Silicon carbide (SiC) is a versatile material widely used in various industries due to its exceptional properties, such as high thermal conductivity, hardness, and resistance to wear and corrosion. The deposition of silicon carbide, particularly in the form of silicon carbide ceramic, is a critical process for applications like conductive ceramics, electric discharge machining, and industrial components. The primary methods for depositing silicon carbide include reaction sintering, atmospheric pressure sintering, and recrystallization sintering, each offering unique advantages depending on the desired microstructure, properties, and application requirements. Additionally, silicon carbide ceramic tubes are manufactured by mixing silicon carbide powder with sintering additives and heating them to extremely high temperatures, enabling the production of dense and complex shapes.
Key Points Explained:
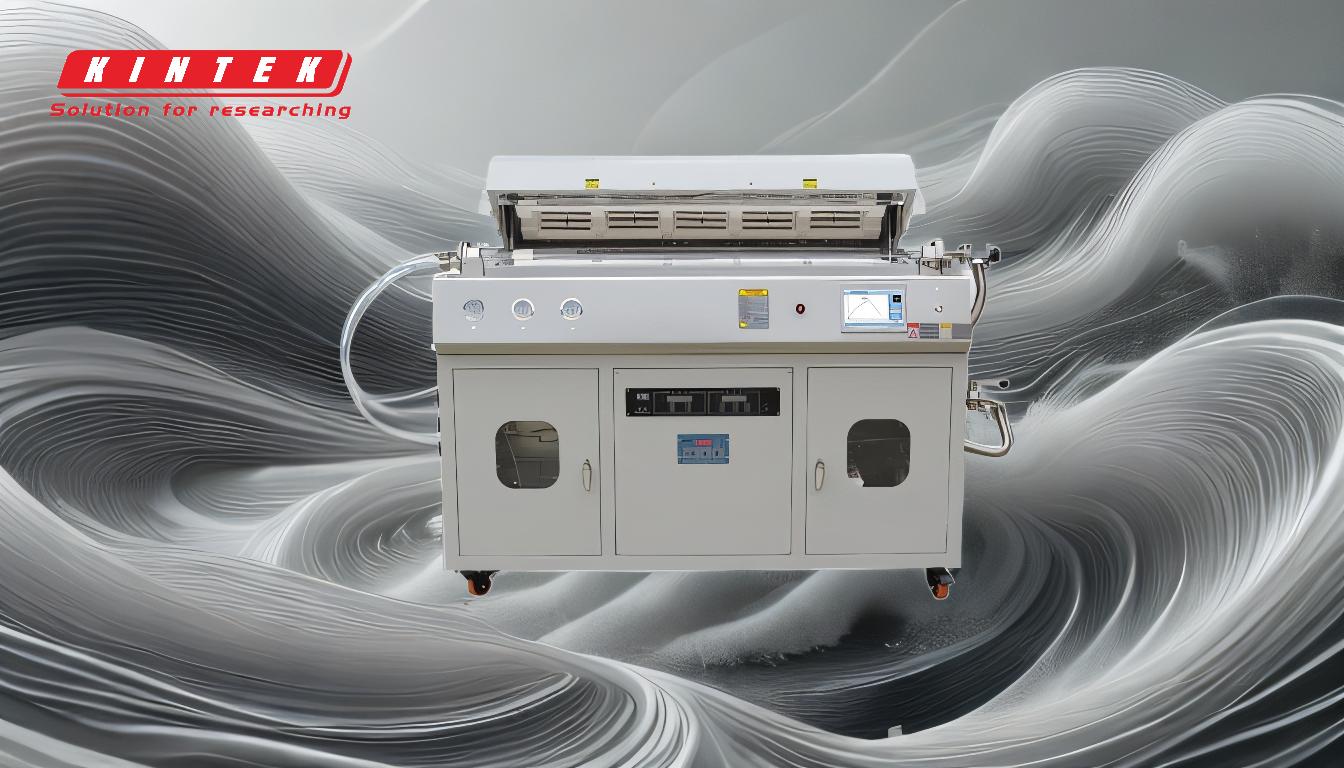
-
Methods of Silicon Carbide Deposition
- Reaction Sintering: This process involves reacting silicon with carbon at high temperatures to form silicon carbide. It is cost-effective and produces materials with good mechanical properties, making it suitable for applications requiring high strength and wear resistance.
- Atmospheric Pressure Sintering: This method uses silicon carbide powder mixed with sintering additives, which are heated under normal atmospheric conditions. It results in dense and high-purity silicon carbide ceramics, ideal for applications requiring tight dimensional control and minimal post-sintering shrinkage.
- Recrystallization Sintering: In this process, silicon carbide is sintered at high temperatures without the use of additives, leading to the formation of a porous structure. This method is often used for applications where thermal shock resistance is critical.
-
Manufacturing Silicon Carbide Ceramic Tubes
- Silicon carbide ceramic tubes are produced by mixing silicon carbide powder with non-oxide sintering additives and heating them to temperatures between 2000°C and 2600°C. This process ensures the formation of extremely dense and durable products.
- The tubes can be shaped using techniques such as casting and dry pressing, allowing for the creation of complex geometries. This is particularly beneficial for industrial applications requiring precise and intricate designs.
- The high density and hardness of silicon carbide enable tight dimensional control and minimal sintering after use, making these tubes suitable for high-performance applications.
-
Applications of Silicon Carbide Ceramics
- Conductive Ceramics: By controlling the resistivity of silicon carbide ceramics to below 100Ω·cm, they can be used in electric discharge machining (EDM). This allows for fast and accurate processing of complex surfaces, making it ideal for manufacturing large or intricately shaped components.
- Industrial Components: Silicon carbide is widely used in the ceramic industry for components such as receiving capsules and muffles. These are essential in the sintering of technical ceramics and porcelain, where high thermal and chemical stability are required.
-
Advantages of Silicon Carbide Deposition
- High Thermal Conductivity: Silicon carbide's ability to conduct heat efficiently makes it suitable for applications involving high temperatures, such as in muffles and heating elements.
- Wear and Corrosion Resistance: The material's hardness and resistance to wear and corrosion ensure long-lasting performance in harsh environments.
- Dimensional Stability: The minimal sintering after use and tight dimensional control make silicon carbide ceramics reliable for precision applications.
-
Considerations for Equipment and Consumable Purchasers
- When selecting silicon carbide ceramics, purchasers should consider the specific application requirements, such as thermal conductivity, resistivity, and dimensional accuracy.
- The choice of deposition method (reaction sintering, atmospheric pressure sintering, or recrystallization sintering) should align with the desired properties and performance characteristics of the final product.
- For industrial applications, the ability to produce complex shapes and maintain high density is a key factor in choosing silicon carbide ceramic tubes.
By understanding these key points, purchasers can make informed decisions about the deposition and application of silicon carbide ceramics, ensuring optimal performance and cost-effectiveness for their specific needs.
Summary Table:
Method | Key Features | Applications |
---|---|---|
Reaction Sintering | Cost-effective, high strength, wear resistance | High-strength components, wear-resistant parts |
Atmospheric Pressure Sintering | Dense, high-purity, tight dimensional control | Precision components, minimal shrinkage applications |
Recrystallization Sintering | Porous structure, thermal shock resistance | Thermal shock-resistant components |
Need high-performance silicon carbide for your application? Contact our experts today to find the right solution!