Thin film nanoparticles are prepared using a variety of deposition techniques that allow precise control over the thickness, composition, and properties of the films. These methods can be broadly categorized into physical, chemical, and electrically-based processes. Common techniques include physical vapor deposition (PVD), chemical vapor deposition (CVD), sputtering, evaporation, spin coating, and layer-by-layer assembly. Each method has its own advantages and is chosen based on the desired properties of the thin film and the application it is intended for. Post-deposition processes like annealing or heat treatment may also be used to enhance the film's properties.
Key Points Explained:
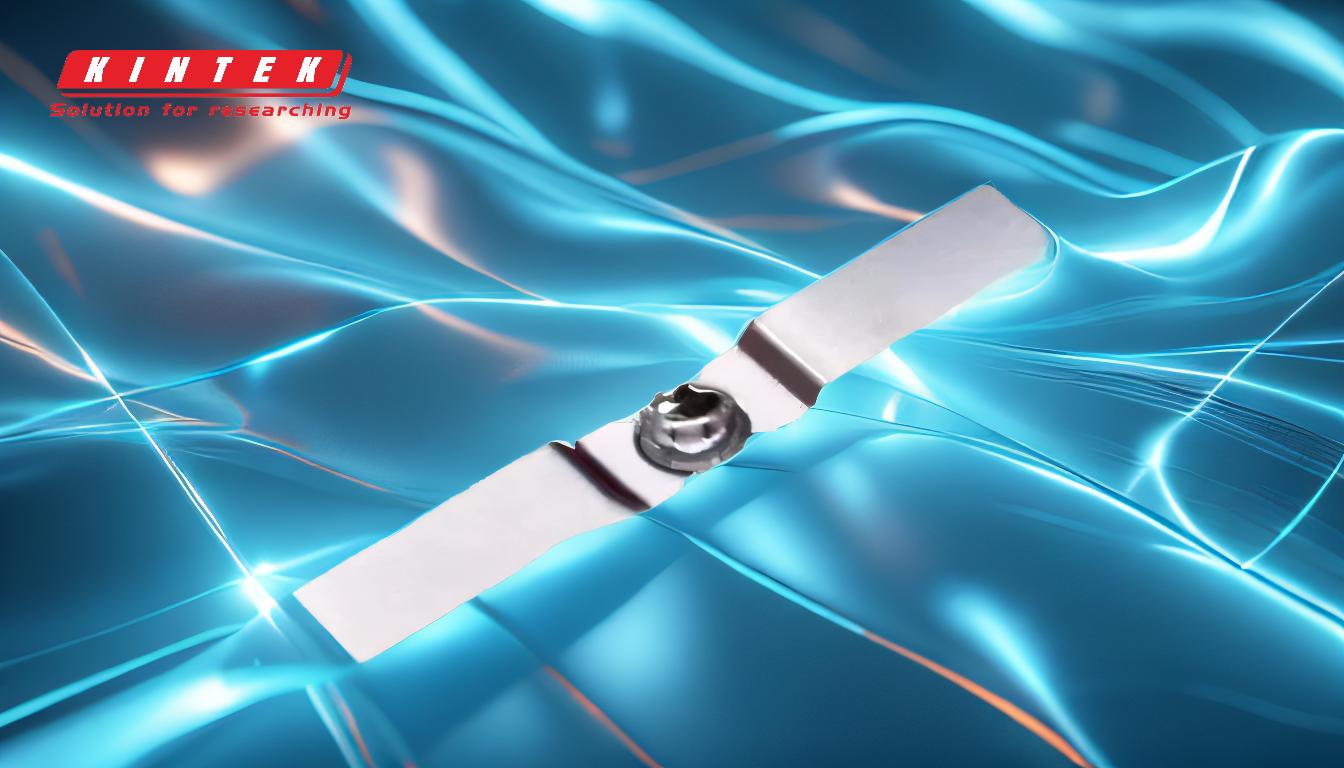
-
Selection of Material (Target)
- The first step in preparing thin film nanoparticles is selecting the appropriate material to be deposited. This material, known as the target, can be a metal, semiconductor, polymer, or other compounds depending on the desired properties of the thin film.
- The choice of material is critical as it determines the electrical, optical, and mechanical properties of the final thin film.
-
Transport of Target to Substrate
- Once the target material is selected, it needs to be transported to the substrate where the thin film will be formed. This can be achieved through various methods such as evaporation, sputtering, or chemical reactions.
- In physical vapor deposition (PVD), the target material is vaporized in a vacuum and then condensed onto the substrate.
- In chemical vapor deposition (CVD), the target material is transported in the form of a gas and then chemically reacts on the substrate to form the thin film.
-
Deposition Techniques
- Physical Vapor Deposition (PVD): This includes methods like evaporation and sputtering. In evaporation, the target material is heated until it vaporizes and then condenses on the substrate. In sputtering, high-energy particles bombard the target, causing atoms to be ejected and deposited onto the substrate.
- Chemical Vapor Deposition (CVD): This involves the use of chemical reactions to deposit the thin film. A precursor gas is introduced into a reaction chamber, where it decomposes or reacts with other gases to form the thin film on the substrate.
- Spin Coating: This technique involves applying a liquid solution of the target material onto a substrate, which is then spun at high speeds to spread the solution evenly and form a thin film.
- Layer-by-Layer (LbL) Assembly: This method involves alternately depositing layers of different materials to build up a thin film with precise control over its composition and thickness.
-
Post-Deposition Processes
- After the thin film is deposited, it may undergo additional processes to enhance its properties. These include:
- Annealing: Heating the thin film to a high temperature to improve its crystallinity and reduce defects.
- Heat Treatment: Similar to annealing, but may involve specific temperature profiles to achieve desired mechanical or electrical properties.
- After the thin film is deposited, it may undergo additional processes to enhance its properties. These include:
-
Applications and Considerations
- The choice of deposition method and post-deposition processes depends on the intended application of the thin film. For example:
- Semiconductors: PVD and CVD are commonly used due to their ability to produce high-purity films with precise control over thickness.
- Flexible Electronics: Spin coating and LbL assembly are preferred for their ability to deposit thin films on flexible substrates.
- Optical Coatings: Sputtering and evaporation are often used to create thin films with specific optical properties.
- The choice of deposition method and post-deposition processes depends on the intended application of the thin film. For example:
-
Advantages and Drawbacks
- PVD: Offers high purity and good adhesion but may require complex equipment and high vacuum conditions.
- CVD: Allows for uniform coatings and can deposit complex materials, but may involve hazardous chemicals and high temperatures.
- Spin Coating: Simple and cost-effective for small-scale production, but may not be suitable for large or complex substrates.
- LbL Assembly: Provides excellent control over film composition and thickness, but can be time-consuming and may require specialized equipment.
In summary, the preparation of thin film nanoparticles involves a series of carefully controlled steps, from material selection to deposition and post-deposition processing. The choice of technique depends on the desired properties of the thin film and its intended application, with each method offering its own set of advantages and challenges.
Summary Table:
Deposition Technique | Key Features | Applications |
---|---|---|
Physical Vapor Deposition (PVD) | High purity, good adhesion | Semiconductors, optical coatings |
Chemical Vapor Deposition (CVD) | Uniform coatings, complex materials | Semiconductors, electronics |
Spin Coating | Simple, cost-effective | Flexible electronics |
Layer-by-Layer (LbL) Assembly | Precise composition control | Flexible electronics, sensors |
Post-Deposition Processes | Purpose | |
Annealing | Improves crystallinity, reduces defects | |
Heat Treatment | Enhances mechanical/electrical properties |
Need help choosing the right deposition technique for your project? Contact our experts today!