Tungsten, known for its high melting point and strength, is significantly affected by heat, which influences its mechanical properties, microstructure, and overall performance. Heat treatment, such as annealing, can alter its ductility and strength, while its body-centered cubic (BCC) lattice structure contributes to its low ductility at room temperature. Metalworking and alloying are also key factors in modifying its properties, particularly in reducing the ductile-to-brittle transition temperature and enhancing strength and ductility through deformation.
Key Points Explained:
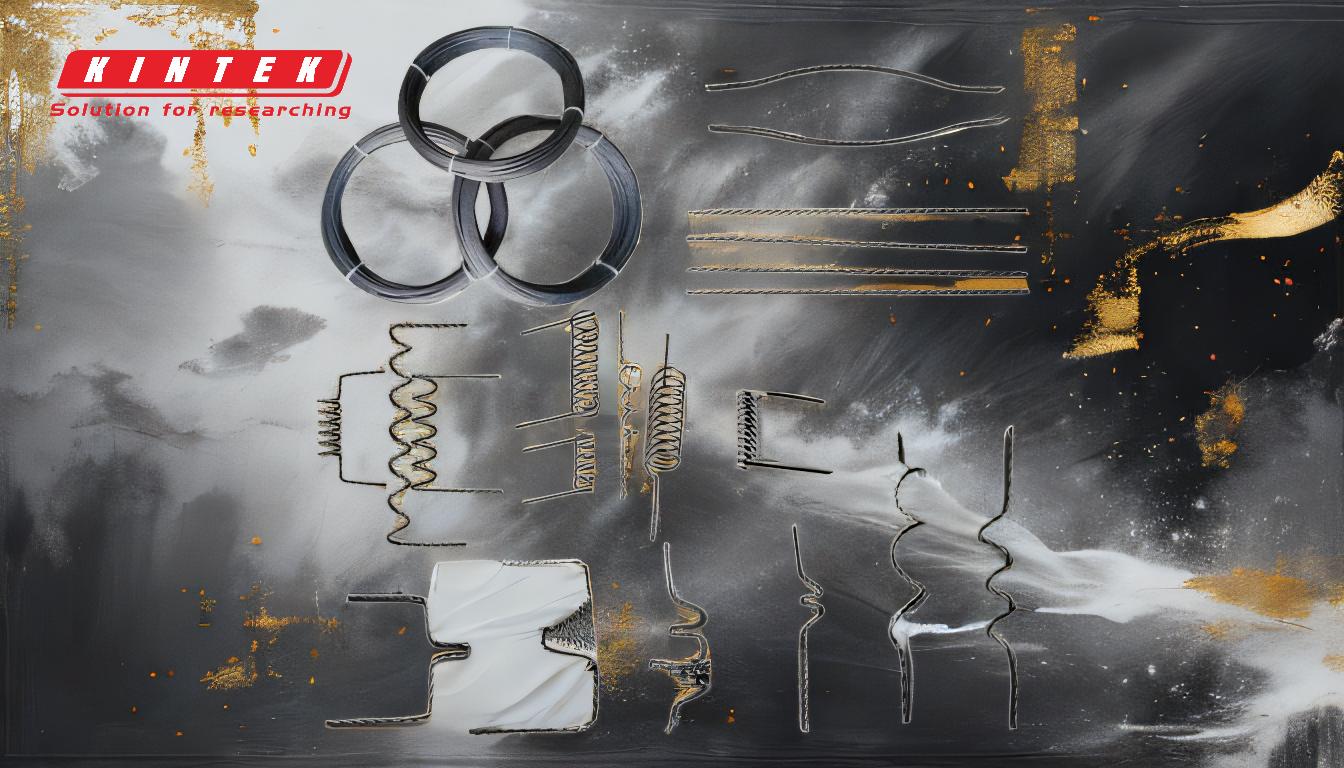
-
Effect of Heat on Tungsten's Mechanical Properties
- Heat treatment, particularly annealing, plays a critical role in altering tungsten's mechanical properties. Annealing can reduce internal stresses, improve ductility, and refine the microstructure.
- At room temperature, tungsten exhibits low ductility due to its BCC lattice structure, which makes it prone to brittleness. However, heat treatment can mitigate this by enhancing its ability to deform plastically.
-
Role of Microstructure in Heat-Affected Tungsten
- The microstructure of tungsten, including grain size and distribution, is influenced by heat. Heat treatment can lead to grain growth or refinement, depending on the temperature and duration.
- A refined microstructure generally improves mechanical properties, such as strength and toughness, by reducing the likelihood of crack propagation.
-
Impact of Alloying and Metalworking
- Alloying tungsten with other elements can improve its high-temperature performance and reduce the ductile-to-brittle transition temperature. This is particularly important in applications where tungsten is exposed to extreme heat.
- Metalworking processes, such as rolling or forging, introduce deformation that enhances strength and ductility. These processes are often combined with heat treatment to optimize the material's properties.
-
Ductile-to-Brittle Transition Temperature
- Tungsten's brittleness at room temperature is a significant limitation, but heat treatment and alloying can lower the ductile-to-brittle transition temperature. This makes it more suitable for applications requiring both strength and toughness.
- Increasing deformation through metalworking also contributes to lowering this transition temperature, improving the material's overall performance.
-
Applications and Considerations for Heat-Affected Tungsten
- Tungsten's ability to withstand high temperatures makes it ideal for applications such as aerospace components, electrical contacts, and high-temperature furnaces.
- However, careful consideration of heat treatment and alloying is necessary to ensure the material meets specific performance requirements, particularly in environments with fluctuating temperatures.
In summary, heat significantly affects tungsten by altering its mechanical properties and microstructure. Proper heat treatment, alloying, and metalworking are essential to optimize its performance, particularly in high-temperature applications. Understanding these factors is crucial for selecting and processing tungsten for specific uses.
Summary Table:
Aspect | Impact of Heat |
---|---|
Mechanical Properties | Heat treatment (e.g., annealing) improves ductility and reduces internal stresses. |
Microstructure | Heat influences grain size, refining microstructure for better strength and toughness. |
Alloying & Metalworking | Enhances high-temperature performance and lowers ductile-to-brittle transition. |
Applications | Ideal for aerospace, electrical contacts, and high-temperature environments. |
Optimize tungsten for your high-temperature applications—contact our experts today!