Biomass pyrolysis is a thermal decomposition process that breaks down organic materials in the absence of oxygen, typically at temperatures ranging from 300°C to 900°C. The process involves several stages, including pre-treatment, pyrolysis, discharging, and de-dusting. During pyrolysis, the biomass decomposes into its constituent parts—cellulose, hemicellulose, and lignin—which further break down into smaller molecules. These molecules form gases, bio-oil, and solid biochar, depending on the temperature and conditions. The process is governed by primary mechanisms like bond breaking and secondary mechanisms involving reactions of volatile compounds, such as cracking and recombination. Understanding these mechanisms is crucial for optimizing biomass pyrolysis for energy and material recovery.
Key Points Explained:
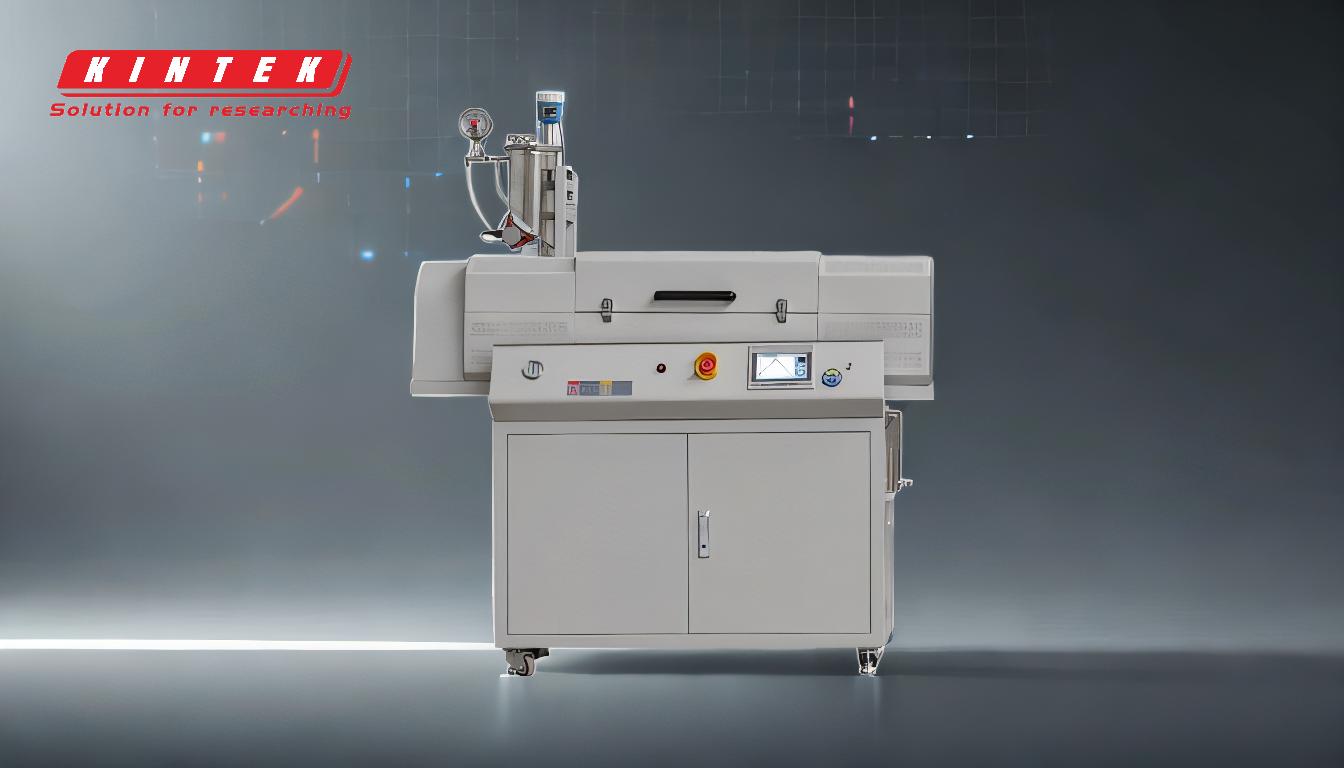
-
Pre-Treatment of Biomass:
- Drying: Moisture is removed from the biomass to ensure efficient pyrolysis.
- Crushing: The biomass is reduced in size to increase surface area, facilitating uniform heating and decomposition.
-
Pyrolysis Stage:
- Temperature Range: Pyrolysis occurs between 300°C and 900°C, with optimal temperatures typically between 400°C and 800°C.
- Absence of Oxygen: The process is conducted in an oxygen-free environment to prevent combustion and ensure controlled decomposition.
-
Decomposition of Biomass Components:
- Cellulose and Hemicellulose: These components break down into smaller, lighter molecules, which form gases and bio-oil upon cooling.
- Lignin: Partially decomposes, leaving behind solid biochar.
-
Primary Mechanisms:
- Bond Breaking: Chemical bonds within the biomass polymers are broken, releasing volatile compounds.
- Volatile Release: The released volatiles are primarily responsible for the formation of gases and bio-oil.
-
Secondary Mechanisms:
- Cracking: Unstable volatile compounds break down further into smaller molecules.
- Recombination: Some volatile molecules may recombine to form more complex compounds.
- Secondary Char Formation: Some of the volatiles may condense and form additional char.
-
Products of Pyrolysis:
- Biochar: The solid residue left after pyrolysis, primarily composed of carbon and ash.
- Bio-Oil: A liquid product formed when the volatile gases condense upon cooling.
- Syngas: A mixture of gases, including hydrogen, carbon monoxide, and methane, which can be used as a fuel.
-
Post-Pyrolysis Steps:
- Discharging: The biochar is cooled and collected for further use or processing.
- De-Dusting: The exhaust gases are cleaned to remove particulates and other harmful substances, ensuring environmental safety.
-
Influence of Temperature and Atmosphere:
- Temperature: Higher temperatures generally lead to more complete decomposition and higher gas yields, while lower temperatures favor biochar and bio-oil production.
- Atmosphere: Pyrolysis can be conducted in a vacuum or inert atmosphere to avoid side reactions like combustion or hydrolysis, improving the recovery of desired byproducts.
-
Mechanisms of Pyrolysis:
- Char Formation: The solid residue (biochar) is formed as a result of the incomplete decomposition of lignin and other complex polymers.
- Depolymerization: Large polymer chains in biomass break down into smaller molecules.
- Fragmentation: Smaller molecules are further broken down into gases and volatile compounds.
By understanding these key points, one can better appreciate the complexity and potential of biomass pyrolysis as a method for converting organic waste into valuable energy and materials.
Summary Table:
Stage | Key Details |
---|---|
Pre-Treatment | Drying and crushing biomass for efficient pyrolysis. |
Pyrolysis | Occurs at 300°C–900°C in oxygen-free conditions; decomposes cellulose, hemicellulose, and lignin. |
Primary Mechanisms | Bond breaking and volatile release form gases and bio-oil. |
Secondary Mechanisms | Cracking, recombination, and secondary char formation. |
Products | Biochar (solid), bio-oil (liquid), and syngas (gases). |
Post-Pyrolysis | Discharging biochar and de-dusting exhaust gases for safety. |
Temperature Influence | Higher temps favor gas yields; lower temps favor biochar and bio-oil. |
Atmosphere Influence | Vacuum or inert atmosphere prevents combustion, improving byproduct recovery. |
Ready to optimize your biomass pyrolysis process? Contact our experts today for tailored solutions!