A pyrolysis system is a complex setup designed to thermally decompose organic materials in the absence of oxygen, converting them into valuable byproducts like syngas, bio-oil, and bio-char. The system typically includes a feeding system, a pyrolysis reactor, a discharging system, a syn-gas recycling system, and a de-dusting system. The reactor is the core component where high-temperature pyrolysis occurs, involving both physical and chemical reactions. The system is designed to operate efficiently, safely, and in compliance with environmental standards, making it suitable for processing materials like biomass, plastics, and tires.
Key Points Explained:
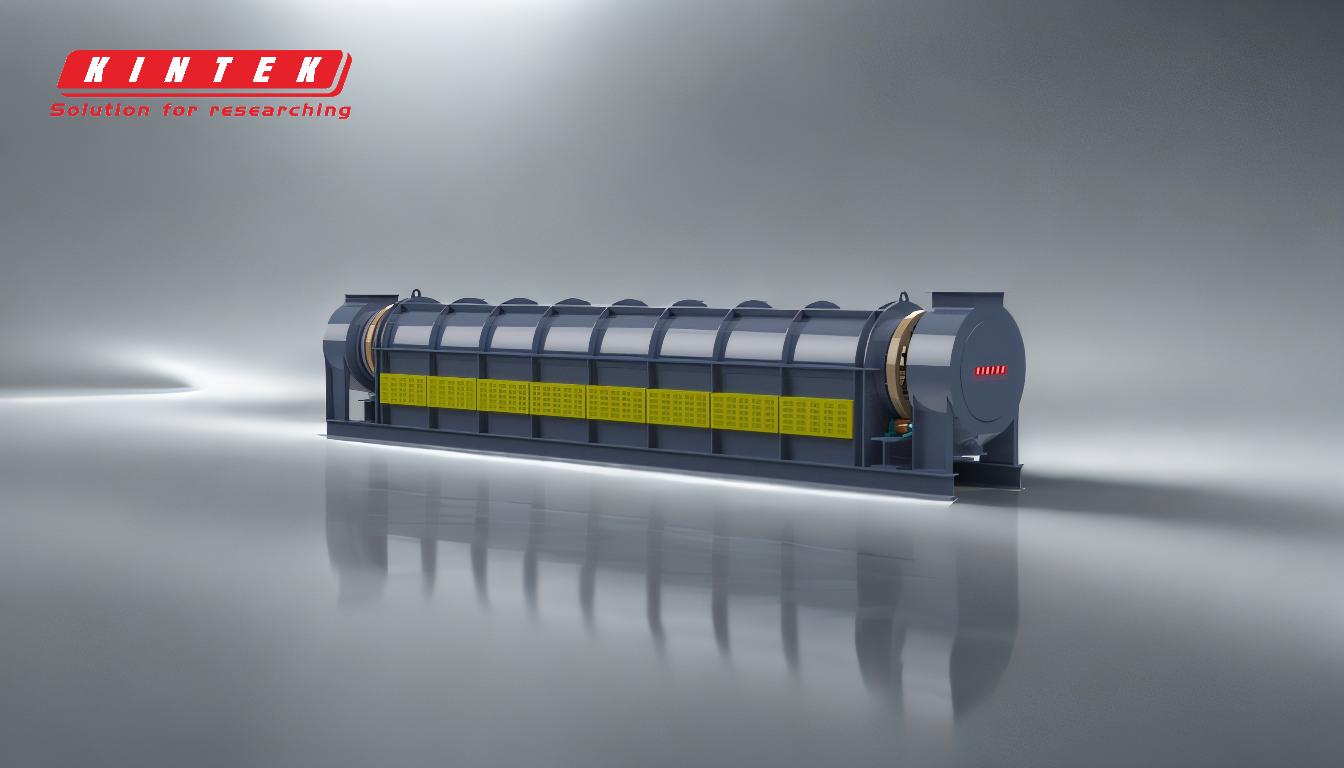
-
Feeding System:
- The feeding system is responsible for delivering raw materials into the pyrolysis reactor in a fully sealed manner. This ensures that no oxygen enters the reactor, which is crucial for the pyrolysis process.
- The system is automated, allowing for continuous and efficient operation, reducing the risk of human error and ensuring consistent feed rates.
-
Pyrolysis Reactor:
- The pyrolysis reactor is the heart of the system where the thermal decomposition of materials occurs. It operates at high temperatures, typically between 400°C and 900°C, in the absence of oxygen.
- The reactor can come in various designs, including batch, fixed-bed, and ablative reactors. Each design has its own advantages and is chosen based on the specific requirements of the pyrolysis process.
- The reactor rotates under the operation of a driving device, ensuring that the raw materials absorb heat evenly and undergo thermal decomposition uniformly.
- The quality and design of the reactor are critical for the efficient operation of the pyrolysis unit, as well as for ensuring the safety of personnel and equipment.
-
Discharging System:
- Once the pyrolysis process is complete, the discharging system transports the resulting carbon black into a tank equipped with a water-cooling pipe. This cooling process is essential to prevent the carbon black from overheating and to prepare it for further processing or storage.
- The system is designed to handle the byproducts efficiently, ensuring that they are safely and effectively removed from the reactor.
-
Syn-Gas Recycling System:
- The syn-gas recycling system captures and recycles the combustible gas produced during the pyrolysis process. This gas can be used to directly heat the reactor, making the system more energy-efficient and sustainable.
- By recycling the syn-gas, the system reduces the need for external energy sources, lowering operational costs and minimizing environmental impact.
-
De-Dusting System:
- The de-dusting system is responsible for purifying the emission gas to meet stringent environmental standards, such as those set by the EU. This system removes particulate matter and other pollutants from the gas before it is released into the atmosphere.
- Ensuring that the emission gas is clean and compliant with regulations is crucial for the environmental sustainability of the pyrolysis system.
-
Types of Pyrolysis Reactors:
- Batch Reactor: A simple, sealed vessel with apertures for introducing the substrate material. It is ideal for operations requiring energy stability and is often used in smaller-scale or experimental setups.
- Fixed-Bed Reactor: A straightforward design where the substrate is introduced at the bottom, and heat is applied. Heat transfer occurs from the walls of the vessel to the substrate at a consistent rate, leading to thermal decomposition. This type of reactor does not require a fluid or always need a catalyst.
- Ablative Reactor: A pressure-driven reactor that works by 'melting' the substrate against the heated walls of the reactor vessel. This design is particularly effective for processing biomass, as the melted material leaves a film of residual oil that acts as a lubricant for other particles.
-
Safety and Control Systems:
- The pyrolysis system includes various safety and control mechanisms to ensure efficient and safe operation. These systems monitor and regulate temperature, pressure, and feed rates, preventing accidents and ensuring consistent product quality.
- Advanced control systems also allow for the automation of many processes, reducing the need for manual intervention and increasing overall system reliability.
In summary, a pyrolysis system is a sophisticated setup designed to convert organic materials into valuable byproducts through thermal decomposition. The system's efficiency, safety, and environmental compliance are ensured through the integration of various components, including the feeding system, pyrolysis reactor, discharging system, syn-gas recycling system, and de-dusting system. Each component plays a critical role in the overall operation, making the system suitable for a wide range of applications, from waste management to renewable energy production.
Summary Table:
Component | Function |
---|---|
Feeding System | Delivers raw materials into the reactor in a sealed, automated manner. |
Pyrolysis Reactor | Core component for thermal decomposition at 400°C–900°C without oxygen. |
Discharging System | Transports and cools carbon black for storage or further processing. |
Syn-Gas Recycling | Captures and recycles combustible gas to heat the reactor, improving efficiency. |
De-Dusting System | Purifies emission gas to meet environmental standards. |
Safety & Control | Ensures safe, automated operation with temperature and pressure monitoring. |
Ready to explore how a pyrolysis system can benefit your operations? Contact us today for expert guidance!