Preparing the surface for PVD (Physical Vapor Deposition) coating is a critical step to ensure the adhesion, durability, and overall quality of the coating. The process involves thorough cleaning, pretreatment, and ensuring the surface is free from contaminants. Proper surface preparation enhances the bonding between the substrate and the coating, leading to improved performance and longevity of the coated product. Below is a detailed explanation of the key steps and considerations involved in preparing the surface for PVD coating.
Key Points Explained:
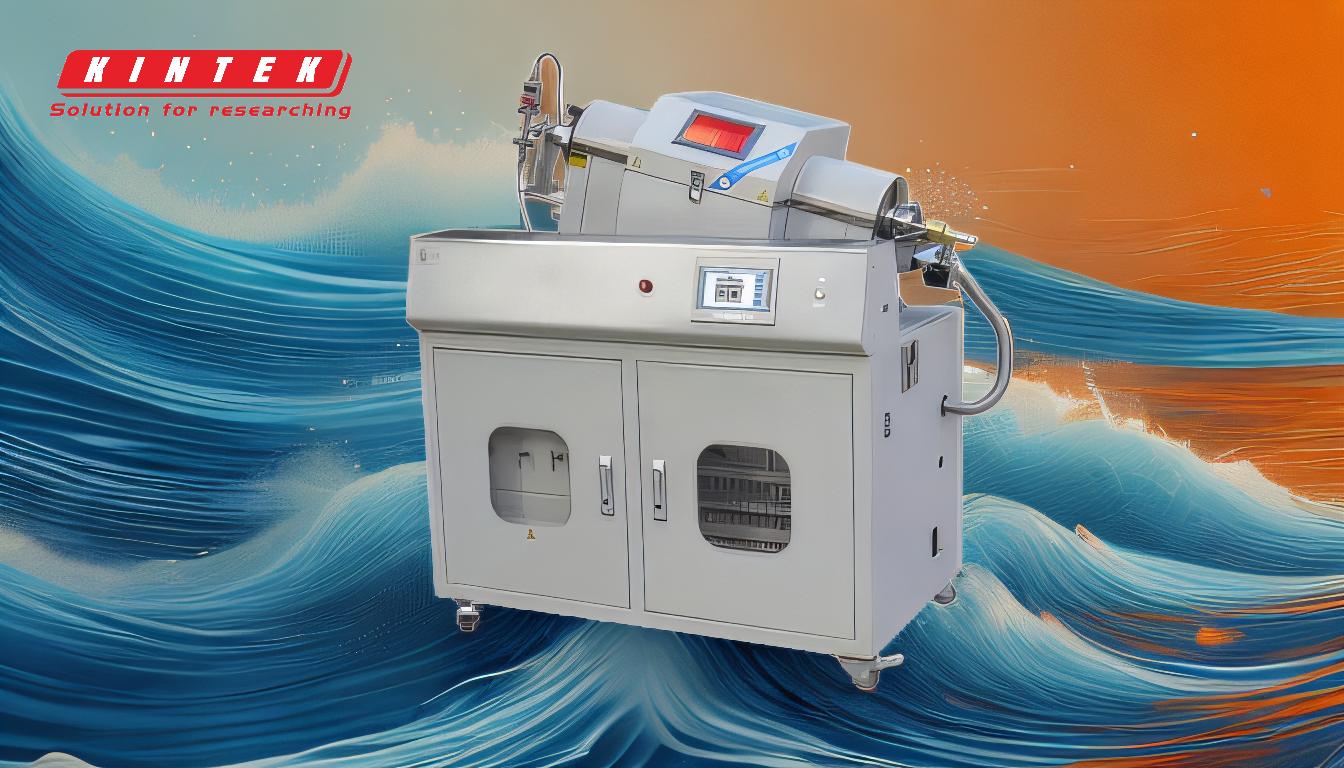
-
Cleaning the Substrate:
- Objective: Remove all contaminants such as oils, lubricants, cooling emulsions, dust, and other residues that could interfere with the adhesion of the PVD coating.
-
Methods:
- Ultrasonic Cleaning: Uses high-frequency sound waves to agitate a cleaning solution, effectively removing contaminants from the surface.
- Rinsing: After ultrasonic cleaning, the substrate is rinsed with deionized water to remove any remaining cleaning agents.
- Drying: The substrate is dried thoroughly to prevent water spots or residues that could affect the coating process.
- Importance: Cleanliness is crucial because even microscopic contaminants can lead to poor adhesion, defects, or premature failure of the coating.
-
Surface Pretreatment:
- Objective: Enhance the surface properties to improve the adhesion and performance of the PVD coating.
-
Methods:
- Mechanical Pretreatment: Techniques like sandblasting or polishing can be used to create a uniform surface texture, which improves coating adhesion.
- Chemical Pretreatment: Acid etching or alkaline cleaning can be employed to remove oxides or other chemical contaminants and activate the surface.
- Plasma Cleaning: A high-energy plasma treatment can be used to clean and activate the surface at a microscopic level, ensuring optimal bonding.
- Importance: Pretreatment ensures that the surface is not only clean but also chemically and physically prepared to bond with the coating material.
-
Avoiding Tightly Sealed Tapped Holes:
- Objective: Prevent trapped air or contaminants from affecting the coating quality.
- Considerations: Tightly sealed tapped holes can trap air or cleaning solutions, leading to uneven coating or defects. It is essential to ensure that all holes and cavities are accessible for cleaning and coating.
- Importance: This step ensures uniform coating coverage and prevents defects that could compromise the performance of the coated product.
-
Line-of-Sight Transfer Nature of PVD:
- Objective: Understand and account for the directional nature of the PVD process.
- Considerations: PVD is a line-of-sight process, meaning that the coating material is deposited in a straight line from the source to the substrate. This requires careful positioning of the substrate to ensure even coverage, especially for complex geometries.
- Importance: Proper positioning and fixture design are critical to achieving uniform coating thickness and avoiding shadowed areas that may remain uncoated.
-
Quality Control and Testing:
- Objective: Ensure the surface preparation meets the required standards before proceeding with the coating process.
-
Methods:
- Visual Inspection: Check for any visible contaminants or defects on the surface.
- Surface Energy Testing: Measure the surface energy to ensure it is suitable for coating adhesion.
- Microscopic Analysis: Use microscopy to inspect the surface at a microscopic level for any irregularities.
- Importance: Quality control ensures that the surface is properly prepared, reducing the risk of coating failures and ensuring consistent results.
-
Environmental and Safety Considerations:
- Objective: Maintain a clean and controlled environment during surface preparation.
-
Considerations:
- Cleanroom Conditions: Perform cleaning and pretreatment in a controlled environment to minimize contamination.
- Personal Protective Equipment (PPE): Use appropriate PPE to protect against chemicals and other hazards during the cleaning and pretreatment processes.
- Importance: A controlled environment and proper safety measures ensure the integrity of the surface preparation process and protect personnel.
By following these steps and considerations, the surface can be effectively prepared for PVD coating, ensuring optimal adhesion, durability, and performance of the final product.
Summary Table:
Step | Objective | Methods | Importance |
---|---|---|---|
Cleaning the Substrate | Remove contaminants like oils, dust, and residues. | Ultrasonic cleaning, rinsing, drying. | Ensures no microscopic contaminants affect adhesion or cause defects. |
Surface Pretreatment | Enhance surface properties for better adhesion. | Mechanical (sandblasting), chemical (acid etching), or plasma cleaning. | Prepares the surface chemically and physically for optimal bonding. |
Avoiding Tightly Sealed Holes | Prevent trapped air or contaminants. | Ensure all holes and cavities are accessible for cleaning. | Ensures uniform coating and prevents defects. |
Line-of-Sight Transfer | Account for the directional nature of PVD. | Proper positioning and fixture design. | Achieves uniform coating thickness and avoids uncoated areas. |
Quality Control | Verify surface preparation meets standards. | Visual inspection, surface energy testing, microscopic analysis. | Reduces risk of coating failures and ensures consistent results. |
Environmental & Safety | Maintain a clean, controlled environment. | Cleanroom conditions, use of PPE. | Protects surface integrity and personnel during preparation. |
Ensure your PVD coating process delivers the best results—contact our experts today for tailored guidance!