Yes, aluminum can be vacuum brazed, and it is a highly effective method for joining aluminum alloys. Vacuum brazing involves heating the aluminum components in a vacuum environment to prevent oxidation and contamination, ensuring a clean and strong joint. This process is particularly advantageous for complex assemblies and high-precision applications, as it allows for the simultaneous brazing of multiple joints with minimal distortion. The vacuum brazing furnace plays a critical role in this process by maintaining a controlled atmosphere and precise temperature, which are essential for achieving high-quality brazed joints.
Key Points Explained:
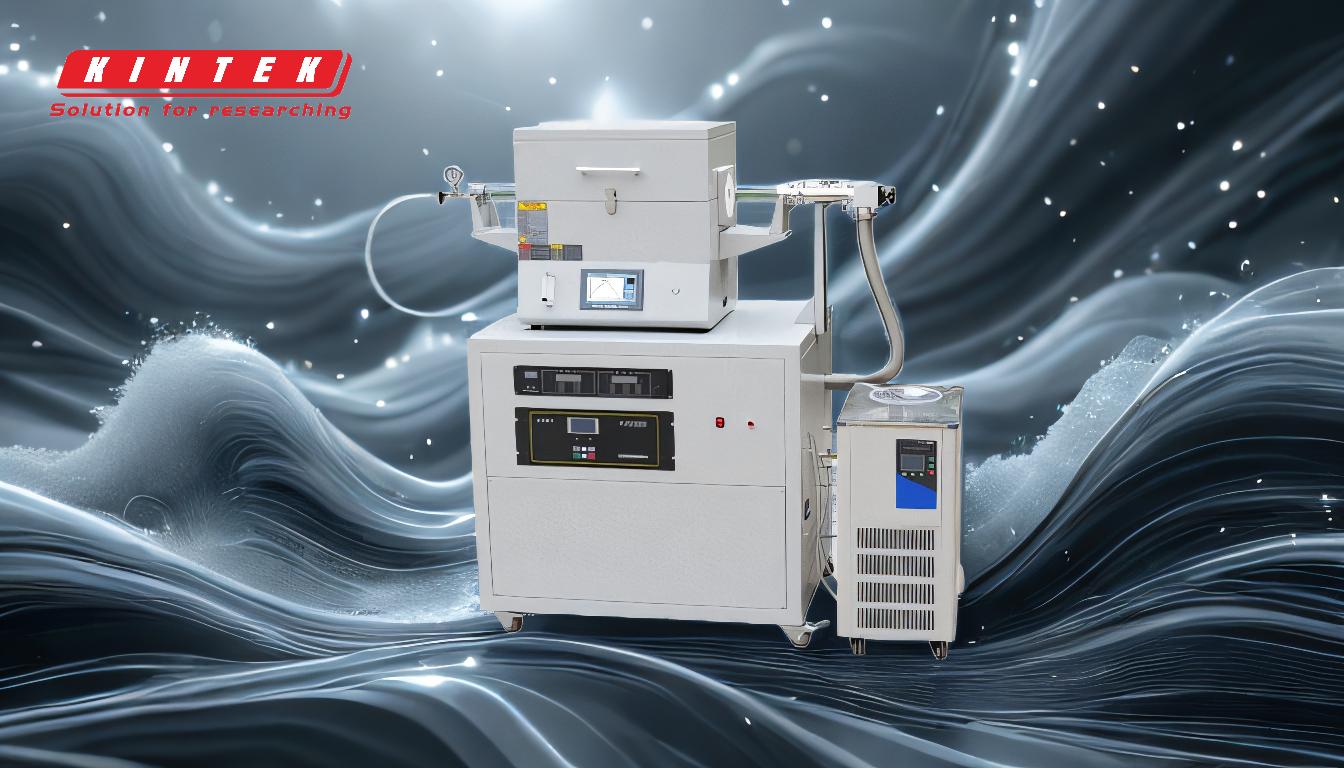
-
Vacuum Brazing of Aluminum:
- Aluminum alloys can be vacuum brazed, which is one of the most effective methods for joining aluminum components. This process is suitable for creating strong, clean, and precise joints, especially in complex assemblies.
- The vacuum environment prevents oxidation, which is crucial for aluminum, as it is highly reactive and prone to forming oxide layers that can interfere with the brazing process.
-
Role of the Vacuum Brazing Furnace:
- A vacuum brazing furnace is specifically designed to remove oxygen from the heating chamber, ensuring that the metals remain uncontaminated during the brazing process.
- The furnace consists of a vacuum system and a heating system. The vacuum system creates and maintains the required vacuum level, while the heating system heats the parts to melt the brazing material, ensuring a strong joint upon cooling.
-
Process Steps in Vacuum Brazing:
- Assembly Placement: The aluminum components, along with the brazing filler material, are assembled and placed into the vacuum chamber.
- Vacuum Creation: The mechanical vacuum pump is started to evacuate air from the chamber. Once a certain vacuum level is achieved, the diffusion pump is connected to further enhance the vacuum.
- Heating: The workpiece is heated to the brazing temperature, which melts the filler material, allowing it to flow into the joints.
- Cooling: After brazing, the workpiece is cooled in the vacuum environment to a safe temperature before removal, preventing oxidation.
-
Advantages of Vacuum Brazing for Aluminum:
- Oxidation Prevention: The vacuum environment eliminates the risk of oxidation, ensuring clean and strong joints.
- Precision and Consistency: Vacuum brazing allows for precise temperature control, resulting in consistent and high-quality joints.
- Complex Assemblies: This method is ideal for complex assemblies with multiple joints, as it ensures uniform heating and minimal distortion.
-
Comparison with Other Brazing Methods:
- Unlike flame brazing or brazing in air furnaces, vacuum brazing does not require flux, which reduces the risk of contamination and post-brazing cleaning.
- Inert gas brazing also prevents oxidation but may not achieve the same level of cleanliness and precision as vacuum brazing.
-
Applications of Vacuum Brazing:
- Vacuum brazing is widely used in industries such as aerospace, automotive, and electronics, where high-quality, reliable joints are essential.
- It is particularly suitable for brazing dissimilar metals, where the vacuum environment ensures compatibility and strength.
In summary, vacuum brazing is a highly effective method for joining aluminum alloys, offering numerous advantages such as oxidation prevention, precision, and suitability for complex assemblies. The vacuum brazing furnace is a critical component in this process, ensuring the necessary conditions for successful brazing.
Summary Table:
Key Aspect | Details |
---|---|
Process | Heating aluminum in a vacuum to prevent oxidation and ensure strong joints. |
Role of Furnace | Maintains controlled atmosphere and precise temperature for high-quality results. |
Advantages | Oxidation prevention, precision, minimal distortion, no flux required. |
Applications | Aerospace, automotive, electronics, and dissimilar metal brazing. |
Ready to achieve high-quality aluminum joints? Contact us today to learn more about vacuum brazing solutions!