Rejuvenating vacuum tubes is a process that involves carefully adjusting the filament voltage to restore the tube's performance. This method is particularly useful for older or degraded tubes that have lost their efficiency. The process begins by increasing the filament voltage to a point where the tube's performance reaches its maximum reading. Once this peak is achieved, the voltage is reduced back to the rated value. The tube is then operated at this rated voltage for at least four hours, after which it is tested. If two consecutive tests, spaced one hour apart, yield the same reading, the tube is considered rejuvenated. This method ensures that the tube's internal components are properly conditioned, restoring it to optimal functionality.
Key Points Explained:
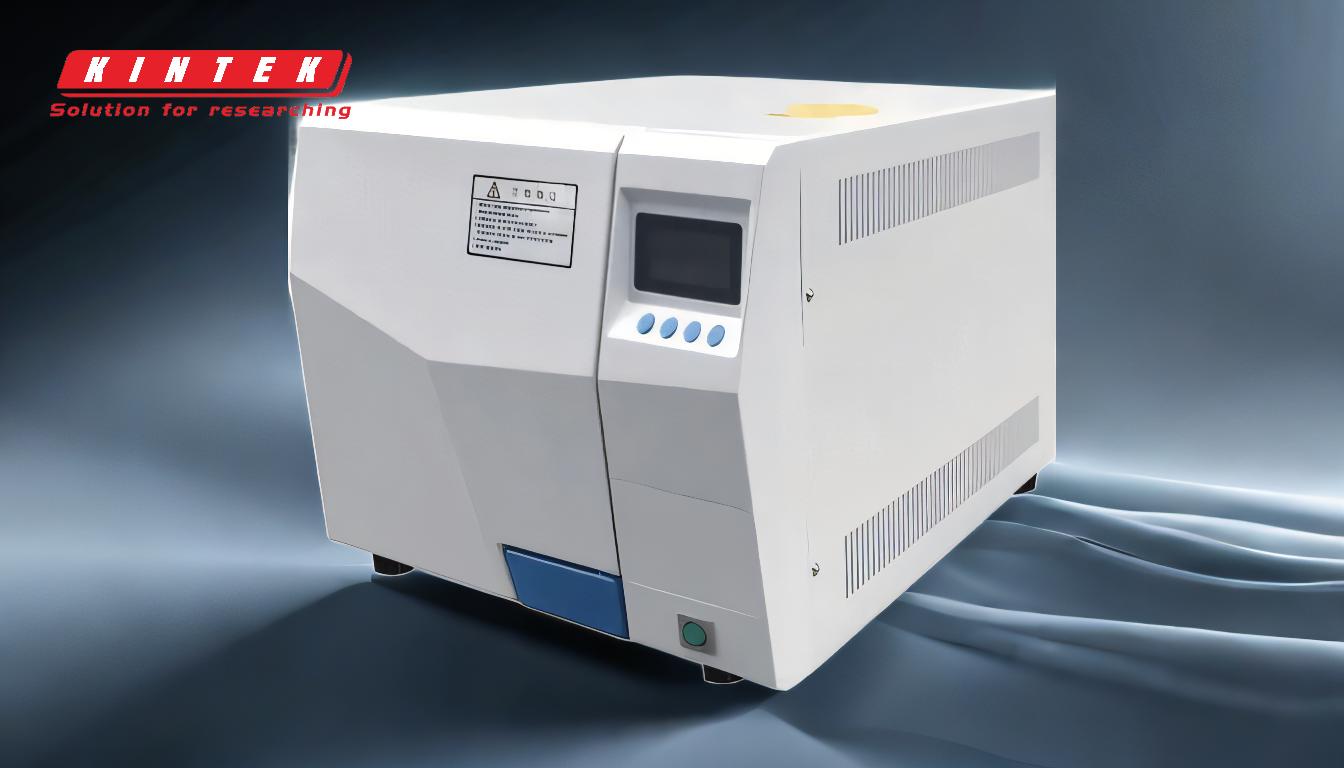
-
Understanding the Rejuvenation Process:
- Rejuvenation is a method used to restore the performance of vacuum tubes that have degraded over time.
- This process is particularly useful for vintage or high-value tubes that may be difficult or expensive to replace.
-
Step-by-Step Rejuvenation Procedure:
-
Initial Voltage Adjustment:
- Start by increasing the filament voltage beyond the tube's rated value. This step is crucial as it helps to "burn off" any contaminants or deposits that may have accumulated on the tube's internal components.
-
Monitoring Performance:
- As the voltage is increased, monitor the tube's performance. The goal is to reach a point where the tube's output (e.g., current, emission) is at its maximum.
-
Reducing Voltage to Rated Value:
- Once the maximum performance is achieved, reduce the filament voltage back to the tube's rated value. This step ensures that the tube is not subjected to excessive stress, which could lead to premature failure.
-
Operating at Rated Voltage:
- Operate the tube at the rated filament voltage for at least four hours. This period allows the tube to stabilize and ensures that any remaining contaminants are fully burned off.
-
Testing the Tube:
- After the four-hour period, test the tube's performance. The key indicator of successful rejuvenation is consistency in performance readings.
-
Verification:
- Conduct two tests, spaced one hour apart. If both tests yield the same performance reading, the tube is considered rejuvenated. This consistency indicates that the tube has been restored to its optimal operating condition.
-
Initial Voltage Adjustment:
-
Importance of Filament Voltage:
- The filament voltage plays a critical role in the rejuvenation process. It directly affects the tube's emission characteristics and overall performance.
- Properly adjusting the filament voltage ensures that the tube's internal components are adequately heated, which is essential for removing contaminants and restoring performance.
-
Safety Considerations:
-
Voltage Limits:
- It is crucial to avoid exceeding the tube's maximum filament voltage, as this can cause permanent damage. Always refer to the tube's datasheet for specific voltage ratings.
-
Monitoring:
- Continuous monitoring during the rejuvenation process is essential to prevent overheating or other forms of damage.
-
Cooling Periods:
- Allow the tube to cool down between tests, especially if multiple rejuvenation cycles are required. This prevents thermal stress and extends the tube's lifespan.
-
Voltage Limits:
-
Benefits of Rejuvenation:
-
Cost-Effectiveness:
- Rejuvenation can extend the life of expensive or hard-to-find vacuum tubes, reducing the need for frequent replacements.
-
Performance Restoration:
- Properly rejuvenated tubes can perform as well as, or even better than, new tubes, ensuring optimal operation in audio equipment, amplifiers, and other applications.
-
Environmental Impact:
- By extending the life of vacuum tubes, rejuvenation contributes to reducing electronic waste, making it an environmentally friendly practice.
-
Cost-Effectiveness:
-
Limitations and Risks:
-
Not All Tubes Can Be Rejuvenated:
- Some tubes may be too degraded or damaged to benefit from rejuvenation. In such cases, replacement is the only viable option.
-
Potential for Damage:
- Incorrectly applied voltage or prolonged operation at high voltages can cause irreversible damage to the tube.
-
Temporary Solution:
- Rejuvenation is not a permanent fix. Over time, the tube may degrade again, requiring additional rejuvenation or eventual replacement.
-
Not All Tubes Can Be Rejuvenated:
-
Practical Applications:
-
Audio Equipment:
- Vacuum tubes are commonly used in high-fidelity audio equipment. Rejuvenation can restore the warm, rich sound that tube amplifiers are known for.
-
Vintage Electronics:
- For collectors and enthusiasts of vintage electronics, rejuvenation is a valuable technique for maintaining and restoring old equipment.
-
Laboratory and Industrial Use:
- In some laboratory and industrial settings, vacuum tubes are still used for specialized applications. Rejuvenation can help maintain the reliability and performance of these critical components.
-
Audio Equipment:
By following these steps and considerations, you can effectively rejuvenate vacuum tubes, ensuring they continue to perform at their best. This process not only saves money but also preserves the unique characteristics that make vacuum tubes desirable in various applications.
Summary Table:
Step | Description |
---|---|
Initial Voltage Adjustment | Increase filament voltage beyond rated value to burn off contaminants. |
Monitor Performance | Track tube output to identify maximum performance. |
Reduce Voltage | Lower voltage to rated value to prevent stress and damage. |
Operate at Rated Voltage | Run the tube at rated voltage for 4+ hours to stabilize. |
Test Tube Performance | Conduct two tests, one hour apart, to verify consistent readings. |
Verification | If readings match, the tube is rejuvenated and ready for use. |
Need help rejuvenating your vacuum tubes? Contact our experts today for personalized guidance!