A rotary kiln is a cylindrical, slightly inclined vessel that rotates slowly around its longitudinal axis. It is designed to heat materials to extremely high temperatures while ensuring uniform exposure to heat through tumbling and mixing. The materials are fed into the upper end and move downward toward the exit port due to the kiln's tilt and rotation. Hot gases, generated either externally or internally, flow through the kiln to facilitate heat transfer. The kiln's internal configuration can be adjusted to optimize material exposure to heat and ensure complete combustion of fuel. This process results in physical and chemical changes in the materials, producing the desired end product.
Key Points Explained:
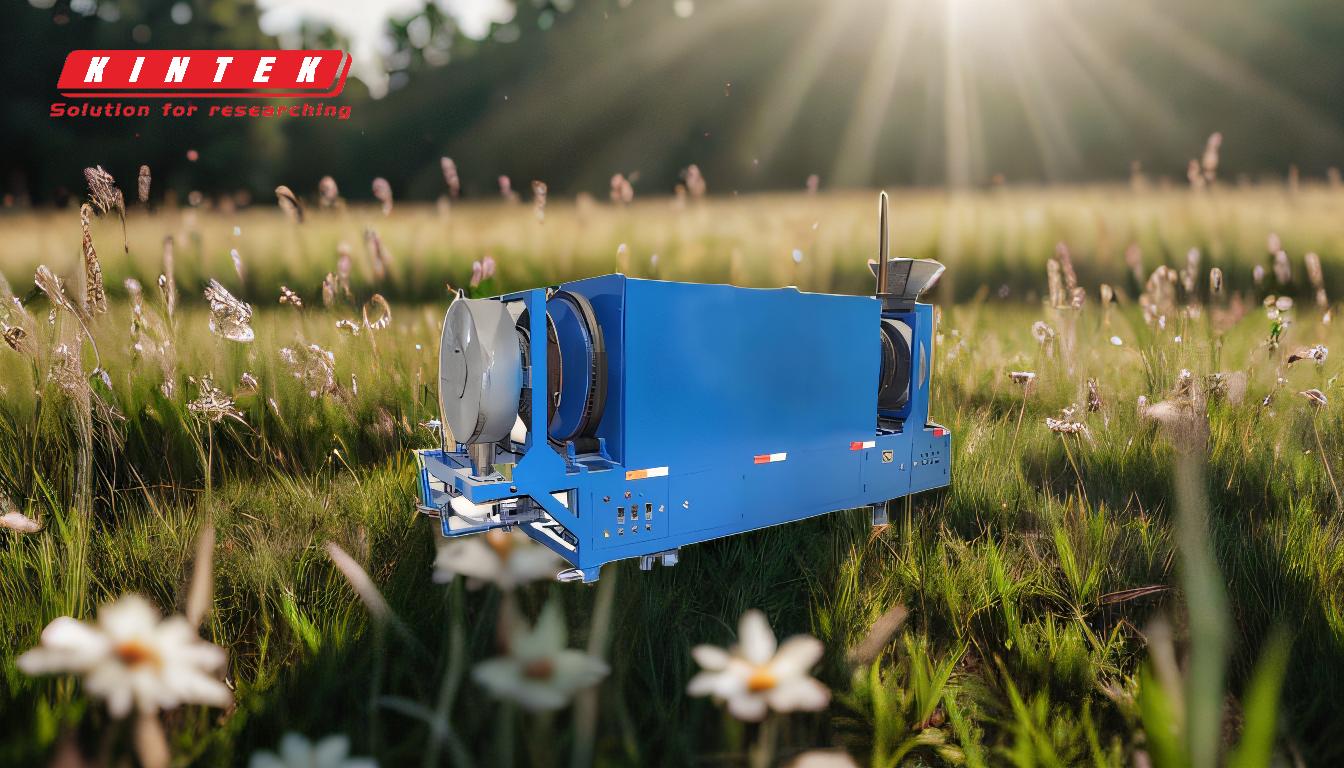
-
Structure and Design of a Rotary Kiln:
- A rotary kiln is a large, hollow, cylindrical vessel made of steel and lined with refractory materials to withstand high temperatures.
- It is slightly inclined (typically 2-5 degrees) from the horizontal to allow materials to move downward by gravity as the kiln rotates.
- The kiln rotates slowly (1-5 revolutions per minute) around its longitudinal axis, ensuring even heat distribution and mixing of materials.
-
Material Feeding and Movement:
- Raw materials are fed into the upper end of the kiln using a feeding device, such as a screw feeder.
- As the kiln rotates, the materials tumble and mix, moving downward toward the lower end due to the kiln's tilt.
- The tumbling action ensures uniform exposure to heat, preventing localized overheating or underheating.
-
Heat Generation and Transfer:
- Heat is generated either by an external furnace or by a flame inside the kiln, projected from a burner-pipe.
- The fuel for combustion can be gas, oil, pulverized petroleum coke, or pulverized coal.
- Hot gases flow through the kiln, either in the same direction as the material (co-current) or in the opposite direction (counter-current), to maximize heat transfer efficiency.
-
Temperature Control and Uniformity:
- The kiln generates extremely high temperatures (up to 1450°C or higher) to superheat the materials.
- The internal configuration, such as the placement of refractory bricks or dams, can be adjusted to control the tumbling action and heat exposure.
- This ensures that the materials undergo the necessary physical and chemical changes uniformly.
-
Physical and Chemical Changes in Materials:
- As the materials move through the kiln, they undergo a series of physical and chemical reactions, such as drying, calcination, and sintering.
- These reactions transform the raw materials into the desired end product, such as cement clinker, lime, or other industrial materials.
-
Exit and Cooling:
- The processed materials exit the kiln at the lower end, where they may be cooled in a separate cooling chamber or by air.
- The cooled product is then collected for further processing or packaging.
-
Operational Adjustments:
- The speed of rotation, tilt angle, and fuel flow rate can be adjusted to optimize the kiln's performance.
- These adjustments ensure efficient heat transfer, complete combustion, and consistent product quality.
By understanding these key points, an equipment or consumable purchaser can better evaluate the operational requirements, maintenance needs, and potential upgrades for a rotary kiln, ensuring optimal performance and longevity of the equipment.
Summary Table:
Aspect | Details |
---|---|
Structure | Cylindrical, inclined vessel made of steel, lined with refractory materials |
Rotation Speed | 1-5 revolutions per minute |
Heat Source | External furnace or internal flame (gas, oil, coal, etc.) |
Temperature Range | Up to 1450°C or higher |
Material Movement | Tumbling and mixing for uniform heat exposure |
Key Processes | Drying, calcination, sintering |
Operational Control | Adjustable rotation speed, tilt angle, and fuel flow rate |
Optimize your material processing with a rotary kiln—contact our experts today for tailored solutions!