Thin film deposition is a critical process in materials science and engineering, used to create layers of material ranging from a few nanometers to several micrometers in thickness. The process involves depositing a thin layer of material onto a substrate, which can be achieved through various methods broadly categorized into chemical and physical deposition techniques. These methods include Physical Vapor Deposition (PVD), Chemical Vapor Deposition (CVD), Atomic Layer Deposition (ALD), and others like spin coating and spray pyrolysis. Each method has unique steps and is chosen based on the desired film properties, such as thickness, composition, and application requirements.
Key Points Explained:
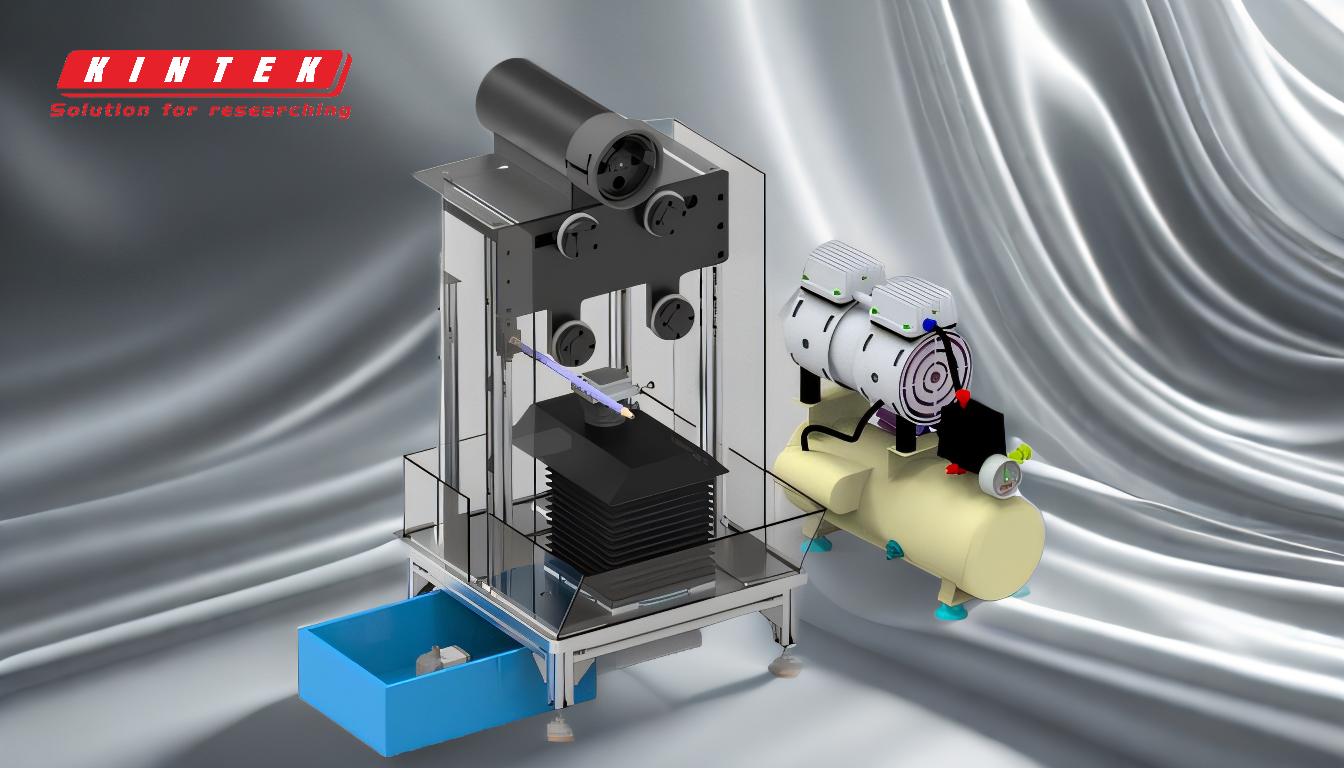
-
Overview of Thin Film Deposition Methods:
- Thin film deposition techniques are broadly categorized into chemical and physical methods.
- Chemical methods include processes like Chemical Vapor Deposition (CVD), Plasma-Enhanced CVD (PECVD), Atomic Layer Deposition (ALD), electroplating, sol-gel, dip coating, and spin coating.
- Physical methods primarily involve Physical Vapor Deposition (PVD), which includes techniques like sputtering, thermal evaporation, electron beam evaporation, molecular beam epitaxy (MBE), and pulsed laser deposition (PLD).
-
Physical Vapor Deposition (PVD):
- PVD involves vaporizing a solid material in a vacuum and depositing it onto a substrate.
- Common PVD techniques include:
- Sputtering: A target material is bombarded with ions, causing atoms to be ejected and deposited onto the substrate.
- Thermal Evaporation: The material is heated until it evaporates and then condenses on the substrate.
- Electron Beam Evaporation: An electron beam is used to heat and evaporate the material.
- Molecular Beam Epitaxy (MBE): A highly controlled method where beams of atoms or molecules are directed at the substrate to grow epitaxial layers.
- Pulsed Laser Deposition (PLD): A laser is used to ablate material from a target, which then deposits onto the substrate.
-
Chemical Vapor Deposition (CVD):
- CVD involves chemical reactions to produce high-purity thin films.
- Common CVD techniques include:
- Chemical Bath Deposition: A substrate is immersed in a chemical solution, and a film is deposited through a chemical reaction.
- Plasma-Enhanced CVD (PECVD): A plasma is used to enhance the chemical reaction, allowing deposition at lower temperatures.
- Atomic Layer Deposition (ALD): Films are deposited one atomic layer at a time, allowing for precise control over thickness and composition.
-
Other Deposition Techniques:
- Spin Coating: A liquid solution is applied to a substrate, which is then spun at high speed to spread the solution into a thin, uniform layer.
- Spray Pyrolysis: A solution containing the desired material is sprayed onto a heated substrate, where it decomposes to form a thin film.
- Electroplating: An electrical current is used to reduce metal ions in a solution, depositing them onto a conductive substrate.
- Sol-Gel: A colloidal solution (sol) is used to form a gel, which is then dried and sintered to create a thin film.
-
Steps in Thin Film Deposition:
- Almost all thin film deposition techniques follow four or five basic chronological steps:
- Preparation of the Substrate: Cleaning and preparing the substrate to ensure proper adhesion of the film.
- Generation of the Vapor or Solution: Creating the vapor or solution from which the film will be deposited.
- Transport of the Vapor or Solution: Moving the vapor or solution to the substrate.
- Deposition of the Film: The vapor or solution condenses or reacts to form a thin layer on the substrate.
- Post-Deposition Treatment: Additional steps like annealing or curing to improve film properties.
- Almost all thin film deposition techniques follow four or five basic chronological steps:
-
Applications of Thin Film Deposition:
- Thin films are used in a wide range of applications, including:
- Electronics: Semiconductor devices, integrated circuits, and displays.
- Optics: Anti-reflective coatings, mirrors, and optical filters.
- Energy: Solar cells, fuel cells, and batteries.
- Protective Coatings: Corrosion-resistant and wear-resistant coatings.
- Thin films are used in a wide range of applications, including:
-
Considerations for Choosing a Deposition Method:
- Film Properties: Desired thickness, uniformity, and composition.
- Substrate Material: Compatibility with the deposition method.
- Cost and Scalability: Cost-effectiveness and ability to scale up for industrial production.
- Environmental and Safety Concerns: Handling of hazardous materials and by-products.
In conclusion, thin film deposition is a versatile and essential process in modern technology, with a wide range of methods available to suit different applications. The choice of deposition technique depends on the specific requirements of the film and the substrate, as well as practical considerations like cost and scalability. Understanding the various methods and their steps is crucial for achieving high-quality thin films with the desired properties.
Summary Table:
Category | Methods | Key Features |
---|---|---|
Physical Vapor Deposition (PVD) | Sputtering, Thermal Evaporation, Electron Beam Evaporation, MBE, PLD | High precision, vacuum environment, ideal for metals and alloys |
Chemical Vapor Deposition (CVD) | CVD, PECVD, ALD, Chemical Bath Deposition | High-purity films, chemical reactions, suitable for complex compositions |
Other Techniques | Spin Coating, Spray Pyrolysis, Electroplating, Sol-Gel | Cost-effective, scalable, versatile for various substrates and materials |
Applications | Electronics, Optics, Energy, Protective Coatings | Used in semiconductors, solar cells, anti-reflective coatings, and more |
Need help selecting the right thin film deposition method for your project? Contact our experts today!