PVD (Physical Vapor Deposition) coatings are known for their exceptional durability and longevity, but they are not indestructible. While PVD coatings are highly resistant to wear, corrosion, and scratches, they can gradually wear down over time due to factors such as friction, impacts, and regular contact with hard surfaces. The lifespan of a PVD coating varies significantly depending on the application, substrate, coating thickness, and maintenance. In jewelry, for example, PVD coatings can last up to 10 years or more with proper care, outperforming traditional electroplated finishes. However, in extreme conditions or with improper maintenance, the coating may degrade faster. Overall, PVD coatings are among the most durable finishes available, but they are not permanent and will eventually show signs of wear.
Key Points Explained:
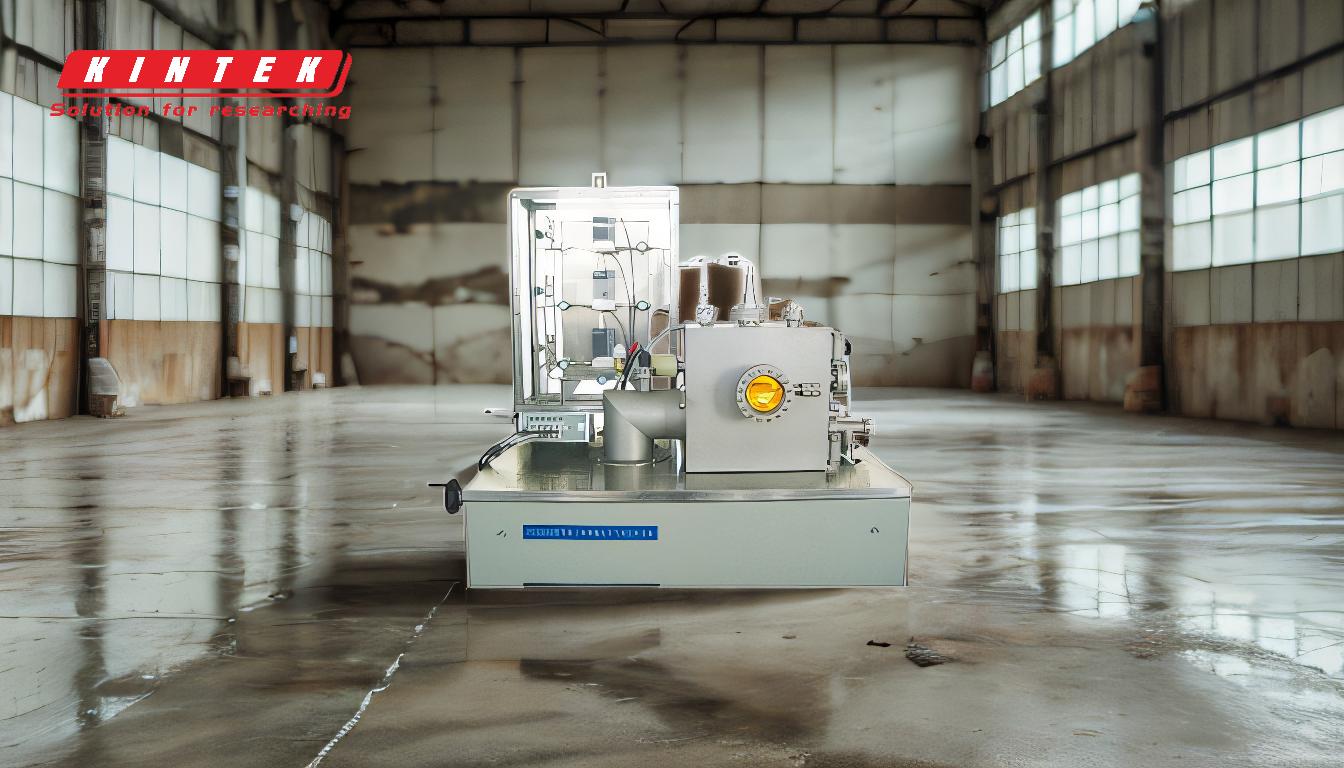
-
Durability of PVD Coatings:
- PVD coatings are highly durable, offering excellent resistance to abrasion, corrosion, and scratches.
- They are considered superior to traditional finishes like electroplating, making them suitable for demanding applications.
- The durability of PVD coatings is attributed to their robust temperature tolerance, impact strength, and high-quality finish.
-
Lifespan of PVD Coatings:
- The lifespan of a PVD coating can range from 10 years to hundreds of years, depending on factors such as:
- Substrate: The material being coated (e.g., metals, plastics).
- Coating Thickness: Thicker coatings generally last longer.
- Application Conditions: The environment in which the coated item is used (e.g., exposure to harsh chemicals, extreme temperatures, or mechanical stress).
- In jewelry, PVD coatings can last up to 10 years with proper maintenance, compared to electroplated jewelry, which typically lasts about 1 year.
- The lifespan of a PVD coating can range from 10 years to hundreds of years, depending on factors such as:
-
Factors Affecting Wear and Tear:
- Friction and Impact: Regular contact with hard surfaces, friction, and impacts can gradually wear down the coating.
- Maintenance: Proper care and maintenance can significantly extend the lifespan of PVD coatings.
- Environmental Conditions: Exposure to harsh environments, such as high humidity or corrosive substances, can accelerate wear.
-
Comparison with Other Coatings:
- PVD coatings are more durable than traditional electroplated finishes. For example:
- PVD-coated jewelry can last 3 years or more with everyday wear, while electroplated jewelry typically lasts about 1 year.
- PVD coatings are more resistant to corrosion and scratches, making them ideal for high-wear applications.
- PVD coatings are more durable than traditional electroplated finishes. For example:
-
Maintenance and Care:
- To maximize the lifespan of PVD coatings, it is important to:
- Avoid exposing the coated item to harsh chemicals or abrasive materials.
- Clean the item regularly with mild soap and water.
- Store the item properly to prevent unnecessary friction or impact.
- To maximize the lifespan of PVD coatings, it is important to:
-
Limitations of PVD Coatings:
- While PVD coatings are highly durable, they are not permanent and will eventually show signs of wear over time.
- The rate of wear depends on the application and environmental conditions. For example, a PVD-coated tool used in heavy industrial applications may wear faster than a PVD-coated piece of jewelry.
In conclusion, PVD coatings are among the most durable and long-lasting finishes available, but they are not immune to wear and tear. With proper care and maintenance, PVD coatings can last for many years, even decades, depending on the application and conditions. However, in high-wear or harsh environments, the coating may degrade faster, highlighting the importance of selecting the right coating for the intended use.
Summary Table:
Aspect | Details |
---|---|
Durability | Highly resistant to wear, corrosion, and scratches. Superior to electroplating. |
Lifespan | 10+ years in jewelry; varies with substrate, thickness, and conditions. |
Factors Affecting Wear | Friction, impact, maintenance, and environmental exposure. |
Maintenance Tips | Avoid harsh chemicals, clean with mild soap, and store properly. |
Limitations | Not permanent; wear depends on application and conditions. |
Want to learn more about PVD coatings or need expert advice? Contact us today!