Black PVD (Physical Vapor Deposition) coatings are renowned for their exceptional durability, resistance to wear, and superior quality compared to traditional finishes. While no coating is entirely immune to wear over time, black PVD coatings are among the most durable options available. Their resistance to corrosion, scratches, and abrasion ensures they maintain their appearance and functionality for extended periods, even in demanding environments. However, factors such as substrate material, application quality, and usage conditions can influence their longevity. Overall, black PVD coatings are highly resistant to wearing off, but they are not entirely indestructible.
Key Points Explained:
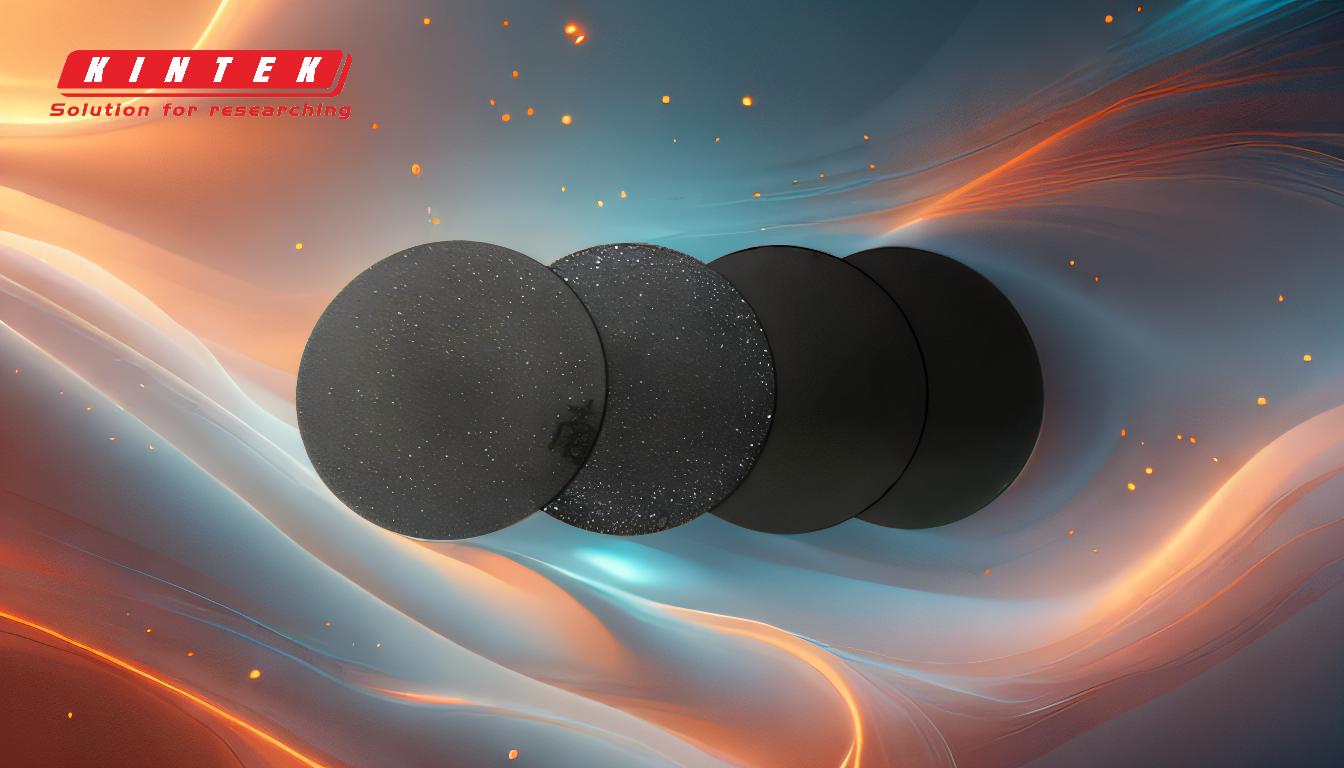
-
Durability of PVD Coatings:
- PVD coatings are considered the most durable coatings available today. They are harder and more resistant to wear, corrosion, and oxidation than traditional finishes.
- The extreme thinness of PVD coatings (0.5 to 5 microns) contributes to their durability, as they bond strongly to the substrate material.
-
Resistance to Wear:
- Black PVD coatings are highly resistant to scratches, abrasion, and corrosion, making them suitable for demanding applications.
- Their hardness and robust temperature tolerance ensure they maintain their integrity under harsh conditions.
-
Factors Influencing Longevity:
- Substrate Material: The properties of the underlying material play a significant role in the coating's durability. For example, coatings on Ti-6Al-4V alloy exhibit improved fatigue and endurance limits.
- Application Quality: Proper application ensures strong adhesion and uniform coverage, enhancing the coating's lifespan.
- Usage Conditions: Exposure to extreme environments or heavy wear can affect the coating's longevity, though PVD coatings are designed to withstand such challenges.
-
Comparison to Traditional Finishes:
- PVD coatings outlast traditional finishes due to their superior hardness and resistance to environmental factors.
- They replicate the original finish of materials with minimal effort, maintaining aesthetics over time.
-
Wear Over Time:
- While PVD coatings are highly durable, they are not entirely immune to wear. Prolonged exposure to abrasive conditions or improper handling may eventually cause the coating to wear off.
- However, the rate of wear is significantly slower compared to other coatings, ensuring long-term performance.
In summary, black PVD coatings are highly resistant to wearing off due to their exceptional durability and resistance to environmental factors. While they may experience wear over time under extreme conditions, their longevity far surpasses that of traditional finishes, making them an excellent choice for demanding applications.
Summary Table:
Key Aspect | Details |
---|---|
Durability | Harder and more resistant to wear, corrosion, and oxidation than traditional finishes. |
Resistance to Wear | Highly resistant to scratches, abrasion, and corrosion; maintains integrity in harsh conditions. |
Factors Influencing Longevity | Substrate material, application quality, and usage conditions affect durability. |
Comparison to Traditional Finishes | Outlasts traditional finishes due to superior hardness and environmental resistance. |
Wear Over Time | Slower wear rate compared to other coatings, but not entirely indestructible. |
Interested in black PVD coatings for your applications? Contact us today to learn more!