Cleaning PVD-coated products requires a careful approach to maintain the integrity and longevity of the coating. The process involves using mild cleaning agents and avoiding harsh chemicals or abrasive tools that could damage the coating. Understanding the PVD coating process and its steps can provide context for why certain cleaning methods are recommended. Below is a detailed explanation of how to clean PVD-coated products, supported by the provided references.
Key Points Explained:
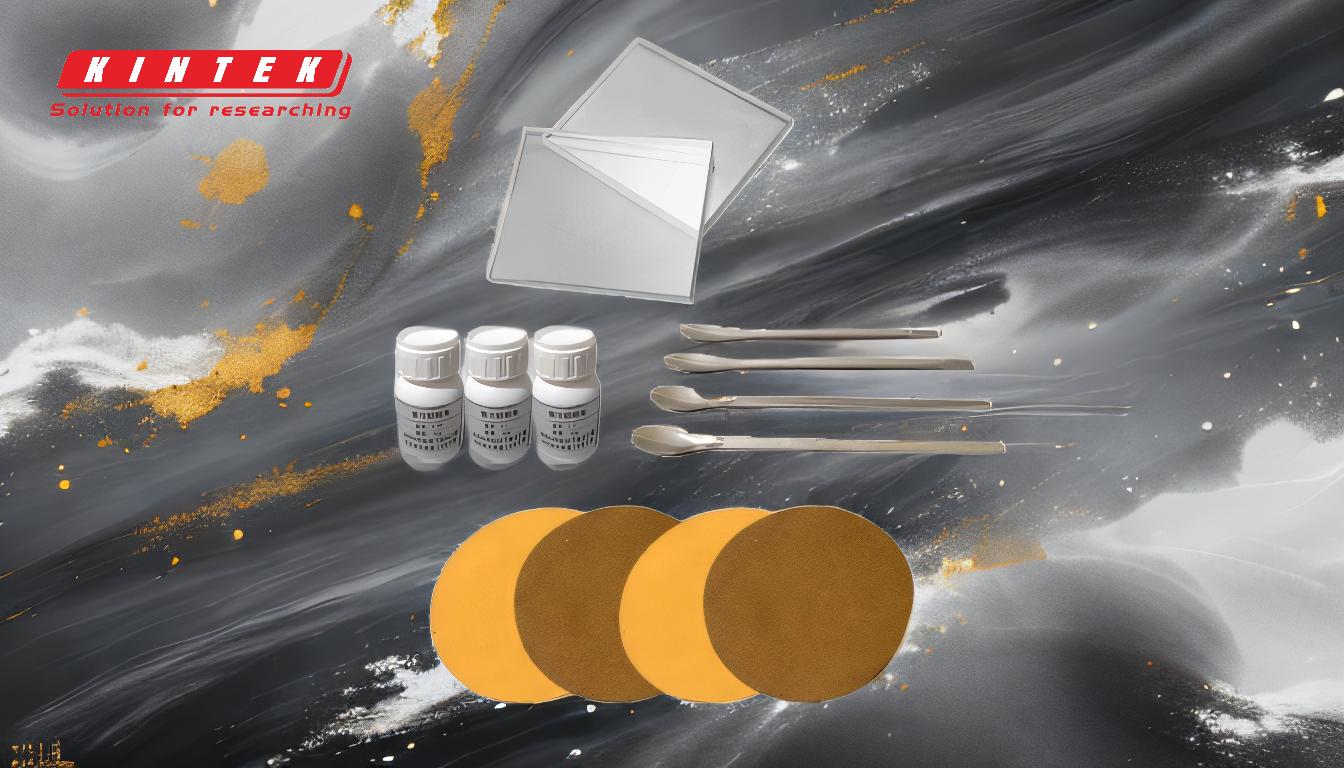
-
Recommended Cleaning Methods for PVD Coatings
- Soft Cloths and Mild Soap: PVD-coated products should be cleaned using soft cloths, water, and mild soap. These materials are gentle enough to avoid scratching or damaging the coating.
- Avoid Harsh Chemicals: Cleaning products containing hydrochloric acid, hydrofluoric acid, phosphoric acid, bleach, or other caustic agents should not be used. These chemicals can degrade the PVD coating, reducing its effectiveness and lifespan.
- Avoid Abrasive Tools: Scouring pads or abrasive cleaning tools should not be used, as they can scratch or remove the coating.
-
Why Gentle Cleaning is Necessary
- Coating Integrity: PVD coatings are thin films deposited onto substrates through a precise process involving evaporation, transportation, reaction, and deposition. These coatings are designed to be abrasion- and corrosion-resistant, but they can still be damaged by harsh chemicals or physical abrasion.
- Adhesion and Durability: The PVD coating process relies on strong adhesion between the coating and the substrate. Harsh cleaning methods can compromise this bond, leading to peeling or flaking of the coating.
-
Understanding the PVD Coating Process
- Steps in PVD Coating: The PVD coating process involves several steps, including substrate cleaning, pretreatment, vaporization, reaction, and deposition. These steps ensure that the coating adheres properly and provides the desired properties, such as hardness, corrosion resistance, and aesthetic appeal.
- Importance of Pre-Cleaning: Before the PVD coating is applied, the substrate undergoes thorough cleaning (e.g., ultrasonic cleaning, rinsing, and drying) to remove contaminants. This ensures proper adhesion of the coating. Post-coating cleaning should be equally gentle to preserve the coating's integrity.
-
Practical Cleaning Tips
- Regular Maintenance: Clean PVD-coated products regularly to prevent the buildup of dirt and grime, which can be harder to remove over time.
- Drying After Cleaning: After cleaning with water and mild soap, ensure the product is dried thoroughly with a soft cloth to prevent water spots or residue.
- Inspection: Periodically inspect the coating for signs of wear or damage. If scratches or discoloration are noticed, avoid further abrasive cleaning and consult a professional for advice.
-
Common Mistakes to Avoid
- Using Bleach or Acidic Cleaners: These can chemically react with the PVD coating, causing it to degrade or discolor.
- Scrubbing with Abrasives: Scrubbing with steel wool, scouring pads, or rough brushes can scratch the coating, making it more susceptible to damage.
- Neglecting Regular Cleaning: Allowing dirt and contaminants to accumulate can make cleaning more difficult and increase the risk of damaging the coating.
-
Long-Term Care for PVD-Coated Products
- Storage: Store PVD-coated products in a clean, dry environment to minimize exposure to moisture and contaminants.
- Protective Measures: Use protective covers or cases for PVD-coated items when not in use to prevent scratches and damage.
- Professional Maintenance: For high-value or heavily used items, consider periodic professional cleaning and maintenance to ensure the coating remains in optimal condition.
By following these guidelines, you can effectively clean and maintain PVD-coated products, ensuring they retain their aesthetic and functional properties for years to come. The key is to use gentle cleaning methods and avoid anything that could compromise the integrity of the coating.
Summary Table:
Key Aspect | Recommendations |
---|---|
Cleaning Tools | Use soft cloths, water, and mild soap. |
Avoid Harsh Chemicals | Stay away from acids, bleach, and caustic agents. |
Avoid Abrasive Tools | Do not use scouring pads or abrasive materials. |
Regular Maintenance | Clean regularly to prevent dirt buildup. |
Drying | Dry thoroughly with a soft cloth to avoid water spots. |
Inspection | Check for wear or damage periodically. |
Storage | Store in a clean, dry place to minimize exposure to contaminants. |
Professional Maintenance | For high-value items, consider professional cleaning and maintenance. |
Need expert advice on maintaining your PVD-coated products? Contact us today for personalized guidance!