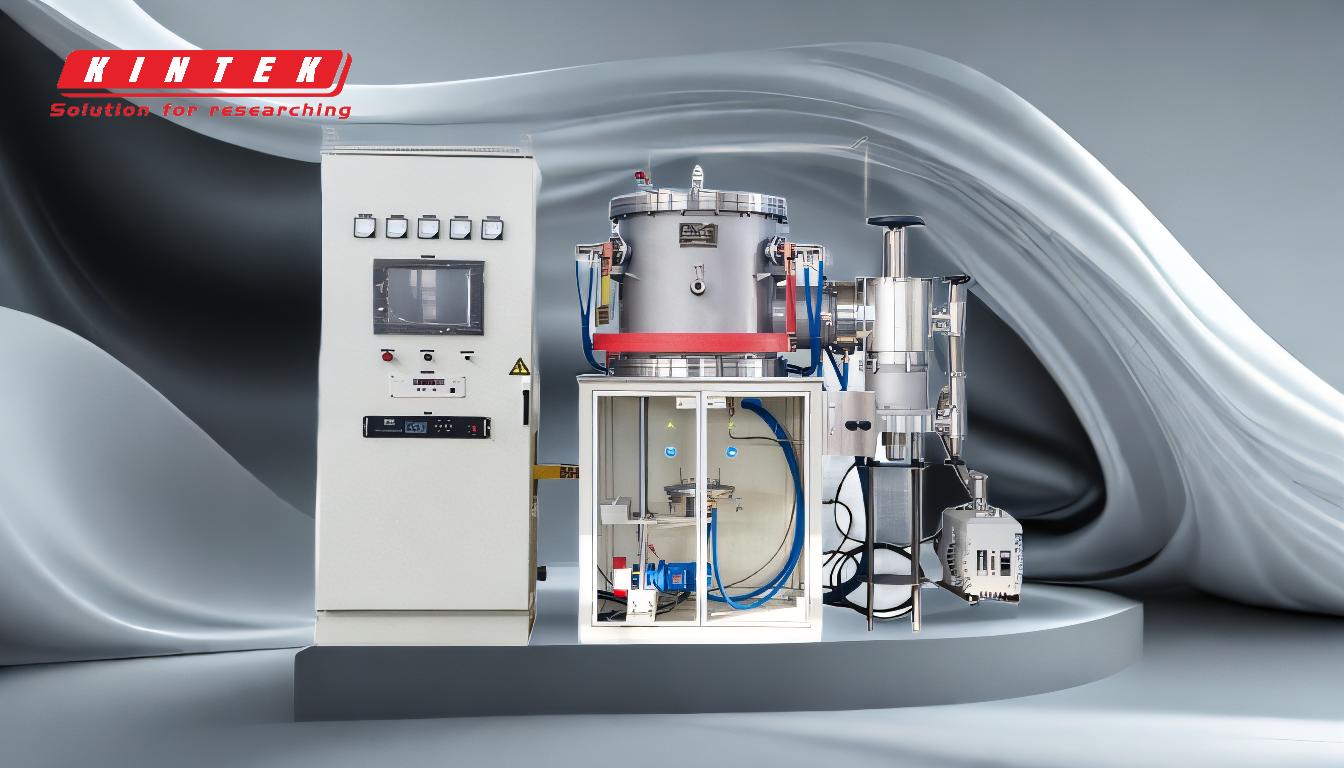
-
How Induction Heating Works for Aluminum:
- Induction heating relies on electromagnetic induction to generate heat in conductive materials.
- When an alternating current passes through a coil (inductor), it creates a rapidly alternating magnetic field.
- This magnetic field induces eddy currents within the aluminum, which generate heat due to the material's electrical resistance.
- Aluminum's high electrical conductivity makes it particularly suitable for induction heating, as it responds well to the electromagnetic field.
-
Advantages of Using Induction Heating for Aluminum:
- Efficiency: Induction heating is highly energy-efficient, as heat is generated directly within the aluminum, minimizing energy loss.
- Precision: The process allows for precise temperature control, which is critical for applications like melting, annealing, or heat treatment.
- Speed: Aluminum heats up quickly due to its low density and high thermal conductivity.
- Cleanliness: Induction heating is a non-contact process, reducing contamination from external sources.
- Automation: The process can be easily integrated into automated systems for industrial applications.
-
Industrial Applications of Induction Heating for Aluminum:
- Melting: Induction furnaces are commonly used to melt aluminum for casting or recycling. The process ensures uniform heating and efficient removal of impurities.
- Heat Treatment: Induction heating is used for processes like annealing, hardening, or tempering aluminum alloys to achieve desired mechanical properties.
- Forging: Aluminum billets can be heated quickly and uniformly before forging, reducing energy consumption and improving product quality.
- Joining: Induction heating is used in applications like brazing or soldering aluminum components.
-
Considerations When Heating Aluminum in an Induction Heater:
- Frequency Selection: The frequency of the alternating current affects the depth of heating. Higher frequencies are used for surface heating, while lower frequencies are better for deeper penetration.
- Material Properties: Aluminum's low melting point (660°C) and high thermal conductivity require careful control to avoid overheating or uneven heating.
- Coil Design: The inductor coil must be designed to match the shape and size of the aluminum workpiece for optimal heating efficiency.
- Impurity Removal: As mentioned in the reference, impurities in aluminum can rise to the surface during melting, making it easier to remove them and obtain pure aluminum.
-
Comparison with Other Heating Methods:
- Gas Furnaces: Induction heating is faster and more energy-efficient than gas furnaces, which rely on combustion and can introduce contaminants.
- Resistance Heating: While resistance heating also uses electrical energy, induction heating is more efficient and provides better control over the heating process.
- Microwave Heating: Induction heating is more suitable for industrial applications due to its scalability and ability to handle larger volumes of material.
-
Challenges and Solutions:
- Oxidation: Aluminum can oxidize when exposed to air at high temperatures. Using a protective atmosphere or vacuum can prevent oxidation.
- Thermal Expansion: Aluminum expands significantly when heated, so proper design and handling are necessary to avoid deformation or cracking.
- Energy Costs: While induction heating is efficient, the initial setup costs can be high. However, the long-term energy savings and productivity gains often justify the investment.
In summary, induction heating is a highly effective method for heating aluminum, offering numerous advantages in terms of efficiency, precision, and cleanliness. By understanding the principles of induction heating and addressing potential challenges, industries can leverage this technology for a wide range of applications involving aluminum.
Summary Table:
Aspect | Details |
---|---|
How It Works | Electromagnetic induction generates eddy currents, heating aluminum. |
Advantages | High efficiency, precise control, fast heating, cleanliness, automation. |
Applications | Melting, heat treatment, forging, joining aluminum components. |
Key Considerations | Frequency selection, material properties, coil design, impurity removal. |
Comparison with Others | More efficient than gas furnaces, better control than resistance heating. |
Challenges & Solutions | Oxidation prevention, handling thermal expansion, managing energy costs. |
Ready to optimize your aluminum heating process? Contact our experts today to learn more!