Cleaning PVD (Physical Vapor Deposition) coatings requires a gentle approach to preserve the integrity and appearance of the coating. The process involves using mild cleaning agents and avoiding harsh chemicals or abrasive tools. A soft cloth, water, and mild soap are typically sufficient for routine cleaning. It is crucial to avoid products containing hydrochloric, hydrofluoric, phosphoric acid, or other caustic agents, as well as bleach and scouring pads, as these can damage the coating. By following these guidelines, you can maintain the durability and aesthetic quality of PVD-coated products.
Key Points Explained:
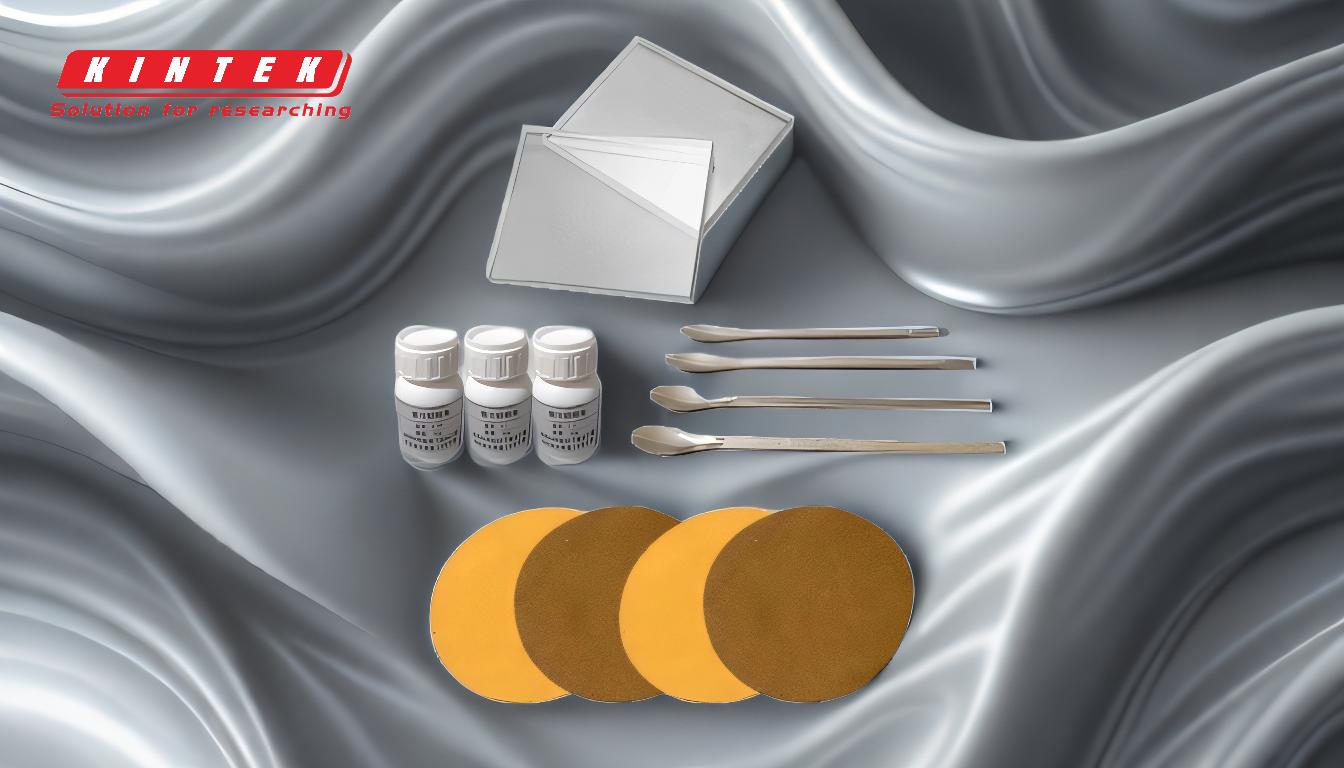
-
Use Mild Cleaning Agents:
- Explanation: PVD coatings are sensitive to harsh chemicals. Mild soap and water are recommended for cleaning because they are gentle enough to remove dirt and grime without damaging the coating.
- Why It Matters: Harsh chemicals can degrade the coating, leading to loss of color, reduced durability, and potential corrosion.
-
Avoid Acidic and Caustic Cleaners:
- Explanation: Cleaners containing hydrochloric, hydrofluoric, or phosphoric acid, as well as other caustic agents, should be avoided. These substances can react with the coating and cause irreversible damage.
- Why It Matters: Acidic and caustic agents can strip away the protective layer of the PVD coating, making it more susceptible to wear and tear.
-
Steer Clear of Bleach and Scouring Pads:
- Explanation: Bleach is a strong oxidizing agent that can discolor or weaken the PVD coating. Scouring pads are abrasive and can scratch the surface, leading to a loss of luster and protection.
- Why It Matters: Using bleach or abrasive tools can compromise the aesthetic and functional properties of the coating, reducing its lifespan.
-
Use Soft Cloths for Cleaning:
- Explanation: Soft cloths are recommended because they are gentle on the surface and do not cause scratches or abrasions.
- Why It Matters: Soft cloths help maintain the smooth and shiny appearance of the PVD coating, ensuring it remains visually appealing and functional.
-
Routine Maintenance:
- Explanation: Regular cleaning with mild soap and water can prevent the buildup of dirt and contaminants, which can degrade the coating over time.
- Why It Matters: Routine maintenance ensures the longevity and performance of the PVD coating, keeping it looking new and functioning effectively.
By adhering to these guidelines, you can effectively clean and maintain PVD-coated products, ensuring they remain durable and visually appealing for a longer period.
Summary Table:
Key Cleaning Tips for PVD Coatings | Why It Matters |
---|---|
Use mild soap and water | Prevents damage from harsh chemicals |
Avoid acidic and caustic cleaners | Protects the coating from irreversible damage |
Steer clear of bleach and scouring pads | Maintains the coating's appearance and durability |
Use soft cloths for cleaning | Prevents scratches and abrasions |
Perform routine maintenance | Ensures longevity and performance |
Need expert advice on maintaining PVD coatings? Contact us today for personalized guidance!