Metal melting in an induction furnace is a highly efficient and controlled process that relies on electromagnetic induction to generate heat within the metal itself. The furnace uses a coil made of conductive material, such as copper, through which an alternating current flows, creating a magnetic field. This magnetic field induces eddy currents within the metal, causing it to heat up and eventually melt. Factors such as temperature, power input, and the presence of impurities influence the melting process. For instance, steel melts at approximately 1370°C (2500°F), and the melting rate can be calculated based on the power input and standard power consumption. Induction furnaces, particularly those using IGBT technology, are widely used in industrial applications due to their precision and energy efficiency.
Key Points Explained:
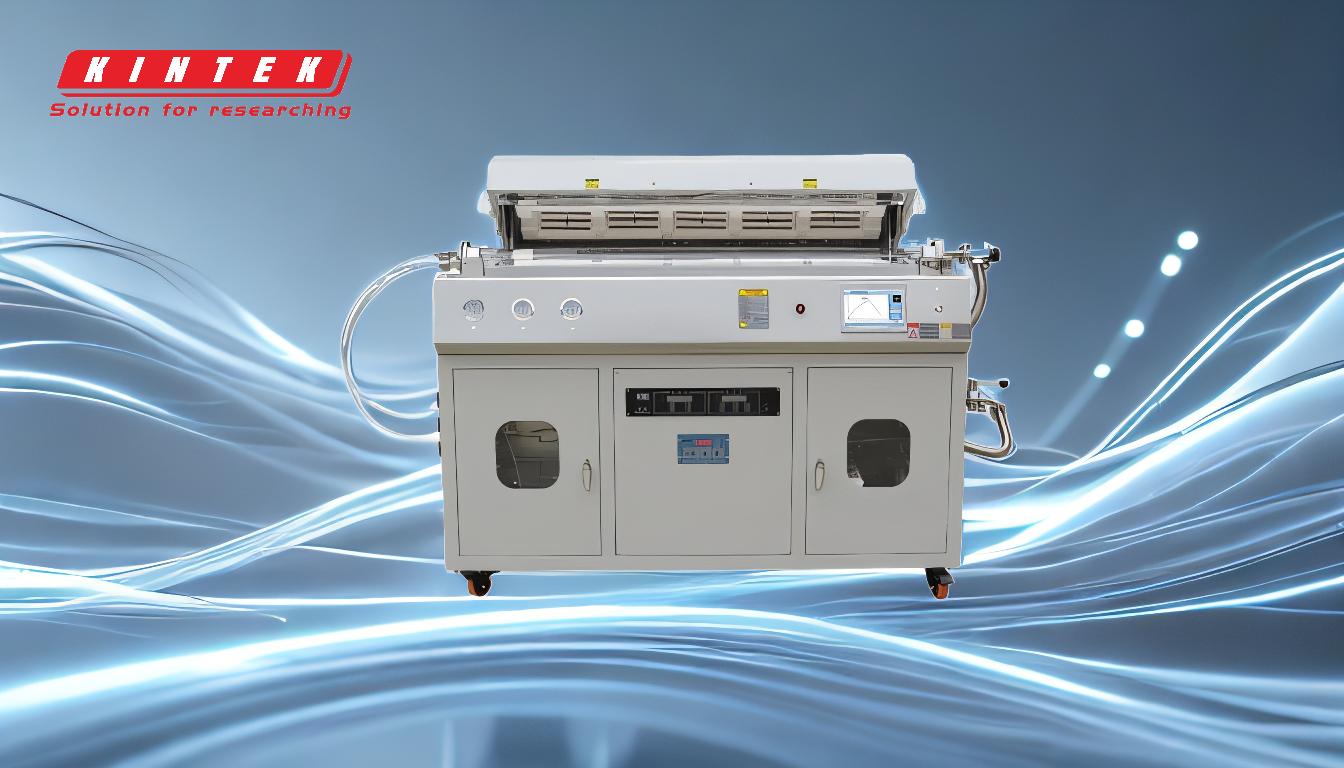
-
Principle of Induction Heating:
- Induction furnaces operate on the principle of electromagnetic induction. A coil made of conductive material, such as copper, carries an alternating current, generating a magnetic field.
- This magnetic field induces eddy currents within the metal placed inside the furnace. The resistance of the metal to these currents generates heat, causing the metal to melt.
- This method ensures that heat is generated directly within the metal, making the process highly efficient and reducing energy loss.
-
Role of IGBT Technology:
- Modern induction furnaces often use IGBT induction furnace technology, which provides precise control over the power supply and frequency.
- IGBT (Insulated Gate Bipolar Transistor) technology allows for efficient switching and regulation of electrical currents, enabling better temperature control and faster melting rates.
- This technology also reduces energy consumption and improves the overall performance of the furnace.
-
Factors Influencing Metal Melting:
- Temperature: The melting point of the metal is a critical factor. For example, steel melts at 1370°C (2500°F).
- Power Input: The power supplied to the furnace directly affects the melting rate. Higher power results in faster melting.
- Impurities and Slags: The presence of impurities or slags can alter the melting characteristics and may require additional processing steps.
- Oxidants: The presence of oxidants can affect the quality of the molten metal and may necessitate the use of protective atmospheres or fluxes.
-
Calculation of Melting Rate:
- The melting rate in an induction furnace can be calculated using the formula: [ \text{Melting Rate (kg/hour)} = \frac{\text{Power (kW)}}{\text{Standard Power Consumption (kWh/ton)}} ]
- For example, a furnace operating at 325 kW with a standard power consumption of 0.625 kWh/kg would have a melting rate of 520 kg/hour.
-
Applications and Advantages:
- Induction furnaces are widely used in industries for melting metals such as steel, iron, aluminum, and copper.
- The process is clean, energy-efficient, and allows for precise control over the melting process, making it ideal for high-quality metal production.
- The use of induction furnaces also reduces the risk of contamination, as the metal does not come into direct contact with the heating element.
-
Comparison with Other Melting Methods:
- Unlike traditional methods such as blast furnaces or electric arc furnaces, induction furnaces do not require a combustion process, reducing emissions and improving environmental sustainability.
- The localized heating in induction furnaces minimizes heat loss and ensures uniform melting, which is particularly beneficial for alloys and specialty metals.
By understanding these key points, equipment and consumable purchasers can make informed decisions about the selection and operation of induction furnaces, ensuring optimal performance and cost-efficiency in metal melting processes.
Summary Table:
Key Aspect | Details |
---|---|
Principle | Electromagnetic induction generates heat directly within the metal. |
IGBT Technology | Ensures precise power control, faster melting, and energy efficiency. |
Critical Factors | Temperature, power input, impurities, and oxidants influence melting. |
Melting Rate Calculation | Melting Rate (kg/hour) = Power (kW) / Standard Power Consumption (kWh/ton). |
Applications | Used for melting steel, iron, aluminum, and copper in industrial settings. |
Advantages | Clean, energy-efficient, and reduces contamination risks. |
Ready to optimize your metal melting process? Contact our experts today to learn more about induction furnaces!