Preparing silicon carbide (SiC) in the laboratory involves a series of chemical and thermal processes to synthesize this high-performance ceramic material. Silicon carbide is widely used in applications requiring high thermal conductivity, mechanical strength, and chemical resistance. The most common laboratory methods for preparing silicon carbide include the Acheson process, chemical vapor deposition (CVD), and sol-gel techniques. Each method has its own advantages and limitations, depending on the desired properties of the final product. Below, we explore the key steps and considerations for preparing silicon carbide in a laboratory setting.
Key Points Explained:
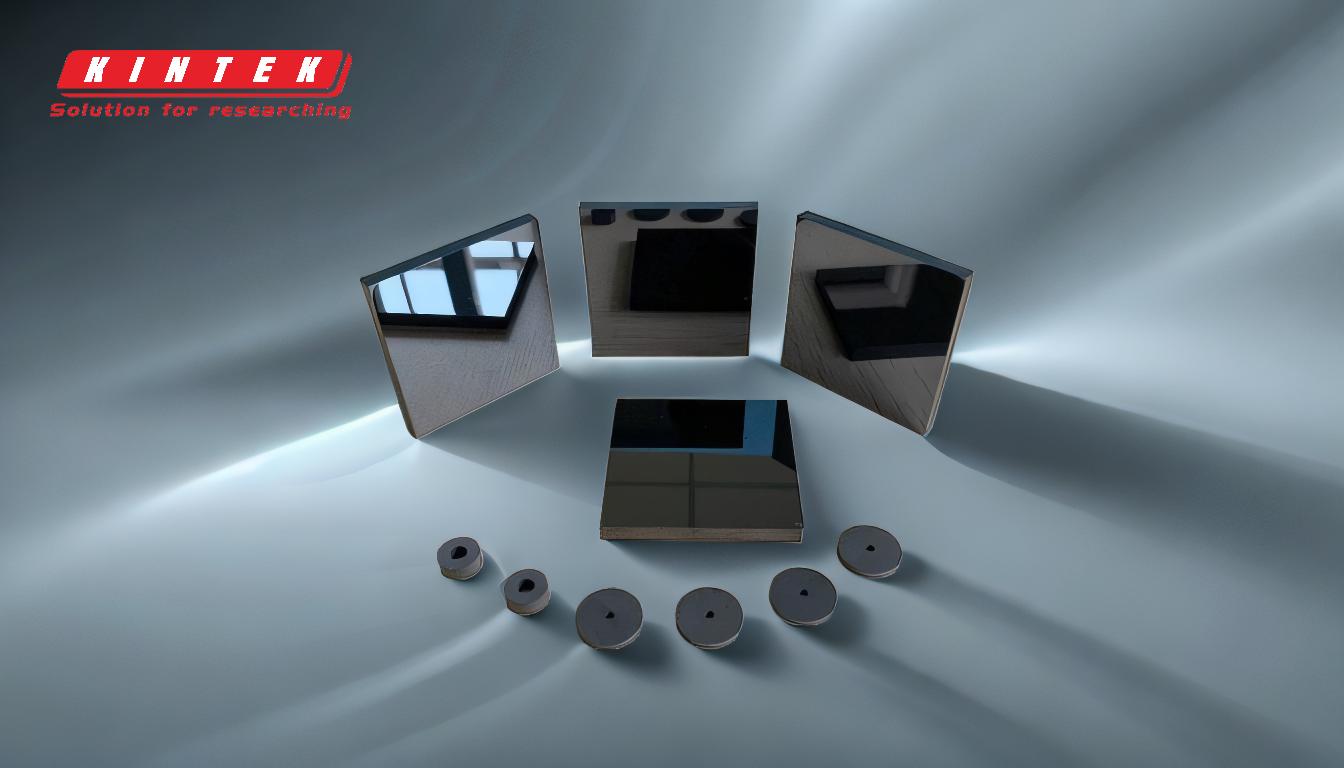
-
Understanding Silicon Carbide and Its Applications
- Silicon carbide (SiC) is a compound of silicon and carbon, known for its exceptional hardness, thermal conductivity, and resistance to oxidation and chemical attack.
- It is used in various industries, including electronics, abrasives, and high-temperature applications.
- The preparation of silicon carbide in the laboratory requires precise control over raw materials, reaction conditions, and post-processing steps to achieve the desired properties.
-
Raw Materials and Precursors
- The primary raw materials for preparing silicon carbide are silicon dioxide (SiO₂) and carbon (C).
- High-purity precursors are essential to avoid impurities that can affect the material's properties.
- In some methods, silicon tetrachloride (SiCl₄) or methyltrichlorosilane (CH₃SiCl₃) are used as silicon sources in vapor-phase reactions.
-
Acheson Process (Solid-State Reaction Method)
- The Acheson process is one of the oldest and most widely used methods for producing silicon carbide.
- It involves heating a mixture of silica sand (SiO₂) and carbon (C) in an electric furnace at temperatures above 2000°C.
- The reaction can be represented as:
[ \text{SiO}_2 + 3\text{C} \rightarrow \text{SiC} + 2\text{CO} ] - The process yields large crystals of silicon carbide, which are then crushed and graded for specific applications.
- This method is cost-effective but requires high energy consumption and produces CO as a byproduct.
-
Chemical Vapor Deposition (CVD)
- CVD is a versatile method for producing high-purity silicon carbide, often used for thin films and coatings.
- In this process, a silicon-containing gas (e.g., SiCl₄ or CH₃SiCl₃) and a carbon-containing gas (e.g., methane, CH₄) are introduced into a reaction chamber.
- The gases decompose at high temperatures (typically 1000–1500°C) and deposit silicon carbide onto a substrate.
- CVD allows precise control over the composition and microstructure of the material, making it suitable for electronic and optical applications.
- However, the process is expensive and requires specialized equipment.
-
Sol-Gel Method
- The sol-gel method is a wet-chemical approach for synthesizing silicon carbide at lower temperatures.
- It involves the preparation of a sol (a colloidal suspension) containing silicon and carbon precursors, followed by gelation and thermal treatment.
- The gel is heated to remove organic components and form silicon carbide.
- This method is advantageous for producing fine powders and nanostructured materials but may require additional steps to achieve high purity.
-
Post-Processing and Characterization
- After synthesis, silicon carbide often undergoes post-processing steps such as grinding, polishing, or sintering to achieve the desired shape and properties.
- Characterization techniques like X-ray diffraction (XRD), scanning electron microscopy (SEM), and Raman spectroscopy are used to analyze the material's structure, purity, and performance.
-
Challenges and Considerations
- The choice of method depends on the intended application, as each method has trade-offs in terms of cost, scalability, and material properties.
- High-temperature processes like the Acheson method require energy-efficient designs to minimize environmental impact.
- For advanced applications, achieving high purity and controlled microstructure is critical, often necessitating the use of CVD or sol-gel techniques.
-
Applications of Silicon Carbide Ceramic
- Silicon carbide ceramics are used in a wide range of applications, including:
- High-temperature components (e.g., furnace parts, rocket nozzles).
- Abrasives and cutting tools.
- Semiconductor devices and electronic substrates.
- Wear-resistant coatings and composites.
- The material's unique combination of properties makes it indispensable in industries requiring durability and performance under extreme conditions.
- Silicon carbide ceramics are used in a wide range of applications, including:
By carefully selecting the appropriate method and optimizing the synthesis conditions, silicon carbide can be prepared in the laboratory with the desired properties for specific applications. For more information on silicon carbide ceramics, visit silicon carbide ceramic.
Summary Table:
Method | Key Features | Advantages | Limitations |
---|---|---|---|
Acheson Process | High-temperature solid-state reaction (SiO₂ + C) | Cost-effective, large crystal production | High energy use, CO byproduct |
Chemical Vapor Deposition (CVD) | Gas-phase reaction (SiCl₄ + CH₄) at 1000–1500°C | High purity, precise control | Expensive, specialized equipment required |
Sol-Gel Method | Wet-chemical synthesis at lower temperatures | Fine powders, nanostructured materials | Additional steps for high purity |
Ready to optimize your silicon carbide synthesis? Contact our experts today for tailored solutions!