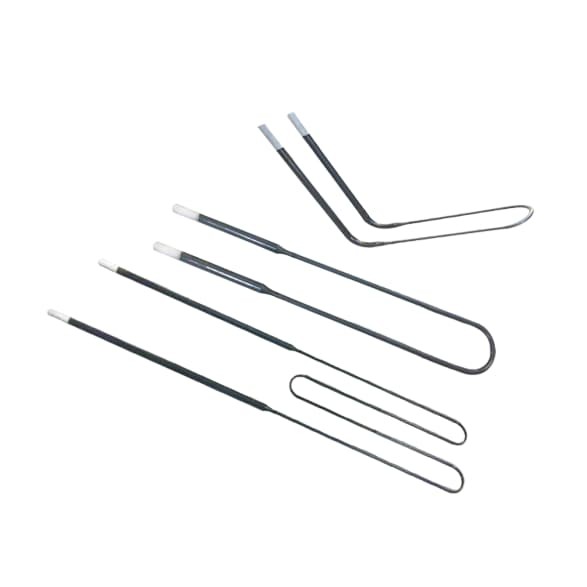
Thermal Elements
Molybdenum Disilicide (MoSi2) Thermal Elements Electric Furnace Heating Element
Item Number : KT-MH
Price varies based on specs and customizations
- hysical Properties
- 6.0±0.1 g/cm3
- Bending Strength
- 500 MPa
- Hardness
- 12 GPa
- Compression Strength
- >1500 MPa
- Water Absorption
- ≤0.2%
- Heated Elongation
- 4%
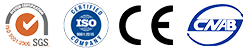
Shipping:
Contact us to get shipping details Enjoy On-time Dispatch Guarantee.
Why Choose Us
Reliable PartnerEasy ordering process, quality products, and dedicated support for your business success.
Introduction
Molybdenum disilicide (MoSi2) heating element is a high temperature resistant heating element made by molybdenum disilicide. When used in high-temperature oxidizing atmosphere, a layer of bright and dense silica (SiO2) glass film is formed on the surface, which can protect the inner layer of silicon molybdenum from oxidation. Therefore, molybdenum disilicide (MoSi2) heating element have unique high-temperature oxidation resistance.
Under the oxidation atmosphere, the maximum operating temperature is 1800 ℃. The resistance of the MoSi2 heating element increases rapidly with the increase of temperature. When the temperature is constant, the resistance value is stable.
Under normal conditions, the element resistance does not change with the length of service time, the correct selection of the surface load of the electric heating element is the key to the service life of the silicon molybdenum bar electric heating element.
Application
Molybdenum dicilicide (MoSI2) heaters are widely used in metallurgy, steel making, glass, ceramics, refractories, crystals, electronic components, semiconductor materials, research, production and manufacturing and other fields, especially for the production of high-performance precision ceramics, high-grade artificial crystals, precision structural metal ceramics, glass fibers, optical fibers and high-grade alloy steel.
- High-Temperature Furnace Operations: MoSi2 elements are crucial in the operation of high-temperature furnaces used in the production of ceramics, glass, and metals, where temperatures can reach up to 1800°C.
- Laboratory Research: In scientific research, these elements are employed in laboratory furnaces for materials testing and synthesis at high temperatures.
- Industrial Processing: They are integral in various industrial processes such as sintering, annealing, and heat treatment of materials.
- Semiconductor Manufacturing: MoSi2 heating elements are used in the fabrication of semiconductors, where precise temperature control is vital.
Detail &Parts
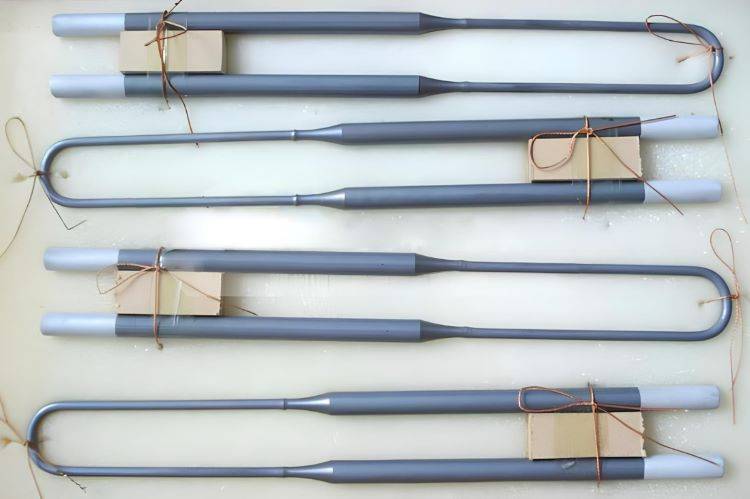
Features
- Molybdenum Disilicide (MoSi2) Heating Elements are renowned for their exceptional performance in high-temperature environments, offering a range of benefits that make them a superior choice for various industrial applications. These elements are not only capable of operating at the highest temperatures but also exhibit remarkable durability and ease of use. Here are the key features that highlight the advantages of MoSi2 Heating Elements:
- High Operating Temperatures: MoSi2 Heating Elements can withstand temperatures up to 1900°C in oxidizing atmospheres, making them ideal for processes requiring extreme heat.
- Stable Resistance: The stable resistance of MoSi2 elements allows for the connection of new and old elements in series without compromising performance. This feature is particularly beneficial for maintaining consistent heating conditions and prolonging the lifespan of the elements.
- Thermal Cycling Resilience: These elements can undergo rapid thermal cycling without degradation, which is crucial for processes that require frequent temperature changes. This resilience ensures that the elements maintain their integrity and efficiency over time.
- Ease of Replacement: MoSi2 Heating Elements are designed for easy replacement, even when the furnace is hot. This feature minimizes downtime and ensures that operations can continue smoothly without significant interruptions.
- Long Inherent Life: With the longest inherent life among electric heating elements, MoSi2 elements offer a cost-effective solution by reducing the frequency of replacements and maintenance.
- Oxidation Resistance: The formation of a protective quartz (SiO2) glass film on the surface of MoSi2 elements provides excellent oxidation resistance, safeguarding the elements from degradation in oxidizing atmospheres.
- Versatile Shapes and Sizes: Available in straight, U-shaped, W-shaped, L-shaped, or custom bent configurations, these elements can be tailored to fit a wide range of furnace designs and operational requirements.
Characteristics
Chemistry Properties
Molybdenum disilicide heating elements have unique high-temperature oxidation resistance. When used in high-temperature oxidizing atmosphere, a layer of bright and dense silica (SiO2) glass film is formed on the surface, which can protect the inner layer of molybdenum disilicide heating elements from oxidation.
Physical Properties
hysical Properties-g/cm3 | Bending Strength-MPa | Hardness -GPa | Compression Strength-MPa | Water Absorption-% | Heated Elongation-% |
6.0±0.1 | 500 | 12 | >1500 | ≤0.2% | 4 |
Working performance in different atmospheres
Atmosphere | T1700 | T1800 | T1850 | T1900 |
Air | 1700 | 1800 | 1830 | 1850 |
N2 Nitrogen | 1600 | 1700 | 1700 | 1700 |
Ar Ne Argon, Helium | 1600 | 1700 | 1700 | 1700 |
Dry Hydrogen (dew point)-80℃ | 1150 | 1150 | 1150 | 1150 |
Wet Hydrogen (dew point)-20℃ | 1450 | 1450 | 1450 | 1450 |
Exogas(e.g. 10% CO2, 50% CO, 15%H2) | 1600 | 1700 | 1700 | 1700 |
Exogas(e.g. 40% CO2, 20% CO) | 1400 | 1450 | 1450 | 1450 |
Cracked and partially burnt ammonia | 1400 | 1450 | 1450 | 1450 |
How to mark the model of molybdenum disilicide (MoSi2) heating element?
- D1: Hot zone diameter
- D2: Cold zone diameter
- Le: Hot zone length
- Lu: Cold zone length
- A: Gap distance
- Standard model number: D1/D2*Le*Lu*A
- For example: D1=6mm, D2=12,Le=200mm,Lu=300mm,A=30mm
- You can specify its model as: 6/12*200*300*30mm
D1 | D2 | Le | Lu | A |
3mm | 6mm | 80-300mm | 80-500mm | 25mm |
4mm | 9mm | 80-350mm | 80-500mm | 25mm |
6mm | 12mm | 80-800mm | 80-1000mm | 25-60mm |
7mm | 12mm | 80-800mm | 80-1000mm | 25-60mm |
9mm | 18mm | 100-1200mm | 100-2500mm | 40-80mm |
12mm | 24mm | 100-1500mm | 100-1500mm | 40-100mm |
Dos and don'ts during the installation of molybdenum disilicide (MoSi2) heating element
Please click here for precautions when installing MoSi2 heating elements
Warnings
Operator safety is the top important issue! Please operate the equipment with cautions. Working with inflammable& explosive or toxic gases is very dangerous, operators must take all necessary precautions before starting the equipment. Working with positive pressure inside the reactors or chambers is dangerous, operator must fellow the safety procedures strictly. Extra caution must also be taken when operating with air-reactive materials, especially under vacuum. A leak can draw air into the apparatus and cause a violent reaction to occur.
Designed for You
KinTek provide deep custom made service and equipment to worldwide customers, our specialized teamwork and rich experienced engineers are capable to undertake the custom tailoring hardware and software equipment requirements, and help our customer to build up the exclusive and personalized equipment and solution!
Would you please drop your ideas to us, our engineers are ready for you now!
FAQ
What Is A Thermal Element?
How Does A Thermal Element Work?
What Are The Advantages Of Using Thermal Elements?
What Are The Different Types Of Thermal Elements?
How Should Thermal Elements Be Calibrated And Maintained?
4.7
out of
5
The molybdenum disilicide heating element arrived in record time. I was so impressed with the speed of delivery.
4.8
out of
5
This product is worth every penny. It's a great value for the price, and its quality is exceptional.
4.9
out of
5
I've been using the molybdenum disilicide heating element for a few months now, and it's still going strong. It's incredibly durable and long-lasting.
4.8
out of
5
The technological advancements in this heating element are remarkable. It's a game-changer in the industry.
4.7
out of
5
The molybdenum disilicide heating element is a reliable and efficient product. It has exceeded my expectations.
4.9
out of
5
I'm thoroughly impressed with the overall performance of the molybdenum disilicide heating element. It's a top-notch product.
4.8
out of
5
The heating element's stability and consistency are commendable. It's a solid choice for various applications.
4.7
out of
5
I highly recommend the molybdenum disilicide heating element to anyone seeking a high-quality and durable product.
4.9
out of
5
The heating element's versatility and adaptability make it suitable for a wide range of applications. It's a versatile product.
4.8
out of
5
The molybdenum disilicide heating element's energy efficiency is impressive. It's a cost-effective solution for heating needs.
4.7
out of
5
The heating element's ease of installation and maintenance make it a user-friendly product. It's a breeze to set up and maintain.
4.9
out of
5
The molybdenum disilicide heating element's safety features are top-notch. It's a secure and reliable product.
4.8
out of
5
The heating element's compact design and lightweight construction make it easy to handle and store. It's a space-saving solution.
Products
Molybdenum Disilicide (MoSi2) Thermal Elements Electric Furnace Heating Element
REQUEST A QUOTE
Our professional team will reply to you within one business day. Please feel free to contact us!
Related Products
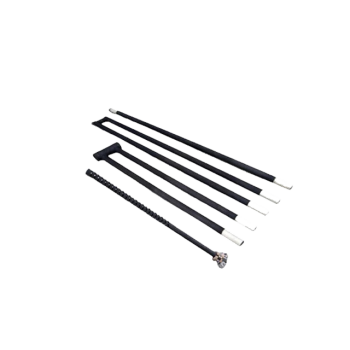
Silicon Carbide SiC Thermal Heating Elements for Electric Furnace
Experience the advantages of Silicon Carbide (SiC) Heating Element: Long service life, high corrosion and oxidation resistance, fast heating speed, and easy maintenance. Learn more now!
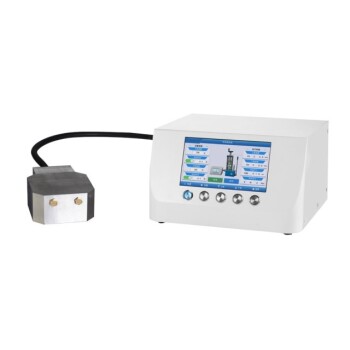
Double Plate Heating Press Mold for Lab
Discover precision in heating with our Double Plate Heating Mold, featuring high-quality steel and uniform temperature control for efficient lab processes. Ideal for various thermal applications.
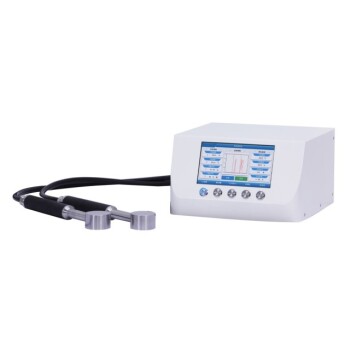
Infrared Heating Quantitative Flat Plate Press Mold
Discover advanced infrared heating solutions with high-density insulation and precise PID control for uniform thermal performance in various applications.
Electric Rotary Kiln Continuous Working Small Rotary Furnace Heating Pyrolysis Plant
Efficiently calcine and dry bulk powder and lump fluid materials with an electric heating rotary furnace. Ideal for processing lithium ion battery materials and more.
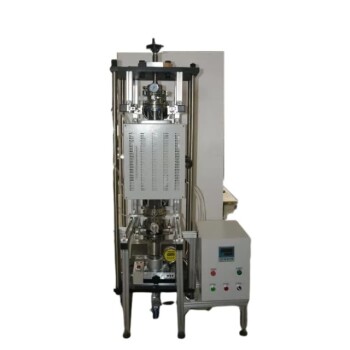
Vacuum Hot Press Furnace Heated Vacuum Press Machine Tube Furnace
Reduce forming pressure & shorten sintering time with Vacuum Tube Hot Press Furnace for high-density, fine-grain materials. Ideal for refractory metals.
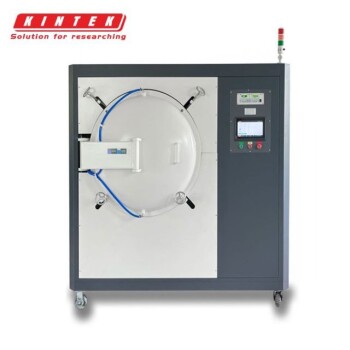
Vacuum Heat Treat Furnace with Ceramic Fiber Liner
Vacuum furnace with polycrystalline ceramic fiber insulation liner for excellent heat insulation and uniform temperature field. Choose from 1200℃ or 1700℃ max. working temperature with high vacuum performance and precise temperature control.
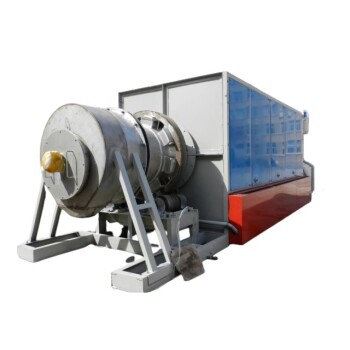
Electric Rotary Kiln Small Rotary Furnace for Activated Carbon Regeneration
Revitalize your activated carbon with KinTek's Electric Regeneration Furnace. Achieve efficient and cost-effective regeneration with our highly automated rotary kiln and intelligent thermal controller.
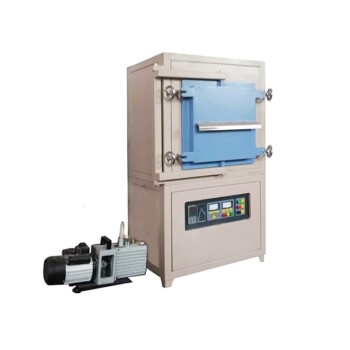
1700℃ Controlled Atmosphere Furnace Nitrogen Inert Atmosphere Furnace
KT-17A Controlled atmosphere furnace: 1700℃ heating, vacuum sealing technology, PID temperature control, and versatile TFT smart touch screen controller for laboratory and industrial use.
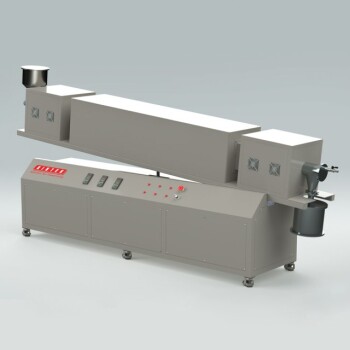
Vacuum Sealed Continuous Working Rotary Tube Furnace Rotating Tube Furnace
Experience efficient material processing with our vacuum-sealed rotary tube furnace. Perfect for experiments or industrial production, equipped with optional features for controlled feeding and optimized results. Order now.
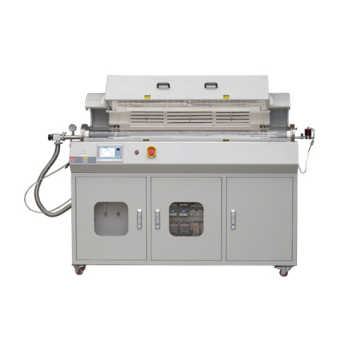
Rotary Tube Furnace Split Multi Heating Zone Rotating Tube Furnace
Multi zone rotary furnace for high-precision temperature control with 2-8 independent heating zones. Ideal for lithium ion battery electrode materials and high-temperature reactions. Can work under vacuum and controlled atmosphere.
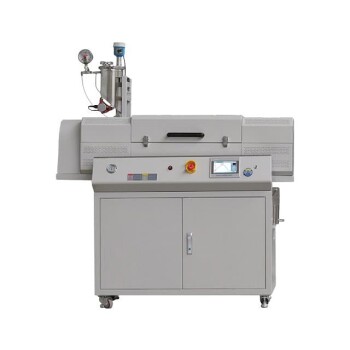
Laboratory Vacuum Tilt Rotary Tube Furnace Rotating Tube Furnace
Discover the versatility of Laboratory Rotary Furnace: Ideal for calcination, drying, sintering, and high-temperature reactions. Adjustable rotating and tilting functions for optimal heating. Suitable for vacuum and controlled atmosphere environments. Learn more now!
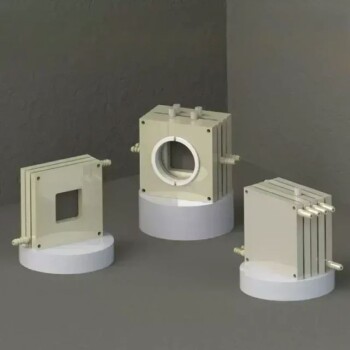
Electrolytic Electrochemical Cell Gas Diffusion Liquid Flow Reaction Cell
Looking for a high-quality gas diffusion electrolysis cell? Our liquid flow reaction cell boasts exceptional corrosion resistance and complete specifications, with customizable options available to suit your needs. Contact us today!
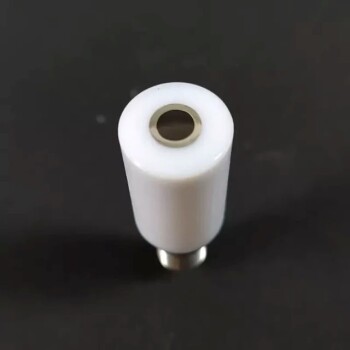
Rotating Disk Electrode and Rotating Ring Disk Electrode (RRDE)
Elevate your electrochemical research with our Rotating Disk and Ring Electrodes. Corrosion resistant and customizable to your specific needs, with complete specifications.
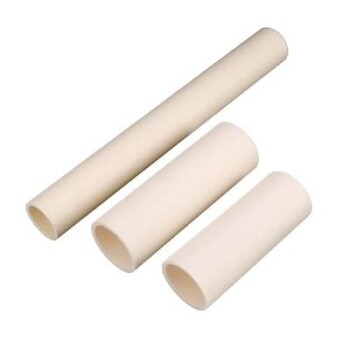
High Temperature Alumina (Al2O3) Furnace Tube for Engineering Advanced Fine Ceramics
High temperature alumina furnace tube combines the advantages of high hardness of alumina, good chemical inertness and steel, and has excellent wear resistance, thermal shock resistance and mechanical shock resistance.
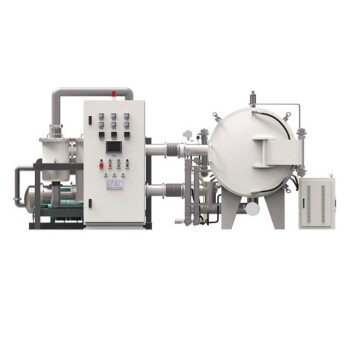
Horizontal High Temperature Graphite Vacuum Graphitization Furnace
Horizontal Graphitization Furnace: This type of furnace is designed with the heating elements placed horizontally, allowing for uniform heating of the sample. It's well-suited for graphitizing large or bulky samples that require precise temperature control and uniformity.
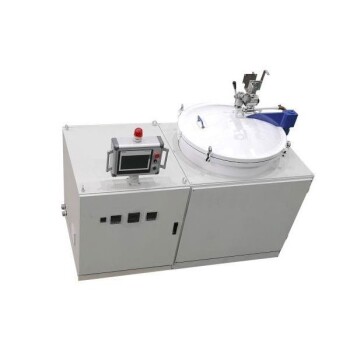
Graphite Vacuum Furnace IGBT Experimental Graphitization Furnace
IGBT experimental graphitization furnace, a tailored solution for universities and research institutions, with high heating efficiency, user-friendliness, and precise temperature control.
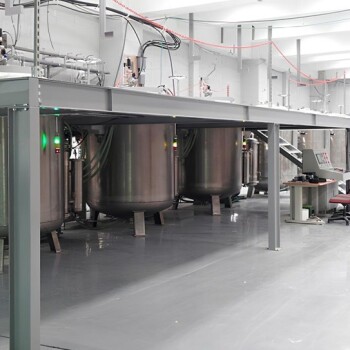
Graphite Vacuum Furnace Negative Material Graphitization Furnace
Graphitization furnace for battery production has uniform temperature and low energy consumption. Graphitization furnace for negative electrode materials: an efficient graphitization solution for battery production and advanced functions to enhance battery performance.

Graphite Vacuum Furnace Bottom Discharge Graphitization Furnace for Carbon Materials
Bottom-out graphitization furnace for carbon materials, ultra-high temperature furnace up to 3100°C, suitable for graphitization and sintering of carbon rods and carbon blocks. Vertical design, bottom discharging, convenient feeding and discharging, high temperature uniformity, low energy consumption, good stability, hydraulic lifting system, convenient loading and unloading.
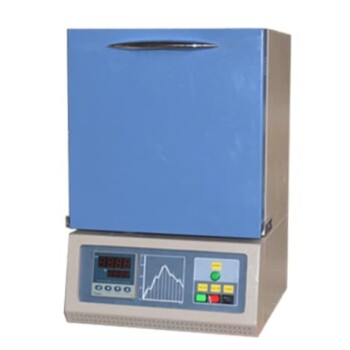
1200℃ Muffle Furnace Oven for Laboratory
Upgrade your lab with our 1200℃ Muffle Furnace. Achieve fast, precise heating with Japan alumina fibers and Molybdenum coils. Features TFT touch screen controller for easy programming and data analysis. Order now!
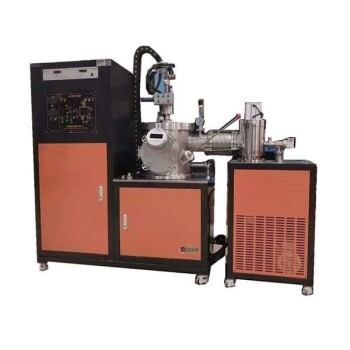
Vacuum Arc Induction Melting Furnace
Discover the power of Vacuum Arc Furnace for melting active & refractory metals. High-speed, remarkable degassing effect, and free of contamination. Learn more now!
Related Articles
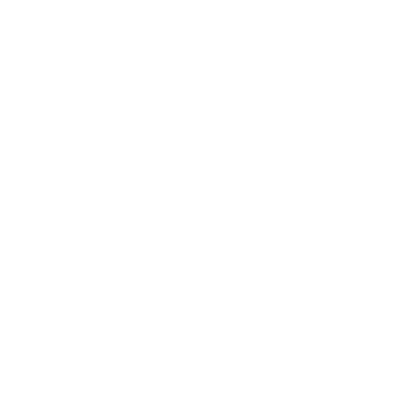
Dos and don'ts during the installation of molybdenum disilicide (MoSi2) heating element
Precautions when installing MoSi2 heating elements
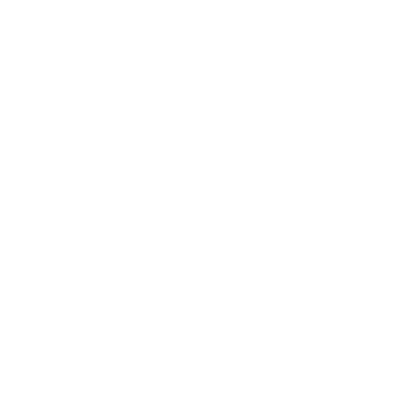
Precautions for installing silicon carbide stick
Precautions for installing silicon carbide stic.
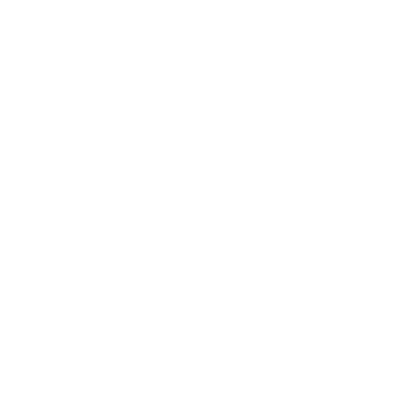
Molybdenum Vacuum Furnace: High-Temperature Sintering and Heat Treatment
Explore the advanced features and applications of molybdenum vacuum furnaces in high-temperature sintering and heat treatment. Learn about their construction, control systems, and maintenance tips.
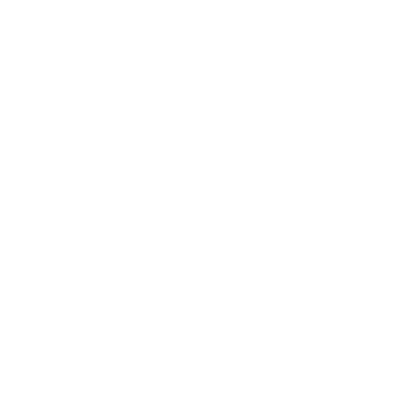
Electric Heating Systems(3): Understanding, Benefits, and Applications
Explore the world of electric heating systems, including electric furnaces, heating elements, and their benefits. Learn about the advantages, disadvantages, and applications of electric heating technology. Discover how electric heating systems work and their role in modern heating solutions.
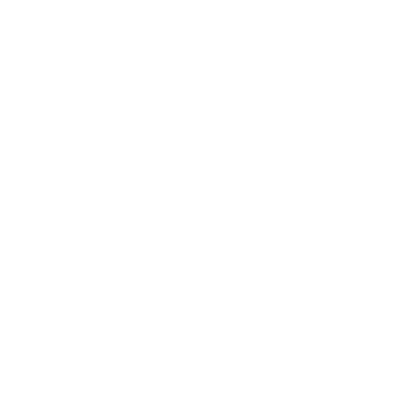
Comprehensive Guide to Muffle Furnace Resistance Wire Design
Detailed analysis of resistance wire design principles, parameters, and calculation techniques for muffle furnace applications.
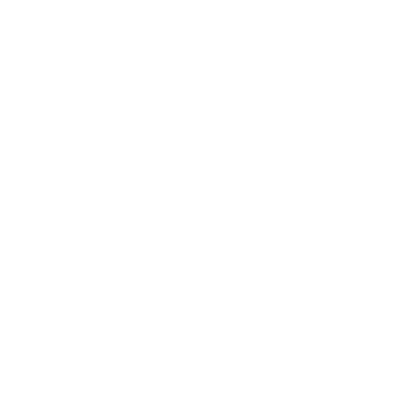
Precision Ceramic Materials for Energy Conversion Applications
Overview of various ceramic materials used in energy conversion technologies, including heaters, piezoelectric ceramics, and solid oxide fuel cells.
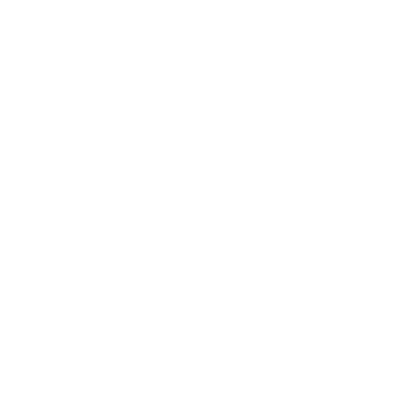
Selecting Heating Elements for Vacuum Furnaces
Guide on choosing heating elements and insulation screens for efficient vacuum furnace operation.
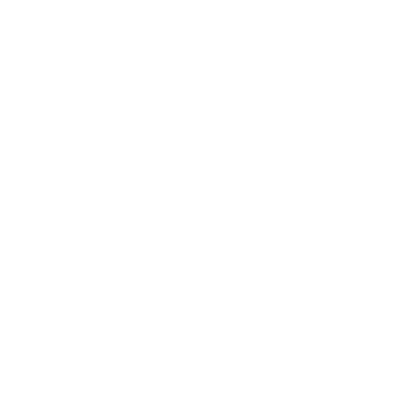
Advantages of Mullite Fiber Lining for High-Temperature Furnaces
Explores the benefits of mullite fiber linings in high-temperature industrial furnaces, focusing on thermal stability, energy efficiency, and long-term cost savings.