A pyrolysis furnace is a critical component in a pyrolysis plant, designed to thermally decompose organic materials in the absence of oxygen. This process, known as pyrolysis, breaks down complex molecules into simpler compounds, such as oil gas, carbon black, and syngas. The furnace operates at high temperatures, typically between 400°C and 800°C, depending on the feedstock and desired outputs. Waste materials like used tires, plastics, rubber, and medical waste are fed into the furnace, where they undergo thermal cracking. The absence of oxygen prevents combustion, ensuring that the materials decompose into useful byproducts rather than burning. These byproducts can then be collected, refined, and repurposed for various industrial applications.
Key Points Explained:
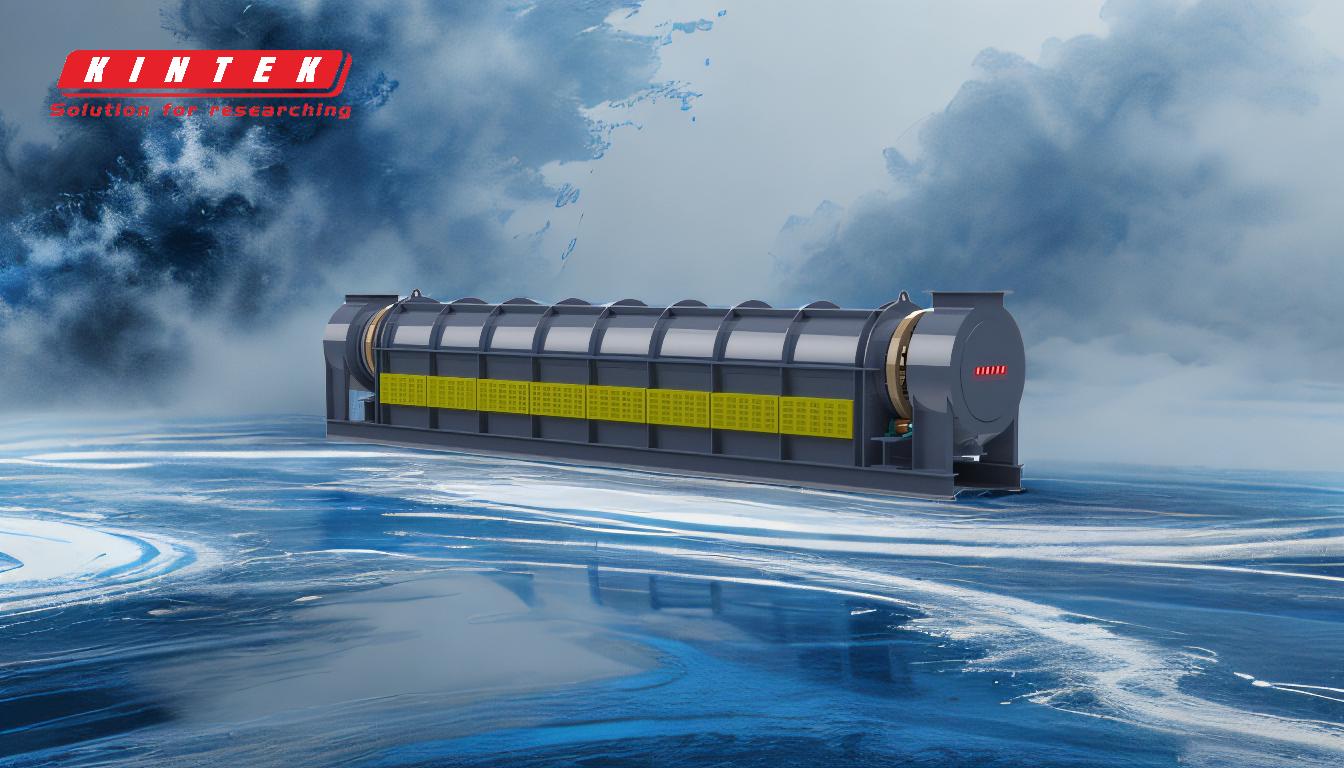
-
Principle of Pyrolysis:
- Pyrolysis is a thermochemical decomposition process that occurs in the absence of oxygen. This lack of oxygen prevents combustion, allowing the material to break down into smaller molecules.
- In a pyrolysis plant, organic materials like tires, plastics, and rubber are heated to high temperatures, causing their molecular bonds to break and form oil gas, carbon black, and syngas.
-
Function of the Pyrolysis Furnace:
- The furnace is the core component where the pyrolysis reaction takes place. It is designed to maintain high temperatures (400°C–800°C) and an oxygen-free environment.
- The furnace heats the feedstock uniformly to ensure efficient thermal decomposition. This is achieved through indirect heating methods, such as hot air or thermal oil circulation.
-
Feedstock and Applications:
- The pyrolysis furnace can process a wide range of waste materials, including used tires, waste plastics, rubber, and medical waste.
- Each type of feedstock requires specific temperature settings and processing times to maximize the yield of valuable byproducts.
-
Byproducts of Pyrolysis:
- Oil Gas: A mixture of hydrocarbons that can be condensed into liquid fuel or used as a gaseous fuel.
- Carbon Black: A fine powder used in manufacturing tires, inks, and coatings.
- Syngas: A mixture of hydrogen and carbon monoxide, which can be used as a fuel or chemical feedstock.
-
Continuous vs. Batch Pyrolysis:
- Continuous pyrolysis plants, like those mentioned in the reference, allow for uninterrupted processing of waste materials, improving efficiency and output.
- Batch pyrolysis plants process materials in discrete batches, which may be more suitable for smaller-scale operations.
-
Environmental Benefits:
- Pyrolysis furnaces help reduce waste by converting non-recyclable materials into valuable resources.
- The process minimizes emissions and pollution, as it operates in a closed system without oxygen.
-
Operational Considerations:
- Proper temperature control is crucial to ensure efficient decomposition and prevent the formation of unwanted byproducts.
- Regular maintenance of the furnace and associated equipment is necessary to ensure long-term reliability and safety.
By understanding how a pyrolysis furnace works, purchasers of equipment and consumables can make informed decisions about the type of pyrolysis plant that best suits their needs, ensuring optimal performance and sustainability.
Summary Table:
Aspect | Details |
---|---|
Principle | Thermochemical decomposition in the absence of oxygen. |
Temperature Range | 400°C–800°C, depending on feedstock and desired outputs. |
Feedstock | Used tires, plastics, rubber, medical waste, and other organic materials. |
Byproducts | Oil gas, carbon black, and syngas. |
Environmental Benefits | Reduces waste, minimizes emissions, and converts non-recyclables into resources. |
Operational Modes | Continuous (efficient, high-output) or batch (suitable for smaller scales). |
Ready to transform waste into valuable resources? Contact us today to find the perfect pyrolysis furnace for your needs!