Chemical vapor deposition (CVD) is a highly controlled process used to deposit thin films of non-volatile solid materials onto a substrate. This is achieved through chemical reactions between gaseous reactants at elevated temperatures, typically around 1925°F (1051°C), within a CVD reactor. The process enhances surface properties such as smoothness, electrical and thermal conductivity, and compatibility with other materials. CVD is versatile and allows precise control over the deposition process, making it a valuable technique in various industries. Its roots can even be traced back to ancient times, as seen in the soot deposition on cave walls from lamps, which is a primitive form of CVD.
Key Points Explained:
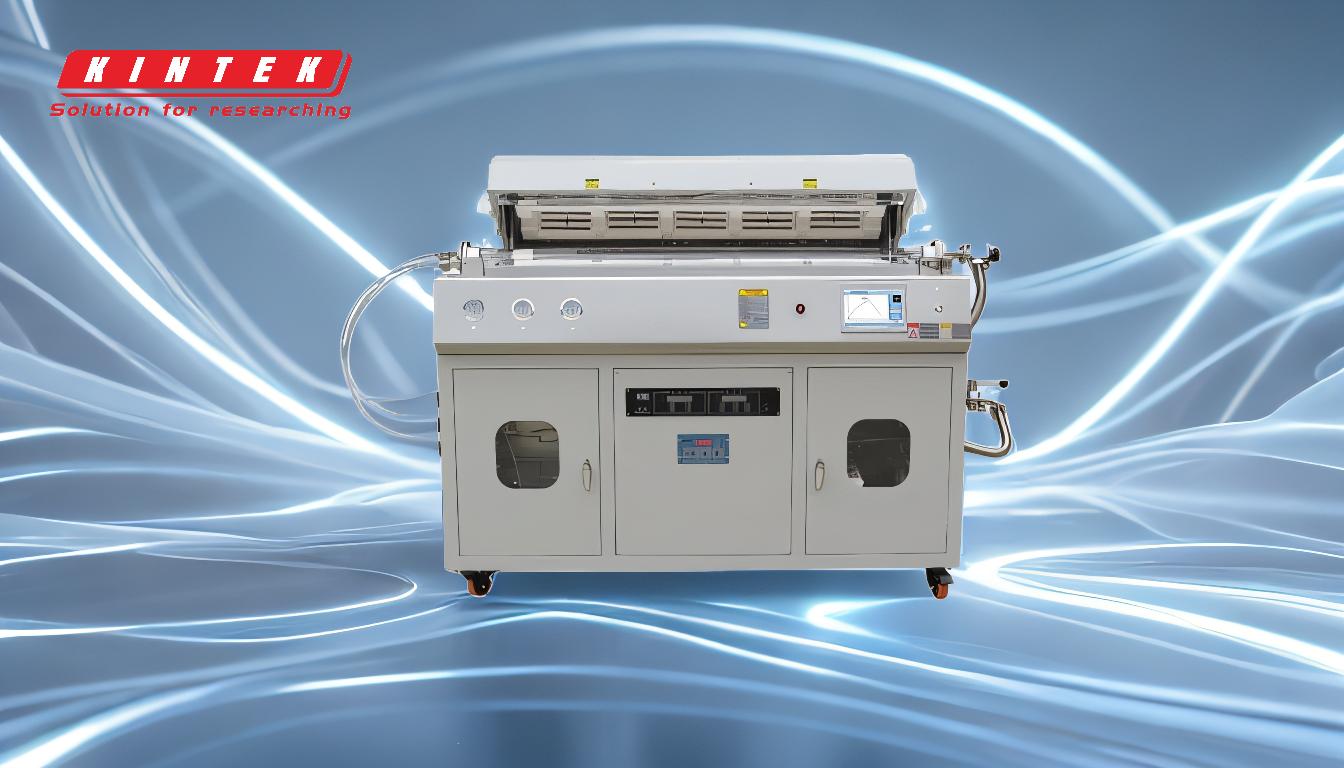
-
Definition and Process of CVD:
- Chemical vapor deposition (CVD) involves the formation of a solid film on a substrate through chemical reactions in the vapor phase. This process occurs in a controlled environment, typically at high temperatures, ensuring the deposition of high-quality films.
-
Temperature and Environment:
- CVD is conducted at elevated temperatures, often around 1925°F (1051°C), within a CVD reactor. The process requires a vacuumed or controlled atmosphere to ensure the chemical reactions occur as intended, providing manufacturers with precise control over the deposition.
-
Surface Improvements:
- CVD enhances surface properties by creating smoother surfaces, improving electrical and thermal conductivity, and increasing compatibility with other materials. This is achieved through the uniform buildup of coating material on the substrate's surface.
-
Historical Context:
- The principles of CVD can be traced back to ancient times. For example, the deposition of soot on cave walls from lamps used by cavemen is considered a rudimentary form of CVD, as described by MIT professor Karen Gleason.
-
Versatility and Control:
- CVD is highly versatile due to its reliance on chemical reactions that occur only in controlled environments. This allows for precise control over the timing and conditions of the deposition process, making it suitable for a wide range of applications.
-
Chemical Reactions:
- The core of CVD lies in the chemical reactions between gaseous reagents and the heated surface of the substrate. These reactions result in the deposition of a solid film, which can consist of atoms, molecules, or a combination of both.
-
Applications and Benefits:
- CVD is widely used in industries requiring thin-film coatings, such as semiconductors, optics, and protective coatings. The process offers benefits like improved surface properties, precise control, and the ability to deposit a variety of materials.
By understanding these key points, one can appreciate the complexity and utility of chemical vapor deposition in modern manufacturing and material science.
Summary Table:
Aspect | Details |
---|---|
Process | Chemical reactions in vapor phase deposit solid films on substrates. |
Temperature | High temperatures (~1925°F/1051°C) in a controlled CVD reactor. |
Surface Improvements | Enhances smoothness, electrical/thermal conductivity, and material compatibility. |
Versatility | Precise control over deposition, suitable for diverse applications. |
Applications | Semiconductors, optics, protective coatings, and more. |
Discover how CVD can revolutionize your manufacturing process—contact us today for expert guidance!