Yes, titanium can be PVD-coated. The PVD (Physical Vapor Deposition) coating process is highly versatile and can be applied to a wide range of materials, including metals like titanium. The process involves vaporizing a solid material in a vacuum and depositing it onto a substrate, forming a thin, durable, and highly adherent layer. Titanium, known for its excellent strength-to-weight ratio and corrosion resistance, can benefit significantly from PVD coatings, which enhance its surface properties such as hardness, wear resistance, and aesthetic appeal.
Key Points Explained:
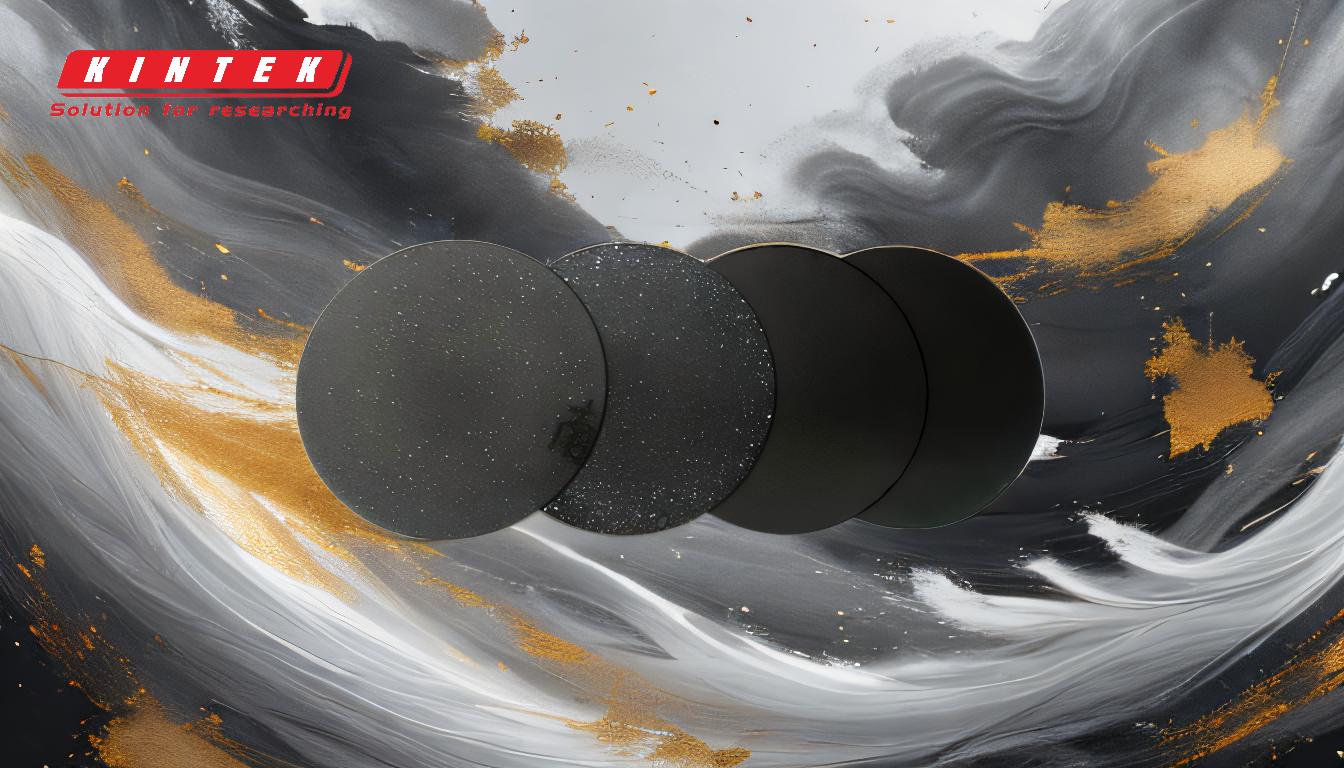
-
PVD Coating Basics:
- PVD coating is a thin-film deposition process that occurs in a vacuum chamber.
- It involves vaporizing a solid material (the target) and depositing it onto a substrate (e.g., titanium) atom by atom.
- The process is environmentally friendly and avoids the use of toxic substances.
-
Steps in the PVD Coating Process:
- Evaporation: The target material is bombarded with a high-energy source (e.g., electron beam, ion bombardment) to dislodge atoms.
- Transportation: The vaporized atoms are transported through the vacuum to the substrate.
- Reaction: Metal atoms can react with reactive gases (e.g., nitrogen, oxygen) to form compounds like nitrides or oxides.
- Deposition: The vaporized material condenses on the substrate, forming a thin, adherent layer.
-
Why Titanium is Suitable for PVD Coating:
- Titanium is a lightweight, strong, and corrosion-resistant metal, making it ideal for applications requiring durability.
- PVD coatings can further enhance titanium's properties, such as increasing its surface hardness and wear resistance.
- The coating can also improve the aesthetic appeal of titanium by adding color or a polished finish.
-
Applications of PVD-Coated Titanium:
- Medical Tools: Surgical instruments and implants benefit from PVD coatings due to their biocompatibility and enhanced durability.
- Aerospace Components: PVD-coated titanium parts are used in aircraft and spacecraft for their strength and resistance to extreme conditions.
- Consumer Goods: Items like watches, jewelry, and eyewear use PVD-coated titanium for its scratch resistance and attractive finish.
- Industrial Tools: Drill bits and cutting tools made from titanium can last longer with PVD coatings.
-
Advantages of PVD-Coated Titanium:
- Durability: The coating can extend the lifespan of titanium products by up to ten times.
- Environmental Benefits: PVD is a greener alternative to traditional coating methods like chrome plating.
- Versatility: The process allows for a wide range of coating materials and finishes, catering to specific application needs.
-
Technical Considerations:
- The PVD process requires a high-vacuum environment (10-3 to 10-9 Torr) to ensure purity and adherence of the coating.
- Inert gases like Argon are often used to create a chemically unreactive atmosphere, preventing contamination.
- The resulting coating is typically a few microns thick and bonds strongly with the titanium substrate, preventing flaking or chipping.
-
Comparison with Other Coating Methods:
- PVD coatings are thinner and more precise than traditional methods like electroplating.
- They offer better adhesion and durability, making them suitable for high-performance applications.
- Unlike some chemical coating processes, PVD does not produce hazardous waste.
In summary, PVD coating is an excellent choice for titanium, offering enhanced durability, functionality, and aesthetic appeal while being environmentally friendly. Its versatility makes it suitable for a wide range of industries, from medical to aerospace.
Summary Table:
Key Aspect | Details |
---|---|
PVD Coating Process | Thin-film deposition in a vacuum chamber, vaporizing and depositing material. |
Titanium Benefits | Lightweight, strong, corrosion-resistant; PVD enhances hardness and finish. |
Applications | Medical tools, aerospace components, consumer goods, industrial tools. |
Advantages | Durability, environmental friendliness, versatility in materials and finishes. |
Technical Considerations | High-vacuum environment, inert gases, strong adhesion, micron-thick coatings. |
Elevate your titanium products with PVD coatings—contact us today for expert solutions!