Maintaining temperature in a chemical reaction is essential for ensuring efficiency, safety, and quality. Temperature control directly impacts reaction rates, product yield, and the overall success of the process. Modern chemical reactors often employ automated systems to regulate temperature, ensuring optimal conditions for exothermic (heat-releasing) or endothermic (heat-absorbing) reactions. These systems include heating and cooling mechanisms, insulation, and real-time monitoring to prevent deviations that could halt the reaction or compromise safety. Proper temperature management also helps avoid unwanted side reactions, ensuring the desired outcome.
Key Points Explained:
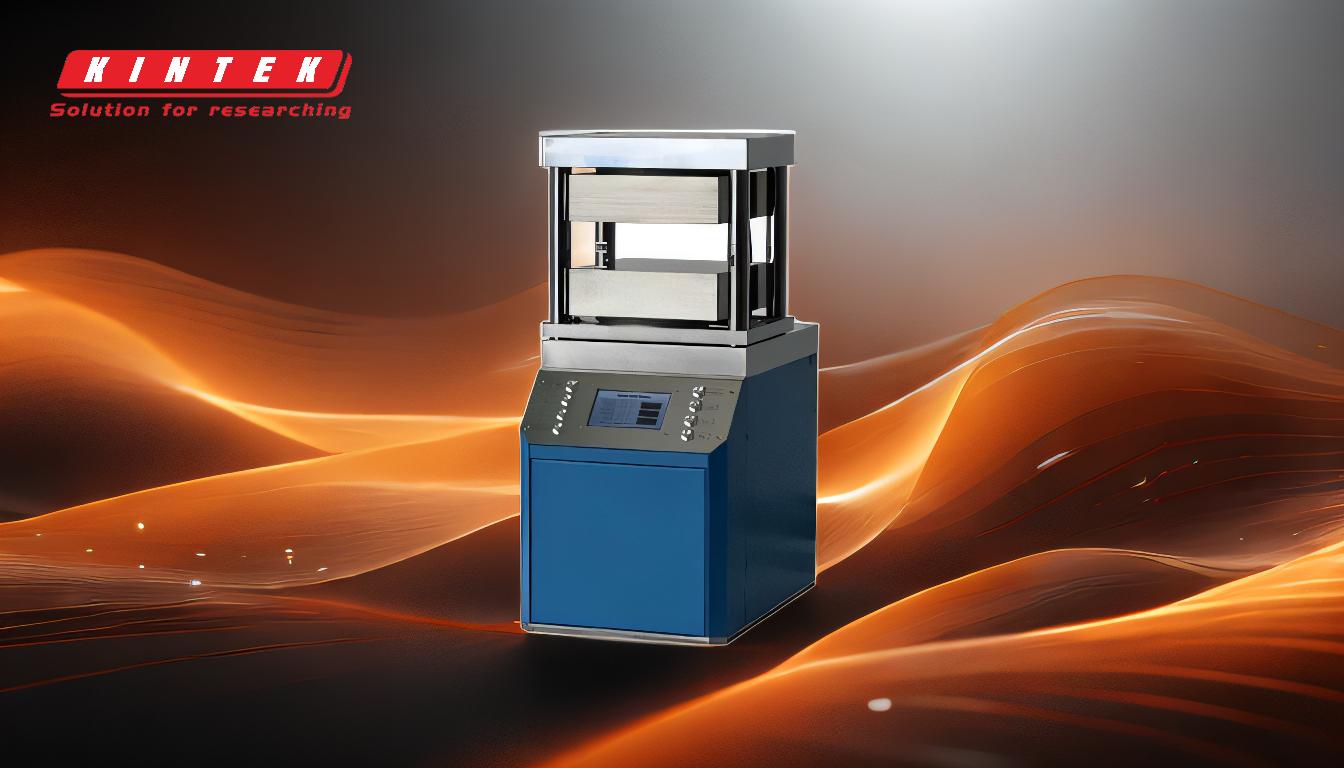
-
Importance of Temperature Control in Chemical Reactions:
- Temperature directly influences reaction kinetics, determining the rate at which reactants convert to products.
- Maintaining the correct temperature ensures the reaction proceeds efficiently and avoids unwanted side reactions.
- For exothermic reactions, excess heat must be removed to prevent runaway reactions, while endothermic reactions require consistent heat input to sustain the process.
-
Automated Temperature Control Systems:
- Modern reactors use automated systems to monitor and adjust temperature in real time.
- These systems include sensors, controllers, and actuators that work together to maintain the desired temperature range.
- Automation ensures precision, reduces human error, and allows for rapid adjustments in response to changes in reaction conditions.
-
Heating and Cooling Mechanisms:
- Heating: Methods such as electric heaters, steam jackets, or heat exchangers are used to supply heat to endothermic reactions.
- Cooling: Cooling jackets, chillers, or cryogenic systems are employed to remove excess heat from exothermic reactions.
- The choice of mechanism depends on the reaction's heat requirements and the reactor's design.
-
Insulation and Heat Retention:
- Proper insulation minimizes heat loss to the surroundings, ensuring consistent reaction conditions.
- Insulating materials, such as fiberglass or ceramic, are used to maintain temperature stability, especially in large-scale reactors.
-
Real-Time Monitoring and Feedback Loops:
- Temperature sensors (e.g., thermocouples or RTDs) continuously measure the reaction temperature.
- Data from these sensors is fed into control systems that adjust heating or cooling mechanisms as needed.
- This feedback loop ensures that the temperature remains within the optimal range, even if external conditions change.
-
Safety Considerations:
- Accurate temperature management prevents overheating, which can lead to dangerous situations such as explosions or equipment failure.
- Automated systems can trigger alarms or shut down the reaction if temperatures exceed safe limits.
-
Optimization for Exothermic and Endothermic Reactions:
- Exothermic Reactions: Heat removal is critical to prevent thermal runaway. Cooling systems must be designed to handle the maximum heat output.
- Endothermic Reactions: Consistent heat input is necessary to maintain the reaction rate. Heating systems must provide uniform and controlled heat distribution.
-
Impact on Product Quality and Yield:
- Maintaining the correct temperature ensures the desired product is formed with minimal impurities.
- Deviations from the optimal temperature range can lead to incomplete reactions, by-products, or degradation of the final product.
-
Scalability and Industrial Applications:
- Temperature control systems must be scalable to accommodate small laboratory setups or large industrial reactors.
- Industrial reactors often incorporate advanced technologies, such as distributed control systems (DCS), to manage complex reactions with multiple temperature zones.
-
Energy Efficiency and Cost Considerations:
- Efficient temperature control reduces energy consumption, lowering operational costs.
- Insulation and optimized heating/cooling systems contribute to energy savings while maintaining precise temperature regulation.
By integrating these elements, chemical engineers and operators can ensure that reactions proceed under optimal conditions, maximizing efficiency, safety, and product quality.
Summary Table:
Key Aspect | Description |
---|---|
Importance of Temperature Control | Influences reaction rates, ensures efficiency, and prevents unwanted side reactions. |
Automated Systems | Real-time monitoring and adjustments for precision and safety. |
Heating Mechanisms | Electric heaters, steam jackets, or heat exchangers for endothermic reactions. |
Cooling Mechanisms | Cooling jackets, chillers, or cryogenic systems for exothermic reactions. |
Insulation | Minimizes heat loss, ensuring consistent reaction conditions. |
Real-Time Monitoring | Sensors and feedback loops maintain optimal temperature ranges. |
Safety Considerations | Prevents overheating, explosions, and equipment failure. |
Exothermic Reactions | Heat removal to prevent thermal runaway. |
Endothermic Reactions | Consistent heat input to sustain reaction rates. |
Product Quality & Yield | Ensures desired product formation with minimal impurities. |
Scalability | Adaptable for small labs or large industrial reactors. |
Energy Efficiency | Reduces energy consumption and operational costs. |
Optimize your chemical reactions with advanced temperature control systems—contact our experts today!