Ion beam-based deposition techniques and sputtering are both physical vapor deposition (PVD) methods used to create thin films, but they differ significantly in their mechanisms, applications, and advantages. Ion beam deposition (IBD) separates the ion source from the target material, allowing for precise control over the deposition process and enabling the use of both conductive and non-conductive materials. It avoids plasma formation between the substrate and target, reducing contamination and making it suitable for sensitive substrates. In contrast, sputtering, particularly magnetron sputtering, relies on plasma to bombard the target material, freeing atoms that deposit onto the substrate. While sputtering is highly automated and ideal for high-volume production, ion beam deposition offers superior film quality and uniformity, albeit at a higher cost and complexity. The choice between these techniques depends on the specific requirements of the application, such as substrate sensitivity, material compatibility, and desired film properties.
Key Points Explained:
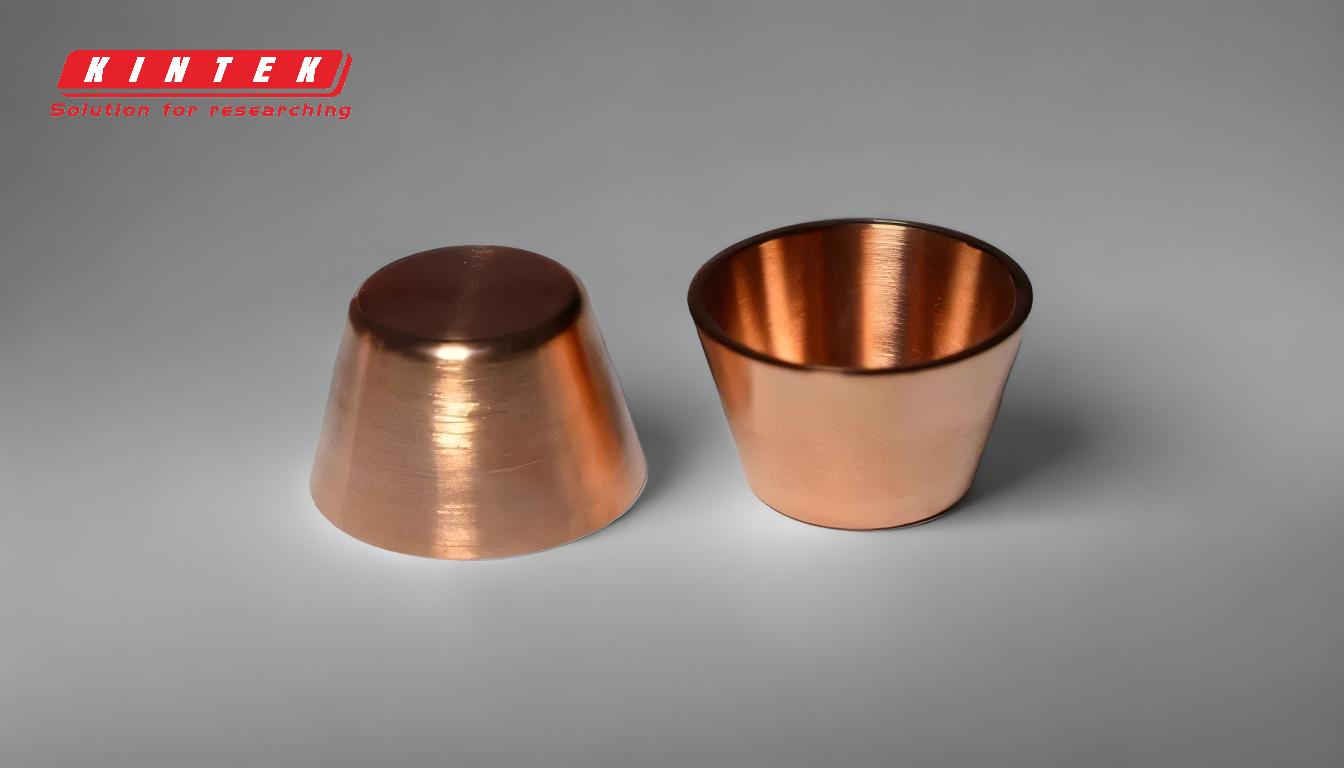
-
Mechanism of Deposition:
- Ion Beam Deposition (IBD): In IBD, an ion beam is generated separately from the target material. The ions are directed toward the target, sputtering atoms that then deposit onto the substrate. This separation allows for precise control over the ion energy and direction, reducing contamination and improving film quality.
- Sputtering (Magnetron Sputtering): In sputtering, a plasma is created between the target and the substrate. The plasma bombards the target material, freeing atoms that deposit onto the substrate. This process is less controlled compared to IBD, as the plasma can introduce impurities and affect sensitive substrates.
-
Plasma Presence:
- Ion Beam Deposition: There is no plasma between the substrate and the target in IBD. This absence of plasma reduces the risk of sputter gas inclusion in the deposit and minimizes damage to sensitive substrates.
- Sputtering: Sputtering relies on plasma to free atoms from the target material. The presence of plasma can lead to contamination and may not be suitable for substrates that are sensitive to plasma exposure.
-
Material Compatibility:
- Ion Beam Deposition: IBD can be used with both conducting and non-conducting targets and substrates. The separation of the ion source from the target material allows for the deposition of insulating materials, which is not possible in traditional sputtering.
- Sputtering: While sputtering is versatile, it typically requires conductive targets. Non-conductive materials can be sputtered using RF sputtering, but this adds complexity to the process.
-
Film Quality and Uniformity:
- Ion Beam Deposition: IBD produces films with better quality and uniformity. The precise control over ion energy and direction results in films with fewer defects and higher consistency, which is critical for applications requiring high precision.
- Sputtering: While sputtering can produce high-quality films, the presence of plasma and less control over the deposition process can lead to variations in film quality and uniformity.
-
Cost and Complexity:
- Ion Beam Deposition: IBD is more costly and complex due to the need for a separate ion source and precise control mechanisms. This makes it less suitable for high-volume production but ideal for applications requiring high precision and quality.
- Sputtering: Sputtering is more cost-effective and simpler, making it suitable for highly automated, high-volume production. It is particularly advantageous for applications requiring rapid deposition times.
-
Applications:
- Ion Beam Deposition: IBD is ideal for applications requiring high-quality films, such as optical coatings, sensitive electronic components, and research applications where film uniformity and purity are critical.
- Sputtering: Sputtering is widely used in industries requiring large-scale production, such as semiconductor manufacturing, decorative coatings, and thin-film solar cells. It is also suitable for experimenting with exotic materials and novel coatings.
In summary, the choice between ion beam-based deposition and sputtering depends on the specific requirements of the application, including the need for film quality, substrate sensitivity, material compatibility, and production scale. Ion beam deposition offers superior control and film quality but at a higher cost and complexity, while sputtering provides a more cost-effective and scalable solution for high-volume production.
Summary Table:
Feature | Ion Beam Deposition (IBD) | Sputtering (Magnetron Sputtering) |
---|---|---|
Mechanism | Separate ion source, precise control | Plasma bombards target, less controlled |
Plasma Presence | No plasma between substrate and target | Plasma present, may cause contamination |
Material Compatibility | Conducting and non-conducting materials | Primarily conductive materials |
Film Quality | Superior quality and uniformity | High quality, but less uniform |
Cost & Complexity | Higher cost, more complex | Cost-effective, simpler |
Applications | Optical coatings, sensitive electronics | Semiconductor, decorative coatings |
Need help choosing the right PVD method for your project? Contact our experts today!