Chemical vapor deposition (CVD) is a sophisticated technique used to create synthetic diamonds by depositing carbon atoms onto a substrate in a controlled environment. The process involves breaking down hydrocarbon gases into carbon plasma, which then deposits onto a substrate, typically silicon, to form a diamond crystal structure. This method operates at relatively low temperatures (around 800–1000°C) and low pressures (<0.1 MPa), making it suitable for industrial applications. The CVD process mimics natural diamond formation but in a controlled, accelerated manner, enabling the production of high-quality polycrystalline diamond films and tools.
Key Points Explained:
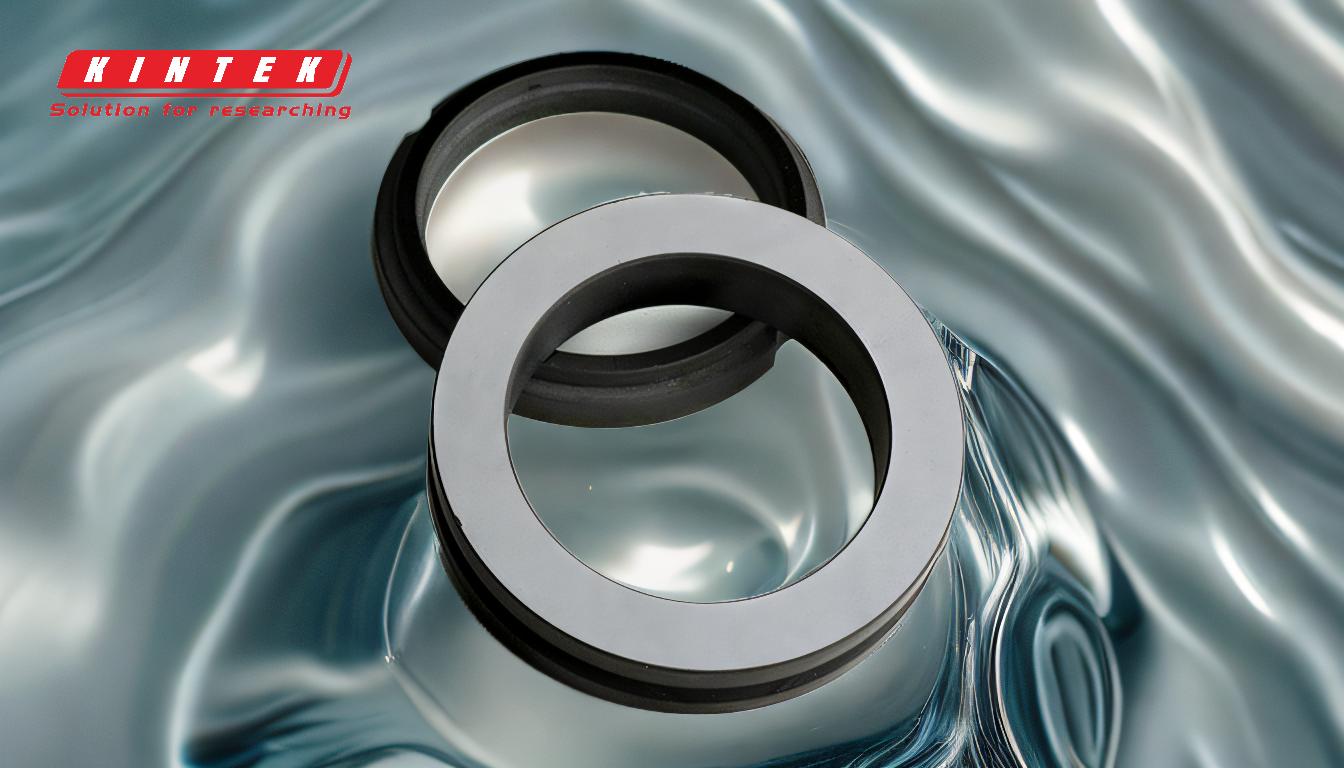
-
Process Overview:
- CVD involves the use of hydrocarbon gases (e.g., methane) that are activated to form a carbon plasma.
- The carbon atoms from the plasma deposit onto a substrate, building up layer by layer to form a diamond crystal structure.
- This process is performed in a vacuum environment to ensure purity and control over the deposition.
-
Key Components:
- Hydrocarbon Gas Mixture: Typically methane (CH₄) mixed with hydrogen (H₂), which provides the carbon source for diamond growth.
- Substrate: Often silicon, which is pre-cleaned using abrasive diamond powder to ensure a suitable surface for diamond nucleation.
- Energy Source: High temperatures (800–1000°C) or plasma activation are required to break down the hydrocarbon gas into reactive carbon species.
-
Chemical Reactions:
- The hydrocarbon gas is cracked at high temperatures, releasing carbon atoms and reactive species.
- These carbon atoms bond together on the substrate surface, forming carbon-carbon (C-C) bonds characteristic of diamond.
- Hydrogen plays a crucial role in suppressing the formation of non-diamond carbon (e.g., graphite) by selectively etching away graphitic carbon.
-
Environmental Conditions:
- Temperature: The process requires high temperatures to provide the energy needed for gas dissociation and carbon deposition.
- Pressure: Low pressure (<0.1 MPa) is maintained to reduce impurities and enhance the efficiency of reactive species collisions with the substrate.
-
Nucleation and Growth:
- Diamond nucleation begins with the adsorption of carbon atoms onto the substrate surface.
- As more carbon atoms deposit, they diffuse across the surface, react, and bond to form diamond crystals.
- The process continues layer by layer until the desired diamond thickness is achieved.
-
Industrial Applications:
- CVD diamond is widely used in the production of polycrystalline diamond films for cutting tools, wear-resistant coatings, and optical components.
- The ability to grow diamonds at relatively low temperatures and pressures makes CVD a cost-effective and scalable method for industrial production.
-
Advantages of CVD Diamond:
- Purity and Quality: CVD allows for the production of high-purity diamonds with controlled properties.
- Versatility: The process can be tailored to produce diamonds with specific characteristics, such as hardness, thermal conductivity, or optical transparency.
- Scalability: CVD is suitable for large-scale production, making it a preferred method for industrial applications.
-
Challenges and Considerations:
- Substrate Preparation: Proper cleaning and preparation of the substrate are critical to ensure successful diamond nucleation.
- Process Control: Precise control of temperature, pressure, and gas composition is necessary to achieve consistent diamond growth.
- Cost: While CVD is more cost-effective than high-pressure high-temperature (HPHT) methods, it still requires significant energy and equipment investment.
By understanding these key aspects, equipment and consumable purchasers can evaluate the suitability of CVD diamond products for their specific applications, ensuring they select materials that meet their performance and budget requirements.
Summary Table:
Key Aspect | Details |
---|---|
Process Overview | Hydrocarbon gases form carbon plasma, depositing onto a substrate layer by layer in a vacuum. |
Key Components | Methane (CH₄) + Hydrogen (H₂), silicon substrate, high temperatures (800–1000°C). |
Chemical Reactions | Hydrocarbon gas cracked into carbon atoms, forming C-C diamond bonds. |
Environmental Conditions | High temperatures (800–1000°C), low pressure (<0.1 MPa). |
Nucleation & Growth | Carbon atoms deposit, diffuse, and bond to form diamond crystals layer by layer. |
Industrial Applications | Cutting tools, wear-resistant coatings, optical components. |
Advantages | High purity, versatility, scalability, and cost-effectiveness. |
Challenges | Substrate preparation, precise process control, and equipment investment. |
Discover how CVD diamonds can transform your industrial applications—contact our experts today to learn more!