Physical Vapor Deposition (PVD) and Chemical Vapor Deposition (CVD) are two widely used techniques for applying thin-film coatings to substrates. While both methods aim to enhance surface properties, they differ significantly in their mechanisms, operating conditions, and resulting coating characteristics. PVD involves the physical transfer of material from a solid source to the substrate, typically under vacuum conditions, while CVD relies on chemical reactions between gaseous precursors and the substrate to form a coating. These differences influence factors such as coating thickness, uniformity, temperature requirements, and material compatibility.
Key Points Explained:
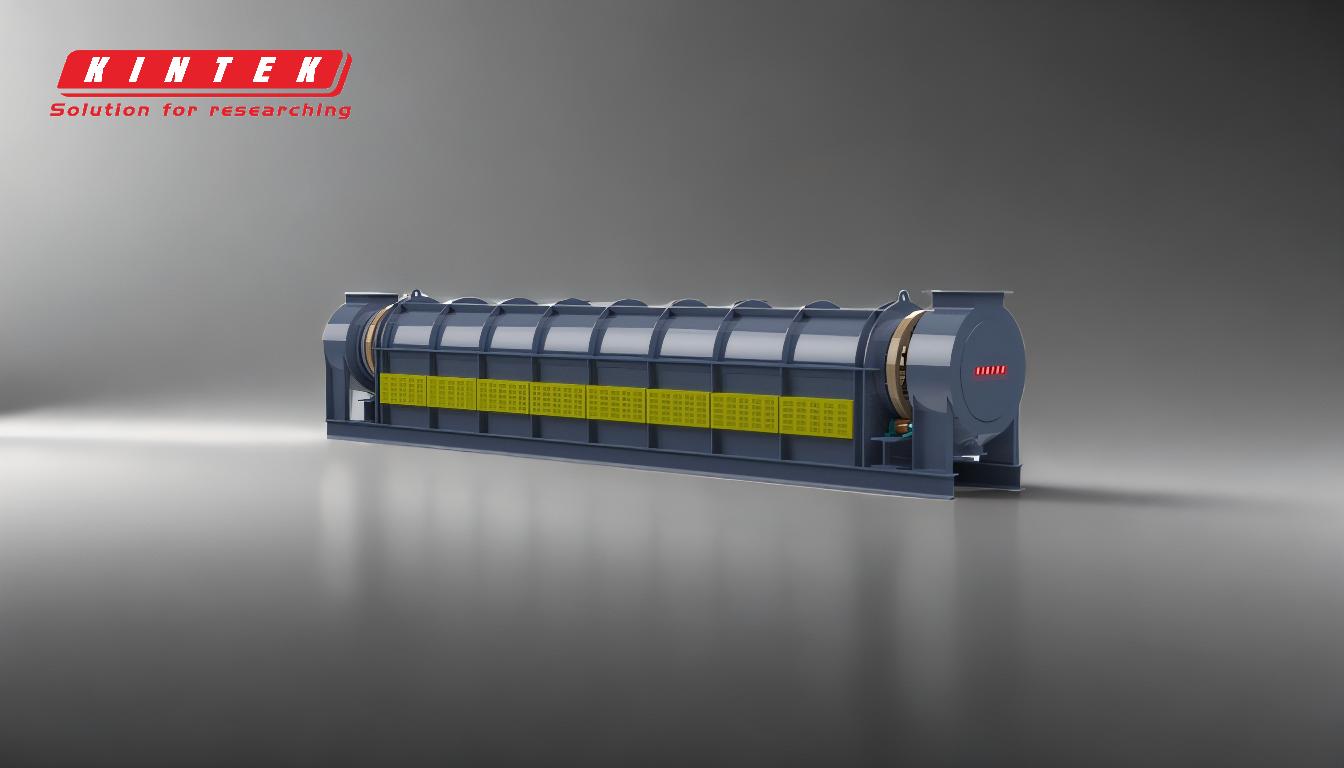
-
Deposition Mechanism:
- PVD: PVD is a line-of-sight process where material is physically vaporized from a solid target and deposited onto the substrate. This process does not involve chemical reactions between the target material and the substrate. Instead, atoms or molecules are ejected from the target and condense on the substrate surface.
- CVD: CVD involves chemical reactions between gaseous precursors and the substrate. The gases react at the substrate surface, forming a solid coating. This process is multidirectional, meaning the coating can cover complex geometries and hidden areas.
-
Operating Temperatures:
- PVD: PVD typically operates at lower temperatures, ranging from 250°C to 500°C. This makes it suitable for substrates that cannot withstand high temperatures.
- CVD: CVD requires much higher temperatures, often between 450°C and 1050°C. The high temperatures are necessary to drive the chemical reactions that form the coating. However, this limits its use with temperature-sensitive materials.
-
Coating Thickness and Uniformity:
- PVD: PVD coatings are generally thinner (3~5μm) and less uniform due to the line-of-sight nature of the process. However, they are faster to apply and can achieve ultra-hard films.
- CVD: CVD coatings are thicker (10~20μm) and more uniform, as the chemical reactions allow for better coverage of complex shapes. The process is slower but produces denser coatings.
-
Material Compatibility:
- PVD: PVD can deposit a wide range of materials, including metals, alloys, and ceramics. This versatility makes it suitable for various applications.
- CVD: CVD is typically limited to ceramics and polymers due to the nature of the chemical reactions involved. It is less versatile in terms of material compatibility.
-
Stress and Surface Properties:
- PVD: PVD coatings often exhibit compressive stress, which can enhance the durability and adhesion of the coating. The process also results in smoother surfaces.
- CVD: CVD coatings may develop tensile stress due to the high processing temperatures, which can lead to fine cracks. The coatings are denser but may require post-processing to achieve smoothness.
-
Applications:
- PVD: PVD is commonly used in applications requiring thin, hard coatings, such as cutting tools, decorative finishes, and wear-resistant surfaces.
- CVD: CVD is preferred for applications needing thick, uniform coatings, such as semiconductor manufacturing, protective coatings, and high-temperature components.
By understanding these key differences, purchasers and engineers can select the appropriate deposition technique based on their specific requirements, such as material compatibility, coating thickness, and operating conditions.
Summary Table:
Aspect | PVD | CVD |
---|---|---|
Deposition Mechanism | Physical transfer of material from a solid source (line-of-sight). | Chemical reactions between gaseous precursors and the substrate. |
Operating Temperatures | 250°C to 500°C (lower temperatures). | 450°C to 1050°C (higher temperatures). |
Coating Thickness | Thinner (3~5μm), less uniform. | Thicker (10~20μm), more uniform. |
Material Compatibility | Metals, alloys, ceramics (versatile). | Ceramics and polymers (limited versatility). |
Stress and Surface | Compressive stress, smoother surfaces. | Tensile stress, denser coatings, may require post-processing. |
Applications | Cutting tools, decorative finishes, wear-resistant surfaces. | Semiconductor manufacturing, protective coatings, high-temperature components. |
Need help choosing between PVD and CVD? Contact our experts today for tailored advice!