Compression molding, a manufacturing process used to shape materials like plastics and rubber, has both positive and negative environmental impacts. On the positive side, it helps reduce waste and energy consumption compared to other methods, and it can incorporate recycled materials, lowering the demand for virgin resources. However, challenges such as material waste from defects (e.g., flow lines, blisters, or heavy flash) and energy-intensive processes can offset some of these benefits. Overall, while compression molding has the potential to be more environmentally friendly, its impact depends on process optimization, material selection, and waste management practices.
Key Points Explained:
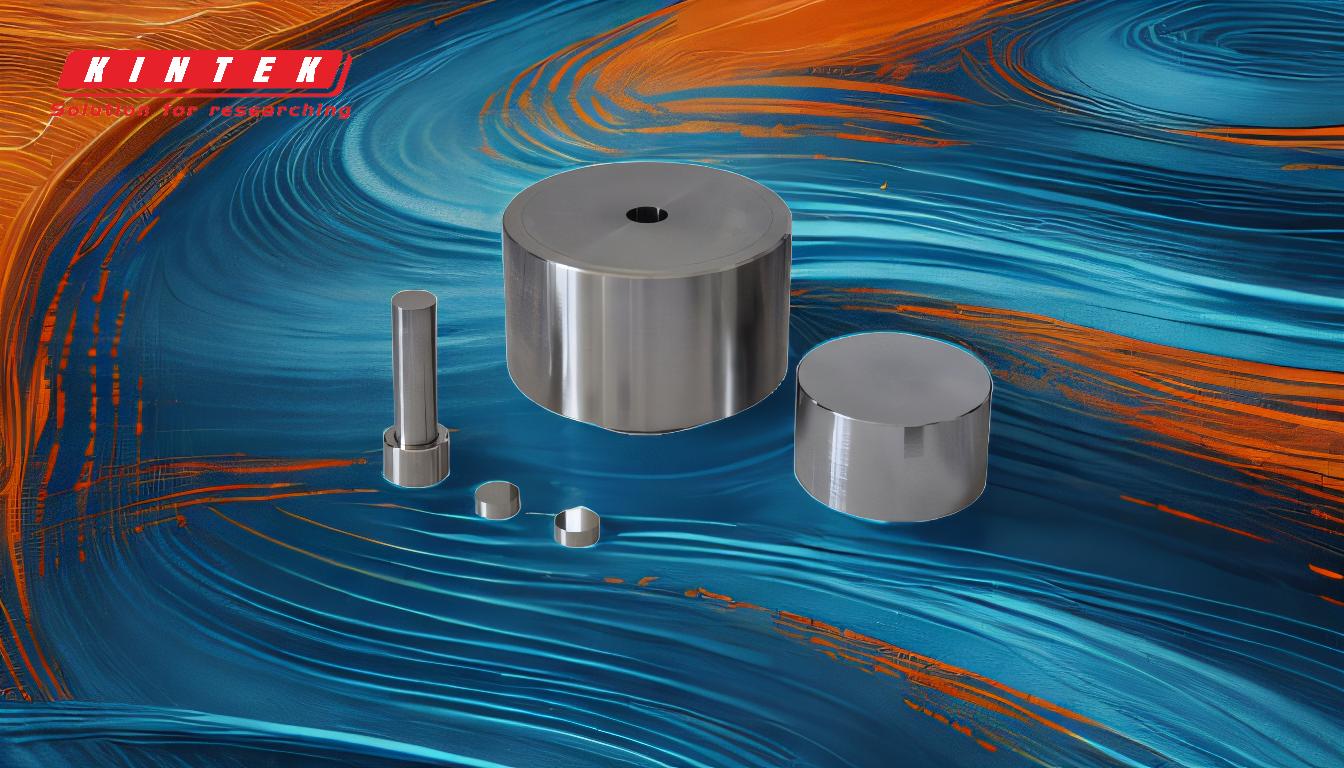
-
Reduction in Waste and Energy Consumption:
- Compression molding is generally more efficient than other molding techniques like injection molding because it uses less energy to heat and shape materials.
- The process minimizes material waste by precisely shaping the material in a closed mold, reducing the need for excess trimming or post-processing.
-
Use of Recycled Materials:
- Compression molding can incorporate recycled plastics or rubber, reducing the reliance on virgin materials and lowering the overall carbon footprint of production.
- This aligns with circular economy principles, where materials are reused and recycled to minimize environmental impact.
-
Challenges Leading to Environmental Concerns:
- Material Waste: Inaccurate cutting or weighing of rubber stock can lead to defects like flow lines, blisters, or unfilled parts, resulting in wasted material.
- Heavy Flash: Excessive material can cause heavy flash, which is difficult to remove and often ends up as waste.
- These challenges highlight the importance of precision in the process to avoid unnecessary environmental harm.
-
Energy Consumption:
- While compression molding is generally energy-efficient, the process still requires significant energy to heat and cure materials, especially for high-temperature applications.
- The environmental impact of this energy use depends on the source of the energy (e.g., renewable vs. non-renewable).
-
Process Optimization for Sustainability:
- To maximize the environmental benefits of compression molding, manufacturers can:
- Use advanced software and machinery to improve material measurement and placement accuracy.
- Implement closed-loop systems to recycle excess material and flash.
- Transition to renewable energy sources for heating and curing processes.
- To maximize the environmental benefits of compression molding, manufacturers can:
-
Comparison with Other Molding Techniques:
- Compared to injection molding, compression molding often requires less energy and produces less waste, making it a more sustainable option.
- However, it may not be suitable for all applications, and its environmental benefits must be weighed against its limitations.
In conclusion, compression molding has the potential to be an environmentally friendly manufacturing process, particularly when optimized for waste reduction and energy efficiency. However, its environmental impact depends on how well manufacturers address challenges like material waste and energy consumption. By incorporating recycled materials and improving process precision, the industry can further enhance its sustainability.
Summary Table:
Aspect | Environmental Impact |
---|---|
Waste Reduction | Minimizes material waste through precise shaping; less trimming/post-processing needed. |
Energy Efficiency | Uses less energy compared to other molding techniques like injection molding. |
Recycled Materials | Incorporates recycled plastics/rubber, reducing reliance on virgin resources. |
Material Waste Challenges | Defects (e.g., flow lines, blisters) and heavy flash can lead to material waste. |
Energy Consumption | High energy use for heating/curing, dependent on energy source (renewable vs. non-renewable). |
Optimization Strategies | Use advanced software, closed-loop systems, and renewable energy to enhance sustainability. |
Want to learn how compression molding can improve your sustainability efforts? Contact us today for expert guidance!